Ultimate Guide to Wood Carving Dremel Bits
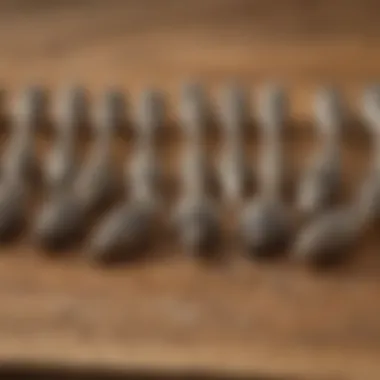
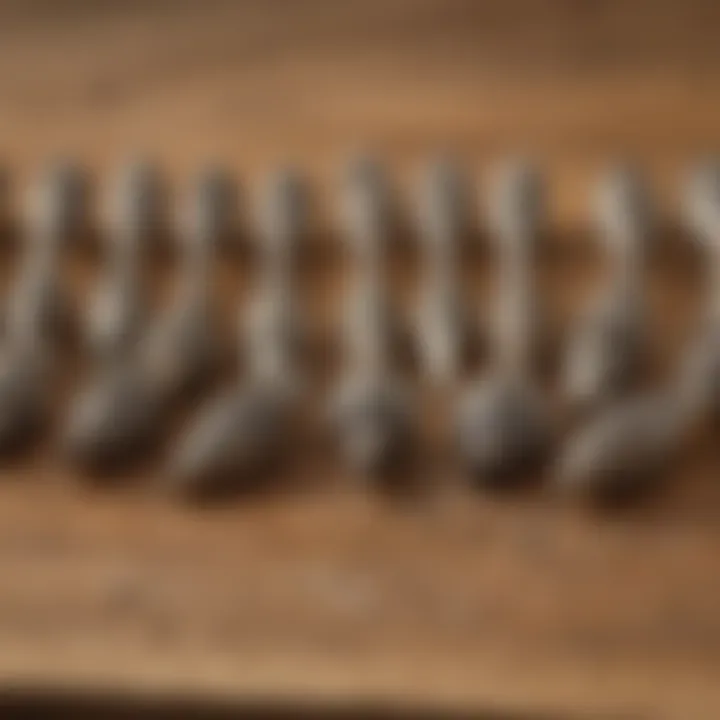
Intro
Wood carving is a fascinating and intricate craft. Having the right tools is crucial for achieving the desired results. One of the most versatile tools in a wood carver's toolkit is the Dremel tool. But not every bit is the same, and selecting the right Dremel bits can vastly improve the quality of work.
Understanding the various types of wood carving Dremel bits is essential for both beginners and professionals. This guide delves into the myriad options available, focusing on their specific applications. By mastering these tools and techniques, you can significantly elevates your wood carving projects.
Types of Wood Carving Dremel Bits
Dremel bits are generally categorized based on their design. Some popular types include:
- Tapered Ball Bits: Good for detailed carving, creating grooves, and finishing details.
- Sanding Drums: Essential for smoothing surfaces or outlining shapes.
- Fleshed-Out Carving Bits: More specialized, these are used for specific styles or effects, frequently seen in intricate designs.
Each bit is suited for particular tasks, making it important to choose based on the project requirements. The correct bit can boost your efficiency and quality.
Applications in Wood Carving
With a variety of bits available, let's consider their applications:
- Inlay Work: Some designs require tight precision; for this, tapered ball bits can give the fine detail necessary for successful completion.
- Shaping: Sanding drums are perfect for shaping a project’s rough edges. These bits allow for gradual shaping without removing excessive material.
- Texturing: Fleshed-out carving bits can add depth and uniqueness to wood carvings. This adds character and diversity to a project.
Understanding which bit works best in a given scenario can empower a crafter’s skill set.
Essential Tips for Effective Use
To ensure efficient use of Dremel bits, consider the following tips:
- Speed Control: Adjust the Dremel speed based on the required precision of the bit. Lower speeds can prevent material burn and allow for better control.
