Mastering the Art of Crafting Metal Casting Molds: An In-Depth Guide
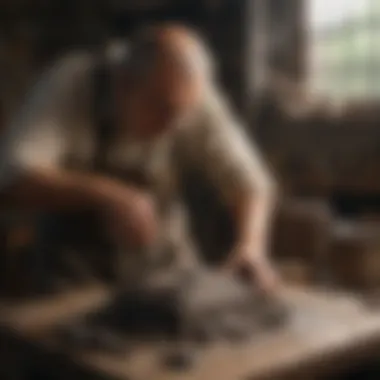
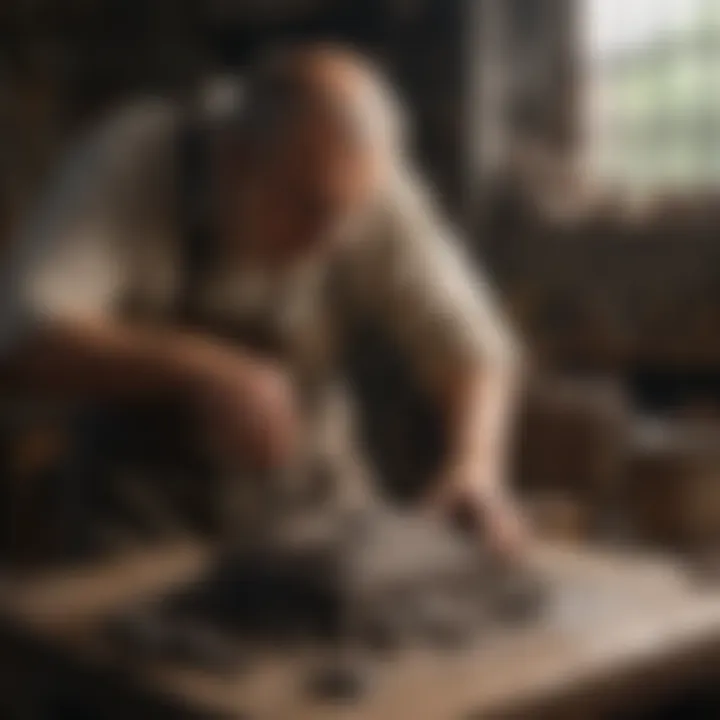
Rock and Fossil Identification
When delving into the intricacies of creating a metal casting mold, understanding various types of rocks and fossils becomes fundamental. Identifying key characteristics, such as texture, color, and composition, is crucial in this process. Utilizing specialized tools like hammers, chisels, and magnifying glasses aids in precise identification.
Collecting Tips and Techniques
In the realm of metal casting mold creation, collecting raw materials is a vital step. Implementing best practices like thorough examination of the material quality and sourcing from reputable suppliers ensures the mold's integrity. Identifying prime sites with optimal rock and mineral deposits enhances the quality of the mold. Adopting safe methods for specimen extraction promotes efficiency and safety throughout the collection process.
Preservation and Display
Preservation methods play a significant role in maintaining the integrity of metal casting molds. Techniques such as sealing in a controlled environment or using protective coatings safeguard the mold from degradation. Adopting proper storage practices, including storing molds in a dry and cool environment, prolongs their lifespan. Consider innovative display ideas to showcase the intricacies of metal casting molds, creating an aesthetically pleasing exhibition.
Geological Insights
Exploring geological formations sheds light on the origin of the materials used in metal casting molds. Investigating the historical significance of rocks and fossils provides a deeper understanding of their relevance in metalworking. Studying notable discoveries in the field offers insights into how these findings have shaped the art of metal casting mold creation.
Introduction to Metal Casting Mold
In the realm of manufacturing and metallurgy, the process of creating metal casting molds stands as a foundational technique that underpins the production of intricate and precise metal components. This crucial initial phase sets the stage for the entire casting process, dictating the final quality and intricacy of the metal piece being forged. Understanding the nuances of metal casting molds is essential for manufacturers, artisans, and enthusiasts seeking to craft bespoke metal objects with precision and finesse.
One of the primary aspects highlighted in the Introduction to Metal Casting Mold is the significance of mold design in influencing the outcome of the casting process. The structural integrity, cooling rate, and intricacy of the final metal product are heavily dependent on the design of the mold. By delving into the fundamentals of mold design, individuals can optimize their casting process, minimize defects, and elevate the overall quality of their finished metal pieces.
