Unveiling the Top Dremel Choices for Glass Etching Enthusiasts
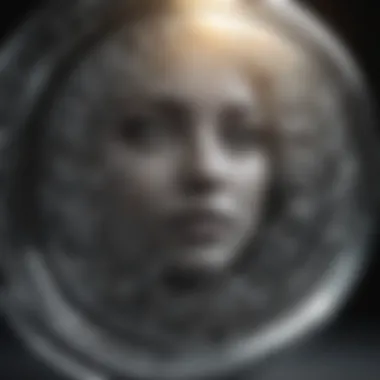
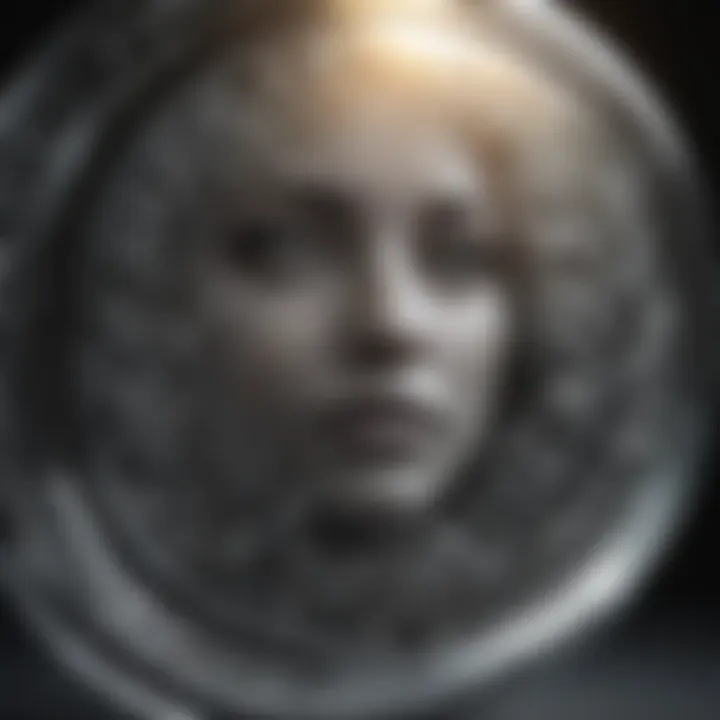
Rock and Fossil Identification
Glass etching entails a meticulous craft that requires attention to detail and the best tools available. When embarking on a glass etching project, utilizing the most suitable Dremel is paramount to achieving refined results. The process involves an intricate dance between the delicate material of glass and the precision of the Dremel tool. Selecting the right Dremel can make all the difference in bringing out the desired patterns and designs on glass surfaces.
Dremel Models and Features
Precision and Control in Glass Etching
Precision and control are crucial elements in glass etching, and the Dremel tool plays a pivotal role in achieving these aspects. The best Dremel for glass etching should provide users with the necessary precision to create intricate designs while offering optimal control for varying depths and speeds. Understanding how different Dremel models excel in precision and control can aid in selecting the ideal tool for achieving desired etching outcomes. Careful consideration of these factors can elevate the quality and intricacy of glass etching projects.
Dremel Attachments for Glass Etching
Introduction
The Art of Glass Etching
Glass etching has a rich historical background, tracing back centuries as an art form that signifies elegance and sophistication. Exploring the History of Glass Etching provides insight into the traditional techniques and patterns that have shaped the way glass is adorned today. Understanding these historical influences lays a solid foundation for appreciating the intricacies of the craft and its enduring popularity among artisans and designers.
When it comes to Techniques and Applications in glass etching, a myriad of innovative approaches and styles can be employed to create stunning visual effects on glass surfaces. From manual hand etching to modern stencil methods, each technique offers unique characteristics and challenges. By exploring the various techniques and applications available, artists can expand their creative horizons and push the boundaries of traditional glass etching norms.
Role of Dremel in Glass Etching
Dremel tools play a pivotal role in glass etching due to their precision and control capabilities. The Precision and Control offered by Dremel tools enable artisans to etch intricate designs with unparalleled accuracy and finesse, enhancing the overall quality of the final product. This level of precision is essential in achieving professional-grade results that meet the high standards of glass etching enthusiasts and collectors worldwide.
The Versatility in Design of Dremel tools further amplifies their value in glass etching applications. With a range of attachments and accessories available, Dremel tools offer endless design possibilities, allowing artists to experiment with various textures, depths, and patterns on glass surfaces. This flexibility in design not only enriches the creative process but also opens up new avenues for artistic exploration and expression.
