Exploring Stone Cutting Chisels: History and Techniques
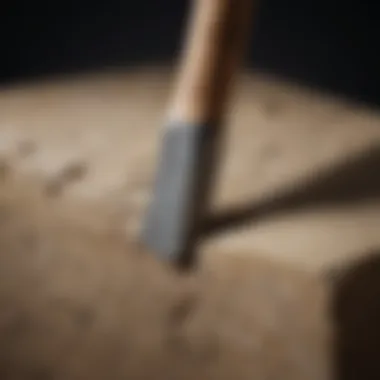
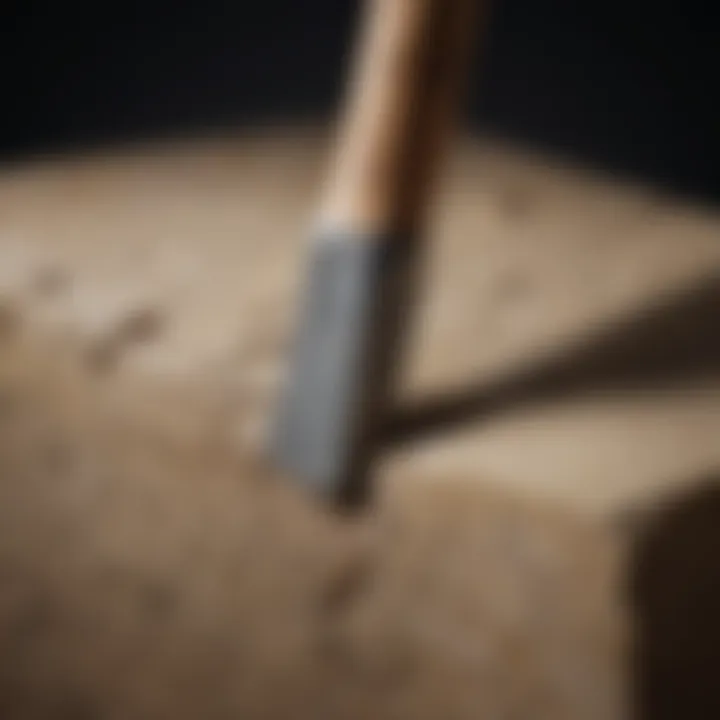
Intro
The world of stone cutting chisels plays a significant role in both art and craftsmanship. Understanding the mechanics of these tools, along with their historical roots, helps artisans refine their skills and enhance the quality of their work. Whether you are a novice eager to learn or an experienced craftsman seeking to sharpen your techniques, grasping the essence of stone cutting chisels is fundamental to your practice.
Stone has been shaped by human hands for thousands of years. From the Great Pyramids in Egypt to the intricate carvings in medieval cathedrals, chisels have enabled artists to express their creativity. This article presents a close look at the different types of chisels, their applications, and maintenance tips that will keep them in peak condition.
At first glance, chisels may seem rudimentary, but they are ultimately pivotal instruments in the delicate dance of stonework. Understanding the varieties available and their proper usage will empower you to turn raw stone into captivating art.
Rock and Fossil Identification
When it comes to stone cutting, it's not just about understanding how to wield a chisel; it's also crucial to recognize the materials you'll be working with.
Types of Rocks and Fossils
Any artisan must first differentiate the types of rocks they will encounter—igneous, metamorphic, and sedimentary. Each type has its unique characteristics:
- Igneous rocks are formed from solidified lava or magma. These include granite and basalt. Their hardness varies, with granite being particularly tough.
- Metamorphic rocks, like marble and slate, have undergone transformation due to heat and pressure. Marble, renowned for its beauty, is a favorite among sculptors.
- Sedimentary rocks such as sandstone and limestone are layered materials, often softer and easier to work with but still possessing their own challenges.
Fossils, remnants of ancient life, can also be found in sedimentary layers. They provide a glimpse into the past, enriching the story of the geological formations you may encounter.
Characteristics to Look For
Identifying rocks and fossils requires a keen eye. Look for:
- Color and Texture: A rock's hue and feel often provide initial clues to its identity.
- Layering: Noticeable layers can indicate sedimentary origins.
- Fossil Imprints: Anomalies in the stone can signal the presence of fossils.
Tools for Identification
Before slicing into the stone, a few tools can assist in identification. For instance, a simple hand lens can magnify small details, while a portable Geiger counter can identify radioactive minerals.
Techniques and Applications of Stone Cutting Chisels
Now that you've got a grasp on rock identification, it’s time to explore the tools that will bring your stone visions to life.