Moreover, the Introduction section serves as a gateway to exploring the various molding techniques and materials used in the creation of metal casting molds. From traditional sand casting to advanced investment casting methods, each technique offers unique advantages and challenges that individuals must navigate in their mold-making journey. Understanding these techniques equips practitioners with the knowledge to select the most suitable approach for their specific metal casting requirements.
Additionally, the Introduction acts as a precursor to unraveling the intricate principles of mold making, such as parting lines, draft angles, and the role of cores and cavities in shaping the final metal piece. By grasping these fundamental principles, individuals gain a holistic perspective on the complexities involved in crafting metal casting molds, enabling them to make informed decisions at every stage of the mold-making process.
Understanding the Basics of Mold Making
Understanding the basics of mold making is a pivotal aspect of the metal casting process, forming the foundation for creating intricate and precise metal casting molds. In this article, delving into the fundamentals of mold making is crucial to comprehend the nuanced techniques, materials, and principles involved in crafting durable molds for metal casting operations. By exploring the basics, enthusiasts and professionals gain a profound understanding of the core concepts that govern successful mold production.
Types of Molding Techniques
Sand Casting
Sand casting stands as a cornerstone technique in mold making due to its versatility and effectiveness. The key characteristic of sand casting lies in its ability to accommodate a wide range of shapes and sizes, making it highly suitable for various casting needs. The uniqueness of sand casting stems from its simplicity, cost-effectiveness, and ability to produce intricate molds with relatively low setup requirements. Despite its advantages in flexibility and affordability, the main disadvantage of sand casting lies in its limited dimensional accuracy when compared to other molding methods.
Investment Casting
Investment casting, also known as the lost-wax method, offers unparalleled intricacy and detail in mold creation, making it a favored choice for producing complex metal parts. The key feature of investment casting is its ability to replicate fine details and maintain tight tolerances, crucial for high-precision components. This technique's superiority in producing intricate designs comes at the cost of higher production expenses and longer processing times, which are essential considerations for mold makers.
Lost Foam Casting
Lost foam casting, characterized by its pattern material's quick vaporization during metal pouring, streamlines the mold making process by eliminating the need for pattern removal. The distinctive feature of lost foam casting lies in its ability to produce near-net shape castings with minimal post-processing requirements, saving time and resources. Despite its advantages in intricate design reproduction and material utilization, the drawback of lost foam casting lies in its reliance on precise process control to avoid defects.
Shell Molding
Shell molding, utilizing resin-bonded sand shells for mold creation, offers superior surface finishes and dimensional accuracy for metal castings. The key characteristic of shell molding lies in its capacity to produce smooth and precise molds suitable for high-performance applications. The unique feature of shell molding is its efficient mold assembly process and exceptional mold strength, ensuring consistency in final castings. However, the main disadvantage of shell molding is its higher material and equipment costs compared to traditional molding techniques.
Materials for Mold Making
Silica Sand
Silica sand plays a pivotal role in mold making due to its high refractoriness and compatibility with various metals, making it an ideal choice for casting ferrous and non-ferrous alloys. The key characteristic of silica sand lies in its thermal stability and excellent surface finish properties, essential for producing quality molds. One unique feature of silica sand is its availability in different particle sizes, offering versatility in mold design. Despite its advantages in mold quality and affordability, the main disadvantage of silica sand is its susceptibility to silicosis, highlighting the importance of proper safety measures during handling.
Plaster of Paris
Plaster of Paris contributes to mold making with its ease of use, quick setting time, and cost-effectiveness, making it a popular choice for simple mold applications. The key feature of Plaster of Paris is its ability to create detailed molds with minimal equipment requirements, suitable for small-scale casting projects. One unique aspect of Plaster of Paris is its ability to absorb moisture from the mold cavity, aiding in smoother castings. However, the disadvantage of Plaster of Paris lies in its lower heat resistance compared to refractory materials, limiting its application in high-temperature casting processes.
