Master the Art of Tumble Polishing Stainless Steel for Rock and Fossil Collectors
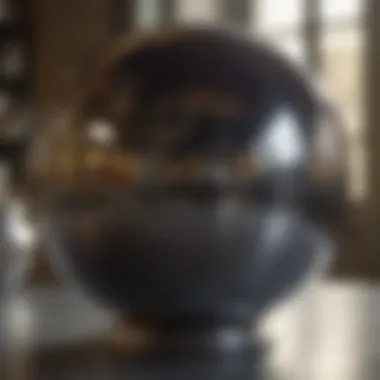

Rock and Fossil Identification
Rock and fossil identification is a fundamental skill for collectors, allowing them to discern the unique features of each specimen. Various types of rocks and fossils exist, ranging from sedimentary to igneous and metamorphic rocks, each possessing distinct characteristics. Sedimentary rocks like sandstone often exhibit layered patterns, while igneous rocks such as granite showcase crystalline structures. Metamorphic rocks like marble display recrystallized textures, providing clues to their formation process. To identify these specimens accurately, collectors need a keen eye for details and a deep understanding of geological processes. Essential tools for identification include magnifying glasses, scratch tests, and hardness scales, enhancing the perceptiveness of collectors in distinguishing rocks and fossils. By honing their identification skills, collectors can enrich their understanding of the earth's geological history and appreciate the diversity of specimens in their collection.
Introduction to Tumble Polishing Stainless Steel
Tumble polishing stainless steel is a meticulous art that plays a pivotal role in enhancing the appearance of specimens for rock and fossil collectors. This introductory section sets the stage for a thorough exploration of the tumble polishing process, from its fundamental principles to advanced techniques. Understanding the nuances of tumble polishing can elevate the aesthetic appeal of stainless steel specimens, making them stand out in any collection.
Understanding Tumble Polishing
Definition and Process
Tumble polishing involves the mechanical smoothing and polishing of stainless steel surfaces through abrasion within a rotating drum or barrel. The process removes imperfections, scratches, and dirt, resulting in a lustrous finish. Its simplicity and efficiency make it a popular choice for enhancing the visual appeal of specimens in the collector's trove.
Benefits of Tumble Polishing
The key benefit of tumble polishing is its ability to achieve consistent results across various specimen shapes and sizes. This method ensures uniformity in finish, making it ideal for improving the overall aesthetics of stainless steel pieces. Additionally, tumble polishing is a time-saving technique that can handle large batches of specimens simultaneously, increasing productivity for collectors.
Types of Tumbling Media
There are various types of tumbling media available, including ceramic media, plastic pellets, and stainless steel pins, each offering distinct advantages depending on the desired polishing outcome. Ceramic media, for example, is known for its durability and ability to provide a smooth finish, while stainless steel pins excel in reaching intricate details on specimens.
Choosing the Right Equipment
Tumblers
Selecting the appropriate tumbler is crucial for successful tumble polishing. Vibratory tumblers are ideal for smaller specimens and delicate materials, while rotary tumblers are more suited for larger batches and heavy-duty polishing requirements. The choice of tumbler should align with the size and nature of the specimens being processed to ensure optimal results.
