Unveiling the Exquisite Art of Rock Cutting and Polishing Machines
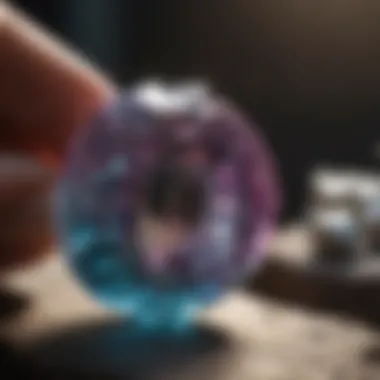
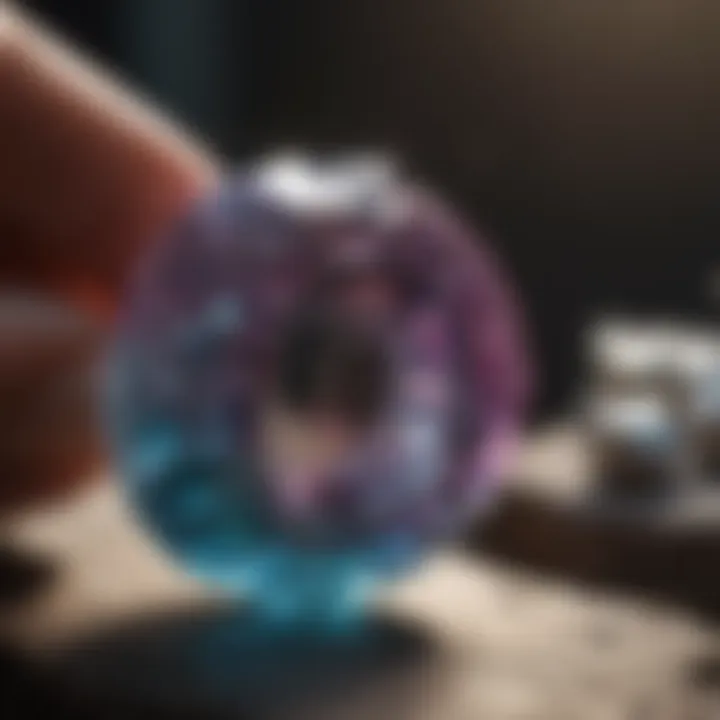
Rock and Fossil Identification
Delving into the realm of rock cutting and polishing machines, it is vital to have a keen understanding of the types of rocks and fossils being worked upon. These specimens vary greatly in their characteristics, with some displaying unique patterns or gem-like qualities that determine their value and application. Oftentimes, tools for identification play a crucial role in discerning the composition and potential of the rocks, aiding artisans in their craft to bring out the best in each piece.
Collecting Tips and Techniques
Upon identifying the target rocks and fossils, the next phase involves the intricate process of collecting them efficiently. Best practices for collection are essential to ensure the integrity and quality of the specimens. Locating prime collecting sites becomes a priority, as these locations hold the promise of yielding exceptional rocks and fossils. Moreover, knowing how to safely extract these specimens without damage is a skill that sets expert collectors apart.
Preservation and Display
After collecting and identifying the rocks and fossils, preservation techniques come into play to maintain their beauty and integrity. Utilizing proper storage methods is crucial for preventing deterioration and ensuring long-lasting quality. Furthermore, creative display ideas add an artistic touch to showcasing these treasures, capturing the attention and admiration of enthusiasts and collectors alike.
Geological Insights
As we venture into the world of rock cutting and polishing machines, gaining geological insights becomes paramount. Understanding the formations and processes that have shaped these rocks and fossils provides valuable context to their beauty and significance. Exploring the historical relevance of these specimens unveils the remarkable stories they carry through time. Moreover, delving into notable discoveries in the field sparks curiosity and appreciation for the wonders that lie beneath the surface.
Prolusion to Rock Cutting and Polishing
In exploring the realm of rock cutting and polishing machines, we embark on a journey through the intricate processes and technologies involved in transforming rough rocks into exquisite gems and specimens. This section serves as a gateway to understanding the fundamental principles that govern the art of lapidary craftsmanship. The significance of rock cutting and polishing lies in its ability to unlock the hidden beauty of raw stones, revealing their true potential through skilled hands and advanced machinery. We delve into the very essence of turning ordinary rocks into mesmerizing pieces of art.