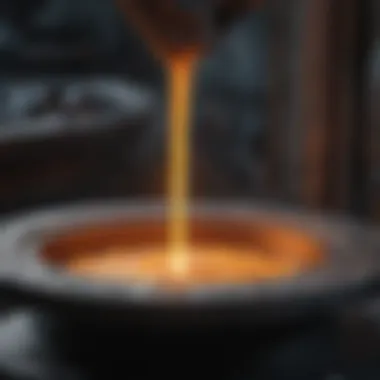
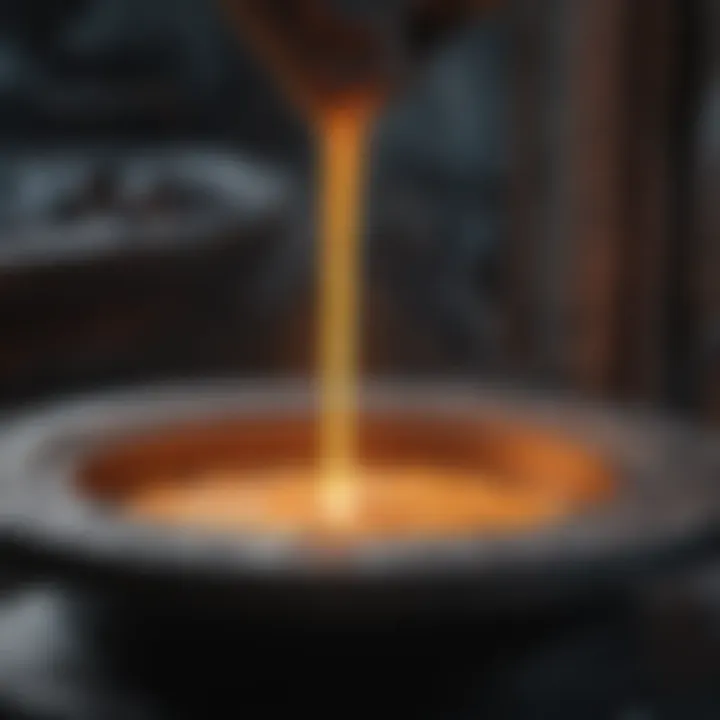
Graphite
Graphite serves as a premium mold material due to its high thermal conductivity, lubricity, and chemical stability, making it an excellent choice for intricate and high-precision applications. The key characteristic of graphite lies in its ability to withstand extreme temperatures and diverse molten metals, essential for producing durable molds. The unique feature of graphite is its self-lubricating properties, reducing mold wear and ensuring smooth metal flow during casting. Despite its advantages in high-temperature applications and mold longevity, the main disadvantage of graphite lies in its higher cost compared to conventional mold materials.
Refractory Ceramics
Refractory ceramics offer exceptional heat resistance, chemical inertness, and dimensional stability, making them ideal choices for high-temperature metal casting processes. The key characteristic of refractory ceramics is their ability to withstand extreme thermal shocks and corrosive environments, ensuring reliable mold performance in demanding casting applications. A unique feature of refractory ceramics is their customizable composition, allowing for tailored properties based on specific casting requirements. However, the main disadvantage of refractory ceramics lies in their brittleness and higher susceptibility to mechanical stress, necessitating careful handling during mold preparation.
Principles of Mold Design
Parting Line
The parting line in mold design marks the boundary between mold halves, influencing casting quality and ease of mold assembly. The key characteristic of the parting line lies in its role in defining part geometry and aiding in establishing mold integrity. One unique feature of the parting line is its impact on material flow during casting, affecting the final part's surface finish. Despite its advantages in facilitating mold separation and assembly, the main disadvantage of the parting line lies in potential flash formation and surface imperfections along the mold split lines.
Draft Angle
Draft angles in mold design are crucial for facilitating pattern removal and preventing part damage during demolding, enhancing overall casting quality. The key characteristic of draft angles lies in their tapering surfaces, allowing for smoother pattern ejection and reducing frictional resistance. One unique feature of draft angles is their contribution to minimizing tool wear and extending mold longevity. Despite its advantages in easing pattern removal and reducing production costs, the main disadvantage of draft angles lies in potential design complexity and material waste in part fabrication.
Cores and Cavities
Cores and cavities are essential components of mold design, forming internal features and geometries within the casting mold. The key characteristic of cores and cavities lies in their role in creating internal part details and shaping the final casting. One unique feature of cores and cavities is their modular design, enabling intricate part geometries and reducing overall mold complexity. Despite their advantages in enhancing casting accuracy and design flexibility, the main disadvantage of cores and cavities lies in the added complexity and assembly time required for multi-part molds.
