Ultimate Guide to Lapidary Polishing Wheels
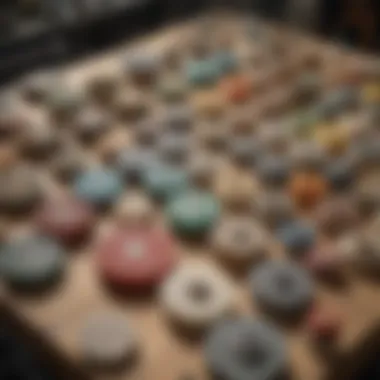
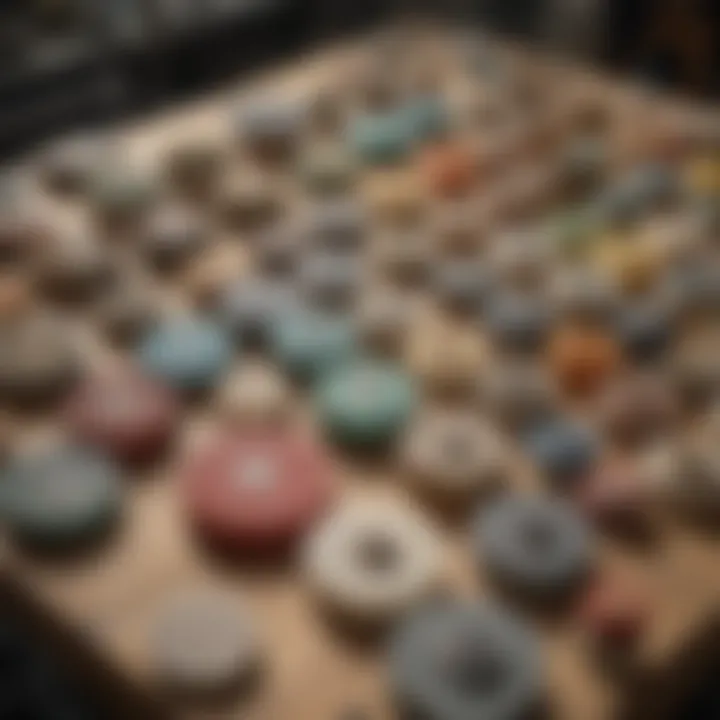
Intro
In the fascinating world of lapidary work, polishing wheels serve as the unsung heroes of the craft. They transform rough stones into dazzling gemstones, playing a crucial role in achieving that mirror-like finish we often admire. These tools aren't just a luxury; they are essential for any serious lapidary practitioner who wishes to elevate their creations.
Understanding the different types of polishing wheels available, their materials, and the techniques to use is invaluable. It can make the difference between a mediocre finish and a gem that captures the very essence of brilliance. Equipped with the right knowledge, you can enhance your lapidary skills and ensure that your polished stones stand out.
Through this guide, we’ll delve deep into various aspects of lapidary polishing wheels, exploring their significance, types, and maintenance practices. From the nitty-gritty details of material compositions to evaluating the craftsmanship they provide, you’ll gain a rounded understanding of how these wheels can profoundly impact your lapidary projects.
Whether you’re an experienced lapidary artisan or just stepping into the realm of gemstone polishing, there’s something in this guide for you. Let’s uncover the intricate world of lapidary polishing wheels.
Foreword to Lapidary Polishing Wheels
Lapidary polishing wheels serve as pivotal tools in the craft of stone finishing, transforming rough stones into beautifully polished gems. The significance of these wheels cannot be overstated, as they are essential for achieving the sought-after shine that enhances the visual appeal of gemstones. Without them, the lapidary process would be like trying to paint a masterpiece with a brush designed for broad strokes—imprecise and lacking finesse.
When talking about lapidary work, one must consider several elements that revolve around polishing wheels, including types, materials, and techniques. All these factors play a crucial role in ensuring that every piece reflects the hard work and artistry of the lapidary craftsmanship. Moreover, selecting the appropriate polishing wheel can make or break the finishing stage of your stone, so understanding their nuances is critical to any craftsman's success.
Understanding Lapidary Work
Lapidary work is as ancient as civilization itself, dating back thousands of years. Traditionally, artisans crafted ornate items from stones, practicing their skills by hand. Today, the practice has evolved, but the essence remains.
In lapidary work, one manipulates stones and minerals in various forms, whether creating jewelry, carvings, or decorative pieces. The process typically includes cutting, shaping, sanding, and ultimately polishing the stones. Each stage demands different tools and skills, especially polishing, where the right wheel dramatically affects the final output.