Types of Chisels
Various chisels exist, each designed for specific tasks. Some of the common types include:
- Point Chisel: Used for roughing out shapes and removing large portions of stone.
- Flat Chisel: Ideal for finishing touches, offering a smoother surface.
- Bushing Chisel: This one creates textured surfaces, often used in sculptures.
- Drift Chisel: A specialized tool for creating holes or splitting stone.
Techniques for Usage
Understanding proper techniques ensures precision in your work. Here are some tips for effective stone cutting:
- Always approach the stone with a clear plan of the design. Knowing where to cut eliminates unnecessary mistakes.
- Use controlled strikes when chiseling, adjusting your force based on the rock type.
- Switch between chisels as required, depending on the shape and depth you aim for.
Finale
Mastering the art of stone cutting involves much more than wielding tools. It's about appreciating the history and nature of the materials at hand. Whether you are preserving fossils, identifying rock specimens, or carving intricate designs, each aspect contributes to a full understanding of the craft. By blending historical knowledge with modern techniques, artisans can continue to create breathtaking works that stand the test of time.
Foreword to Stone Cutting Chisels
Understanding stone cutting chisels is essential for anyone working with stone. These tools are not just simple implements; they are the backbone of the craft, allowing artisans to chip away at the solid mass of rock and shape it into something extraordinary. Chiseling has roots that stretch back to ancient civilizations, reflecting the human instinct to create and modify our environment. Knowing about chisels equips enthusiasts and professionals alike with the knowledge to appreciate the intricacies of both the tool and the craft.
Definition and Purpose
Stone cutting chisels are specialized tools crafted primarily for shaping stone. At their core, they consist of a sharp edge attached to a handle, designed to withstand significant force and impact during use. Their purpose transcends mere cutting; they are instruments of artistic creation as well as practical construction. In essence, these chisels empower stoneworkers to:
- Carve Detailed Designs: Whether it's an intricate sculpture or the subtle details of architecture, chisels allow for precision work.
- Create Flat Surfaces: For masonry, the ability to flatten stone is vital for creating structures that stand the test of time.
- Shape Stone for Various Needs: From creating stone tools in ancient times to modern artistic stone carving, the chisel’s versatility remains unmatched.
In this way, they form a bridge between raw material and finished creation, embodying both art and technology.
Historical Background
The history of stone cutting chisels is as rich as the stones they sculpt. The use of chisels dates back thousands of years, with evidence found in ancient Egypt, where workers used copper chisels to carve monuments. As societies advanced, so too did the tools. Bronze and eventually iron chisels emerged during the Bronze Age, enhancing durability and effectiveness.
In the Middle Ages, skilled craftsmen pushed the boundaries of stonework, using chisels to produce stunning cathedrals and castles. The Renaissance saw a flourishing of artistic expression through stone carving, marking a peak in the development of chisels tailored for specific styles and techniques.
"From rough-hewn stones in ancient quarries to the delicately carved statues of today, the evolution of chiseling tools reflects humanity's desire to shape the world."
Today, modern materials like high-alloy steel and innovations in design have further refined the art of stone cutting. Understanding this history not only enriches the appreciation for these tools but also highlights the continuous journey of craftsmanship that defines stonework.
Types of Stone Cutting Chisels
Understanding the various types of stone-cutting chisels is vital for both new and seasoned stoneworkers. Each chisel is designed with unique features that make it particularly suited for different tasks in stone shaping and carving. Whether you're working on a chiseled sculpture or just need to make some precise cuts for masonry, knowing which chisel to employ can save time, effort, and prevent damage to the workpiece. This section dives deeper into the main types of chisels available, detailing their unique advantages and applications.