Purpose of the Article
The primary objective of this article is to aid readers in identifying the Best Dremel for Glass Etching tailored to their specific needs and preferences. By delving into the unique features and performance attributes of different Dremel models, individuals can make informed decisions that align with their glass etching aspirations. This in-depth exploration of Dremel options aims to streamline the selection process, empowering users to unlock their full creative potential and achieve stunning results in their glass etching endeavors.
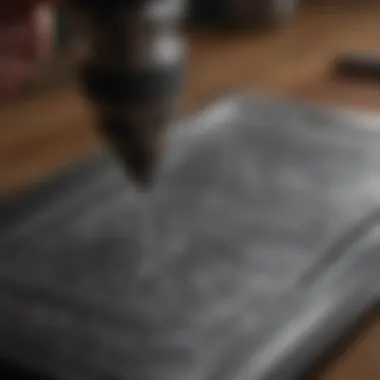
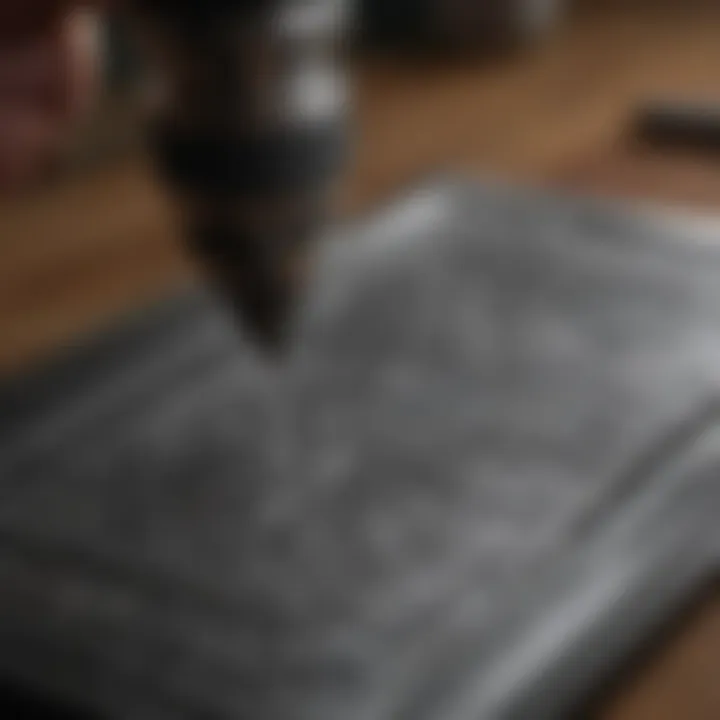
Understanding Glass Etching
Glass etching is a meticulous art form that requires precision and expertise. In this article, we delve into the significance of understanding glass etching to guide readers through this intricate process. By exploring the nuances of glass etching, enthusiasts can unearth the techniques and tools necessary to achieve stunning results in their projects.
Chemical vs. Mechanical Etching
Differences and Considerations
When it comes to etching glass, a key decision individuals face is choosing between chemical and mechanical etching methods. The fundamental disparity lies in the approach: chemical etching involves using substances like acids or creams to create designs, while mechanical etching utilizes tools like the Dremel to carve patterns into the glass. Understanding these differences is crucial as they impact the level of detail, safety considerations, and artistic possibilities of the etching process. Both methods have their merits and drawbacks. Chemical etching offers intricate detailing and controlled results, perfect for fine designs. However, it necessitates caution due to the use of potentially hazardous chemicals. On the other hand, mechanical etching with a Dremel provides versatility and speed in creating patterns but may require more practice to master intricate designs. By comprehending the disparities between chemical and mechanical etching, enthusiasts can tailor their approach to suit their artistic vision.
Safety Precautions
Protective Gear
Safety is paramount when engaging in glass etching, especially when working with chemicals or machinery. Protective gear such as gloves, goggles, and aprons serves as a shield against accidental exposure to harmful substances or glass shards. Incorporating protective gear into the etching process ensures the practitioner's well-being and minimizes potential risks, underscoring the importance of prioritizing safety in creative endeavors. While protective gear safeguards against immediate hazards, proper ventilation is equally indispensable for a safe etching environment. Adequate airflow disperses fumes from chemicals and reduces the risk of inhalation, promoting a healthier workspace. Ventilation systems or working in well-ventilated areas are imperative considerations to fortify safety measures during glass etching procedures.