Understanding Lapidary Art
History of Lapidary Craftsmanship
Delving into the annals of history, we uncover the roots of lapidary craftsmanship and its profound influence on the world of gemstone aesthetics. The history of lapidary craftsmanship traces back to ancient civilizations where meticulous handwork defined the beauty of gemstones. Its artistry is imbued with cultural heritage and traditional techniques, showcasing the mastery of artisans through millennia. The historical context of lapidary craftsmanship provides a rich tapestry of knowledge that shapes modern practices, offering insights into the evolution of gem cutting and polishing.
Significance of Rock Cutting and Polishing
The meticulous process of rock cutting and polishing holds a paramount significance in the lapidary world, as it determines the final form and brilliance of gemstones. The precision involved in cutting raw rocks into specific shapes and sizes is a testament to human ingenuity and artistic vision. Rock cutting and polishing serve not only as technical procedures but also as forms of artistic expression, where creativity meets craftsmanship in a harmonious blend. The significance lies in the ability to enhance the natural beauty of minerals, bringing forth their luster and color in dazzling displays of lapidary artistry.
Role of Technology in Modern Lapidary
Evolution of Rock Cutting Machines
The evolution of rock cutting machines has revolutionized the field of lapidary work, injecting precision and efficiency into the once labor-intensive process. These machines have transitioned from manual tools to sophisticated devices driven by advanced technologies. Their precision cutting mechanisms and automated functionalities have elevated the quality and output of gemstones, meeting the demands of a contemporary market. The evolution continues to push the boundaries of what is achievable in rock cutting, reshaping the landscape of lapidary art.
Innovations in Polishing Equipment
Innovations in polishing equipment have fine-tuned the art of giving gemstones their final gleam and polish. Advanced technologies and materials have transformed the way stones are polished, offering enhanced finishes and textures. Modern polishing equipment not only enhances the aesthetic appeal of gemstones but also ensures durability and long-lasting beauty. The innovations in polishing equipment complement the cutting processes, creating a seamless workflow that results in stunning gemstone creations.
Key Components of Rock Cutting Machines
In the tantalizing realm of rock cutting and polishing machines, the backbone lies in understanding the crucial elements constituting these intricate devices. Key components of rock cutting machines include the blades and abrasives, water cooling systems, as well as clamping and feeding mechanisms. These components work synchronously to ensure precise and efficient cutting and polishing of rocks into splendid gems and specimens. Their role in the process is paramount, dictating the quality and accuracy of the final outcome.
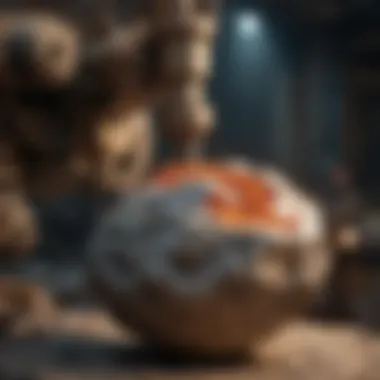
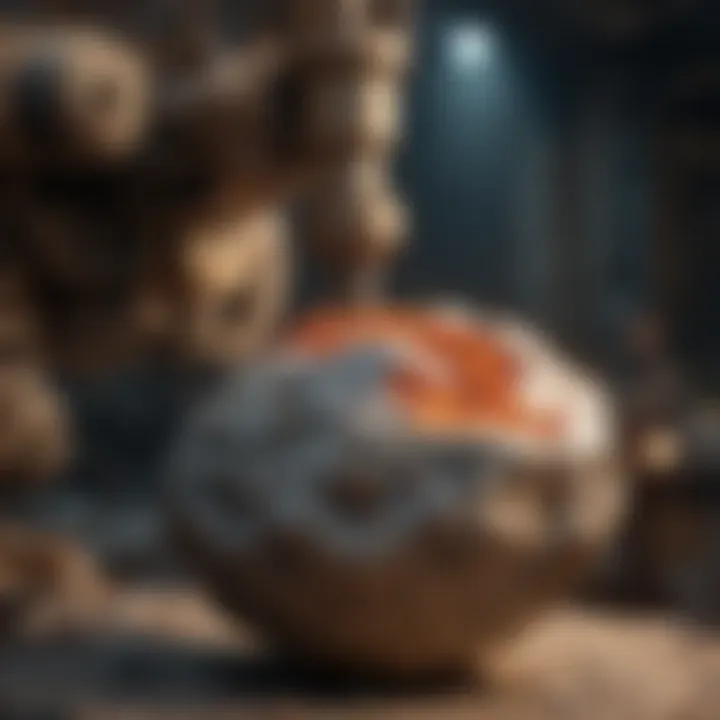
Blades and Abrasives
Diamond Blades
Diamond blades stand as stalwart pillars in the domain of rock cutting machines, revered for their unparalleled hardness and durability. The key characteristic of diamond blades lies in their ability to seamlessly slice through robust rocks with precision, leaving behind a clean and smooth finish. Their unique feature of diamond-tipped edges ensures longevity and resistance to wear, making them a favored choice for rock cutting enthusiasts. Despite their remarkable advantages, diamond blades may pose challenges in terms of initial cost and maintenance, factors that are carefully weighed against their superior cutting performance.