Point Chisels
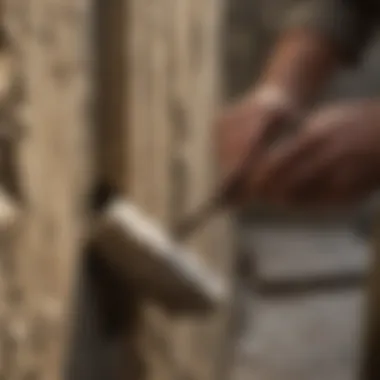
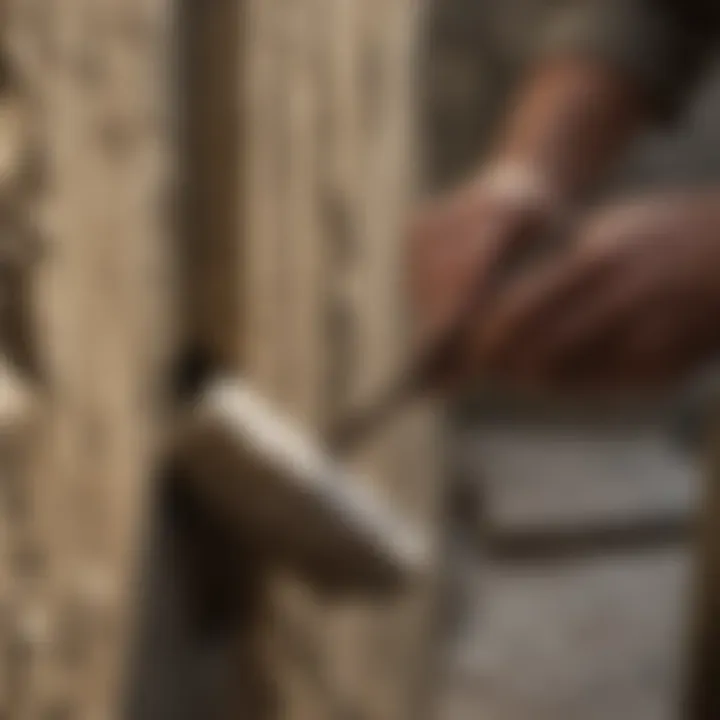
Point chisels are often the first line of attack for stone carvers. Characterized by their pointed tips, they excel at breaking apart stone, making them ideal for roughing out shapes and removing material. When wielded properly, a point chisel can create clean lines and precise indentations. These chisels are particularly useful when starting a new piece of work, allowing the artisan to establish a foundation before refining details.
Flat Chisels
Flat chisels serve a different purpose compared to their pointed counterparts. With a wide, flat blade, they are designed for more extensive operation, making them instrumental in smoothing surfaces or creating broad, even cuts. Their ability to cover a larger area means that they’re fantastic for clearing away excess material quickly. Given their versatility, flat chisels are also commonly found in masonry, where they can help shape hard stone and concrete.
Claw and Plug Chisels
Claw and plug chisels hold a specialized place in stone cutting. The claw chisel, resembling a claw hammer’s front, features sharpened teeth that sink into stone surfaces. It's primarily used for removing hairs or rough patches to create a finer finish. On the other hand, plug chisels serve to create holes or indentations where plug stones can be inserted. This is particularly useful for applications in masonry and stone construction where aligning stones accurately is essential.
Specialized Chisels
Lettering Chisels
Lettering chisels are a unique category designed specifically for creating inscriptions, signs, or decorative engravings. They have a narrower and sharper edge, allowing for precise letters and intricate details. A key characteristic of lettering chisels is their ability to create clean, well-defined characters on stone surfaces. For artisans focused on memorial work or estate signage, these chisels prove to be exceptionally beneficial. However, their delicate structure makes them less effective for heavy-duty tasks like breaking stones or shaping large pieces.
Bevel Chisels
Bevel chisels have a distinctive angled blade, which provides a unique advantage for creating beveled edges or achieving more complex contours in stone. Their ability to redefine angles in stone is what makes them popular among artists and craftsmen who need a polished finish. One notable feature of bevel chisels is the precision cut they can achieve, allowing for detailed work on ornate pieces. However, the specific angle and edge sharpening required can be a disadvantage for those who do not routinely sharpen their tools, as a dull bevel chisel can lead to improper cuts and increased frustration when working on intricate designs.
Material Composition of Chisels
Understanding the material composition of chisels is vital as it significantly influences their effectiveness and longevity. Stone cutting is no easy task, and having the right tools can mean the difference between a smoothly shaped surface and a jagged edge. Composed mainly of various types of steel, chisels require a careful balance of durability, hardness, and resistance to wear. Insights into the materials lead to informed choices, empowering artisans to select chisels that match their specific needs in stone working.
Steel Types
Carbon Steel
Carbon steel stands out as a prevalent choice for stone cutting chisels. Known for its strength and edge retention, this type of steel is carefully crafted by adding a specific amount of carbon to iron. One of the key characteristics of carbon steel is its ability to harden during the manufacturing process, resulting in chisels that can endure the grinding and striking forces encountered during stone cutting.
The unique feature of carbon steel chisels is their straightforward sharpening process. When these chisels dull over time – and they will – resharpening can be accomplished with minimal effort, restoring their effectiveness. However, on the flip side, high-carbon steel chisels can be somewhat brittle. If not handled correctly, they might chip or break under extreme stress. This factor makes them particularly beneficial for regular users who maintain proper care and handling.
Alloy Steel
In contrast, alloy steel chisels are formulated using a mix of various elements, enhancing specific properties like toughness, strength, and resistance to wear. These added materials, such as nickel, manganese, or chromium, provide alloy steels with superior durability compared to their carbon counterparts. The key characteristic that makes alloy steel desirable in chisels is its ability to withstand heavier workloads without significant degradation.