Lapidary enthusiasts often view their craft as a blend of art and science. They must not only appreciate the beauty of stones but also understand the mechanics behind the tools used. This intricate balance makes polishing wheels integral to their work, as achieving a flawless finish can reveal the inner beauty of the stone, showcasing unique colors and patterns that might otherwise remain hidden.
Role of Polishing Wheels in Lapidary
Polishing wheels are the unsung heroes of lapidary work. They essentially act as the final brushstroke on a canvas, giving life and vibrancy to meticulously crafted stones. The role they play is multifaceted:
- Achieving Finishes: Different wheels yield distinct finishes. A rough wheel prepares the surface, while finer wheels bring out a brilliant shine that catches the eye.
- Material Compatibility: Some wheels work better with certain materials. Knowing which wheel to pair with which stone can save time and effort.
- Time Efficiency: Using the right polishing wheel not only enhances the finish but also expedites the overall process. A skilled lapidary understands that time spent choosing the correct wheel is time well invested.
"A good lapidary understands their tools like a musician understands their instrument—it's the key to creating harmonious results."
In summation, the interplay between polishing wheels and lapidary work demands a symbiotic relationship; the right choice can elevate a simple stone to a work of art. As we delve further into this guide, we will explore the various types of polishing wheels available, the materials they are made from, and how one can select and maintain them effectively.
Types of Lapidary Polishing Wheels
When discussing lapidary work, knowing the types of polishing wheels is instrumental. Each type caters to specific materials and varies in functionality, offering unique benefits that can enhance your gemstone finishing processes. A well-informed choice helps practitioners achieve superior results while optimizing time and resources.
Diamond Wheels
Diamond wheels are, without any doubt, the superstar in the world of lapidary polishing tools. These wheels are embedded with industrial-grade diamond particles, giving them remarkable hardness. This means they can tackle even the toughest stones. For collectors or craftsmen working with hard materials like quartz or agate, diamond wheels are often the go-to choice. They create a smooth finish that can be hard to achieve otherwise.
One key consideration about diamond wheels is their lifespan. Unlike other polishing wheels, diamond wheels last considerably longer, making them cost-effective over time. However, they may carry a little bit of a higher upfront cost, so keep an eye on your budget as you make your selection. Given the toughness of these wheels, they require a distinct approach when used - slower speeds, ample water for cooling, and consistent monitoring of wear ensure optimal performance.
Ceramic Polishing Wheels
Ceramic wheels occupy an important place in the polishing lineup. These wheels utilize ceramic materials for their smoothness and consistency. Ideal for softer stones, such as some types of calcite or jade, they do a fine job of producing a luster that showcases the stone's natural beauty.
One notable benefit of ceramic wheels is their versatility. They can be employed for both rough shaping and fine polishing, making them suitable for a range of lapidary projects. Plus, they are generally more affordable than diamond wheels. A downside, however, could be that they wear down faster, requiring more frequent replacements. Knowing the right type of stone to apply this wheel on is essential for achieving the desired results.
Bristle Wheels
Bristle wheels have a softer touch, crafted from nylon or similar materials. They serve a unique purpose in the polishing process. The bristles allow for gentle finishing and are particularly great for intricate designs or articles that need a lighter touch. If you’re working on jewelry with delicate settings or need to remove fine scratches, bristle wheels come to the rescue. Furthermore, you can apply various polishing compounds to enhance the final finish.
One critical factor to note is the pressure applied while using bristle wheels. Too much force could damage softer stones or intricate details. Therefore, it’s best to let the wheels do the work, using a light hand to achieve the best results.
Felt Wheels
Felt wheels often get overlooked, yet they are indispensable for achieving a high-gloss finish. Made from compressed felt, these wheels are widely used for applying polishing compounds such as rouge or tin oxide. They are the final touch in many lapidary projects, bringing out the shimmer and shine that can elevate a piece from merely crafted to extraordinarily alluring.
A significant advantage with felt wheels is their ability to conform to irregular stone surfaces. Their flexibility means they can get into small nooks and crannies, providing an even finish without risk of damage. It’s important to remember, though, that they require proper cleaning and care to maintain their effectiveness over time.
Sanding Wheels
Sanding wheels serve as the first step before polishing. Constructed with various grits, ranging from coarse to fine, they help shape and smooth the stones as a preparatory measure. They’re an essential tool for anyone looking to refine the outlines of a stone or remove significant imperfections before moving on to polishing.
Choosing the right grit is a crucial point. For example, a coarse grit is excellent for heavy shaping, while a finer grit will allow for smoother transitions. Keep in mind that using sanding wheels too aggressively on softer stones can result in scratches or gouges. Therefore, moderate pressure and gradual progression through grits can yield the best outcomes.
