Unveiling the Fascinating Process of Crafting Talc Powder
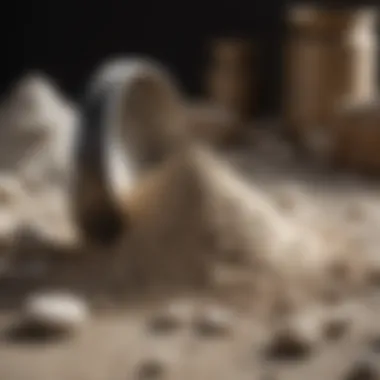
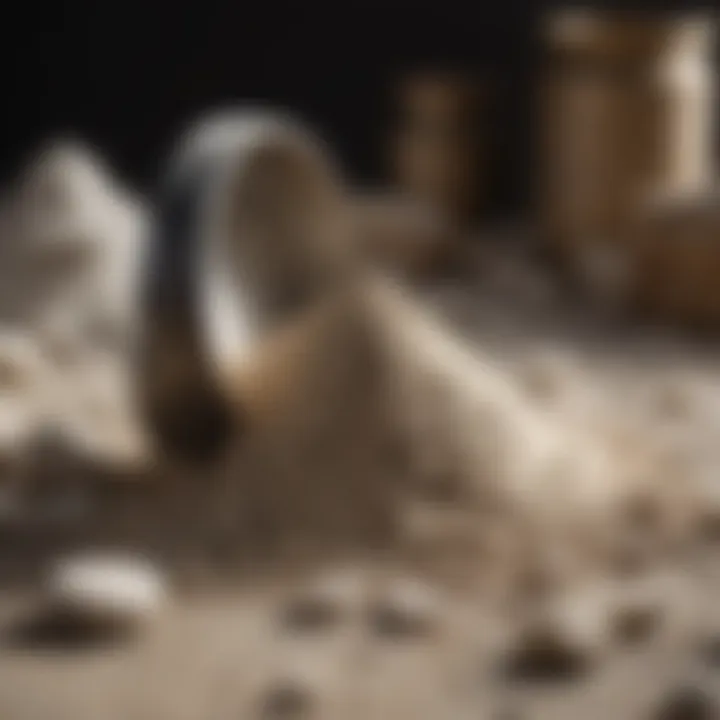
Rock and Fossil Identification
In the realm of talc powder manufacturing, understanding the source material is paramount in ensuring the quality and consistency of the end product. Talc, a metamorphic mineral derived from magnesium minerals and composed of hydrated magnesium silicate, originates from specific rock formations. Identifying the geological formations containing talc deposits is crucial for efficient extraction processes. By discerning the types of rocks where talc is found and mastering the characteristics that distinguish talc-bearing rocks, manufacturers optimize their sourcing strategies to procure high-grade raw materials. Utilizing specialized tools such as rock hammers, hand lenses, and streak plates aids in the identification and differentiation of talc-rich ores from surrounding minerals.
Extraction Techniques
Once the talc-bearing rocks have been identified and acquired, the extraction process commences. Mineralogists and geologists work in tandem to locate prime talc-rich sites, often situated in metamorphic terrain. Through controlled blasting and excavation techniques, raw talc is unearthed and transported to processing facilities for further refinement. The extraction phase calls for adherence to stringent safety protocols to safeguard operatives and the environment from potential hazards. Techniques such as hand sorting and mechanical separation are employed to isolate talc from accompanying minerals efficiently, setting the stage for subsequent processing stages.
Refinement and Processing
Upon extraction, raw talc undergoes a series of meticulous steps to purify and enhance its properties, transforming it into the coveted talc powder. The refinement process involves grinding the talc into fine particles, followed by purification methods to eliminate impurities and enhance brightness and purity levels. Utilizing state-of-the-art processing technologies, manufacturers achieve the desired particle size distribution and chemical composition crucial for diverse industrial applications. Quality controls are implemented at every stage to ensure the final talc powder meets stringent industry standards and customer specifications.