Gating and Risers
Gating and risers in mold design are critical for controlling metal flow, solidification, and part quality during casting operations. The key characteristic of gating and risers lies in their function of directing molten metal into the mold cavity and preventing defects like shrinkage and porosity. One unique feature of gating and risers is their adaptive design, allowing for customized sprue and runner configurations based on part geometry and metal characteristics. Despite their advantages in optimizing metal flow and promoting sound castings, the main disadvantage of gating and risers lies in the potential for misruns and inconsistencies if improperly designed.
Step-by-Step Process of Making a Metal Casting Mold
In this section, we will delve into the critical aspect of the metal casting process: the step-by-step procedure of creating a metal casting mold. This stage is paramount in the overall production process as it sets the foundation for the final product. By understanding the intricacies of each step involved in creating the mold, enthusiasts and professionals gain a comprehensive insight into the meticulous craftsmanship required for successful metal casting.
The importance of the step-by-step process lies in its precision and attention to detail. Each stage, from pattern creation to metal pouring, plays a crucial role in determining the quality and integrity of the final cast product. By following a systematic approach, manufacturers ensure consistency and accuracy in their mold-making, resulting in superior metal castings. This section will outline the key elements, benefits, and considerations essential for mastering the art of making metal casting molds.
Pattern Creation
Designing the Pattern
Designing the pattern is a fundamental step in mold-making that entails creating a replica of the desired final product. The accuracy and intricacy of the pattern design directly impact the quality of the mold and, subsequently, the casting. By meticulously crafting the pattern to exact specifications, manufacturers can achieve precise outcomes without compromising on intricacy.
The advantage of designing the pattern lies in its ability to serve as a blueprint for the mold, guiding the subsequent stages of the casting process. Through innovative pattern design, manufacturers can not only replicate complex shapes and details but also optimize the mold for efficient metal flow and solidification. However, the complexity of pattern design may pose challenges in intricate mold geometries, requiring advanced expertise and tools for successful implementation.
Selecting Pattern Materials
Selecting the appropriate materials for pattern-making is critical to achieving high-quality molds and castings. The chosen materials must exhibit dimensional stability, heat resistance, and ease of handling to ensure accurate replication during casting. Common materials include wood, plastic, and metal, each offering unique properties that cater to specific casting requirements.
The key advantage of selecting pattern materials lies in their impact on the final mold's durability and surface finish. Optimal material choice minimizes pattern distortion during mold preparation and allows for precise reproduction of intricate details. However, material selection must consider factors such as cost, tooling complexity, and stability to balance performance and feasibility in mold-making processes.
Pattern Assembly
Pattern assembly encompasses the integration of individual pattern components to form a complete and functional template for the mold. This stage requires meticulous alignment and bonding to ensure uniformity and structural integrity within the pattern. By meticulously assembling pattern elements, manufacturers can eliminate potential defects and inefficiencies in the final casting.
The advantage of pattern assembly lies in its role in consolidating multiple pattern components into a cohesive unit ready for mold creation. Through strategic assembly techniques, manufacturers can streamline the mold-making process, enhancing efficiency and accuracy. However, challenges may arise in intricate assembly configurations, necessitating advanced skills and tools to achieve optimal results.
Mold Preparation
Molding Flask Setup
The setup of the molding flask is a critical aspect of mold preparation that dictates the mold's overall structure and support. The flask serves as a containment vessel for the mold material, providing stability and shape definition during the molding process. Proper flask setup ensures uniform mold density and minimizes deformation risks during casting.