Tools and Materials
When embarking on a glass etching project, the choice between using etching cream or a Dremel tool significantly influences the outcome. Etching cream offers a chemical-based solution that efficiently etches glass surfaces without the need for intricate hand movements. Conversely, employing a Dremel provides artists with greater control and precision, enabling them to craft intricate designs with ease. Understanding the unique attributes of both etching cream and Dremel tools allows practitioners to select the most suitable method for their creative vision. Moreover, the type of glass utilized in the etching process plays a pivotal role in the final result. Various glass types, such as tempered or annealed glass, offer distinct textures and resistance levels to etching techniques. By familiarizing oneself with the characteristics of different glass types, artists can make informed decisions regarding which glass best complements their desired artistic expression.
Choosing the Best Dremel for Glass Etching
In the realm of glass etching, the selection of the right Dremel tool holds paramount importance. The precision and finesse required in this craft demand a tool that not only offers control but also versatility in design. Choosing the best Dremel for glass etching is pivotal in achieving the desired artistic results. Ensuring the tool's compatibility with various glass types and the specific needs of the etching process is crucial for a successful outcome.
Factors to Consider
Speed Settings
The speed settings on a Dremel tool play a crucial role in glass etching. The ability to adjust the speed allows for intricate detailing and varying depths of etching. High speeds are ideal for precision work, while lower speeds offer more control for delicate designs. The convenience of easily switching between speed settings enhances the user's efficiency and overall performance, making it a popular choice among glass etchers. However, while speed settings provide versatility, improper use may lead to errors in design work or damage to the glass surface.
Ergonomics
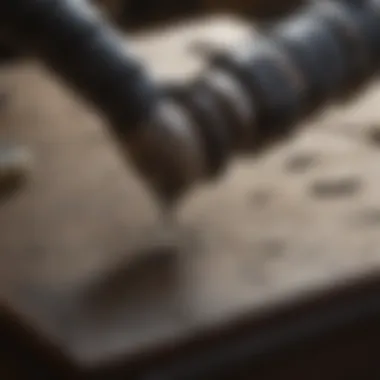
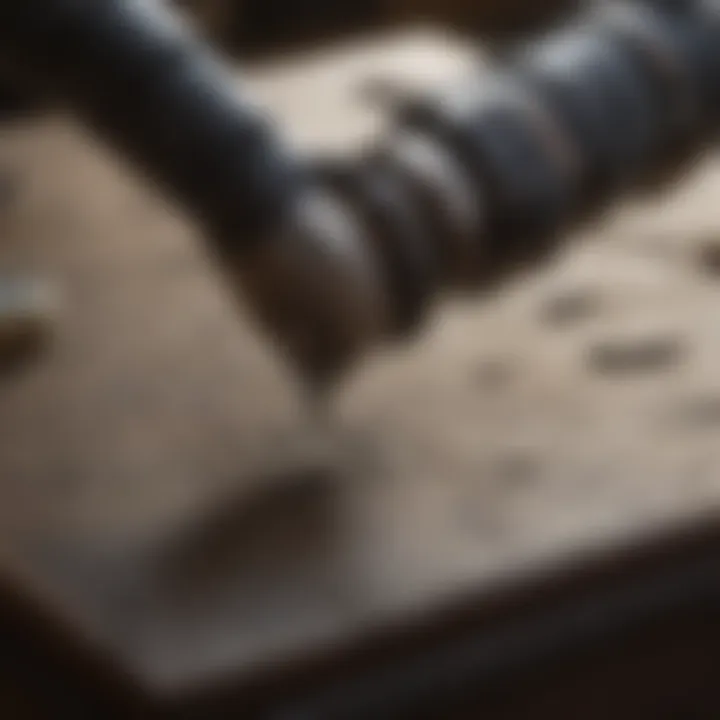
Ergonomics is a key consideration when selecting a Dremel for glass etching. The ergonomic design of a tool ensures user comfort during prolonged use, reducing fatigue and improving precision. A well-designed Dremel fits comfortably in the hand, allowing for better control and maneuverability, ultimately enhancing the quality of the etching work. The ergonomic features of a Dremel contribute to ease of use, making it a preferred choice for glass etchers. Nonetheless, ergonomics alone may not compensate for other essential features needed for successful glass etching.