Applications and Market Trends
The versatility of talc powder transcends industries, finding application in sectors such as cosmetics, plastics, ceramics, and pharmaceuticals. Its unique properties, including softness, lubricity, and chemical inertness, make talc a sought-after ingredient in various products. The market trends for talc powder reflect its indispensable nature, with growing demand for high-quality talc across global markets. Market dynamics, regulatory considerations, and technological advancements play a pivotal role in shaping the future landscape of the talc powder industry, driving innovation and sustainability practices.
Conclusion
The journey of talc powder from rock to refined product is a testament to the delicate balance between nature's bounty and scientific ingenuity. By unraveling the intricate process of manufacturing talc powder, we gain a profound appreciation for this versatile mineral's significance across multiple sectors. As we look towards the future, trends indicate a continued reliance on talc powder for its exceptional properties and myriad applications, underscoring its enduring value in an ever-evolving industrial landscape.
Introduction to Talc Powder
In the vast realm of industrial minerals, talc powder stands out as a versatile and essential component with a myriad of applications. This article serves as a guiding light into the intricate process of manufacturing talc powder, unraveling the layers of complexity and precision involved in its production. Understanding the significance of talc powder sets the stage for a detailed exploration of its journey from raw form to refined product. From its unique physical and chemical properties to its industrial importance, talc powder holds a prominent place in various sectors.
Understanding Talc as a Mineral
Talc, a hydrated magnesium silicate mineral, is characterized by its softness, smoothness, and pearly luster. As one of the softest minerals on earth, talc possesses lubricating and anti-sticking properties that make it highly valuable in industrial processes. Its lamellar structure allows it to be easily ground into a fine powder, ideal for a wide range of applications. Moreover, talc's heat resistance and chemical inertness further enhance its suitability for diverse uses.
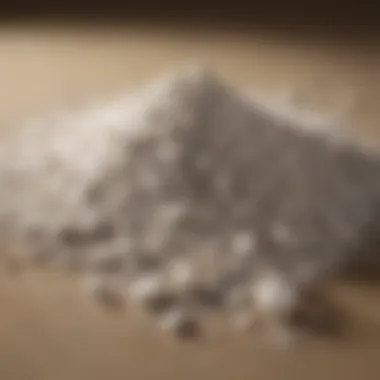
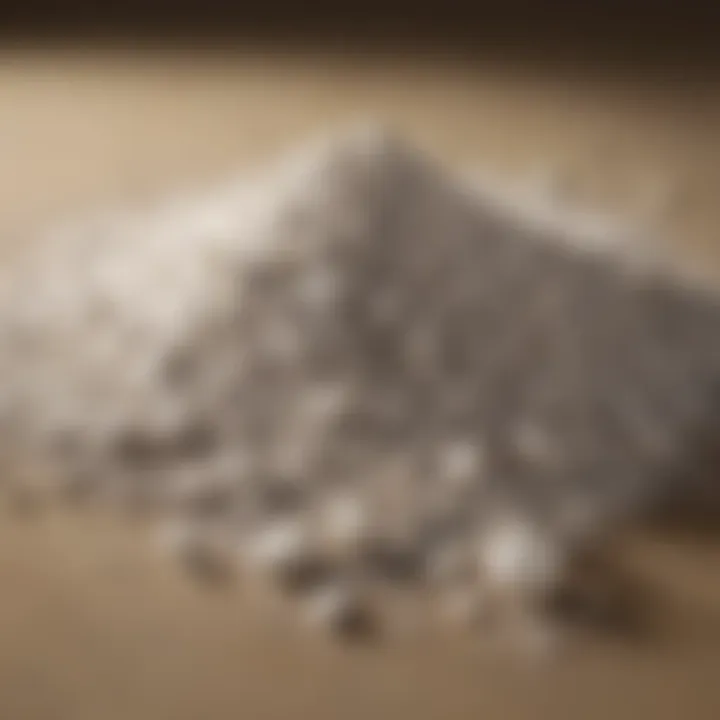
Importance and Applications of Talc Powder
The significance of talc powder spans across industries such as cosmetics, plastics, pharmaceuticals, and ceramics. In the cosmetics industry, talc serves as a vital ingredient in products like powders and blushes, providing a silky-smooth texture and absorbent properties. In plastics, talc acts as a reinforcing filler, enhancing mechanical properties and dimensional stability. Additionally, talc powder is integral to pharmaceutical formulations, where it serves as an excipient in tablets and powders.