Media Separators
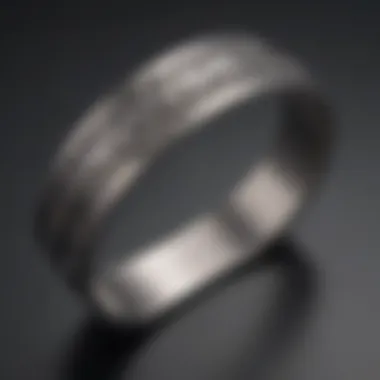
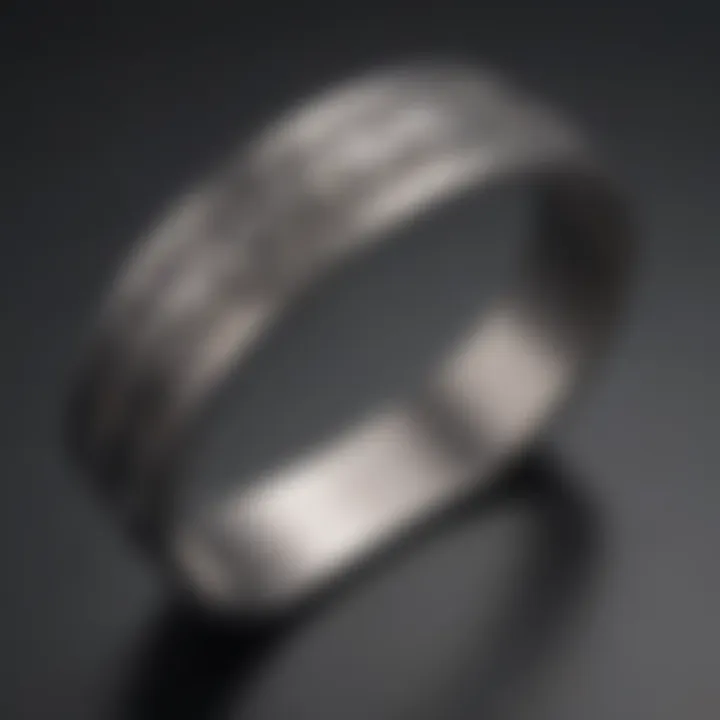
Media separators play a vital role in separating the abrasive media from the polished specimens after tumbling. Their efficient functionality helps maintain the quality of the finished products and streamline the polishing process by eliminating the need for manual sorting.
Work Area Setup
A well-organized work area is essential for a smooth tumble polishing operation. Proper ventilation, adequate lighting, and designated spaces for different stages of the process contribute to a safe and efficient working environment. An organized setup minimizes the risk of errors and ensures consistent results across all specimens.
Preparation of Stainless Steel Specimens
Cleaning and Degreasing
Before tumble polishing, thorough cleaning and degreasing of stainless steel specimens are imperative to ensure effective polishing results. Removing surface contaminants and oils prepares the specimens for optimal abrasion during the tumble polishing process, resulting in a flawless finish.
Surface Inspection
Inspection of the stainless steel surfaces prior to polishing allows collectors to identify any imperfections or scratches that need to be addressed. This step ensures that the specimens are polished uniformly, eliminating blemishes and enhancing the overall appearance of the finished products.
Tumble Polishing Techniques
Tumble Polishing Techniques play a pivotal role in this comprehensive guide, offering rock and fossil collectors essential insights into refining the appearance of stainless steel specimens. By delving into specific elements like abrasive media selection, optimizing tumbling time, and final touches, readers will grasp the intricacies of achieving impeccable results through the tumbling process. The significance of mastering these techniques lies in elevating the visual aesthetics and overall quality of the specimens, transforming them into exquisite pieces that dazzle enthusiasts.
Abrasive Media Selection
Types of Abrasives
Exploring the Types of Abrasives is crucial in understanding how different abrasive materials contribute to the overall tumble polishing process. These abrasives, ranging from silicon carbide to aluminum oxide, each possess unique characteristics that impact the rate of material removal and the level of surface finish achieved. By selecting the appropriate abrasive based on hardness, shape, and particle size, rock and fossil collectors can effectively tailor their tumbling approach to enhance specific aspects of their stainless steel specimens, ensuring a flawless outcome.
Choosing the Right Grit Size
Choosing the Right Grit Size is a paramount consideration when embarking on the tumble polishing journey. The grit size determines the aggressiveness of the abrasive action, influencing the speed and depth of material removal. By understanding the relationship between grit size and surface finish, collectors can determine the optimal grit size for their specimens, striking a balance between efficient polishing and preserving intricate details. This informed selection process guarantees that the desired level of shine and refinement is achieved during tumbling, yielding exceptional results.