Carbide Grits
As a vital element in rock cutting machines, carbide grits offer a robust alternative to traditional cutting methods. The key characteristic of carbide grits is their exceptional hardness and wear resistance, ideal for handling tough rocks and minerals. Their unique feature lies in the ability to maintain sharpness even under demanding conditions, providing consistent cutting efficiency. While carbide grits offer distinct advantages in cost-effectiveness and longevity, they may exhibit limitations when faced with extremely hard or abrasive materials, necessitating careful selection based on the specific cutting requirements.
Water Cooling Systems
Importance of Cooling in Cutting
The significance of cooling in cutting processes cannot be overstated, especially in the realm of rock cutting machines. Effective cooling plays a pivotal role in dissipating heat generated during cutting, thereby preventing damage to both the machinery and the rocks being processed. As a crucial element in enhancing cutting precision and prolonging tool life, cooling mechanisms ensure optimal performance and efficiency. Its unique feature lies in its ability to maintain stable operating temperatures, safeguarding against thermal stress and ensuring consistent cutting outcomes. However, improper cooling methods may lead to reduced cutting efficiency and potential damage to the machinery, emphasizing the need for well-designed cooling solutions tailored to the specific cutting requirements.
Types of Cooling Mechanisms
Embracing diverse cooling mechanisms is essential in maximizing the efficiency and effectiveness of rock cutting machines. Different types of cooling mechanisms offer varying benefits, ranging from water-based systems to air cooling setups. The key characteristic of these systems lies in their capacity to regulate temperatures efficiently, providing a controlled environment for cutting operations. Each cooling mechanism boasts a unique feature, be it versatility, energy efficiency, or enhanced cooling capacity, catering to different needs and preferences. While these mechanisms offer distinct advantages in promoting cutting precision and prolonging tool life, selecting the most suitable type is essential to ensure optimal performance and longevity of the cutting equipment.
Clamping and Feeding Mechanisms
Secure Clamping for Precision
Securing rocks unequivocally during the cutting process is integral to achieving precise and accurate results in rock cutting machines. Secure clamping mechanisms employ a combination of robust clamps and fixturing systems to hold rocks in place, minimizing vibrations and deviations during cutting. The key characteristic of secure clamping lies in its ability to maintain stability and alignment, essential for intricate cutting tasks. Its unique feature enables operators to adjust and customize the clamping force according to the rock's hardness and shape, ensuring consistent cutting performance. While secure clamping systems offer advantages in enhancing cutting precision and operator safety, they may require meticulous setup and calibration to optimize their efficiency based on the cutting requirements.
Automated Feeding Systems
Automated feeding systems revolutionize the feeding process in rock cutting machines, streamlining operations and enhancing efficiency. The key characteristic of automated feeding systems lies in their ability to control feed rates and pressures with precision, ensuring consistent cutting performance. Their unique feature of programmable automation enables customized feeding sequences based on rock characteristics, enhancing cutting accuracy and repeatability. While automated feeding systems offer advantages in reducing manual labor and improving cutting efficiency, they may necessitate regular maintenance to uphold optimal functionality. Overall, integrating automated feeding systems into rock cutting machines elevates operational efficiency and productivity, heralding a new era of precision cutting in the lapidary industry.
Precision in Rock Cutting
Rock cutting is a precise art form that requires meticulous attention to detail and accuracy. In the realm of lapidary craftsmanship, where raw rocks are transformed into exquisite gems and specimens, precision plays a paramount role. Achieving precision in rock cutting involves utilizing advanced technologies and techniques to ensure optimal results. It is not merely about cutting rocks; it is about sculpting them with finesse and expertise. Precision in rock cutting guarantees that the final product meets the desired specifications and quality standards.