A unique feature of alloy steel chisels is their enhanced fatigue resistance, allowing them to endure repeated strikes without losing integrity. This can be a significant advantage for professionals engaged in demanding stone cutting tasks. That said, alloy steels can be more challenging to sharpen compared to carbon steels. Novices may find the sharpening process a tad more intricate, but the trade-off is a longer-lasting, robust tool that proves its worth over time.
Surface Treatments
Surface treatments further enhance chisels regarding strength and performance.
Hardening Processes
One of the crucial aspects of hardening processes is establishing a chisel's surface hardness while maintaining some flexibility in the core. This flexibility provides added resilience during use, reducing the likelihood of chipping or breaking. A prevalent method for hardening includes heat treatment, where chisels are heated to high temperatures, then cooled through various techniques such as quenching in oil or water.
It’s worth mentioning that while hardening processes significantly increase toughness, improperly managed treatments can lead to warping. Thus, understanding these processes is essential for engineers and manufacturers.
Coatings and Their Benefits
Coatings serve as protective layers on chisels, augmenting their resilience against wear and corrosion. Common surface coatings include tungsten carbide or titanium nitride. These coatings are typically applied through processes such as vapor deposition.
A key benefit of these coatings is their ability to prolong the lifespan of the chisels, ultimately delivering greater value for money. However, not all coatings are equal. While they can enhance surface hardness and reduce friction during use, they may also add a layer of complexity during resharpening. Some artisans prefer to avoid coated chisels since it can complicate the maintenance process, potentially outweighing the benefits.
Techniques in Stone Cutting
Understanding the various techniques in stone cutting provides artisans with essential skills needed for refining their craft. These techniques, whether basic or advanced, enable stoneworkers to transform raw materials into precise and beautifully detailed pieces. Mastery of these methods elevates one's work, ensuring that every cut is intentional and contributes to the overall vision of the piece. Such techniques not only dictate the flow of the work process but also impact the final product's aesthetics and structural integrity.
Basic Chiseling Techniques
Basic chiseling techniques constitute the foundation for any stonecarver's skillset. They often include fundamental methods like striking techniques, tool positioning, and controlled pressure application. For instance, a well-placed blow with a hammer can yield a clean line, while an errant tap can result in unwanted chips. Learning to control the angle of attack and cycle of pressure makes all the difference in achieving precise cuts.
Common techniques include:
- Direct or hammer chiseling: Utilizing a hammer and chisel together, this approach strikes directly onto the stone, allowing for immediate shaping.
- Rubbing: This involves using a flat chisel to smooth out stone surfaces, ensuring an even finish that prepares the stone for further detailing.
- Pitting: By creating small indentations on the stone surface, one can create textures or patterns before moving to more detailed work.
These basic methods empower beginners, providing them with tools to handle various stone materials confidently.
Advanced Techniques
Advanced techniques in stone cutting push boundaries, allowing experienced artisans to explore intricate designs and unique methods. These techniques require a deeper understanding of both the tools and the materials at hand. Among the advanced techniques, two notable methods are Pattern Punching and Curvilinear Cuts.
Pattern Punching
Pattern punching is a technique that enables stoneworkers to create decorative designs or intricate patterns on the surface of stone. The key characteristic of pattern punching is its ability to provide a repetitive, yet customizable approach to stone decoration. This technique stands out due to its precision; artisans can produce complex designs methodically. In this context, the uniqueness of pattern punching is evident as it allows for both creativity and consistency, making it a popular choice for architects and artists alike.
However, the technique’s precision might require considerable practice, especially when aiming for a flawless execution. The primary advantage is the efficiency with which complex patterns can be replicated, but one must also be wary of potential mistakes that can mar the overall piece if not executed correctly.