Mining and Extraction of Raw Talc
In the realm of talc powder production, the mining and extraction of raw talc play a pivotal role in setting the foundation for the entire manufacturing process. Understanding the significance of this initial phase is crucial to appreciating the journey from natural deposits to a refined, versatile product ready for industrial applications.
Locating Talc Deposits
The first step in the extraction process involves identifying and locating viable talc deposits. This task demands a meticulous approach, as talc deposits are typically found in metamorphic rock formations created under specific geological conditions. Geologists and mining experts employ various geological surveys and mapping technologies to pinpoint areas rich in talc minerals. Factors such as the geological structure, mineral composition, and proximity to existing infrastructure are carefully assessed to ensure an efficient extraction process.
Methods of Extracting Talc Ore
Once the talc deposits are identified, the extraction of talc ore commences through a series of specialized techniques. Open-pit mining and underground mining are the two primary methods employed, each offering distinct advantages based on the deposit's depth, size, and surrounding environment. Open-pit mining, suitable for shallow deposits, involves the removal of overlying soil and rock to access the talc ore beneath. Conversely, underground mining is utilized for deeper deposits, requiring shafts and tunnels to extract the talc ore safely.
These extraction methods require a harmonious blend of expertise, technology, and environmental considerations to extract the raw talc effectively while minimizing ecological impact. By adhering to stringent extraction practices, the mining and extraction of raw talc pave the way for the subsequent processing stages, ensuring the quality and sustainability of talc powder production.
Processing of Talc Ore
In the realm of talc powder manufacturing, the processing of talc ore serves as a vital stage that contributes significantly to the quality and characteristics of the final product. This section delves deep into the essential process of transforming raw talc ore into a refined form ready for further micronization and conversion. Understanding the nuances of how talc ore is processed is fundamental to grasping the impeccable nature of talc powder found in various industrial applications.
Crushing and Grinding of Talc Ore
Crushing and grinding of talc ore signify the initial steps in the progression towards creating high-grade talc powder. The process commences with the extraction of talc ore from its natural deposits, progressing to crushing machinery that breaks down the ore into smaller fragments. Subsequently, grinding machines further pulverize the ore into a fine consistency, ensuring uniform particle size distribution. This meticulous process is imperative in achieving the desired texture and reactivity of the final talc powder product. Engineers and technicians oversee this phase meticulously, adhering to precise parameters to guarantee the optimal physical properties of the powdered talc.
Sorting and Purification of Talc
Once the talc ore is finely ground, the next crucial step involves sorting and purifying the material to eliminate impurities and enhance its chemical composition. Through advanced sorting techniques, contaminants are effectively removed, promoting the purity and quality of the talc powder. Purification procedures involve various chemical treatments and filtration processes to enhance the talc's brightness, whiteness, and clarity. This phase demands rigorous quality control measures to deliver talc powder of superior quality, meeting the stringent standards of industries ranging from pharmaceuticals to cosmetics.