In summary, understanding the various types of lapidary polishing wheels is vital for achieving excellent results. Each type offers specific benefits, and selecting the right one based on the stone and desired finish can make all the difference in lapidary craftsmanship.
Materials Used in Polishing Wheels
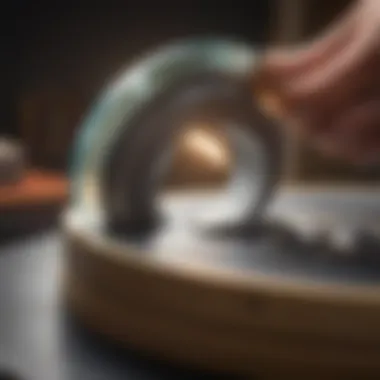
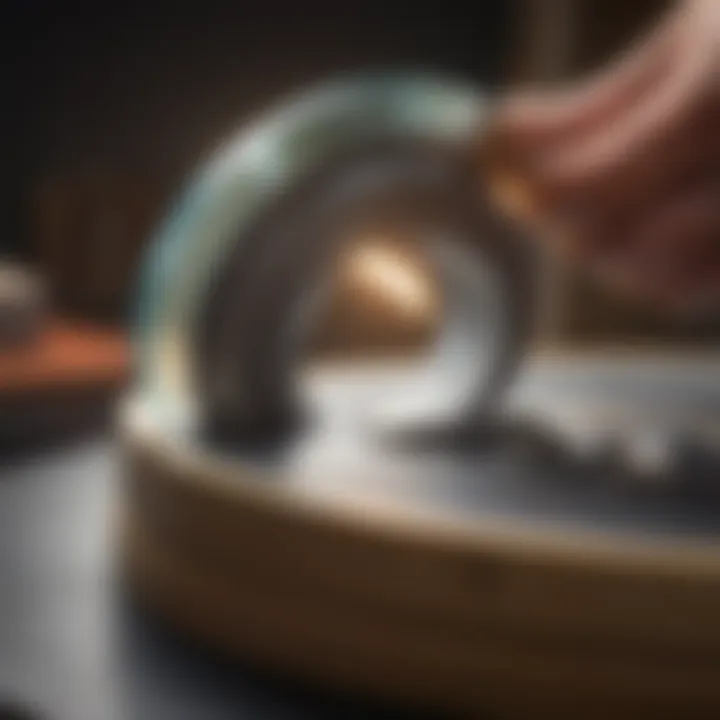
In the world of lapidary work, the materials constituting polishing wheels play a pivotal role in determining the quality and final appearance of stones. Different materials offer unique advantages tailored to specific types and qualities of gemstones. Using the right material, lapidary craftsmen can optimize their polishing techniques, ensuring that gems not only shine but also retain their integrity throughout the polishing process. As such, understanding these materials is fundamental for anyone serious about enhancing their lapidary skills.
Common Polishing Materials
Aluminum Oxide
Aluminum oxide serves as a widely accepted material in polishing wheels due to its toughness and versatility. This compound is notably used to create grit that tackles a variety of stones effectively, making it a choice material for many enthusiasts. What sets aluminum oxide apart is its ability to provide a smooth finish on hard rocks, which is a crucial aspect of lapidary polishing.
Among its benefits, the key characteristic of aluminum oxide is its durability. It resists breakage and maintains effectiveness throughout multiple uses. However, it does have a few downsides; for instance, on softer stones, it may wear them down quicker than desired, possibly altering their natural structure. Still, for those looking to polish a patch of quartz or agate, aluminum oxide often comes highly recommended.
Silicon Carbide
Silicon carbide comes into play with its unique attributes that cater to a specific subset of polishing needs. Known for being one of the hardest abrasives available, it excels particularly at dealing with harder materials, capable of grinding faster than many alternatives. This makes silicon carbide an advantageous choice for stones that demand aggressive material removal.
The standout feature of silicon carbide is its ability to generate a high-quality polish without needing excessive pressure. This means a lapidary can work efficiently and achieve desired results more quickly. On the flip side, its aggressive nature might not be suitable for softer gemstones like turquoise, which could easily chip or scratch under its influence. Therefore, careful selection is advised depending on the type of stone in question.
Ceramic Compounds
Ceramic compounds add yet another layer of diversity in polishing materials. The integration of ceramic materials allows for a balanced polishing experience, combining both hardness and flexibility. This makes them excellent for achieving fine finishes on various stones while also being relatively easy on the material compared to other harder abrasives.