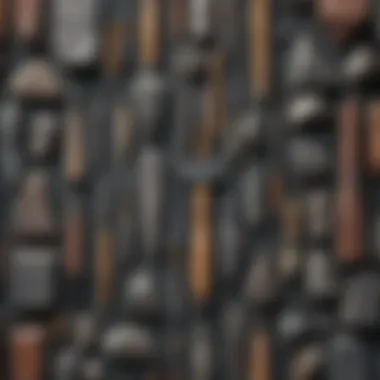
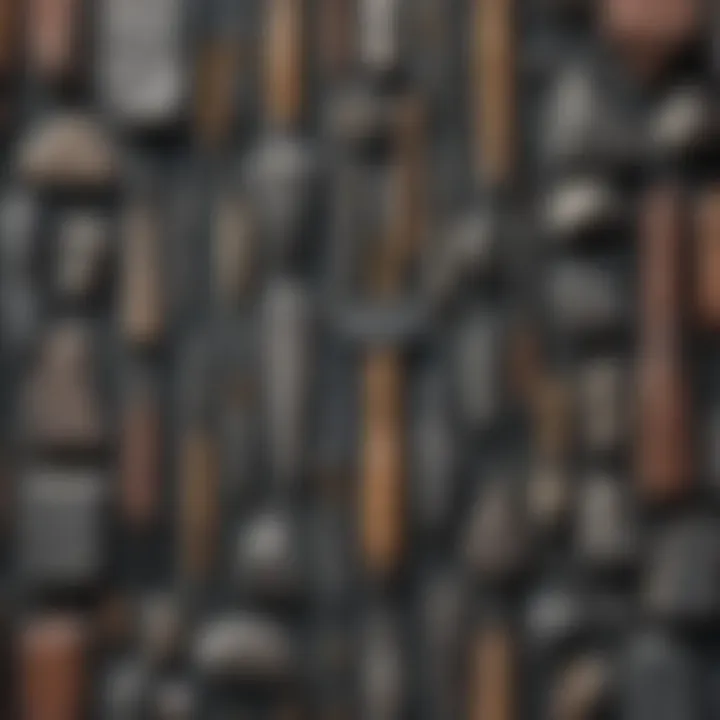
Curvilinear Cuts
Curvilinear cuts refer to the smooth, flowing contours that artisans create in stone. This technique is particularly valuable when crafting organic shapes or intricate designs that require a gentle touch. The main aspect of curvilinear cuts lies in their aesthetic appeal and functionality, often giving a naturalistic quality to sculptures and architectural features.
What distinguishes curvilinear cuts is their capacity to breathe life into the stone, as it appears to flow with motion rather than sit rigidly. Although it requires an advanced level of technique to execute these cuts correctly, it is beneficial in achieving harmonious designs.
However, operating with curves can be more challenging compared to straight lines, increasing the risk of miscalculating angles or pressure, which could lead to material wastage. Despite these challenges, when mastered, this technique can elevate the craftsmanship to remarkable heights.
"Mastering both the basic and advanced techniques of chiseling is not merely about the tools used, but about the artistry of shaping stone into meaningful forms."
As artisans refine these skills, they will find that the techniques they choose to employ will significantly influence their work, directly impacting both their creative expression and the functionality of the stone pieces they develop.
Proper Usage of Stone Cutting Chisels
Understanding the proper usage of stone cutting chisels is essential, especially for artisans and hobbyists alike. It not only ensures efficiency and precision in work but also significantly reduces the risks associated with stone cutting. Misusing tools can lead to subpar results and even accidents. Therefore, knowing how to handle chisels correctly is fundamental for anyone involved in stonework, whether they're crafting sculptures, executing architectural designs, or restoring historical artifacts.
Safety Precautions
When wielding stone cutting chisels, safety should always be at the top of the priority list. Here are a few key safety measures to keep in mind:
- Eye Protection: Always wear safety goggles. Chips and dust can fly unpredictably, possibly causing eye injuries.
- Gloves: While handling chisels and stone, protective gloves can provide an extra layer of security against sharp edges.
- Stable Work Surface: Ensure that the stone is securely anchored. An unstable surface can lead to accidents.
- Proper Stance: Maintain a balanced stance. Standing safely can help you control the chisel better, minimizing the chances of slipping.
Safety isn’t just about personal protection. It’s also about maintaining a productive working environment.
Tools and Equipment
To maximize effectiveness and safety while using chisels, several tools and pieces of equipment can enhance your experience.
Safety Gear
Safety gear plays a crucial role in the proper usage of stone cutting chisels. This includes not only protective eyewear and gloves but also hard hats and hearing protection when necessary. The key characteristic of safety gear is that it provides a barrier against potential hazards in the environment. For stonework, this is particularly relevant because of the risk posed by flying debris and heavy materials.
A beneficial choice for many stoneworkers has been the use of cut-resistant gloves. These gloves uniquely combine dexterity with protection, allowing for fine control while safeguarding fingers from cuts. However, their advantage can also be a disadvantage. If they are too thick, they might hinder delicate chiseling work where precision is paramount.
Support Tools
Support tools include clamps and vices that help secure the stone while you work. Their contribution to the overall goal of safe and effective stone cutting cannot be overstated. The key characteristic of support tools is their ability to stabilize the workpiece, allowing for greater control during the chiseling process.