- Hand Positioning: Hold the tool steadily at an optimal angle for clear lines and details. Avoid using too much pressure.
- Practice Makes Perfect: Experiment on scrap wood to gauge how different bits perform.
These strategies be particularly useful for both novice and seasoned carvers. Improving performance will reflect in the quality of final output.
Dremel presents one of the unique occasions to hone your talents in artistry and technique. Choosing the correct Dremel bit can make the difference between a feeling of frustration and Dear achievement.
Understanding your tools lays the foundation for mastery in wood carving.
Prelude to Wood Carving
Wood carving is an ancient art form that combines creativity and skill. This discipline allows artists to transform ordinary wood into extraordinary pieces of art or functional objects. Understanding the intricacies of wood carving is vital for both beginners and experienced carvers. The significance of this introduction serves to emphasize the unique value of the craft, its various applications, techniques, and the satisfaction it brings to somebdy.
Dremel tools have revolutionized wood carving, enabling a greater degree of precision and complexity that manual methods alone cannot achieve. They offer a wide range of tools and bits that vary in shape and size, enhancing the capabilities of carvers. Selecting the right tools is essential—misalignment can lead to inferior results and even spoil the entire piece.
Key elements of wood carving include:
- Understanding the wood - Various types of wood react differently to carving techniques. Familiarity with these materials influences not only the finished product but the required tools as well.
- Choosing the correct technique - Carving varies dramatically between styles and desired outcomes. Each style requires specific techniques which may require different Dremel bits.
- Attention to detail - The fine features in your project can create a significant impact. The right Dremel tips allow a carver to pay closer attention to such elements.
Ultimately, by starting with a robust understanding of wood carving, each artist can begin their journey more prepared. Engaging deeply with the fundamental concepts now ensures a much smoother path towards mastering detailed woodwork with Dremel technology.
Understanding Dremel Tools
Dremel tools occupy a significant space in the woodworking world. They are rotary tools known for their versatility and ease of use. Dremels support various bits, facilitating multiple functionalities such as carving, engraving, sanding, and more. Understanding these tools is vital for a successful wood carving journey. Knowing how Dremel tools operate and their capabilities can enhance your craftsmanship. Moreover, the right technique matched with the right tool can greatly improve the quality of your work. This section focuses on elaborating on Dremel tools, their usage, and the beneficial aspects they offer when carving wood.
What is a Dremel Tool?
A Dremel tool is a high-speed rotary device. It was designed with a compact form factor, enabling close engagement for fine detail work. Although "Dremel" often refers broadly to rotary tools, it is important to note that it is a trademarked brand offering numerous models tailored to various tasks.
Dremel tools feature a rotatory motor that spins at high speeds. The spindle holds different bits that one can replace according to the desired application. This world of functionality makes it an attractive choice for many woodworkers, from hobbyists to professionals. It can handle a vast array of materials, but this article focuses solely on its applications for wood carving.