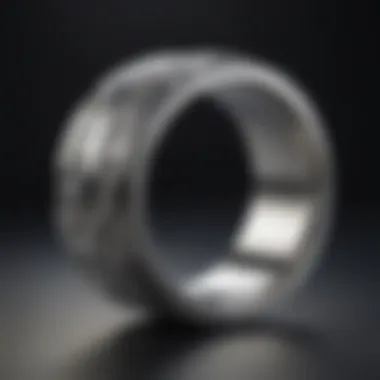
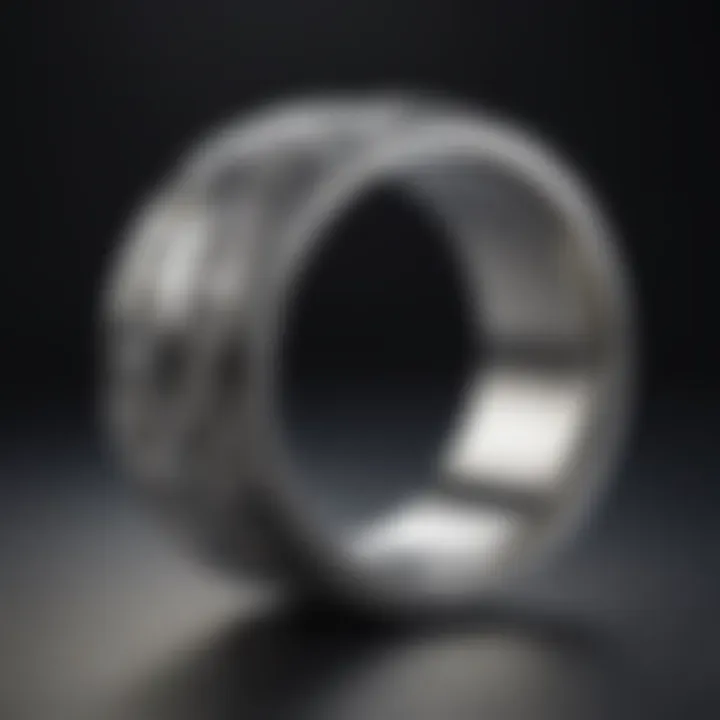
Optimizing Tumbling Time
Factors Affecting Tumbling Duration
Factors Affecting Tumbling Duration are key determinants in the efficiency and effectiveness of the polishing process. Variables such as barrel load, abrasive type, and specimen hardness significantly impact the duration required to attain the desired finish. By recognizing these factors and their interplay, collectors can fine-tune their tumbling parameters to maximize productivity and outcome consistency, ensuring uniform results across all specimens. This meticulous approach fosters precision and control in the tumbling process, empowering collectors to achieve impeccable finishes with minimal deviation.
Monitoring Progress
Monitoring Progress stands as a critical aspect of successful tumble polishing, allowing collectors to track the evolution of their specimens throughout the tumbling cycle. By observing changes in surface texture, shine levels, and overall appearance, enthusiasts can gauge the effectiveness of their tumbling setup and make real-time adjustments as needed. This proactive monitoring facilitates the preservation of specimen integrity and ensures that the desired finish is achieved within the designated tumbling timeframe, promoting efficiency and optimal results.
Finishing Touches
Polishing Compounds
Polishing Compounds serve as the final step in the tumble polishing process, imparting a lustrous sheen to stainless steel specimens. These compounds, formulated with abrasive particles suspended in a carrier solution, facilitate the removal of fine scratches and surface imperfections, enhancing the visual appeal of the specimens. By selecting the appropriate compound based on material compatibility and desired finish, collectors can elevate the brilliance of their specimens to a professional standard, creating a show-stopping display of polished stainless steel.