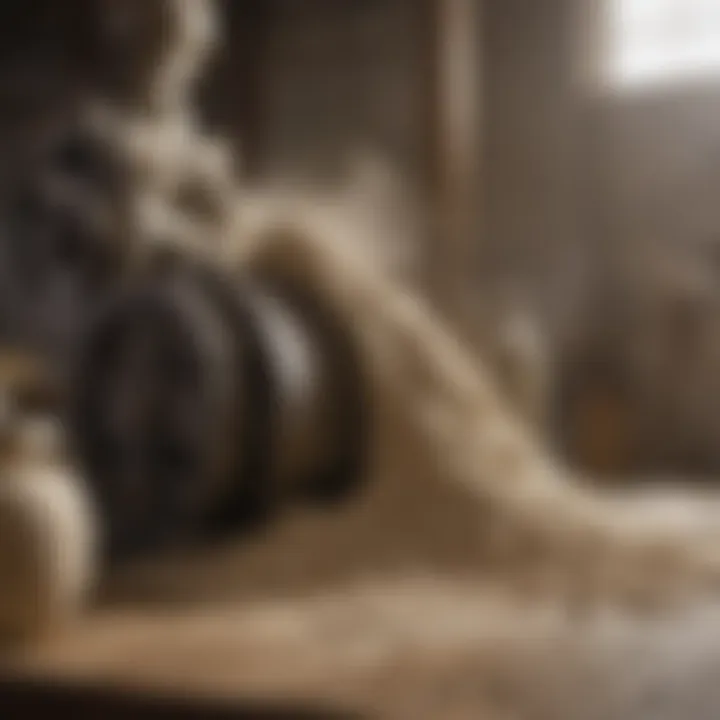
Conversion to Talc Powder
In the realm of talc powder production, the stage of conversion holds paramount significance. This pivotal phase marks the transition from processed ore to the fine, powdery substance widely utilized across diverse industries. The conversion process encapsulates a series of meticulously orchestrated steps, each contributing to the refinement and enhancement of the final product. With meticulous care and precision, the conversion to talc powder sets the foundation for the quality and applicability of the end product.
The conversion to talc powder is an intricate procedure that involves various essential elements. One of the key components of this stage is the grinding and micronization process. Through grinding, the talc ore is finely pulverized into minute particles, ensuring a uniform and consistent texture. Micronization further refines the talc particles, reducing them to a precise size that meets industry specifications. This dual approach not only enhances the functional properties of talc powder but also optimizes its performance in different applications.
Furthermore, when considering the benefits of the conversion process to talc powder, it is imperative to highlight its role in enhancing the mineral's physical and chemical characteristics. By undergoing grinding and micronization, talc acquires improved fineness and homogeneity, leading to enhanced dispersion and absorption properties. This enhanced quality makes talc powder a preferred choice in industries such as cosmetics, pharmaceuticals, and plastics, where uniformity and purity are paramount.
In addition to the technical aspects, considerations about the conversion to talc powder include the optimization of production efficiency and cost-effectiveness. Manufacturers strive to fine-tune their processes to ensure maximum yield and minimal wastage during conversion. Implementing precise particle size control measures and quality checks at each stage of the conversion process is indispensable to maintain the integrity and consistency of the final talc powder product. By prioritizing these considerations, producers can offer high-quality talc powder that meets the stringent standards of various industrial sectors.
Quality Control Measures
Quality control measures play a pivotal role in ensuring that talc powder produced adheres to strict standards of purity and quality. In the context of this article on the manufacturing process of talc powder, quality control measures encompass a variety of protocols and checks that are integrated at various stages of production.
One of the key elements of quality control measures is the rigorous testing conducted to verify the purity and fineness of the talc powder. By analyzing the composition of the powder and assessing its particle size distribution, manufacturers can guarantee that the final product meets industry specifications. This meticulous attention to detail not only enhances the overall quality of the talc powder but also cultivates trust among consumers and industries relying on this mineral for their applications.
Moreover, quality control measures serve as a safeguard against any potential contaminants that could compromise the efficacy and safety of the talc powder. Through systematic quality checks and continuous monitoring, manufacturers can identify and rectify any deviations from the desired composition, ensuring consistency and reliability in the final product. This proactive approach underscores the importance of maintaining high standards throughout the manufacturing process.