Benefits of Using Dremel for Wood Carving
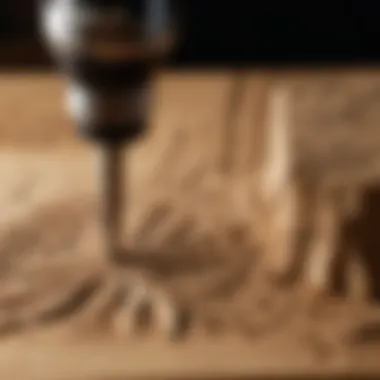
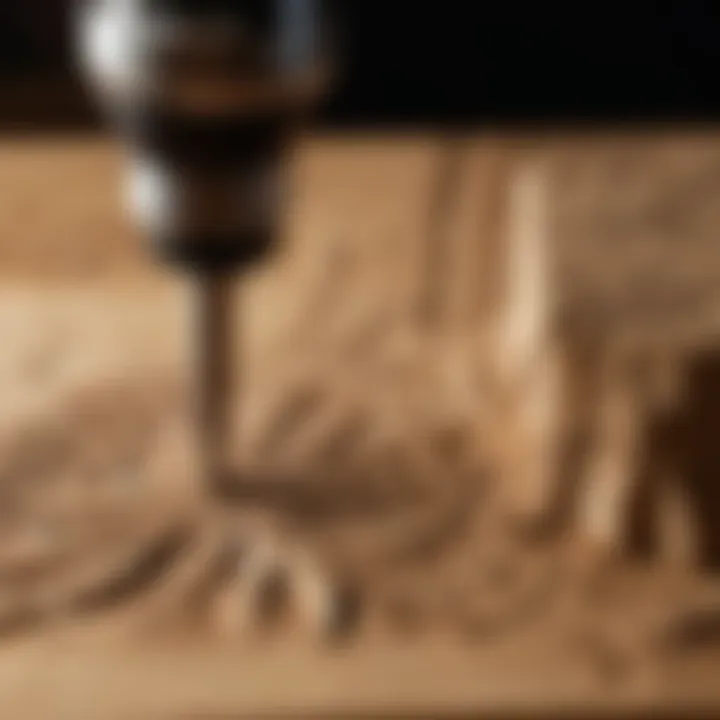
Using a Dremel tool for wood carving presents many compelling advantages.
- Precision: The high speed maximizes control, enabling intricate details in a piece. You can perform delicate work on small projects or add subtle design features in larger projects.
- Versatile Bit Options: Dremel tools accommodate many different bits. Users can easily switch bits, from sanding discs to engraving tools. This makes the Dremel instrumentally adaptable, catering to different project requirements.
- Ergonomics and Comfort: Most models have a lightweight design that allows users to work for extended periods without excessive fatigue. The applicable shaped handles are engineered for optimal grip, a crucial factor in detailed carving tasks.
- Availability and Affordability: Dremel tools like Dremel 3000 and Dremel 4300 are widely available. Their market presence often leads to competitive pricing.
- Ease of use: Beginners and skilled crafters alike find Dremels user-friendly. Simple operation rules and an intuitive design allow almost anyone to start creating wood carved pieces with confidence.
Utilizing Dremel tools effectively can transform wood carving into a more enjoyable and rewarding experience. Within this guide, we will continue to explore various Dremel bits, assisting you in selecting the tools relevant to your carving tasks.
Types of Dremel Bits for Wood Carving
Understanding the various types of Dremel bits is crucial for wood carving enthusiasts and professionals alike. Each type serves distinct purposes, impacting the quality and effectiveness of your projects. Selecting the right bit can make a noticeable difference in precision and finish. Using the proper tool allows you to achieve intricate designs, clean cuts, and smooth surfaces. Furthermore, recognizing the differences in materials, shapes, and applications ensures that every wood carving project meets your creative expectations.
High-Speed Steel Bits
High-speed steel bits are commonly used in wood carving. They are durable and maintain their sharpness through extended use. These bits excel in cutting and shaping various wood types, providing precision for both detailed and bulk work. Their affordability makes them a good choice for both beginners and experienced woodworkers. However, it is important to note that overuse can cause heating, potentially affecting the performance of the bit. Therefore, always monitor the temperature while working with high-speed steel bits.
Carbide Bits
Carbide bits are favored for their hardness and strength. They last significantly longer than other types and are less prone to dulling. This characteristic makes them ideal for carving denser woods or enduring materials. Carbide bits can create fine details with their unique shapes and are effective for both hollowing and smoothing. Care should be taken, as they can cause burning if pushed too hard against the wood. Their high durability means an initial investment may be wise for serious carvers seeking long-term use.
Diamond Bits
Diamond bits feature a coating of diamond particles, making them incredibly effective for specific applications like detailing and engraving. They are particularly useful when working with hardwoods and for creating intricate patterns. The versatility of diamond bits allows for precision finishing on surfaces and can provide a polished appearance. These bits come in various shapes and sizes, suitable for over a range of carving techniques. Yet, it's important to utilize them correctly, as improper use can lead to tooling damage.
