Unveiling the Art of Metal Casting: A Beginner’s Extensive Guide
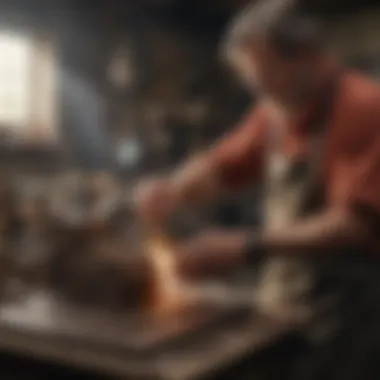
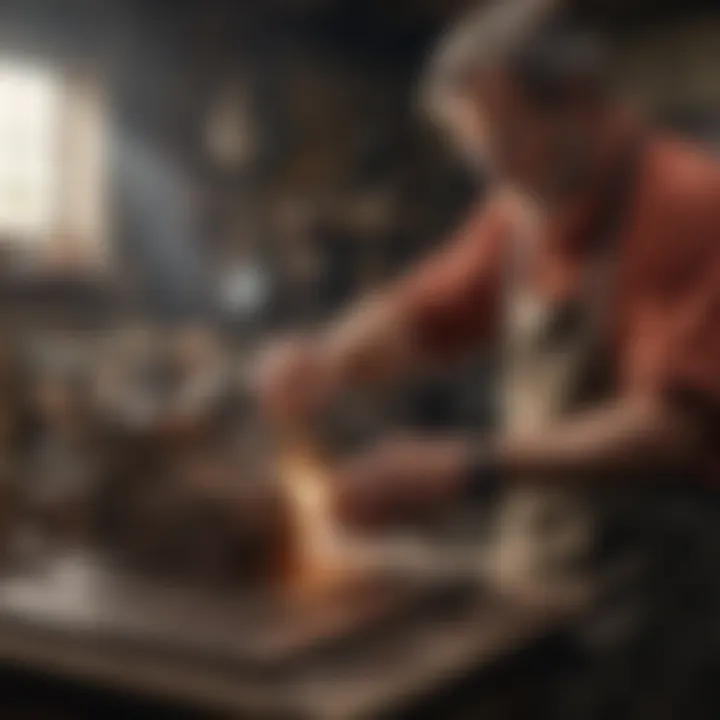
Rock and Fossil Identification
In the realm of metal casting, a fundamental aspect is understanding the types of metals that are commonly used in the process. Among the most prevalent are iron, steel, aluminum, and copper, each possessing distinct characteristics and properties that influence their suitability for various casting techniques. Beginners must familiarize themselves with these metals' unique attributes to make informed decisions when embarking on their casting projects. It is essential to recognize the different melting points, fluidity levels, shrinkage rates, and other factors that play a crucial role in the casting process.
As enthusiasts progress in their metal casting journey, they will encounter advanced techniques that require a deeper understanding of alloy compositions, metallurgical reactions, and intricate design considerations. Delving into these complexities opens up a world of creative possibilities, allowing practitioners to experiment with intricate molds, intricate shapes, and specialized casting methods. These advanced techniques elevate the art of metal casting, enabling enthusiasts to push the boundaries of their creativity and craftsmanship.
Collecting Tips and Techniques
When it comes to collecting materials for metal casting, beginners should adopt best practices that ensure the quality and integrity of their projects. Choosing high-quality raw materials is paramount, as impurities or inconsistent compositions can compromise the final casting results. It is advisable to source materials from reputable suppliers or trusted sources to guarantee the authenticity and purity of the metals.
Locating prime collecting sites can also significantly impact the quality and diversity of materials available for casting. Beginners should explore a variety of sources, including specialized metal shops, online marketplaces, scrapyards, and recycling centers, to expand their inventory of raw materials. By diversifying their sources, enthusiasts can access a broad range of alloys, ingots, scrap metals, and other materials that can enrich their casting projects.
To safely extract specimens from their collected materials, beginners must adhere to proper handling and processing procedures. This includes using appropriate safety gear, following established guidelines for cutting and shaping metals, and implementing effective ventilation systems to minimize exposure to fumes or hazardous particles. By prioritizing safety measures and best practices in material handling, enthusiasts can create a secure and controlled environment for their casting endeavors.
Preservation and Display
After mastering the art of metal casting, enthusiasts may wish to explore techniques for preserving their creations and displaying them with pride. Preservation methods vary depending on the types of metals used in casting, as different alloys may require specific care to prevent corrosion, oxidation, or structural degradation. Utilizing protective coatings, storage solutions, and climate-controlled environments can extend the longevity and aesthetics of cast metal objects.