Computer-Aided Cutting
CAD Software Integration
CAD software integration revolutionizes the way rocks are cut and shaped. By digitizing the design process, lapidaries can create intricate cutting patterns with unparalleled accuracy. The key characteristic of CAD software integration lies in its ability to translate complex designs into precise cutting instructions. This enables lapidaries to replicate intricate patterns consistently, ensuring uniformity across multiple pieces. The unique feature of CAD software integration is its flexibility, allowing for intricate designs that would be challenging to achieve manually. The advantages of CAD software integration in rock cutting include enhanced productivity, minimized material wastage, and the ability to customize designs with ease.
Advantages of Precision Cutting
Precision cutting offers a plethora of benefits in the world of lapidary artistry. The key characteristic of precision cutting is its ability to ensure uniformity and consistency in the final products. By cutting rocks with precision, lapidaries can achieve smooth surfaces, sharp edges, and perfect dimensions. This level of accuracy enhances the visual appeal of the gemstones and increases their market value. The unique feature of precision cutting is its ability to mitigate the risk of errors, resulting in higher efficiency and lower production costs. The advantages of precision cutting include improved quality control, reduced rework, and enhanced customer satisfaction.
Wire Saw Technology
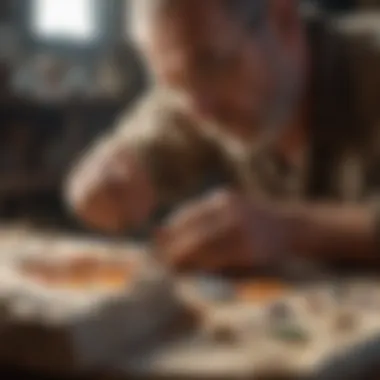
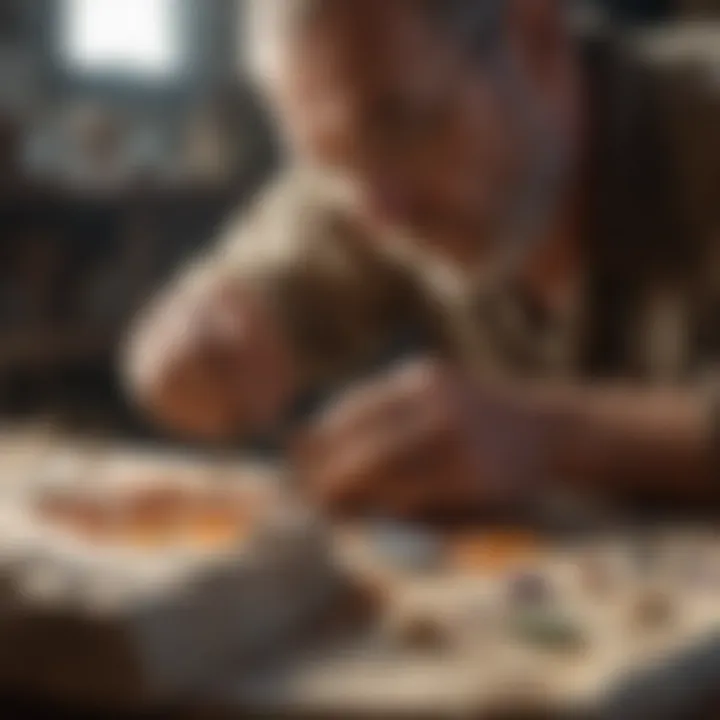
Wire saw technology is a game-changer in rock cutting, offering efficiency and precision like never before. The efficiency of wire saws lies in their ability to slice through hard rocks with minimal wastage. Unlike conventional cutting methods, wire saws generate clean and precise cuts, minimizing material loss. The key characteristic of wire saw technology is its versatility, allowing lapidaries to cut rocks of various shapes and sizes with ease. The unique feature of wire saws is their ability to cut intricate designs and curves smoothly, enhancing the creative possibilities in lapidary work.
Applications in Lapidary
Wire saw technology finds versatile applications in the field of lapidary art. From cutting large rock slabs to shaping delicate gemstones, wire saws offer precision and efficiency across various tasks. The key characteristic of wire saw applications in lapidary is their ability to handle a wide range of materials, from soft minerals to hard rocks. This versatility makes wire saws a popular choice among lapidaries seeking high-quality cuts with minimal material wastage. The unique feature of wire saw applications is their adaptability to different cutting environments, whether in a workshop setting or on-site during excavation projects. The advantages of wire saw applications in lapidary include increased productivity, enhanced precision, and the ability to tackle complex cutting challenges.