Sanding Discs and Drums
Sanding discs and drums play vital roles in achieving a smooth finish on wood. They help in prepping surfaces or removing excess material efficiently. Discs reduce roughness that can occur after cutting, while drums are perfect for concave or larger surfaces. Different grits are available, allowing you to choose the best fit according to the finishing aspect you desire. Always ensure that you select the right grit. A coarser choice can remove too much material, while too fine can extend the finishing time unnecessarily.
Engraving Bits
Engraving bits are designed for precision work. They carve designs and lettering into the wood with accuracy. Various shapes help create different engraving effects. Popular choices resemble pens and small chisels, enabling more controlled strokes. These bits are particularly favored for decorative purposes or as a signature touch on wood projects. When selecting engraving bits, consider the intricacy of your design, ensuring you have the correct type for your specific needs.
Choosing the appropriate Dremel bit is fundamental in achieving your wood carving goals. Each type serves unique functions, and understanding their applications will enhance your workmanship greatly.
Choosing the Right Bit for Your Project
Choosing the right bit for your wood carving project is fundamental to achieving the desired results. The wrong bit can cause unwanted damage to your workpiece and hinder your creative process. It's vital to understand various factors and applications associated with each type of Dremel bit, ensuring that you approach each project with the right tools at hand.
Factors to Consider
When selecting a Dremel bit, there are several key factors to think about:
- Material Type: Different bits are designed for specific wood types. For instance, soft woods require lighter bits, like engraving bits, while harder woods may benefit from more robust options, such as carbide bits.
- Project Specifics: Consider the intricacy of your design. For detailed patterns, finer bits work well. If you're doing rough shaping, larger bits are suitable.
- Dust and Debris: Think about the resulting shavings when using a Dremel tool. Some bits might create more dust than others, which can interfere with visibility and the carving process.
- Ergonomics and Control: The shape and size of the bit can influence the level of control you have during carving. Select bits that fit comfortably in your hand while allowing precision maneuvering.
- Speed and Power of Your Dremel Tool: Match your bit choice with the capabilities of your Dremel tool. Some bits require higher RPM (revolutions per minute) to operate efficiently, while others work just as well at lower speeds.
Paying attention to these factors can make a significant difference in both the process and the final outcome of your wood carving.
Common Applications for Each Bit Type
Each type of Dremel bit serves specific applications:
- High-Speed Steel Bits: Ideal for detailed cuts and shapes. They are perfect for initial roughing and allow for smooth finishes.
- Carbide Bits: These tend to last longer and can handle tougher woods. Their primary applications include shaping and smoothing.
- Diamond Bits: Excellent for intricate designs and etching, diamond bits are crucial when a high level of precision is required. They're particularly effective for ornamental work.
- Sanding Discs and Drums: These are useful for shaping and finishing. They can refine surfaces and designs on wood projects to create a polished look.
- Engraving Bits: Best for etching finer details and creating personalized designs on wood surfaces. Ideal for names or logos.
Understanding the specific applications not only helps in achieving specific results but also ensures that your tools work effectively, thus enhancing your wood carving experience.
Using the correct bit type is essential for maximizing both precision and efficiency in your projects.
How to Use Dremel Bits Effectively
Using Dremel bits effectively is crucial for anyone serious about wood carving. The effectiveness with which you employ these tools can dramatically influence not only the quality of your work but also the efficiency of the process. Understanding how to navigate the various applications and techniques will enhance your proficiency as a carver.