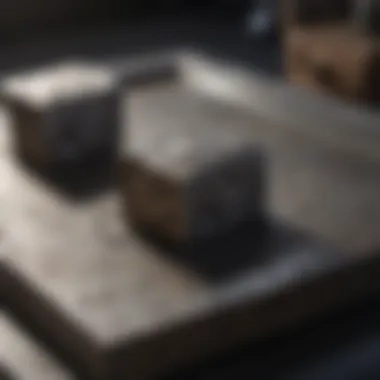
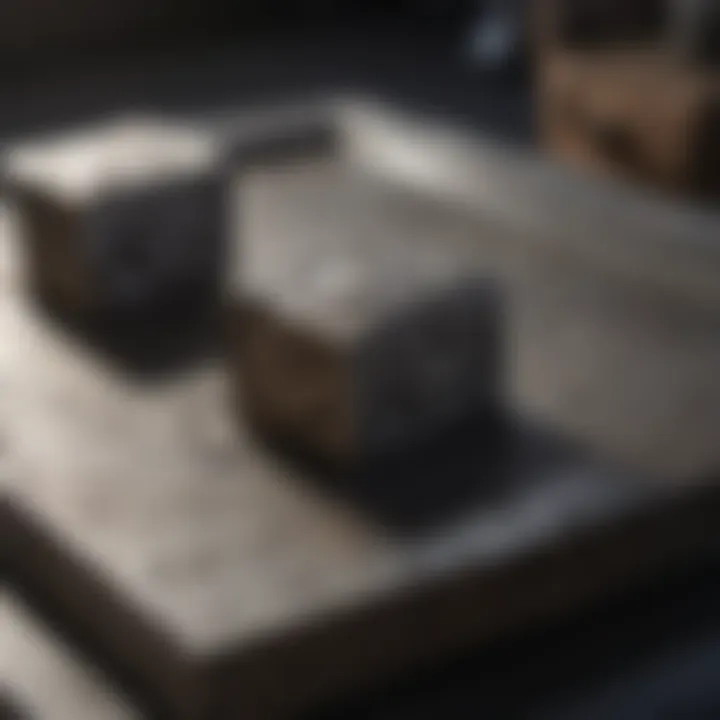
The key characteristic of molding flask setup lies in its ability to create a controlled environment for mold formation, essential for preserving intricate pattern details. By establishing a secure flask configuration, manufacturers can enhance mold stability and facilitate efficient material compaction. However, flask setup complexity and size scalability may present challenges in accommodating diverse casting requirements.
Flask Coating
Flask coating refers to the application of a protective layer on the internal surfaces of the mold cavity to prevent adhesion and facilitate mold release. Coatings such as graphite, ceramic, or refractory materials enhance mold durability and aid in achieving smooth casting surfaces. Proper flask coating promotes optimal metal flow and minimizes defects in the final casting.
The advantage of flask coating lies in its ability to optimize mold surface characteristics, such as porosity and thermal insulation, crucial for successful casting outcomes. By selecting suitable coating materials and techniques, manufacturers can prolong mold lifespan and improve casting quality. However, variations in coating thickness and application methods may impact coating uniformity and consistency across the mold surface.
Mold Curing
The mold curing process involves allowing the assembled mold to set and solidify before proceeding with metal pouring. Curing methods, such as air drying or heat treatment, promote mold strength and dimensional stability essential for withstanding molten metal temperatures. Proper curing ensures mold integrity and minimizes risks of cracking or distortion during casting.
The key characteristic of mold curing lies in its impact on the mold's mechanical properties and thermal resistance, crucial for successful metal casting. By implementing appropriate curing techniques, manufacturers can enhance mold durability and optimize casting performance. However, variations in curing time and conditions may affect mold strength and overall casting quality.
Metal Pouring and Casting
Furnace Operation
Furnace operation plays a pivotal role in the metal casting process by facilitating the melting and casting of metal alloys. The furnace serves as the primary heat source for metal transformation, enabling controlled alloy melting and temperature regulation for casting. Efficient furnace operation ensures uniform metal flow and optimal casting conditions for superior part quality.
The key characteristic of furnace operation lies in its ability to maintain precise temperature control and heating rates essential for different metal alloys. By calibrating furnace settings according to specific alloy requirements, manufacturers can achieve consistent casting results and minimize material wastage. However, furnace operation complexity and energy consumption may pose challenges in balancing cost efficiency and casting performance.
Pouring Techniques
Pouring techniques refer to the methods used to transfer molten metal from the furnace to the mold cavity during casting. Proper pouring techniques involve controlled metal flow and filling strategies to prevent turbulence and air entrapment within the mold. Strategic pouring enhances casting integrity and surface finish for high-quality final products.