Art of Rock Polishing
Rock polishing is a crucial element in the realm of lapidary craftsmanship. It plays a significant role in the transformation of raw rocks into exquisite gems. The meticulous process of polishing enhances the beauty and luster of the rocks, bringing out their inherent characteristics and brilliance. Without proper polishing techniques, the true potential of a stone cannot be realized. In this article, we will explore the intricate art of rock polishing, delving into the specific methods, benefits, and considerations that are essential for achieving stunning results.
Grinding and Pre-Polishing
Role of Grinding in Polishing
Grinding is a fundamental step in the polishing process, where rough surfaces are smoothened and refined. Its primary goal is to prepare the rock for polishing by removing imperfections and irregularities. Grinding ensures that the surface is even and free from any flaws, laying the foundation for a flawless polish. In this article, we emphasize the vital role of grinding in achieving the desired finishing of gemstones. Its precision and efficiency make it a popular choice in the lapidary industry, guaranteeing consistent results with each use.
Preparation for the Polishing Stage
The preparation phase before polishing is critical in ensuring a successful outcome. It involves cleaning the rock, inspecting for any remaining blemishes, and selecting the appropriate polishing method. This preparatory stage sets the tone for the final polish, determining the level of shine and quality of the end product. Effective preparation not only streamlines the polishing process but also enhances the overall aesthetic appeal of the gemstone. Attention to detail during this phase is essential for achieving exceptional results when polishing rocks.
Polishing Techniques
Rotary Tumbling
Rotary tumbling is a popular polishing technique that involves placing rocks or gemstones in a rotating barrel with abrasive grit. The tumbling action smoothens the surface of the rocks, gradually polishing them to a brilliant shine. This technique is valued for its ability to polish multiple rocks simultaneously while maintaining consistent results. Rotary tumbling is a versatile method suitable for various types of stones, making it an efficient choice for lapidary enthusiasts seeking high-quality finishes.
Vibratory Polishing
Vibratory polishing utilizes a vibrating motion to enhance the polishing process. The gentle vibrations help in achieving a smooth and glossy surface on the rocks. This technique is renowned for its ability to polish intricate shapes and delicate gemstones without causing damage. Vibratory polishing offers a gentle yet effective way to bring out the natural beauty of different types of rocks, providing a flawless finish that captivates admirers.
Final Finishing Touches
Buffing and Burnishing
Buffing and burnishing are essential steps that provide the final sheen and polish to the gemstones. Buffing involves using a soft cloth wheel to create a smooth and shiny surface, while burnishing uses friction to enhance the luster of the rocks. These finishing touches add depth and brilliance to the gemstones, elevating their visual appeal and desirability. The meticulous application of buffing and burnishing techniques ensures a professional finish that meets the highest standards in lapidary craftsmanship.
Use of Polishing Compounds
Polishing compounds are integral to achieving a fine polish on gemstones. These compounds help in removing scratches, refining surfaces, and enhancing the shine of the rocks. By selecting the appropriate polishing compound, lapidary artists can achieve different levels of finish, from matte to mirror-like surfaces. The careful application of polishing compounds is essential for bringing out the unique features and colors of each stone, emphasizing their natural beauty and allure.
Advancements in Lapidary Technology
A crucial aspect of the fascinating world of rock cutting and polishing machines is the constant evolution and advancement of lapidary technology. In this article, we delve deep into the realm of technological progress within the lapidary industry, showcasing the integration of cutting-edge innovation into traditional craftsmanship. Exploring the latest advancements in machinery and processes, we shed light on how technology has revolutionized the way rocks are transformed into stunning gemstones and specimens, catering to the needs of both professionals and enthusiasts alike.