Safety Precautions
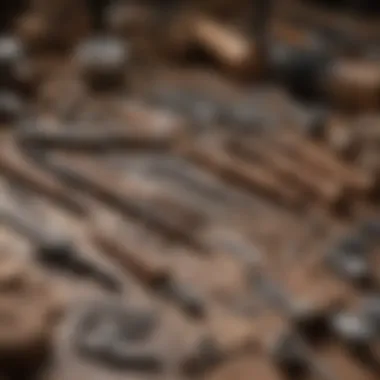
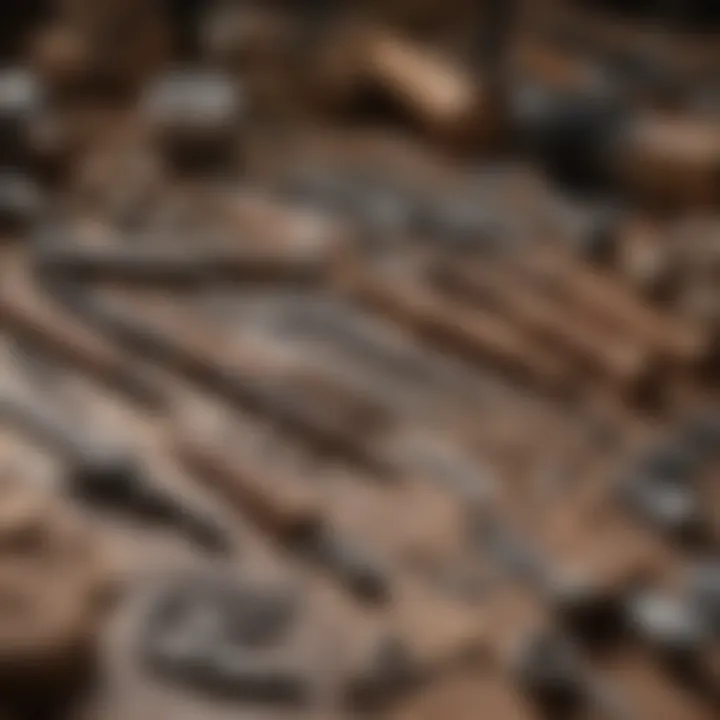
Safety cannot be overstated when it comes to using Dremel bits. Mishandling these powerful tools can result in serious injuries. Before you begin any project, here are some key precautions:
- Wear Safety Goggles: Protect your eyes from flying debris.
- Use a Dust Mask: Inhalation of wood dust can be harmful.
- Ensure a Firm Grip: Hold both the tool and the workpiece securely to avoid slips.
- Check for Defects: Inspect Dremel bits for cracks or damage before use. Defective bits can break during operation, posing a serious risk.
- Disconnect When Changing Bits: Always unplug or turn off the Dremel tool while changing bits to prevent accidental startups.
By adhering these simple guidelines, the risks involved in wood carving can be minimized.
Setting Up Your Workspace
The workspace layout greatly impacts your carving experience. A well-organized and efficient workspace enables focused creativity while minimizing distractions. To set it up:
- Table Surface: Select a sturdy table or workbench. It should be long-lasting, smooth and secure. A rubber mat can help stabilize your workpiece.
- Good Lighting: Ensure proper lighting to illuminate your workspace clearly. Consider using a task light aimed directly at the project area.
- Organized Tools: Keep Dremel bits and other related tools easily accessible. An organizer or toolbox specifically for your carving tools is a good investment.
- Ventilation: Make sure there’s proper ventilation in your workspace to avoid inhaling dust.
- Sit or Stand Comfortably: Depending on your preference, position yourself in a way that allows for comfort over lengthy carving sessions.
A thoughtful setup creates an environment conducive to creativity and reduces the chance of mistakes caused by distractions.
Basic Techniques for Wood Carving
Mastering some basic techniques is essential for optimizing the use of your Dremel bits. While this list is not exhaustive, it provides a foundation upon which you can build:
- Delicate Touch: Light pressure allows you more control over the cutting depth.
- Steady Movements: Instead of rushed and haphazard actions, slow and steady movements often yield better results.
- Different Angles: Vary the angle of the tools to achieve different textures and finishes on the wood.
- Practice control with varying speeds: Adjust the speed settings on your Dremel for larger cuts as faster speeds might be required, whereas finer detailing may need slower speeds.
- Carving in Layers: Developing your form gradually can help in achieving desired intricacies without overcutting.
Implementing these techniques systematically can vastly improve the results of your wood carving endeavors.