Final Inspection
Final Inspection marks the culminating stage of the tumbling journey, where collectors meticulously assess the quality and integrity of their polished specimens. By scrutinizing the surface for uniformity, shine consistency, and blemishes, enthusiasts can ascertain the success of the tumbling process and identify any areas that may require further refinement. This detailed inspection ensures that the specimens meet the desired specifications and quality standards, signifying the completion of a meticulous and rewarding tumble polishing endeavor.
Advanced Tips and Troubleshooting
In the realm of tumble polishing stainless steel, the section on Advanced Tips and Troubleshooting plays a pivotal role. The importance of this topic lies in its ability to provide enthusiasts and collectors with invaluable insights into elevating their polishing techniques to achieve exceptional results. By focusing on specific elements such as burnishing techniques, mirror finish methods, addressing common issues, and safety measures, readers can refine their skills and overcome challenges they may encounter during the tumbling process.
Enhancing Shine and Finish
Burnishing Techniques:
Diving into Burnishing Techniques, we uncover a method that contributes significantly to the overall goal of achieving a flawless finish on stainless steel specimens. The key characteristic of Burnishing Techniques is their ability to refine and smoothen surfaces with precision, ultimately enhancing the shine and luster of the material. This technique is a popular choice in the context of this article due to its effectiveness in revitalizing dull surfaces and creating a uniform, high-quality finish. One unique feature of Burnishing Techniques is their versatility, allowing for varying degrees of polish intensity depending on the specific requirements of the specimens being worked on.

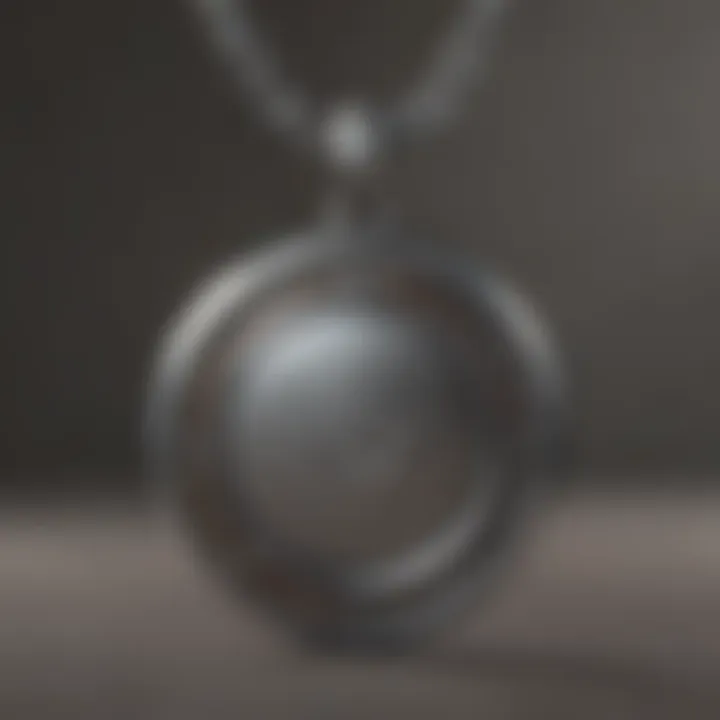
Mirror Finish Methods:
When exploring Mirror Finish Methods, we encounter a technique that makes a substantial impact on the final appearance of stainless steel items. The key characteristic of Mirror Finish Methods is their remarkable ability to produce a reflective surface that mimics a mirror, achieving a polished and flawless look. This method is favored in the context of this article for its proven track record in delivering outstanding results that meet the highest standards. A unique feature of Mirror Finish Methods is their capability to accentuate intricate details while providing a durable and long-lasting finish, making them a desirable choice for enhancing the aesthetics of polished specimens.
Addressing Common Issues
Uneven Polishing:
Delving into Uneven Polishing, we confront a common issue that can hinder the desired outcome of stainless steel tumbling. The key characteristic of Uneven Polishing is its disruptive impact on the overall finish, causing inconsistencies in shine and texture. Despite its negative implications, addressing Uneven Polishing is crucial in perfecting the polishing process, making it a necessary consideration in this article to ensure uniform and high-quality results. One unique feature of resolving Uneven Polishing is the opportunity to apply tailored solutions that rectify specific problem areas, resulting in a flawless and professional finish.