Many stoneworkers find that using a bench vice not only secures their material but also frees their hands to focus on creating the desired shape. A unique feature of these tools is their adjustability, which allows for a customized fit for different stone sizes. The drawback, however, may be the need for extra setup time.
"Safety is not just a responsibility; it's a vital necessity in stone cutting."
Maintenance of Stone Cutting Chisels
Maintaining stone cutting chisels is crucial for any artisan or stone worker. Just like a craftsman takes pride in working with quality materials, the longevity and effectiveness of chisels heavily depend on regular maintenance practices. By caring for these tools, one can ensure accuracy in every cut, retain their efficiency, and minimize potential hazards during use.
Proper maintenance extends the lifespan of chisels, which ultimately saves time and money in the long run. Neglected tools become dull and ineffective, leading to inefficient work and the potential for more significant hazards. Regular cleaning, sharpening, and proper storage are key components of an effective maintenance routine.
Cleaning Procedures
Cleaning your chisels requires a systematic approach. When stone dust and debris accumulate, they can affect the cutting edge and the overall performance. A quick cleanup after each use goes a long way. Here’s how to go about it:
- Brush away debris: Use a stiff brush to remove dust and small stone particles from the chisel’s surface. Avoid moisture, as it can prompt rusting, especially on carbon steel chisels.
- Wipe with a cloth: Following the brush, a dry cloth can help to ensure no remaining dust lingers on the chisel.
- Inspect for damage: While cleaning, take a moment to inspect the chisel for any chips or cracks. Early detection can prevent further damage.
By sticking to a routine, you protect the integrity of these tools, ensuring optimal performance whenever they're put to work.
Sharpening Techniques
When it comes to sharpening chisels, two predominant methods are discussed: manual sharpening and mechanical sharpening. Both have their distinct advantages, depending on the precision and effort an artisan is willing to invest.
Manual Sharpening
Manual sharpening is often favored for its ability to give the artisan complete control over the angle and pressure applied. A whetstone or sharpening file is commonly used, allowing for a nuanced touch that can shape the edge perfectly to the desired angle.
- Key Characteristic: This method enhances the artisan's skill. It allows for detailed, careful work, which can be especially important for more intricate designs.
- Unique Feature: The tactile feedback received during manual sharpening is invaluable. Artisans can feel the chisel’s edge becoming sharper under their fingers, making it easier to achieve the desired sharpness.
- Advantages/Disadvantages: While it can be time-consuming, manual sharpening often results in a finely tuned edge, suitable for intricate tasks. On the downside, it may require a steeper learning curve for beginners.
Mechanical Sharpening
On the other hand, mechanical sharpening employs machines, such as bench grinders or belt sanders, to quickly restore edges.
- Key Characteristic: This method excels in speed. It’s particularly useful for those who have many chisels or large workloads.
- Unique Feature: Mechanical sharpeners often come with adjustable settings that can accommodate different chisel profiles, which makes it versatile.
- Advantages/Disadvantages: While it can save time, there is a risk of over-grinding if precision is not carefully monitored, which could lead to uneven edges or damage.
Storing Chisels Properly
Storing chisels the right way has its own importance. Improper storage can lead to physical damage or deterioration over time. Here are a few guidelines to consider:
- Dedicated storage: Use a dedicated toolbox or a rack designed for holding chisels. This prevents them from knocking against one another, which can dull or chip the edges.
- Dry environment: Always store chisels in a dry space. Moist environments lead to rust, especially with tools made from carbon steel.
- Avoid overcrowding: If chisels are packed too tightly, it increases the risk of edge damage and makes it challenging to find the right tool when needed.