In the realm of talc powder production, embracing quality control measures is synonymous with upholding integrity and excellence in every batch manufactured. The benefits of prioritizing quality control extend beyond meeting regulatory requirements; they embody a commitment to delivering superior talc powder that meets the diverse needs of industries ranging from cosmetics to pharmaceuticals. By integrating quality control measures seamlessly into the manufacturing process, producers can affirm their dedication to precision and customer satisfaction.
Testing for Purity and Fineness
Testing for purity and fineness stands as a critical aspect of quality control measures within the realm of talc powder manufacturing. It involves a series of sophisticated analyses and evaluations aimed at assessing the chemical makeup and particle size distribution of the talc powder.
The testing process typically entails conducting in-depth examinations to measure the purity of the talc powder, ensuring that it meets stringent standards for industrial applications. By subjecting the powder to comprehensive purity tests, manufacturers can validate its suitability for various end uses, ranging from plastics to ceramics.
Furthermore, testing for fineness involves scrutinizing the particle size distribution of the talc powder, a factor that directly influences its performance in different applications. Whether micronizing the powder to achieve a specific particle size or verifying its uniformity across batches, evaluating fineness is crucial for maintaining consistency and efficacy.
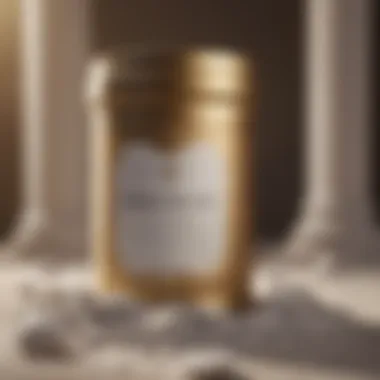
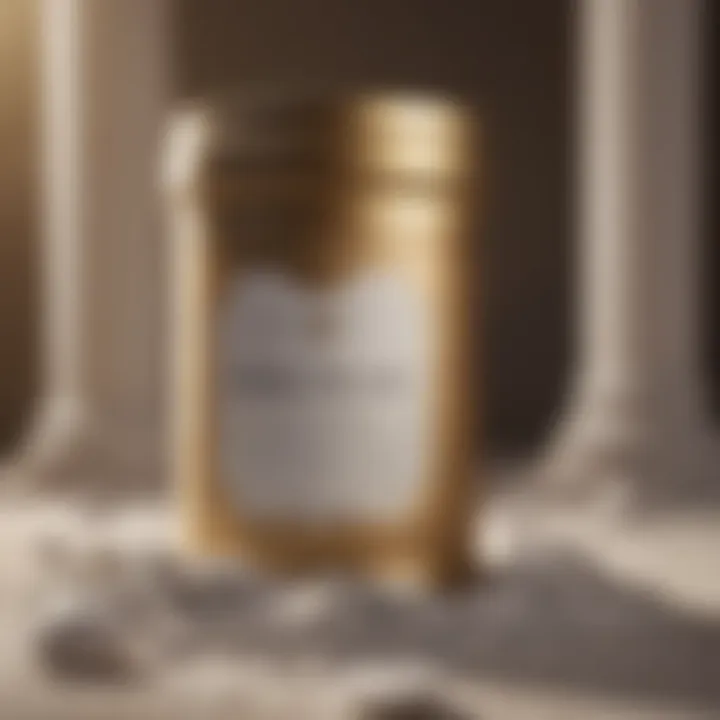
By prioritizing testing for purity and fineness, manufacturers can ascertain the quality of their talc powder, instilling confidence in consumers and fostering a reputation for reliability. This emphasis on rigorous testing not only ensures regulatory compliance but also underscores a commitment to excellence and precision in the production of talc powder.
Packaging and Distribution
Packaging and distribution play a pivotal role in the overall process of manufacturing talc powder. The meticulous processes involved in packaging and ensuring efficient distribution are crucial in maintaining the quality and integrity of the talc powder as it reaches end-users and various industries. Packaging is not merely about containment; it is a strategic component that contributes to safeguarding the product while facilitating its transportation and storage.