A distinct advantage of ceramic polishing wheels is their resistance to thermal degradation, meaning they can endure higher speeds without losing effectiveness. However, they are not always as aggressive as diamond or silicon carbide options, which means that for heavily flawed surfaces or challenging stones, they might not cut it. Yet, for those seeking a refined polish on diverse materials, ceramic compounds represent a popular and beneficial choice.
Specialized Polishing Compounds
There are also specialized compounds that serve niche purposes in lapidary polishing, often catering to specific finishes or stone types.
Tripoli
Tripoli is a fine polishing powder that comes into play toward the end of the polishing process. Characterized by its light color and soft texture, it excels in delivering a high-gloss finish on softer materials. Lapidaries often reach for tripoli when they pursue a detailed quality, aiming for that extra shine that catches the eye.
The unique quality of tripoli lies in its ability to produce exceptional luster without scratching the surface of softer gemstones. However, it’s not a one-size-fits-all solution, as tripoli may not be effective on harder stones, where heavier abrasives are required. Thus, knowing when and how to use tripoli is critical for avoiding missteps in the polishing process.
Rouge
Rouge is another specialized polishing compound, often recognized for its ability to impart a brilliant shine to stones, particularly metals. It consists primarily of iron oxide and is favored by many lapidary artists for its effectiveness on precious metals and certain types of natural stones.
The standout attribute of rouge is its ability to create a mirror-like finish, adding a level of intensity to the polish that is hard to achieve with other materials. However, it’s worth noting that usability can be limited to very specific applications, as its iron content might not suit all gemstone polishing needs. Understanding its characteristics helps lapidaries make informed decisions about when and where to incorporate rouge into their work.
Tin Oxide
Last but not least, tin oxide finds its place in the repertoire of polishing materials, particularly when the goal is to achieve the highest level of shine. Often regarded as one of the finest polishing materials available, tin oxide is favored for its work on glass and gemstones alike.
What makes tin oxide so special is its ultra-fine particles, which help in creating a velvety smooth finish. While beneficial, its costs can be higher than typical abrasives, and it may require specific conditions to ensure optimal results. Therefore, a lapidary ha to gauge its usage based on the future needs of their stones and their overall polishing objectives.
Selecting the right materials for polishing wheels not only enhances the quality of your finished pieces but also ensures that your tools and stones remain in good condition. As discussed, every choice has its pros and cons, making it essential to weigh your options carefully.
Selecting the Right Polishing Wheel
Selecting the appropriate polishing wheel is crucial for achieving the desired finish on gemstones and other materials in lapidary work. A well-chosen wheel will not only save time but can also enhance the quality of the final product. This section explores several components essential to that selection: assessing your stone type, understanding grit sizes, and considering wheel compatibility. Each of these elements plays a significant role in not just the process, but also in ensuring that the investment made in materials and time yields the best results.
Assessing Your Stone Type
The stone you intend to polish can significantly impact the choice of polishing wheel. Different materials require varying levels of abrasion and finishing, which makes understanding your stone type paramount. For instance, softer stones such as soapstone or limestone can often benefit from less aggressive polishing media. On the other hand, harder stones like granite or quartz demand more robust wheels, typically those made of materials like diamond or high-quality ceramic.
Consider also the characteristics: Is your stone translucent or opaque? Does it have fissures that could crack under pressure? For delicate stones, a lighter touch with gentler wheels is necessary to avoid damaging the material. Conversely, if you’re dealing with a tougher gem like topaz, a more aggressive wheel might be warranted that can handle the hardness without strain.
A quick checklist for assessing your stone type includes:
- Hardness Rating: Use the Mohs scale to gauge the mineral's hardness.
- Transparency: Translucent gems often require more refined finishing methods.
- Fractures: Assess for any existing cracks or weak points in the stone.
Understanding Grit Sizes
Grit size refers to the size of the particles embedded in the polishing wheels, and it’s described numerically, with a higher number indicating a finer grit. Understanding which grit to use for different stages of polishing involves a bit of strategy. Typically, the process starts with coarser grits to shape and smooth the stone, then transitions to finer grits to give it a brilliant finish.
For example, starting with a 100 or 200 grit wheel is common for initial shaping. This removes larger imperfections and prepares the stone for finer detailing. After that, moving to a 600 grit wheel for smoothing is a common practice. Finally, to achieve a glossy finish, you might conclude with a 1200 or higher grit wheel.
Here’s how grit size generally breaks down:
- Coarse Grit (60-220): Ideal for initial shaping and fast material removal.
- Medium Grit (240-600): Effective for refining the shape and reducing scratches from the coarse stage.
- Fine Grit (800+): Used for achieving a smooth, polished finish.