Remember: Each carving project is unique, so integrating your personal skills with these basic techniques offers room for creativity.
Maintenance of Dremel Bits
Proper maintenance of Dremel bits is paramount for anyone engaged in wood carving. Keeping bits in excellent condition ensures optimal performance, longevity, and the quality of the finished product. Neglecting to maintain these essential tools can lead to inefficient carving, inconsistent results, and can cause overlapping rong-term damage to both the bits and the wood being worked on. Beyond improving operational efficiency, regular maintenance supports safety during use.
Cleaning Your Bits
Keeping Dremel bits clean contributes significantly to consistent performance. Various materials can accumulate on bits during use. Among these are resin, dust, and wood particles which affix themselves to the surfaces. To clean your bits effectively:
- Let the bits cool down. Before touching anything recently used, ensure it has cooled to avoid burns.
- Use a brush. A soft nail brush can dislodge debris from finer areas. Avoid any harsh scratching as it can damage the bit's surface.
- Soaking. For persistent residues, soak in a solution of water and gentle soap for a few minutes. A soft toothbrush can be helpful to get into crevices after soaking.
- Rinse and dry. After cleaning, rinse always in clean water to remove any soap residue and dry thoroughly to prevent rust.
The benefits of keeping Dremel bits clean include improved efficiency and longer lifespan of the bits, which should aide your carving process significantly.
When to Replace Bits
Knowing when to replace Dremel bits is as important as knowing how to maintain them. Dull bits compromise both precision and result quality. Signs that a bit may need replacing include:
- Visible Damage: Chips, chips or other cracks on the bit’s cutting edge indicate wear.
- Diminished Performance: If the bit is not carving effectively or requires unnecessary force, it may be time for a change.
- Color Changes: Any discoloration can prevent proper operation and may reflect overheating.
- Frequent Breakage: If you find that bits break often, it can signal degradation and impending need for replacements.
Replacing worn or damaged bits enables you to maintain your high standards ensuring your carving projects reflect quality and care. Investing in fresh bits regularly allows for continued enjoyment of the craft without encountering frustrating setbacks due to bit failure.
Regularly evaluate the condition of your Dremel bits to optimize your wood carving experience.
Advanced Wood Carving Techniques with Dremel
Advanced wood carving represents the pinnacle of skill and creativity for artists and craftsmen alike. In this guide, we deepen the exploration of Dremel tools and bits used for masterful carvings, emphasizing the factors that elevate ordinary pieces into extraordinary artworks. By honing more sophisticated techniques, carvers are able to achieve depth and detail that make their work compelling. The efficient use of Dremel tools amplifies this aim and can have a significant impact on the outcome of wood carving projects.
Creating Intricate Designs
Creating intricate designs with a Dremel tool requires planning and patience. Start by pondering the final design and sketch it letely before committing to wood. Working on softer woods, such as basswood or pine, allow for deeper carvings and fine detailing with minimized effort. The smaller one can go with engraving bits the better; fine-point engraving bits, like the 107, can carve very small details.
It can be beneficial to practice on scrap pieces attractive, finding balance in design. The Dremel's variable speed control allos for intricate shaping, which is encouraging one to test with different pressures. Remember that careful, incremental removal, helps refine the shapes more accurately. The intricate nature of your carvings may create a delicate sense of character, even on simpler concepts.
Tips for Creating Intricate Designs
- Plan Thoroughly: Sketch designs and question their feasibility on wood.
- Choose of Designs: Intricate designs can vary in patterns and shapes, so opt for what your, grasp allows.
- Experiment: Work with a variety of bits to find what provides the desired effect.