Automated Polishing Systems
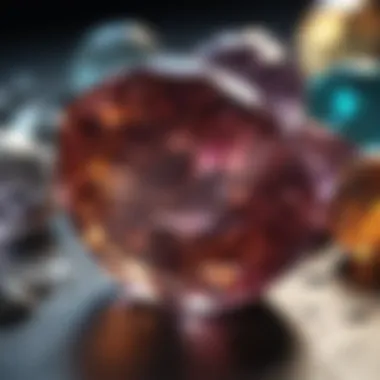
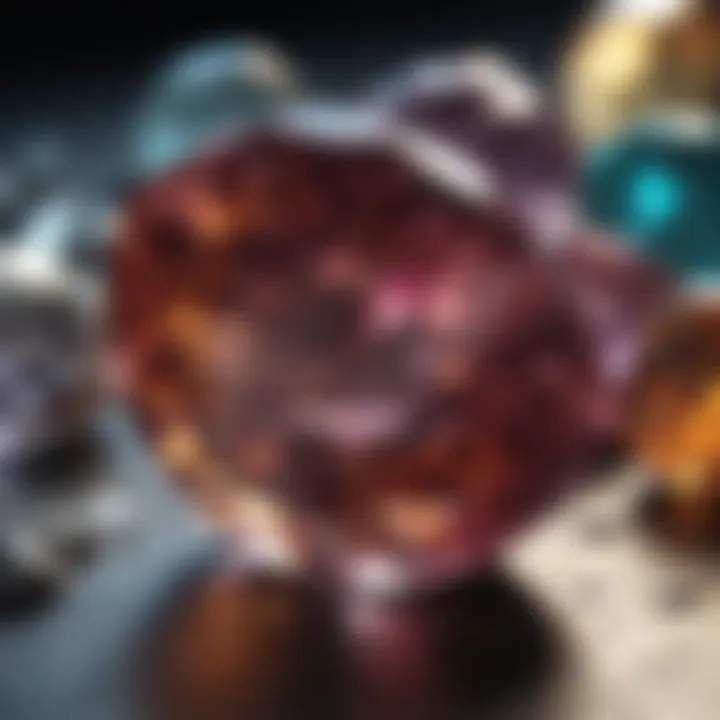
Robotics in Polishing
Robotics in polishing plays a pivotal role in optimizing the polishing process, offering unparalleled precision and efficiency. The integration of robotic systems automates intricate polishing techniques, ensuring consistent results with minimal human intervention. This technology revolutionizes the traditional hand-polishing methods, enhancing productivity and quality control. The key characteristic of robotics in polishing lies in its ability to replicate complex motions and pressure applications, mimicking artisanal hand-polishing with unprecedented accuracy. This feature makes robotics a popular choice in the lapidary industry, enabling flawless finishes and intricate detailing that traditional methods struggle to achieve.
Benefits of Automated Processes
Automated processes in rock polishing bring forth a myriad of benefits that streamline the production workflow and elevate the final output's quality. By automating repetitive tasks, such as polishing and buffing, efficiency is significantly increased, leading to higher productivity rates. The key characteristic of automated processes is the reduction of human errors and inconsistencies, ensuring uniformity in the polishing results. This approach not only saves time but also enhances the overall precision and repeatability of the polishing stages. One unique feature of automated processes is the ability to store and reproduce customized polishing sequences, catering to specific gemstone shapes and sizes. While automation offers immense advantages in terms of productivity and quality, potential drawbacks may include initial investment costs and the need for specialized training to operate the automated systems effectively.
Integration of IoT
Smart Polishing Solutions
The integration of IoT (Internet of Things) technology in polishing solutions brings forth a new era of smart manufacturing in the lapidary industry. Smart polishing solutions leverage IoT connectivity to enable real-time monitoring and control of the polishing process, enhancing operational efficiency and quality assurance. The key characteristic of smart polishing solutions is their ability to gather and analyze data from the polishing machines, allowing for predictive maintenance and optimization of polishing parameters. This innovative approach is a beneficial choice for the article as it ensures consistent quality standards and operational transparency, meeting the demands of a technologically-driven market.
Remote Monitoring Capabilities
Remote monitoring capabilities empower operators to oversee the polishing processes from any location, offering flexibility and convenience in production management. The key characteristic of remote monitoring capabilities is the remote access to machine performance data and analytics, providing valuable insights for operational enhancements. This feature is a beneficial choice for the article as it caters to the industry's increasing need for real-time monitoring and decision-making. One unique advantage of remote monitoring is the ability to troubleshoot and adjust polishing parameters remotely, minimizing downtime and optimizing production efficiency. While remote monitoring enhances operational flexibility, potential disadvantages may involve cybersecurity concerns and the reliance on stable internet connectivity for uninterrupted monitoring.