The advantage of pouring techniques lies in their direct impact on casting soundness and defect prevention during metal flow. By employing suitable pouring methods, manufacturers can minimize casting flaws such as porosity and metal splash, improving overall part quality. However, variations in pouring speed and direction may influence mold filling patterns and casting solidification, requiring precision and expertise for optimal results.
Cooling and Demolding
Cooling and demolding are critical steps following metal pouring, ensuring proper part solidification and mold removal. Controlled cooling rates enable gradual part solidification, reducing internal stresses and enhancing material properties. Demolding techniques, such as vibration or thermal shock, aid in releasing the casting from the mold without damage.
The unique feature of cooling and demolding lies in their role in establishing part geometry and surface finish post-casting. By implementing gradual cooling processes and appropriate demolding strategies, manufacturers can minimize part distortion and surface defects. However, challenges may arise in balancing cooling rates with production timelines, necessitating efficient demolding methods and quality inspection for successful part release.
Advanced Techniques and Considerations
In the realm of metal casting mold creation, understanding advanced techniques and considerations is paramount. These elements play a crucial role in elevating the quality and precision of the final product. By delving into advanced techniques, professionals in the field can explore innovative methods that enhance efficiency and productivity. Moreover, considering various aspects such as material selection, design intricacies, and meticulous execution ensures the successful creation of intricate molds for metal casting. The incorporation of advanced techniques and considerations not only showcases expertise but also paves the way for the implementation of cutting-edge practices in the metal casting industry.
Investment Casting Process
Wax Pattern Creation
The process of wax pattern creation holds significant importance in the investment casting process. This initial step involves the creation of a wax model that replicates the final product before metal casting. The key characteristic of wax pattern creation lies in its ability to capture intricate details and fine features with exceptional precision. This method is a popular choice for its capability to produce complex geometries and smooth surface finishes, making it highly desirable for applications requiring precision and intricacy. However, one drawback of wax pattern creation is its susceptibility to breakage or deformation if not handled with care during the molding process.
Ceramic Shell Building
In the investment casting process, the ceramic shell building technique plays a crucial role in creating a robust mold for metal casting. The key characteristic of ceramic shell building is its ability to withstand high temperatures without deforming or cracking, ensuring the integrity of the mold during the casting phase. This technique is highly beneficial for intricate designs and detailed components, providing excellent dimensional accuracy and surface finish. Despite its advantages, ceramic shell building may involve longer lead times and require skilled craftsmanship for optimal results.
De-Waxing and Casting
De-waxing and casting are integral steps in the investment casting process that involve the removal of the wax pattern and the subsequent casting of molten metal into the ceramic mold. The key characteristic of de-waxing and casting is the transformation of the hollow ceramic mold into a metal component through a precise and controlled casting process. This method offers the advantage of producing intricate and near-net-shape parts with minimal material wastage. However, one challenge of de-waxing and casting is the potential for defects such as porosity or misruns, which require meticulous monitoring and control throughout the process.
3D Printing for Mold Making
Benefits of 3D Printing
Integrating 3D printing technology in mold making presents a myriad of benefits for enhancing efficiency and flexibility in the production process. The key characteristic of 3D printing is its ability to fabricate intricate geometries and customized molds with exceptional speed and accuracy. This additive manufacturing method is a popular choice for its rapid prototyping capabilities, allowing for quick iterations and design modifications. Additionally, 3D printing reduces material waste and energy consumption compared to traditional mold making methods, making it a sustainable solution for intricate mold designs.