Proper storage methods are essential for maintaining the quality and condition of completed casting projects. Enthusiasts should store their creations in dry, cool environments to minimize the risk of moisture damage or environmental degradation. Additionally, organizing and cataloging cast metal pieces can facilitate easy access and retrieval for future display or reference, enhancing the overall experience of metal casting enthusiasts.
Creative display ideas offer a platform for enthusiasts to showcase their metal casting skills and creativity. Whether designing custom stands, mounting options, or exhibition arrangements, creative presentation enhances the visual impact and storytelling behind each cast metal piece. By incorporating innovative display techniques, enthusiasts can captivate viewers, spark conversations, and leave a lasting impression with their metal casting creations.
Geological Insights
While metal casting focuses on the art and science of shaping molten metals, it is essential to appreciate the geological insights that underpin this craft. Understanding geological formations, natural processes, and the historical significance of metals provides a context for enthusiasts to deepen their appreciation and knowledge of the materials they work with. By exploring the origins of metals, their mineral compositions, and the geological forces that shape them, practitioners can gain a newfound respect for the inherently dynamic nature of metals.
Furthermore, delving into the historical significance of metals uncovers a rich tapestry of cultural, industrial, and artistic developments that have shaped human civilization. From ancient metallurgy practices to modern innovations in alloy design, the legacy of metals resonates across time and continents, reflecting humankind's ingenuity and resourcefulness. By tracing the historical lineage of metals, enthusiasts can connect with a legacy of craftsmanship, innovation, and cultural exchange that continues to inspire contemporary metal casting practices.
Notable discoveries in the field of metal casting offer insights into groundbreaking technologies, artistic achievements, and visionary projects that have propelled the craft forward. From innovative casting methods to revolutionary material hybrids, these discoveries showcase the boundless potential of metal casting as a dynamic and evolving discipline. By staying informed and engaged with the latest developments in the field, enthusiasts can draw inspiration, guidance, and motivation to push the boundaries of their own metal casting endeavors.
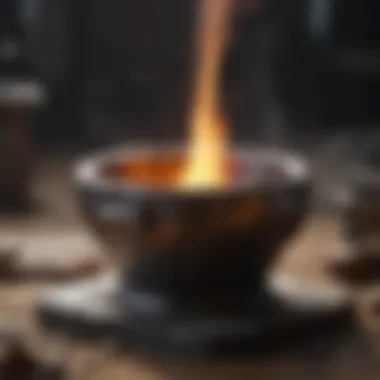
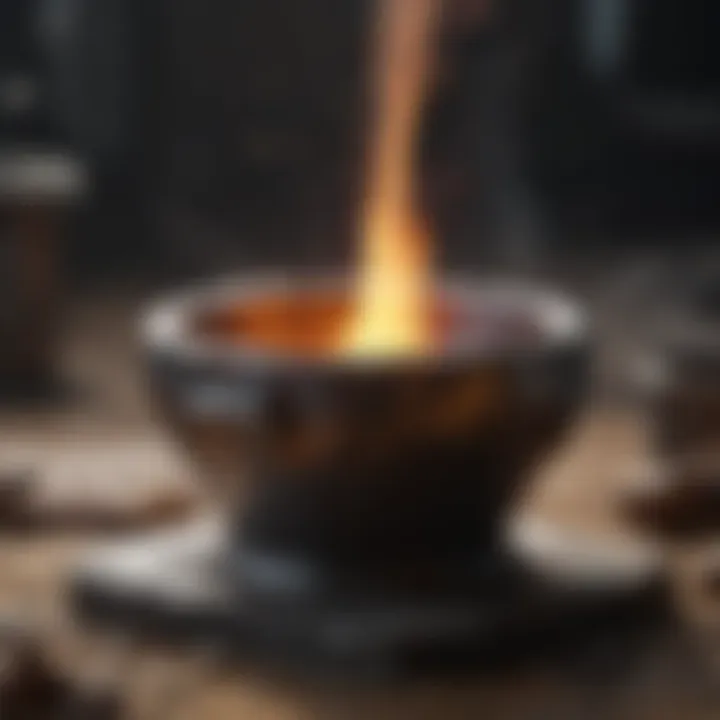
Introduction to Metal Casting
Metal casting is a fundamental process in manufacturing, with a rich history and extensive industrial applications. This section serves as a gateway to the intricate world of metal casting, laying the foundation for beginners to explore this fascinating field in depth. Understanding the basics of metal casting is crucial for enthusiasts looking to hone their skills and knowledge in this craft. Whether pursuing it as a hobby or a potential career path, mastering metal casting promises a creative outlet and a valuable skill set.