Top Dremel Models for Glass Etching
Dremel vs. Dremel Lite
When comparing Dremel 4300 and Dremel Lite for glass etching, the decision rests on nuanced differences. The Dremel 4300 offers higher power and a wider range of accessories, making it suitable for intricate and complex etching projects. On the other hand, the Dremel Lite is compact, lightweight, and more user-friendly, catering to beginners or those prioritizing portability. The versatility and power of the Dremel 4300 may outshine the simplicity and ease of use offered by the Dremel Lite, depending on the etcher's specific requirements.
Dremel Micro vs. Dremel Stylo
In the comparison between Dremel Micro and Dremel Stylo for glass etching, distinct features come into play. The Dremel Micro's compact size and precision make it ideal for detailed and intricate designs, offering enhanced control and maneuverability. Conversely, the Dremel Stylo's ergonomic design and comfortable grip provide ease of use for more extended etching sessions. Both models excel in different aspects, with the choice likely dependent on the user's preference for either precision or comfort during glass etching tasks.
Reviews and Comparisons
Pros and Cons
Analyzing the pros and cons of various Dremel models for glass etching helps in making an informed decision. Understanding the advantages, such as versatility in design and power, and potential drawbacks, like intricate upkeep or noise levels, guides users in selecting the most suitable tool for their etching endeavors. By weighing the pros and cons, etchers can ascertain which features align best with their artistic goals and practical requirements.
User Experiences
User experiences with different Dremel models for glass etching offer valuable insights into the tools' performance and suitability for various projects. The firsthand accounts of users highlight aspects like usability, durability, and specific capabilities that may not be evident from technical specifications alone. By delving into user experiences, prospective buyers can gain a comprehensive understanding of how different Dremel models fare in real-world glass etching scenarios, aiding in the decision-making process.
Tips for Successful Glass Etching
Glass etching is a meticulous craft that requires precision and attention to detail. In this article, we will delve into essential tips for successful glass etching, ensuring that every aspiring artist or hobbyist can achieve exquisite results. These tips serve as invaluable guidance, offering insights into the nuances of the process and how to overcome common challenges. Whether you are a beginner or an experienced etcher, incorporating these tips into your practice can elevate your work to new heights.
Practice and Patience
Developing Skills
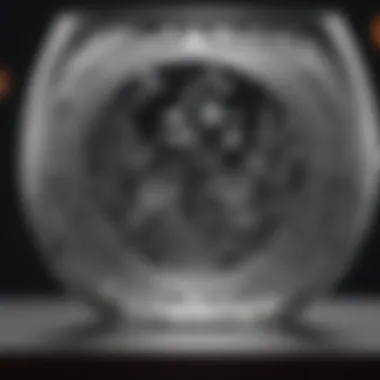
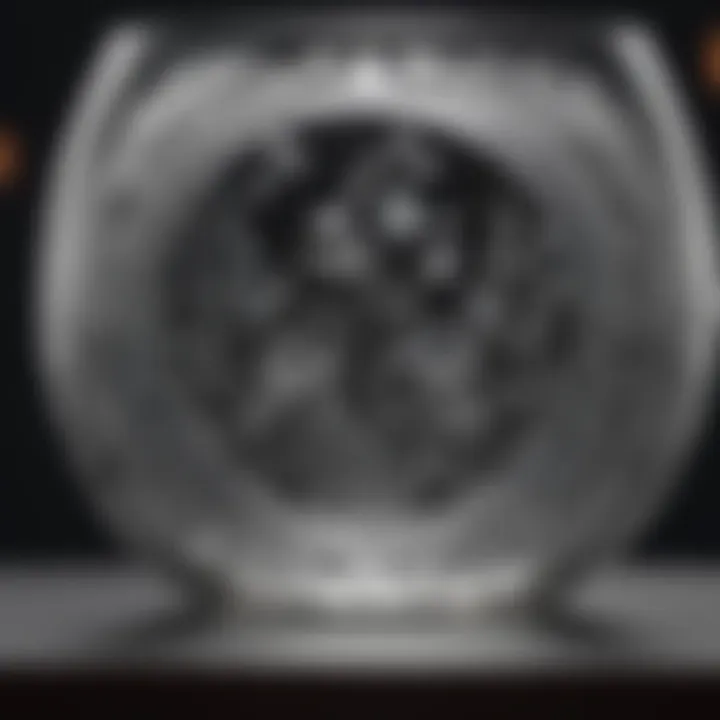
Developing skills in glass etching is a fundamental aspect that contributes significantly to the overall mastery of this art form. The key characteristic of developing skills lies in the consistent practice and refinement of techniques necessary for achieving precision and finesse in glass etching. By dedicating time to honing your skills, you can enhance your ability to create intricate designs and flawless finishes. The unique feature of developing skills is its capacity to nurture creativity and craftsmanship, allowing etchers to express their artistic vision with clarity and artistry. While the process of skill development may require patience and perseverance, the rewards of mastering this craft are immeasurable, making it a vital choice for anyone seeking to excel in glass etching.