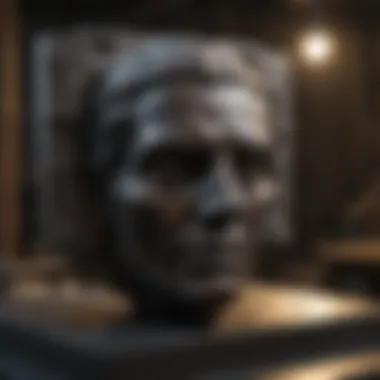
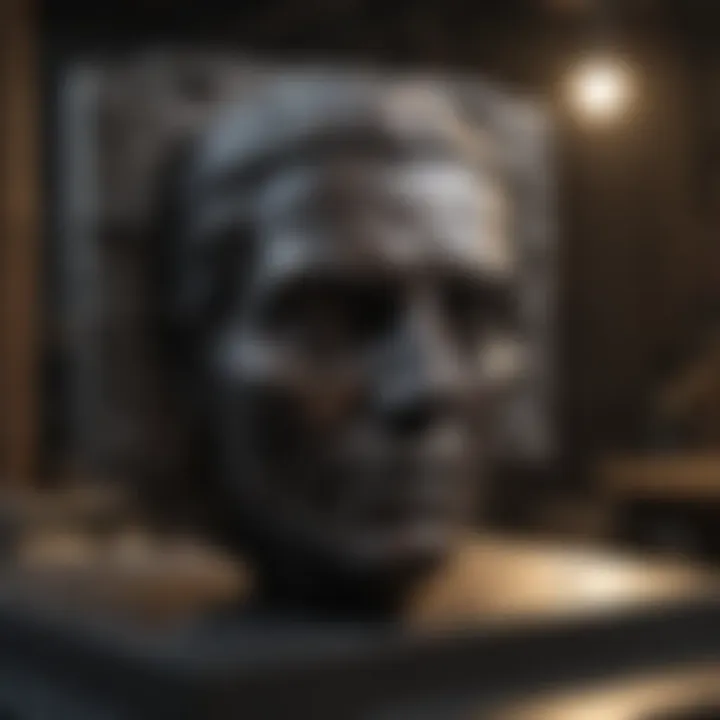
Design Considerations
When employing 3D printing for mold making, considering design intricacies is vital to ensuring the successful fabrication of high-quality molds. The key characteristic of design considerations in 3D printing lies in optimizing geometries for additive manufacturing, including supports, cooling channels, and part orientation. This approach enhances the structural integrity and surface finish of the final mold while minimizing printing time and material usage. However, design considerations may involve additional pre-processing steps and parameter adjustments to achieve the desired mold quality.
Post-Processing Steps
Post-processing steps are essential in finalizing 3D-printed molds to meet dimensional accuracy and surface finish requirements. The key characteristic of post-processing steps is their role in removing support structures, smoothing surfaces, and finishing details to enhance the overall mold quality. This phase often includes techniques such as sanding, polishing, and heat treatment to optimize the mold's performance and appearance. While post-processing steps contribute to refining mold characteristics, they can also prolong the production timeline and introduce additional labor costs, depending on the complexity of the mold design.
Quality Control and Testing
Dimensional Accuracy
Ensuring dimensional accuracy in metal casting molds is paramount for guaranteeing precise and consistent part production. The key characteristic of dimensional accuracy lies in maintaining tight tolerances and geometrical specifications to meet design requirements. This aspect is a beneficial choice for optimizing part functionality and assembly compatibility, especially in industries where precision is critical. However, maintaining dimensional accuracy may pose challenges in controlling shrinkage and distortion during the cooling and solidification stages of the casting process.
Defect Detection
Detecting and addressing defects in metal casting molds is essential for preventing manufacturing inconsistencies and product failures. The key characteristic of defect detection is its ability to identify imperfections such as inclusions, porosity, or surface irregularities that can compromise part quality. This aspect is a popular choice for enhancing product reliability and performance by mitigating defects early in the production cycle. Implementing defect detection measures requires advanced testing techniques and quality control protocols to ensure that molds meet stringent industry standards.
Non-Destructive Testing
W## hile ensuring mold quality, incorporating non-destructive testing methods plays a vital role in evaluating internal integrity and material properties without damaging the mold. The key characteristic of non-destructive testing lies in its non-invasive nature, allowing for comprehensive inspection of mold components using techniques such as ultrasound, x-ray, or eddy current testing. This method offers the advantage of identifying defects or anomalies hidden within the mold structure, enabling corrective actions to be taken before casting operations begin. Despite its advantages, non-destructive testing may require specialized equipment and trained personnel to perform accurate and reliable inspections, adding complexity and cost to the quality control process.
Safety Measures and Best Practices
Safety measures and best practices are crucial elements in the realm of metal casting mold creation. They serve as fundamental pillars in ensuring the well-being of individuals involved in the process. Implementing comprehensive safety measures not only safeguards against potential hazards but also contributes to the efficiency and precision of mold making.