Scratch Removal:
Scratch Removal emerges as a vital aspect in the pursuit of flawless stainless steel specimens post-tumbling. The key characteristic of Scratch Removal is its capacity to eliminate blemishes and imperfections that may detract from the overall aesthetics of polished items. Scratch Removal is a popular choice in this article due to its effectiveness in restoring the pristine appearance of specimens, enhancing their visual appeal. A unique feature of Scratch Removal is its ability to target and eradicate surface flaws with precision, allowing for a seamless finish that meets the highest standards of quality.
Safety Measures
Protective Gear:
Safety Measures encompassing Protective Gear are essential elements to consider when engaging in tumble polishing activities with stainless steel. The key characteristic of Protective Gear is its role in safeguarding practitioners from potential hazards during the polishing process, ensuring their well-being. Protective Gear is a beneficial choice in this article for its ability to provide necessary protection against sharp edges, abrasive materials, and chemical exposure, enhancing the safety of individuals working with stainless steel items. One unique feature of choosing appropriate Protective Gear is the added peace of mind and confidence it instills in users, allowing them to focus on perfecting their polishing techniques without compromising safety.
Proper Ventilation:
Detailing Proper Ventilation as a critical safety measure in stainless steel tumble polishing unveils its significant contribution to creating a safe working environment. The key characteristic of Proper Ventilation is its ability to maintain air quality by dissipating potentially harmful fumes and particles generated during the tumbling process. Proper Ventilation is a popular choice highlighted in this article for its crucial role in minimizing health risks associated with inhaling dust, chemicals, or polishing residue. A unique feature of Proper Ventilation is its capacity to promote a comfortable and healthy workspace, enhancing overall well-being and productivity for individuals engaged in stainless steel polishing activities.
Conclusion
In this comprehensive guide on tumble polishing stainless steel aimed at rock and fossil collectors, the importance of the conclusion section lies in summarizing and reinforcing the key takeaways from the entire article. This final section serves as a crucial wrap-up, highlighting the significance of implementing the techniques and tips discussed throughout the guide. By emphasizing the value of continual learning and practice in achieving optimal polishing results, the conclusion acts as a motivational endpoint for collectors to put their newfound knowledge into action.
Final Thoughts on Tumble Polishing Stainless Steel
Achieving Spectacular Results
Achieving spectacular results in tumble polishing stainless steel is a pivotal aspect that significantly impacts the overall appearance and value of collected specimens. The key characteristic of achieving spectacular results lies in the precision and consistency of the polishing process, ensuring a flawless finish that enhances the visual appeal of the stainless steel pieces. This method is a popular choice for collectors seeking to showcase their specimens in the best possible light, as it brings out the inherent beauty of the stainless steel while maintaining durability. The unique feature of achieving spectacular results is its ability to elevate the aesthetic quality of the specimens, making them stand out in any collection. While this approach requires meticulous attention to detail and patience, the benefits of achieving spectacular results in this article are undeniable, resulting in a remarkable transformation of the polished pieces.
Continual Improvement
Continual improvement plays a vital role in the realm of tumble polishing stainless steel, contributing to the ongoing enhancement of polishing techniques and outcomes. The key characteristic of continual improvement is its focus on refining and adapting existing methods to achieve better results with each polishing cycle. This approach is a beneficial choice for enthusiasts looking to constantly elevate their skills and reach new levels of proficiency in stainless steel polishing. The unique feature of continual improvement is its ability to drive innovation and creativity in the polishing process, fostering a culture of experimentation and growth among collectors. While continual improvement requires dedication and a willingness to embrace change, its advantages in this article are clear; by consistently refining techniques and exploring new approaches, collectors can ensure that their polished specimens continue to evolve and impress over time.