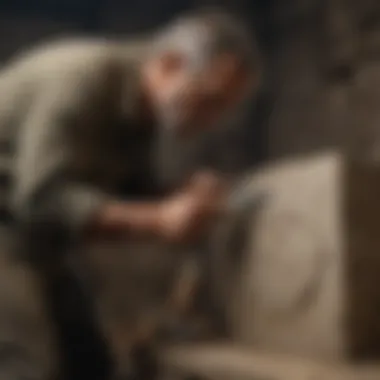
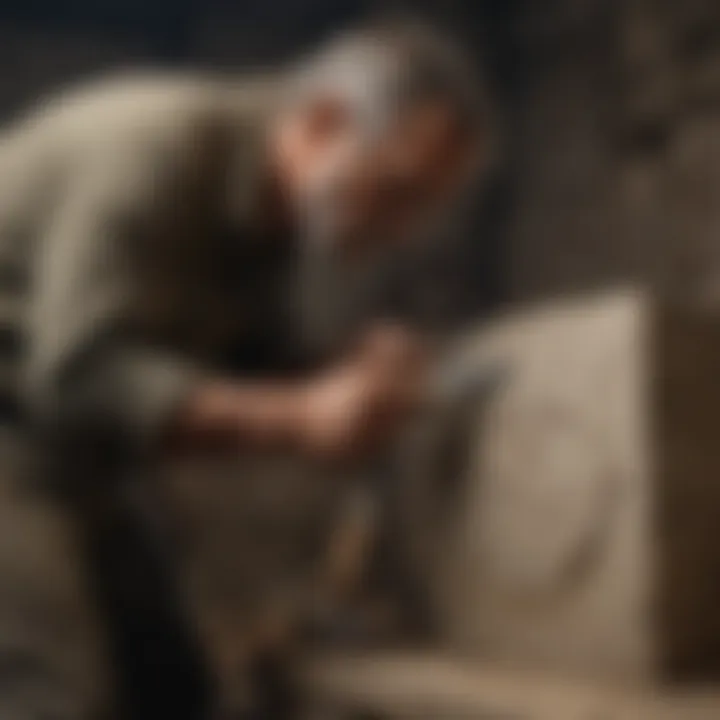
"Well-maintained tools make for a well-maintained craft, and investing time in care can yield remarkable benefits."
By following these maintenance practices, stone cutting chisels can retain their effectiveness and reliability, making them indispensable tools in any stone worker's arsenal.
Applications in Various Fields
The realm of stone cutting chisels extends far beyond the simple act of carving. Their applications in diverse fields highlight the importance of skillful manipulation of stone to create functional art. Here, we delve into the integral roles that these tools play in three primary areas: artistic stone carving, architectural masonry, and restoration projects.
Artistic Stone Carving
Artistic stone carving is a discipline that thrives on creativity and precision. Stone cutting chisels are essential for transforming raw stone into intricate sculptures and ornamental designs. Artists select specialized chisels that suit their artistic vision—each chisel type, like the detailing of the bevel or the fineness of a lettering chisel, can significantly influence the final piece.
A notable benefit of using these chisels is their ability to achieve fine detail and texture. Artists often rely on point chisels for initial shaping and flat chisels for smoothing surfaces. The tactile nature of stone itself adds to the artist's inspiration, as every strike against the hard surface yields a reshaping of both the material and the artist's intent. Here, the relationship between stone and craftsman is dynamic, creating a tapestry that marries technique with artistic expression.
Architectural Masonry
In architecture, stone cutting chisels are indispensable tools that facilitate the creation of sturdy structures. They are employed extensively in masonry to shape and join stones, ensuring that buildings stand the test of time. The precision afforded by chiseling is vital, as unevenly cut stones can compromise the structural integrity of a building.
Moreover, the use of chisels allows for aesthetic considerations. Stonemasons often create decorative elements, blending functionality with artistry. This intersection of beauty and engineering is where design meets durability. Depending on project requirements, different chisels are utilized to achieve varied finishes and outlines, ensuring that buildings harmoniously fit into their environments while serving their purposes.
Restoration Projects
Restoration projects represent another critical application for stone cutting chisels. When restoring historical buildings or monuments, artisans face the task of matching the original stonework. Here, the importance of understanding material properties and historical techniques becomes paramount.
Using chisels with care, craftsmen can meticulously remove damaged sections of stone and replace them with new pieces that blend seamlessly into the original structure. This process not only requires technical accuracy but also a deep respect for the historical context of the work.
Key considerations in restoration include:
- Material Matching: Ensuring that the new stone matches the original, avoiding aesthetic pitfalls.
- Techniques Preservation: Employing traditional chiseling methods that honor the craftsmanship of earlier artisans.
- Informed Sensitivity: Recognizing the historical and cultural significance of the structures being restored.
In many ways, restoration acts as a dialogue between the past and present, facilitated by chisels that hold the power to mend and preserve.
In summary, stone cutting chisels are not just tools; they are vital instruments that empower artisans across various fields. Whether sculpting a piece of art, constructing an enduring building, or restoring a treasured historical site, the artistry and science of stone cutting chisels continue to leave an indelible mark on our cultural landscape.
Challenges in Stone Cutting
When engaging in the meticulous craft of stone cutting, various challenges arise that can complicate even the most straightforward of projects. Addressing these challenges is not just a necessity, but an integral part of mastering the art. Learning about these obstacles provides insights into how to maneuver around them, thus ensuring smoother workflows and superior results.
Material Variability
Stone, in its essence, is not a uniform material. Different types possess varied hardness, texture, and structural integrity. This variability influences the choice of tools and techniques. For instance, granite is famously tough, necessitating robust chisels, whereas softer stones like limestone can often be shaped with less intensive tools.