Considering Wheel Compatibility
Once you know your stone type and the appropriate grit sizes, the next step is to ensure that your polishing wheels are compatible with your lapidary equipment. Each polishing wheel has a specific arbor size and may also have particular mounting requirements. Ensuring that the chosen wheel fits your machine is critical.
It’s worthwhile to keep the following in mind:
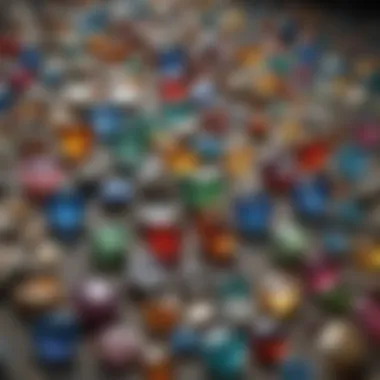

- Arbor Size: Check the wheel's specifications to match your machine.
- Wheel Thickness: Thicker wheels can handle more pressure but might be less versatile.
- Material Compatibility: Some machines are designed for specific types of wheels, like diamond or felt.
In summary, selecting the right polishing wheel isn’t just about picking one off the shelf. It’s an involved process that requires a solid understanding of the stones you’re working with, the function of different grits, and the specifications of your equipment. Follow these guidelines to ensure you pick the wheel that will help you achieve the best results in your lapidary projects.
Using Lapidary Polishing Wheels Effectively
Using lapidary polishing wheels effectively is crucial to achieving that stunning, mirror-like finish on gemstones. The art of lapidary involves transforming rough stones into polished masterpieces, and polishing wheels play a key role in this transformation. By mastering how to use these wheels, you can enhance both the beauty of your stones and the efficiency of your lapidary work.
Preparation of the Stone
Before diving into the actual polishing process, preparing your stone is essential. It may sound simple, but paying attention to this step can save you a lot of heartache in the long run. First, ensure the stone is clean and free from any debris or dust. A dirty stone can lead to unsightly scratches during polishing, negating the hard work you've put into shaping it. Using warm soapy water and a soft cloth will often do wonders.
Next, assess the shape and flatness of your stone. If the surface is uneven, you might need to use a grinding wheel first to achieve an appropriate profile. Keep in mind that a little patience here can pay off later, as a well-prepared stone yields better results when using polishing wheels. You might also consider using a lubricant during the polishing process; it helps in reducing heat and allows the wheel to work more efficiently.
Proper Wheel Operation Techniques
Using your polished wheel doesn't just involve turning it on and starting to push stones against it. There are techniques that must be taken into account for effective polishing. For one, the rpm of the wheel should match with the type of polishing you are aiming for. A higher speed usually produces a finer finish on harder materials. However, too high a speed might generate heat that can damage softer stones.
Additionally, don’t forget about the angle. Holding your stone at the right angle against the wheel can make all the difference. Generally, keeping a 45-degree angle allows for uniform polishing. You also need to apply even pressure while moving the stone over the surface of the wheel. If you press too hard or unevenly, it could lead to an uneven finish or worse, breakage of the stone. Remember that practice makes perfect; try to be gentle when learning.
Timing and Pressure Applications
Timing is everything when it comes to polishing. It’s not just about how long you polish, but also when to change the wheels or the grit. After a few minutes of polishing, it's wise to check your work. If you find you're not making progress as expected, it may be time to switch to a finer grit or a different type of wheel.
In terms of pressure, less is often more. Applying too much pressure can lead to premature wear on the wheel and can also hurt the stone. Start with lighter pressure and increase it gradually as you gauge the response of the stone and wheel. Over time, you'll develop a sense for how much force to apply.
"Proper technique leads to both improved efficiency and superior outcomes in lapidary work. Don’t rush; take the time to master the processes."
Maintenance of Lapidary Polishing Wheels
Proper maintenance of lapidary polishing wheels is crucial for both the longevity of the tools and the quality of the work produced. Just like a craftsman sharpens their tools to ensure precision, maintaining polishing wheels ensures that they perform effectively and yield the desired results when finishing stones. Without adequate care, users may find that their wheels degrade faster, resulting in subpar finishing or the necessity for frequent replacements.
Cleaning Techniques
Keeping your polishing wheels clean is fundamental. The buildup of dust, residual polishing compound, or stone particles can impede performance. A simple cleaning routine can go a long way. Here are several techniques:
- Water Rinsing: Whenever you finish using a wheel, rinse it under water while it's still spinning. This can wash away most debris.
- Soft Brush: For stubborn residue, gently scrub the wheel with a soft brush. This is especially useful for ceramic wheels that might catch fine particles more easily.
- Cleaning Solutions: Utilize specialized detergent or cleaners designed for lapidary equipment. A solution can further break down compounds and restore peak performance.