Future Prospects of Rock Cutting and Polishing Machines
In the ever-evolving landscape of lapidary craftsmanship, the future prospects of rock cutting and polishing machines hold paramount significance. This section delves into the innovative pathways and emerging trends shaping the realm of gemstone production. As technology continues to advance, the intersection of artistry and precision in rock cutting and polishing unveils new possibilities and challenges. Understanding the trajectory of this field not only aids in predicting market shifts but also paves the way for sustainable practices and experiential advancements.
Sustainable Practices in Lapidary
Recycling and Circular Economy
Exploring sustainable practices within the domain of lapidary, recycling and circular economy methodologies stand out as pillars of environmental stewardship and resource optimization. The concept of repurposing waste materials and adhering to a cyclical production model aligns with the ethos of eco-conscious gemstone production. By emphasizing the reuse and reintegration of resources, lapidary artisans can mitigate the industry's carbon footprint and reduce environmental impact. Despite challenges in scale and efficiency, incorporating recycling and circular economy principles fosters a circularity that transcends traditional linear production models.
Eco-Friendly Polishing Methods
Within the realm of eco-friendly polishing methods, a focus on non-toxic compounds, energy efficiency, and water conservation emerges as a driving force towards sustainable lapidary practices. By leveraging biodegradable solutions, renewable energy sources, and minimized water usage, lapidary workshops can align their polishing processes with eco-friendly standards. The unique feature of eco-friendly polishing methods lies in their ability to combine cutting-edge technology with ecological mindfulness, offering a harmonious blend of innovation and sustainability. While initial adoption may pose challenges in cost and accessibility, the long-term benefits of eco-friendly polishing methods outweigh conventional practices, positioning them as pivotal components of responsible gemstone production.
Customization and Personalization Trends
Tailored Gem Cutting Services
The rise of tailored gem cutting services signifies a shift towards bespoke craftsmanship and individual expression within the lapidary industry. By offering customized cutting solutions tailored to clients' specifications, lapidary artisans can cater to diverse aesthetic preferences and unique gemstone requirements. The key characteristic of tailored gem cutting services lies in their commitment to precision, flexibility, and client collaboration. This personalized approach not only enhances customer satisfaction but also elevates the craft of gem cutting to an art form that transcends mass production norms. Despite challenges in scalability and production time, the demand for personalized gem cutting services underscores a growing appreciation for artisanal expertise and distinctive creations.
Artisanal Polishing Techniques
Embracing artisanal polishing techniques signifies a return to heritage practices, handcrafted precision, and artistic flair in the lapidary domain. By employing traditional methods, specialized tools, and expert insights, lapidary artisans can imbue each gemstone with a unique character and aesthetic finesse. The key characteristic of artisanal polishing techniques lies in their meticulous attention to detail, tactile finesse, and reverence for the gemstone's intrinsic beauty. This hands-on approach not only celebrates craftsmanship but also revives traditional polishing methods that showcase the human touch in a technology-driven era. Despite challenges in scalability and standardization, artisanal polishing techniques add a layer of authenticity and intimacy to the gem cutting process, appealing to connoisseurs seeking personalized and artisan-crafted gems.
Exploring Unconventional Materials
Diamond Alternatives
Venturing into diamond alternatives opens a realm of sustainable, diverse, and innovative materials that challenge traditional gemstone norms. By considering alternatives such as lab-grown diamonds, moissanite, or cubic zirconia, lapidary artisans can offer environmentally conscious and affordable options without compromising quality or brilliance. The key characteristic of diamond alternatives lies in their ethical sourcing, customizable features, and diverse aesthetic appeal. This shift towards non-traditional materials not only disrupts established gemstone hierarchies but also promotes inclusivity and creativity within the lapidary sphere. Despite challenges in market acceptance and consumer perception, diamond alternatives present a frontier of possibilities for conscious consumers and cutting-edge designers.
Innovative Polishing Surfaces
Exploring innovative polishing surfaces introduces a tapestry of textures, finishes, and visual effects that redefine the boundaries of traditional lapidary aesthetics. By utilizing surfaces such as textured laps, composite wheels, or specialized media, lapidary artisans can achieve avant-garde polishing results that transcend conventional gloss and luster. The key characteristic of innovative polishing surfaces lies in their versatility, experimental potential, and ability to create unique gemstone finishes. This departure from conventional polishing methods not only sparks creativity but also invites exploration of unconventional design elements and tactile experiences. Despite challenges in standardization and consistency, innovative polishing surfaces offer a playground for artistic experimentation and transformative gemstone expressions.