Moreover, even within a single type, factors such as mineral composition and weathering can affect stone quality. Artisans must be prepared to assess these characteristics on-site. Performing a preliminary test cut can provide vital feedback about the chisel's performance and the appropriate force needed.
"Understanding the stone's nature is one half of the battle. The other half? Adapting your approach accordingly."
It’s worth noting that different stones can behave unpredictably. For example:
- A chisel may glide effortlessly through one section of the marble but struggle in another due to density differences.
- Unseen fractures or inclusions can lead to unexpected breaks, challenging the artisan's skill and patience.
Tool Wear and Tear
As much as the stone presents its own complications, the chisels themselves are not immune to wear and tear. Over time, cutting edges dull, reducing effectiveness and precision. Regular maintenance is essential to prolonging the lifespan of chisels.
When chisels become worn, several issues can arise:
- Increased effort required: A dull chisel demands more pressure, which not only slows down the process but can also lead to injuries.
- Reduced quality of work: Without a sharp edge, achieving clean cuts becomes a formidable challenge, resulting in jagged edges instead of smooth finishes.
- Inconsistent results: Variability in tool condition can affect uniformity across a project.
To mitigate these issues, artisans need to adopt a proactive maintenance routine. Techniques such as regular sharpening should be integrated into the work process.
Additionally, investing in high-quality chisels, like those from brands such as Black Diamond or Estwing, can significantly ease some of the wear problems. Remember, a well-maintained tool not only extends its usability but enhances the overall craftsmanship of the project.
Future Directions in Stone Cutting Technology
As we step into a new era of craftsmanship in stone cutting, the evolution of tools and methods holds both promise and intrigue. Innovations in technology are pivotal for enhancing the efficiency and precision of stonework, catering to the demands of modern artisans and rock enthusiasts alike. Understanding these advancements is crucial for anyone keen on mastering the art of stone cutting. With the industry evolving, we can expect exciting developments on the horizon.
Emerging Tools and Techniques
The landscape of stone cutting is witnessing the birth of several groundbreaking tools that redefine traditional practices. Manufacturers continuously innovate, introducing diamond-tipped chisels and pneumatic chisels that significantly enhance the cutting process. These tools not only streamline the work but also reduce physical strain on the artisan. Here are some notable emerging tools:
- Laser Cutters: Laser technology is gradually penetrating the stone cutting market. These machines offer precision and the ability to execute intricate designs with ease. They minimize waste and errors, leading to better material utilization.
- Water Jet Cutters: Utilizing high-pressure water mixed with abrasive particles, water jet cutters can slice through stone with an accuracy that is hard to achieve using conventional methods. This technology opens the door to complex shapes and designs, allowing for greater artistic expression.
- CNC Machines: Computer Numerical Control machines have revolutionized various manufacturing industries, including stonework. CNC routers automate the cutting process, ensuring consistent quality and reducing human error. Craftsmen can design patterns digitally, and the machine will replicate them precisely.
These tools make stone cutting not just a laborious task, but a sophisticated, high-tech craft. As they become more affordable and accessible, they’re likely to find a place in both professional and hobbyist workshops.
Integration with Digital Technologies
The integration of digital technologies into stone cutting processes is another promising frontier. This evolution is not merely a trend; it’s a substantial shift in how artisans approach their craft. The marriage of digital design and stone manipulation leads to several compelling advantages:
- Precision Design Software: Programs such as AutoCAD or Rhino allow artisans to create detailed, precise designs. These digital blueprints can be directly fed into CNC machines, ensuring that the final product matches the envisioned design accurately, saving time and material.
- 3D Printing in Prototyping: Before carving into stone, 3D printing techniques can be leveraged to create prototypes of designs. This allows artisans to visualize their work in different scales and material, providing an opportunity for adjustments early in the process.
- Virtual Reality Tools: Some cutting-edge artisans are using virtual reality to simulate their stone cutting environments. These tools enable users to practice and visualize their cuts in a virtual space, refining their techniques and decisions before touching the stone.
The future of stone cutting tech isn't just about faster tools; it's about a holistic approach where artisans can combine traditional skills with modern innovations. This synergy enhances creativity, productivity, and ultimately, the quality of stonework.
"As technology expands, so does our ability to explore and express creativity through the enduring medium of stone."
Embracing these advancements not only paves the way for better craftsmanship but also empowers a new generation of stone workers to push the boundaries of what’s possible in the field. Just as the ancients shaped their environments with the tools of their time, contemporary artisans now have the unique opportunity to craft their visions with a blend of tradition and innovation.