- Air Blowing: A blast of air from an air compressor can assist in dislodging particles lodged deep in the wheel's structure.
Storing Your Wheels
Proper storage of lapidary polishing wheels is another key aspect of maintenance. It’s not just about protecting the wheels from dust; it’s also about preventing physical damage and ensuring that they retain their shape and effectiveness. Here are some best practices:
- Vertical Storage: Store wheels vertically to prevent warping. This is crucial for materials like felt or bristle wheels.
- Temperature Control: Keep them in a cool, dry place. Extreme temperatures or humidity can affect the integrity of the materials.
- Covering: If possible, cover wheels with a cloth or plastic to prevent dust accumulation. This simple act can save time in cleaning later.
Signs of Wear and Replacement
Every tool has its limits, and lapidary polishing wheels are no exception. Recognizing when a wheel is worn out can save time and enhance the quality of the final product. Here are some signs that it might be time to replace your wheel:
- Not Polishing Effectively: If you notice that the wheel is not achieving the desired shine or finish like it used to, it may be worn.
- Visible Damage: Cracks, chips, or distortions on the wheel surface are indications of wear that can affect performance.
- Changing Grit: If you find that the grit is wearing unevenly or has changed from what it should be, this is a clear signal for replacement.
- Shimmer and Shine: For felt wheels, if they lose their luster or appear too flat, they may need to be replaced to maintain quality.
Overall, diligent care and maintenance of lapidary polishing wheels not only prolong their life but also enhance the results derived from their use. Just as a painter cares for their brushes, so too must the lapidary artist nurture their wheels.
Practical Applications in Lapidary Work
Lapidary work is a craft that combines art with meticulous skill. The tools used in this field, particularly polishing wheels, play a pivotal role in achieving the desired finish on gemstones. Understanding the practical applications of these polishing wheels is essential for anyone looking to elevate their lapidary projects. Not only do these wheels provide the necessary polish, but they also ensure that stones are transformed from rough specimens into stunning pieces ready for various uses, including jewelry, decorative art, and geological displays.
Creating Jewelry from Stones
Turning raw stones into beautiful jewelry pieces is perhaps one of the most rewarding applications in lapidary work. Polishing wheels are integral to this process. After shaping stones on diamond wheels, it becomes imperative to refine their surfaces using softer polishing wheels, such as felt or bristle wheels.
The right grit size is crucial here. For instance, using a fine grit on a felt wheel can impart a mirror-like finish on a cabochon, making it sparkle under light. This not only enhances the stone’s natural beauty but also attracts potential buyers, especially in artisanal markets.
When crafting jewelry, consider the stone's characteristics. Some stones, like opals, require gentler techniques to prevent damage. Aligning the polishing wheel speed and pressure helps achieve optimal results, preventing scratches that would mar the final product. It's a blend of art and technique, underscoring how essential polishing wheels are in producing exquisite jewelry pieces.
Crafting Decorative Items
In addition to jewelry, polishing wheels find their place in creating decorative items such as sculptures and coasters. These artifacts need to showcase the stone’s unique patterns and colors, which are best revealed through careful polishing. The use of softer materials, like those found in ceramic or felt polishing wheels, allows for a gradual refinement of the surface, bringing out the intricate textures nestled within the stone.
Creating such items, however, requires a thoughtful approach. Different stones react variably to polishing. For example, a softer stone might polish beautifully with less pressure, while harder stones, like granite, may need a more aggressive technique initially before transitioning to finer wheels.
"Polishing isn't just about the shine; it's about understanding your medium and working in harmony with it."