Packaging Process of Talc Powder
The packaging process of talc powder involves a series of carefully orchestrated steps to preserve the product's quality and properties. From selecting the appropriate packaging materials to implementing standardized packing procedures, every detail matters. The packaging must not only be durable and tamper-resistant but also user-friendly for easy handling and use. Labels providing essential information such as product specifications, usage instructions, and safety guidelines are affixed to enhance clarity for the end-users.
Logistics and Supply Chain of Talc Products
The logistics and supply chain management of talc products are intricate operations that require seamless coordination and precision. Efficient logistics ensure timely delivery of talc powder to various destinations while minimizing the risk of damage or contamination. Supply chain management involves overseeing the entire journey of talc products from production facilities to distribution centers and ultimately to the end-consumers. Utilizing advanced tracking technologies and optimized transportation routes streamline the process, reducing costs and enhancing customer satisfaction.
Environmental Impact and Sustainability
The topic of environmental impact and sustainability within the realm of talc powder manufacturing is of paramount importance. As industries continue to expand globally, the need to address the environmental repercussions of extracting and processing talc has become increasingly crucial. Sustainability in talc production involves minimizing the ecological footprint left by mining activities and ensuring that the process remains eco-friendly throughout.
One of the key elements to consider regarding the environmental impact is the preservation of natural habitats and ecosystems where talc deposits are located. Responsible mining practices are not only about extracting the mineral efficiently but also about mitigating any negative effects on the surrounding environment. This includes biodiversity conservation, soil protection, and water resource management to uphold a sustainable balance.
Moreover, sustainability in talc powder manufacturing extends to energy consumption and reducing greenhouse gas emissions. Implementing cleaner technologies and optimizing production processes can significantly decrease the carbon footprint associated with talc extraction and processing. By investing in renewable energy sources and improving efficiency, companies can minimize their environmental impact and contribute to a greener future.
Efforts towards recycling and reusing talc waste play a crucial role in enhancing the sustainability of talc production. Instead of disposing of by-products and waste materials, recycling initiatives aim to transform these materials into useful inputs for other industries, thus reducing overall waste generation. By promoting a circular economy approach, the talc industry can maximize resource utilization and minimize environmental harm.
Conclusion
In the realm of talc powder manufacturing, the Conclusion serves as the keystone that solidifies the understanding gleaned from this intricate process. By delving into the minutiae of the production journey, we gain a profound appreciation for the meticulous craftsmanship involved. The Conclusion encapsulates not only the steps undertaken from raw extraction to the final refined form but also highlights the significance of quality control measures in ensuring a superior product. As we navigate through this article, it becomes apparent that the Conclusion acts as the insightful reflection point, emphasizing the intersection between traditional methods and technological advancements in the talc powder industry.
Summary of the Talc Powder Production Process
Unveiling the complexity behind the production of talc powder, this article has meticulously detailed every facet of the process. From the initial mining and extraction stages to the rigorous refining procedures, each step plays a crucial role in enhancing the quality and purity of talc powder. The Summary succinctly encapsulates the extensive journey undergone by talc ore to transform into the fine powder that finds versatile applications across industries. By comprehensively outlining the progression from ore to powder, readers will gain a holistic understanding of the thorough craftsmanship and attention to detail embedded in the talc powder production process.
Future Trends in Talc Powder Manufacturing
As the talc powder manufacturing landscape continues to evolve, it is essential to forecast the future trends that will shape this industry. From technological innovations streamlining production processes to heightened emphasis on sustainable practices, the future of talc powder manufacturing promises advancements that cater to both quality and eco-conscious demands. By anticipating market shifts towards eco-friendly materials and sustainable sourcing, manufacturers can adapt their production methods to align with consumer preferences and regulatory standards. The trajectory of future trends aims to not only elevate the efficiency of talc powder manufacturing but also underscore the industry's commitment to environmental responsibility and product innovation.