Personal Protective Equipment (PPE)
Safety Glasses
Safety glasses play a vital role in protecting the eyes of individuals working in environments where particles or chemicals may pose a risk. Their impact-resistant lenses shield against debris, dust, and splashes, enhancing safety and visibility. The lightweight and ergonomic design of safety glasses ensures comfort during extended periods of use, making them a popular choice among mold makers. Despite their efficacy, safety glasses may fog up in humid conditions, necessitating occasional adjustments for optimal vision.
Gloves
Gloves are essential in maintaining hand protection while handling materials and tools during mold making. Their non-slip surface enhances grip and dexterity, promoting safe and precise work practices. The durability and flexibility of gloves make them a preferred choice for tasks requiring tactile sensitivity. However, prolonged glove usage may lead to hand perspiration and discomfort, necessitating periodic breaks for ventilation.
Respiratory Protection
Respiratory protection is vital in safeguarding against inhalation of harmful fumes or particulates generated during metal casting mold creation. Respirators equipped with proper filtration systems ensure clean air intake, minimizing the risk of respiratory issues. The adjustable straps and ergonomic design of respiratory protection devices enhance wearer comfort and secure fit. While offering extensive respiratory defense, these devices may feel restrictive over prolonged periods, requiring occasional breaks for comfort and respite.
Workshop Safety Guidelines
Ventilation Systems
Ventilation systems play a critical role in maintaining air quality and temperature within the workspace, promoting a safe and comfortable environment for mold making. Their efficient air circulation capabilities mitigate the accumulation of dust, fumes, and excessive heat, enhancing overall working conditions. The adjustable settings and noise levels of ventilation systems ensure customizable and non-disruptive operation, aligning with diverse workshop requirements. However, prolonged exposure to ventilation noise may lead to fatigue, necessitating intermittent breaks for hearing protection.
Fire Safety Measures
Fire safety measures are paramount in preventing and addressing potential fire hazards that may arise during metal casting mold creation. Fire extinguishers, emergency exits, and fire alarms constitute essential components of a robust fire safety plan, ensuring swift and effective responses to emergencies. The regular maintenance and inspection of fire safety equipment guarantee optimal functionality and readiness in critical situations. While indispensable for workshop safety, fire safety measures demand periodic training and drills for procedural familiarity and swift execution.
Emergency Response Plans
Emergency response plans delineate predetermined protocols and procedures to follow in the event of accidents, injuries, or emergencies within the workspace. These plans outline emergency contacts, evacuation routes, and first aid measures, empowering individuals to act swiftly and decisively during critical situations. Regular review and practice of emergency response plans foster preparedness and efficiency, instilling a culture of safety and accountability within the workshop. Despite their indispensable nature, emergency response plans require ongoing refinement and adaptation to align with evolving safety standards and operational dynamics.
Conclusion
In the intricate world of metal casting mold creation, the Conclusion section serves as the ultimate destination, encapsulating the essence and significance of the entire guide. As we embark on this journey from understanding the basics of mold making to exploring advanced techniques, safety measures, and best practices, the Conclusion acts as the anchor that ties together all the pieces of knowledge acquired along the way. It serves as a place of reflection and consolidation, where we appreciate the artistry and precision required in crafting metal casting molds.
Looking back on the exhaustive details provided in this guide, one can appreciate the meticulous attention to detail involved in each step of the process. From selecting the right materials for mold making to implementing intricate design considerations, every aspect contributes to the successful creation of a metal casting mold. The Conclusion section, therefore, highlights the culmination of efforts, emphasizing the need for practitioners to embrace quality control measures and adhere to best practices to achieve flawless results.
Moreover, the Conclusion section sheds light on the transformative potential of mastering metal casting mold creation. By delving into the nuances of investment casting and utilizing cutting-edge 3D printing technologies, enthusiasts and professionals gain a competitive edge in the industry. This final section acts as a testament to the continuous growth and innovation within the realm of mold making, challenging individuals to push boundaries and explore new horizons.
Ultimately, the Conclusion is not just a mere endpoint; it symbolizes a new beginning for those passionate about metal casting molds. It encourages readers to apply the knowledge garnered from this comprehensive guide to their practical endeavors, fostering a culture of continuous learning and improvement. The insights shared in the Conclusion section pave the way for a future where creativity, skill, and resourcefulness converge to shape the landscape of metal casting mold creation, setting new standards of excellence in the field.
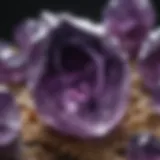