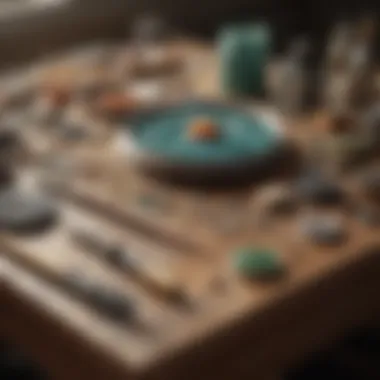
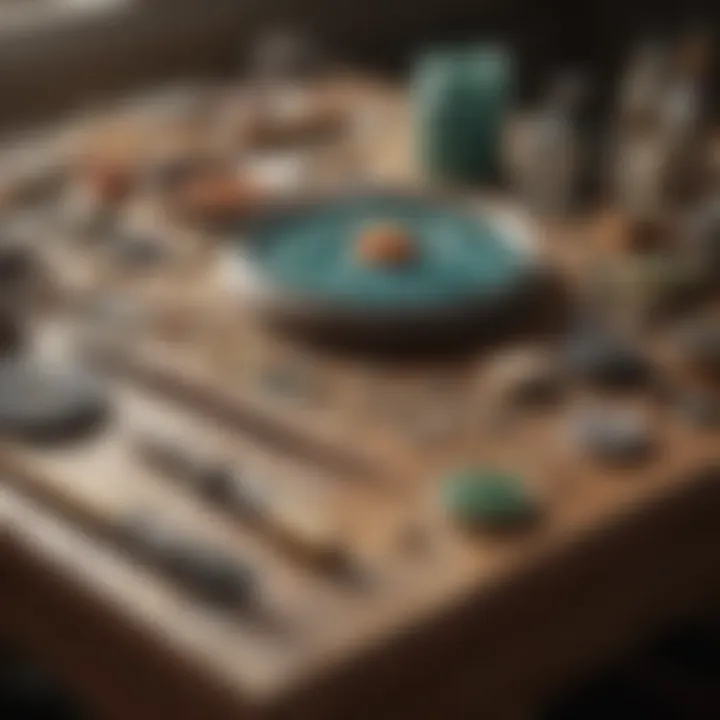
The tools you choose can either enhance or overshadow your creativity. Thus, being strategic about which polishing wheels you employ can make all the difference in crafting stunning decorative pieces that invite admiration.
Enhancing Geological Collectibles
For rock and fossil collectors, polishing is essential to enhance the aesthetics and educational value of their finds. Whether it’s a polished geode or a fossil, polishing wheels serve to highlight the detailed formations that nature has meticulously crafted over eons.
Collectors often use diamond polishing wheels at the initial stages to tackle rough surfaces and establish a basic shape. Following that, switching to softer materials helps reveal the gem-like finish that showcases colors and textures. This not only improves their display but adds significant value to the collectible.
Moreover, completing this process with specific polishing compounds can protect the surface from environmental damage. For instance, a final polish with tin oxide can help achieve a brilliant sheen while repelling dust and moisture, thereby preserving the item.
In summary, lapidary polishing wheels are not merely tools; they are the bridge between raw materials and finished art forms. From creating wearable art to displaying geological wonders, the practical applications of these wheels are vast and pivotal in delivering stunning results for every lapidary artist.
Safety Considerations
Safety must be front and center when engaged in lapidary work. The delicate balance between creativity and caution cannot be overstated—ensuring one's well-being is paramount. Personal injuries, harmful exposure to dust, and unforeseen accidents can happen, particularly when working with powerful machines and fine materials. Thus, a clear understanding of safety mechanisms represents not just a precaution, but a foundational aspect of effective lapidary practice that allows practitioners to focus on their craftsmanship without distraction from hazards.
Personal Protective Equipment (PPE)
Utilizing the proper personal protective equipment (PPE) can mean the difference between a great lapidary session and a potentially dangerous scenario. The most common types of PPE recommended include:
- Safety glasses: These should be worn to shield the eyes from stone chips and dust. Look for ANSI Z87.1-rated glasses to ensure adequate protection.
- Dust masks or respirators: Fine particles can easily be inhaled during the polishing process, leading to respiratory issues. A mask that filters out particles is essential, especially when working with materials that can create toxic dust.
- Hearing protection: Many polishing wheels can be rather loud, leading to potential hearing damage after extended use. Earplugs or noise-canceling headphones can mitigate this risk.
- Gloves: Durable, cut-resistant gloves help avoid cuts or abrasions from sharp stone edges. Choose gloves that allow for dexterity while providing sufficient protection.
It's like an onion—layering up with these safety features will help you peel away risks, allowing you to focus on honing your skills.
Work Environment Safety Tips
Creating a safe work environment is equally crucial. The workspace should be organized and free from clutter, reducing the chances of accidents. Here are a few safety tips to keep in mind:
- Adequate ventilation: Always work in a well-ventilated area to help disperse dust and fumes. If possible, use a dust collection system to keep the air clean.
- Sturdy work surfaces: Ensure your workbench is durable and won’t wobble during use. This prevents slips and accidents—think of it as the foundation of your lapidary castle.
- Proper lighting: Ensure your workspace is well-lit. This will help you see what you’re doing, preventing mistakes and allowing you to produce better finishes on your stones.
- Regularly maintained equipment: Regular checks on your polishing wheels and tools can prevent malfunction. A smooth running tool is safer and more efficient, which means you spend less time fixing problems.
Leading with safety in a lapidary setting is not just about compliance, it's about fostering an environment where creativity flourishes. When practitioners take these precautions, they maximize their enjoyment of the art form while minimizing risks. Remember to always prioritize your well-being; after all, a true craftsman takes care of their tools—the most valuable of which is themselves.