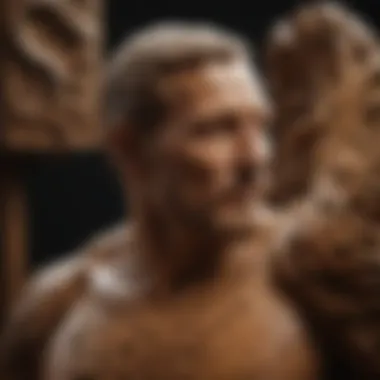
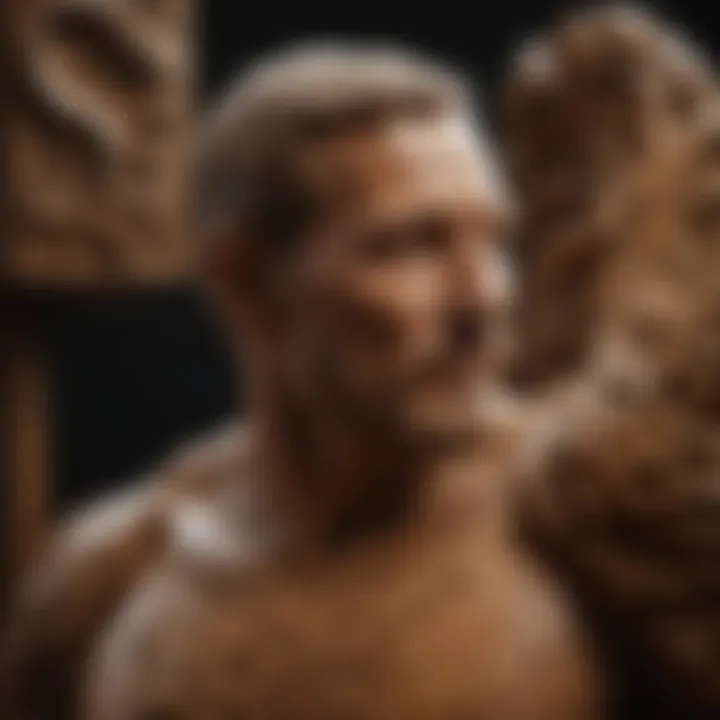
Inlay Work
Inlay work is another advanced technique that involves embedding contrasting materials in wood carvings. This often results in visually striking pieces that display creativity. Factors such as compatibility, color contrast, and craftsmanship determine the success of inlay processes. Beginners, however, might want to experiment with simple shapes before advancing.
The importance of preparation cannot be overstated. Carving precise cavities with appropriate Dremel bits is a necessity. This practice tends to boost the final presentation. When applying inlays, materials like epoxy or small gems add obvious realia. Moreover, exclusive attention to detail lays the groundwork for successful adhesion.
Suggestions for Practice in Inlay Work
- Select Appropriate Wood: Simpler grades of wood accommodate those intriguing artificial materials.
- Use Suitable Bits: Bits like rotary burrs create clean and precise holes for the inlay.
- Verify Fitment: Test inlays within cut spaces before bonding.
- Finish Properly: Smooth the finished product for optimal reflectivity and aesthetic appeal.
Common Issues and Troubleshooting
Troubleshooting common issues in wood carving using Dremel bits is essential for achieving high-quality results. As a woodworker, recognizing and addressing these issues promptly can enhance the efficiency of your projects and improve your overall experience. Failing to troubleshoot might lead to significant frustrations, wasted materials, and unsatisfactory finished products.
Overheating Problems
Overheating is a prevalent issue when using Dremel bits for wood carving. Excessive heat can damage both the bit and the wood being worked on. The causes of overheating can vary. They may include prolonged usage without breaks, applying too much pressure, or selecting an inappropriate bit for the task.
To mitigate overheating, consider implementing the following practices:
- Choose the Right Speed: Each Dremel bit has an optimal speed range. Running the bit too fast or too slow can generate unnecessary heat.
- Take Breaks: Give both the tool and the workpiece time to cool down. Smaller projects tend to require frequent breaks, while more extensive workings need a well-planned downtime.
- Adjust Pressure: Don't force the bit into the wood. Let the bit do the cutting at its natural speed to minimize friction and overheating.
- Monitor Temperature: Occasionally check the temperature of the bit with your hand. If it feels uncomfortably hot, it's time to pause. This simple method can save your tools and improve work quality.
Proper management of overheating issues can significantly extend the lifespan of your Dremel bits and improve the quality of your carvings.