Maintenance and Care
Cleaning Dremel Tips
Maintaining the cleanliness of your Dremel tips is crucial for ensuring optimal performance and longevity of your tools. The key characteristic of cleaning Dremel tips is its ability to prevent residue buildup and avoid potential damage to the etching surface. By regularly cleaning your Dremel tips, you can prolong their lifespan and maintain the quality of your etching work. The unique feature of cleaning Dremel tips is its simplicity yet profound impact on the overall etching process. While it may seem like a mundane task, the thorough cleaning of Dremel tips can prevent contamination and ensure consistent results in your glass etching projects. Incorporating this practice into your routine is a wise choice for preserving the efficiency and effectiveness of your tools.
Innovative Techniques
Layering Effects
Layering effects add depth and dimension to glass etching, creating visually stunning designs with intricate detail. The key characteristic of layering effects is their versatility in enhancing the overall aesthetic appeal of etched glass. By incorporating multiple layers into your designs, you can achieve a sense of depth and texture that captivates the viewer's eye. The unique feature of layering effects lies in the creative freedom they provide, allowing artists to experiment with different patterns and textures to create truly unique pieces. While mastering layering effects may require practice and experimentation, the results are well worth the effort, offering endless possibilities for artistic expression and innovation.
3D Etching
3D etching brings a new dimension to glass art, elevating traditional etching techniques to create captivating three-dimensional designs. The key characteristic of 3D etching is its ability to add depth and realism to glass surfaces, making the etched designs more lifelike and engaging. By manipulating light and shadow through strategic etching patterns, artists can bring their creations to life in a way that flat etching cannot achieve. The unique feature of 3D etching is its capacity to push the boundaries of traditional glass etching, opening up a world of possibilities for creating immersive and dynamic artworks. While mastering the intricacies of 3D etching may require patience and skill, the end results speak for themselves, showcasing the power of this innovative technique in the realm of glass artistry.
Conclusion
In the realm of glass etching, the choice of Dremel plays a pivotal role in determining the quality and intricacy of the final artwork. Selecting the best Dremel for glass etching is more than just a decision; it is a crucial step towards achieving precision and control essential for creating exquisite designs. The significance of this process lies in the ability to streamline the etching experience, enabling artists and craftsmen to express their creativity with finesse. By understanding the distinct features and capabilities of various Dremel models, individuals can elevate their glass etching projects to new heights, pushing the boundaries of artistry.
Summarizing Key Points
Impact of Dremel Choice
The impact of selecting the right Dremel for glass etching cannot be understated. It directly affects the artist's ability to execute intricate designs with precision and finesse, reflecting the dedication to craftsmanship and attention to detail. The ideal Dremel choice enhances not only the efficiency of the etching process but also contributes significantly to the overall quality of the finished artwork. By opting for a Dremel model that offers versatility in speed settings and ergonomic design, artisans can unlock new creative possibilities and achieve remarkable results in their glass etching endeavors.
Artistic Possibilities
Exploring the artistic possibilities unlocked by choosing the best Dremel for glass etching opens a world of innovation and creativity. The selected Dremel model acts as a catalyst for artistic expression, enabling artists to actualize intricate designs and delicate patterns with ease. The key characteristic of artistic possibilities lies in the seamless integration of precision and control, allowing craftsmen to push the boundaries of conventional glass etching techniques. By harnessing the unique features of a high-quality Dremel, artists can imbue their projects with unmatched elegance and sophistication, elevating their artistic vision to new dimensions.
Inspiration for Future Projects
Continued Exploration
The spirit of continued exploration fuels the passion for glass etching, inspiring artists to constantly innovate and push artistic boundaries. Embarking on new projects and experimenting with different techniques are essential aspects of artistic growth, nurturing creativity and refining craftsmanship. The key characteristic of continued exploration lies in the journey of self-discovery and artistic development, fostering a sense of curiosity and resilience in the face of creative challenges. By embracing the ethos of exploration, artists can chart new artistic territories, unveiling fresh perspectives and endless possibilities in the realm of glass etching.