Future Trends in Lapidary Polishing Technology
As the world moves forward, so does the craft of lapidary work. Understanding the future trends in lapidary polishing technology is crucial for seasoned jewelers as well as hobbyists. These trends aim to enhance efficiency, reduce environmental impact, and improve the quality of finishes on gemstones. Staying informed about these developments not only keeps lapidary artists ahead of the curve but also enhances their craftsmanship.
Technological Innovations
New technologies are continuously reshaping the landscape of lapidary polishing. One integral development is the rise of computer-aided design (CAD) software, making it easier for lapidary artisans to visualize their designs before committing to the stone. This allows for precision like never before, which can result in fewer errors and waste.
Furthermore, innovations in polishing wheel fabrication have led to the introduction of wheels that incorporate synthetic and natural resins, which not only enhance durability but improve the functionality too. Technology such as laser cutting is also becoming prevalent, creating more intricate designs in polishing wheels that cater specifically to individual needs.
"The future of lapidary polishing wheels could very well lie in a harmony of tradition and technology, with new materials augmenting age-old practices."
In addition to material enhancements, automation and robotics are coming into play. While still in the early stage in many workshops, robots equipped with advanced programming can produce consistent finishes much faster than manual methods can achieve. This could revolutionize larger-scale operations where speed is paramount.
Sustainable Materials and Practices
As sustainability becomes increasingly important across industries, lapidary work is no exception. The adoption of sustainable materials in polishing wheels can significantly reduce the carbon footprint associated with gemstone finishing. Recycled materials are being used to create new polishing wheels, while also maintaining the quality expected by artisans.
Moreover, companies are exploring the use of biodegradable resins and natural abrasives. This shift not only meets eco-friendly standards but also appeals to the growing consumer base that values sustainability.
A near future will likely consist of workshops that emphasize zero-waste practices. This entails more efficient use of materials and innovative methods for recycling exhausted polishing wheels. Such practices are not just cutting costs but are also crucial for preserving resources in an industry heavily reliant on raw materials.
In summary, the future of lapidary polishing technology promises exciting prospects that blend innovation with ecological responsibility. Keeping an eye on these trends could lead to not only better gemstones but also a more sustainable practice overall.
End
Understanding the nuances of lapidary polishing wheels is paramount for any passionate artist or collector diving into the realm of gemstone finishing. This section synthesizes the critical points discussed in the article, highlighting the relevance of polishing wheels as indispensable tools in lapidary work.
Summary of Key Insights
Lapidary polishing wheels are not just accessories; they are essential instruments that can make or break the end product of any lapidary endeavor. From diamond wheels to various compounds, each type provides distinct advantages that can enhance the texture and clarity of your stones.
- Diverse Types: We discussed the versatility among polishing wheels, including diamond and ceramic options, each suited for specific tasks and stone types. This range ensures that practitioners can achieve desired finishes tailored to the unique characteristics of each gemstone.
- Material Matters: The choice of materials in polishing wheels significantly impacts the effectiveness of the polishing process. Using the right grit and compounds can result in finishes that are difficult to achieve otherwise.
- Proper Techniques: A significant portion of success in lapidary polishing comes from understanding effective operating techniques, such as timing and pressure applications. These practical skills can be refined over time, making a noticeable difference in finished stones.
Ultimately, selecting the right polishing wheel involves critical assessment of stone type, desired finish, and expertise level, alongside a willingness to adapt techniques as needed. This thoughtful approach ensures the quality of work remains high, fostering a deeper appreciation for the art of lapidary.
Encouragement for Practitioners
If you're navigating the world of lapidary work, it's critical to remember that mastery does not happen overnight. Each gemstone presents a unique puzzle, requiring patience and experimentation with different tools and techniques. Embrace the learning curve; it’s all part of the artistry.
- Start with high-quality wheels that fit your working style, and don't hesitate to experiment with different materials and techniques.
- Pay heed to the subtleties in polishing – subtle adjustments can lead to significant improvements in results.
- Engage with the community, share experiences, and seek advice on platforms like reddit.com or specialized forums to expand your knowledge and skillset.
Taking time to engage with this craft will not only yield better results but will also enhance your enjoyment and understanding of the intricate beauty found in every gem.
"Patience is vital in lapidary work; every stone has a story that unfolds with each polishing movement."
Embrace your journey in lapidary work, and remember, the beauty of the process is as gratifying as the finished pieces. With attention to detail and a willingness to learn, your skills will flourish, ultimately leading to stunning outcomes that truly reflect your dedication.