Poor Finish Quality
That risk of poor finish quality is another common concern during wood carving projects. Issues such as surface scratches, uneven cuts, and vague details can diminish the overall appearance of the workpiece. More often than not, the core contributors include the choice of bit, speed settings, and the technique applied.
To enhance finish quality, examine these suggestions:
- Choose The Correct Bit: Different bits are designed for specific tasks. Using a fine-sanding drum for smooth surfaces or a high-speed steel bit for defined edges can lead to better results.
- Understand Material Differences: Different types of wood react differently to carving. Softer woods may chip easily, while denser woods require sharper bits and more thoughtful techniques.
- Maintain Your Bits: Dull or damaged bits can compromise the finishing quality. Regularly inspect your tools for signs of wear and replace them when necessary.
- Practice Correct Technique: Ensure you maintain a steady hand and work at an even pace. Erratic movements can result in uneven surfaces.
By implementing these strategies, woodcarvers can significantly improve the finish quality. Taking the time to address these common issues helps in achieving satisfaction with one's creations.
Finale
The conclusion of this article emphasizes the significance of understanding wood carving Dremel bits for both beginners and seasoned artisans. The range of bits—from high-speed steel to diamond—serves different purposes, enabling a variety of techniques and artistry levels in wood carving. Choosing the right bit along with proper maintenance extends the lifespan of these tools and ensures finer results in projects.
Effective use of Dremel bits greatly influences the quality of finish one can achieve. The insights about common issues and troubleshooting techniques can also preemptively address problems that woodcarvers may face.
Factors such as material type, desired texture, and intricate detailing can impact the choices made in selecting Dremel bits. Thus, these considerations should form part of a deliberate strategy for successful wood carving endeavors.
Furthermore, the advanced techniques discussed highlight the versatility of Dremel tools, catering to various artistic styles and project demands.
Nevertheless, continuous learning and experimentation are crucial. Utilizing resources like en.wikipedia.org and britannica.com for further research can deepen understanding and open doors to innovative carving methods.
Ultimately, mastering the art of wood carving with Dremel tools and bits holds immense potential for creative expression. It encourages the exploration of new techniques while solidifying a foundational knowledge that can elevate any wood carving project.
Resources for Further Learning
Understanding the tools and techniques involved in wood carving using Dremel bits is one thing; however, continual learning keeps the knowledge relevant and enriched. In our rapidly evolving world of crafting, accessing resources for further learning is crucial.
One of the main imports of continuous education is to gain fresh perspectives and insights regarding wood carving methodologies. Wood carving communities have existed for 🤔 decades, allowing enthusiasts to share their experiences and tricks of the trade.
Many people overlook the value of tutorials and workshops that specialize in wood carving. Specialist sites and youtube channels can provide invaluable, actionable tips, fostering growth through visual learning. Learning directly from experts can humanize the techniques often portrayed in written guides, thereby enhancing comprehension and application.
Notable resources to consider include:
- Webinars and Online Classes: Websites likeEnvision Foxoften offer sessions on carving techniques tailored for different skill levels.
- Books: A well-stocked library relevant to woodworking and carvings fills your knowledge gaps. Titles like The Complete Book of Woodcarving provide in-depth strategies and ideas.
- Community Forums: Websites like Reddit and downtime on forums allow enthusiastic discussion. Such platforms create an backyard for sharing problems, solutions, and motivation among carvers at every level.
- Social Media Groups: On Facebook, multiple groups focus on wood carving, showcasing artists' work and allowing for real-time draw and growth.
Investing in knowledge paves the way for elevating craftsmanship. Emphasizing connections with informative resources helps in fostering a more versatile skill set in wood carving, therefore ultimately underpinning the quality and creativity in your projects.
"The beauty of learning is that no matter where you start from, there are always layers of skill and knowledge to uncover."
In sum, exploring additional resources not only bridges gaps in personal skills, but also allows for engagement with a broadening community of wood carving enthusiasts and experts.