Exploring the Origins of Metal Casting
Metal casting dates back thousands of years, with ancient civilizations like the Mesopotamians and Egyptians pioneering early casting techniques. The Evolution of Metal Casting Techniques has seen significant advancements over time, from the use of basic molds to complex foundry operations. These techniques have played a vital role in the development of various industries, revolutionizing manufacturing processes and driving innovation.
Importance of Metal Casting in Industrial Applications
Metal casting plays a key role in a wide range of industrial applications, serving as the backbone of many manufacturing processes. The Key Role of Metal Casting in Manufacturing Processes lies in its ability to produce intricate parts and components with precision and efficiency. By utilizing metal casting, industries can create complex shapes, durable products, and customized solutions to meet diverse market demands. The versatility and reliability of metal casting make it a valuable technique for various sectors, including aerospace, automotive, and engineering.
Basic Principles of Metal Casting
In the realm of metal casting, understanding the basic principles is paramount. This section serves as a foundational pillar in our comprehensive guide, laying the groundwork for enthusiasts to grasp the core concepts essential for successful metal casting endeavors. Delving into the intricacies of metal casting processes, materials, and techniques, this section aims to equip beginners with the necessary knowledge to navigate the world of metalwork with confidence.
Understanding Foundry Operations
Melting and Pouring Techniques:
Exploring the nuances of melting and pouring techniques is crucial in metal casting. Melting raw materials to their molten form and skillfully pouring them into molds are fundamental steps in the casting process. This section sheds light on the significance of precision in temperature control, ensuring the proper flow and solidification of molten metal for impeccable castings. The key characteristic of melting and pouring techniques lies in their ability to transform solid metals into fluid states, allowing for the creation of intricate shapes and designs. While these techniques require mastery and experience, they are indispensable in achieving high-quality castings in various industrial applications.
Mold Preparation and Casting:
Mold preparation and casting are intricate processes that underpin the success of metal casting projects. From designing mold cavities to selecting appropriate materials, every step impacts the final product's quality and integrity. This section delves into the meticulous craftsmanship involved in preparing molds, emphasizing the need for attention to detail and precision. The unique feature of mold preparation and casting lies in the art of shaping and solidifying molten metal within custom-made molds, unveiling creative possibilities for casting enthusiasts. While offering unparalleled flexibility in design and composition, this method requires strict adherence to safety protocols and best practices to mitigate potential challenges during metal solidification.
Types of Metals Used in Casting
Aluminum, Bronze, Iron, and Steel Alloys:
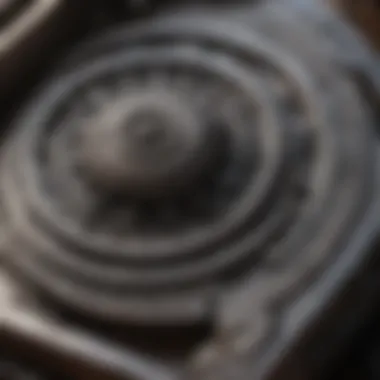
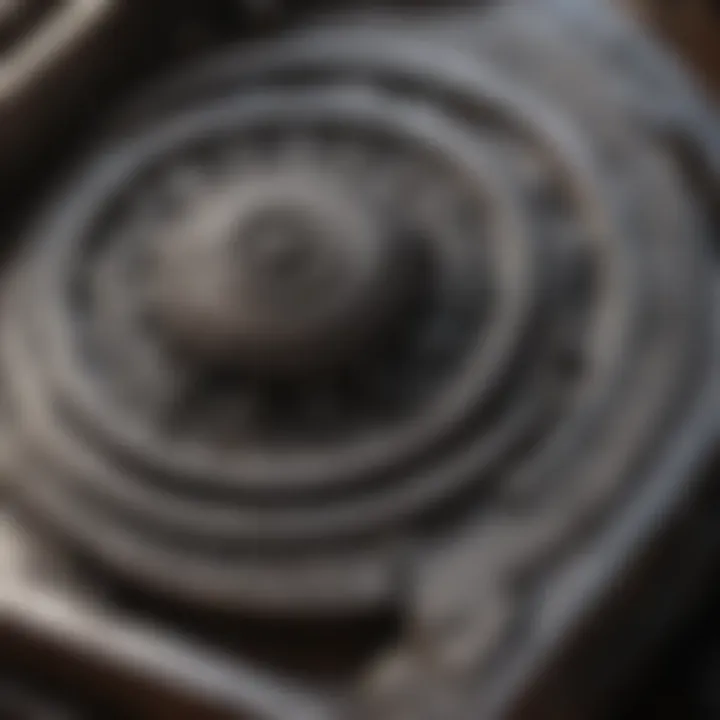
The selection of metals plays a critical role in metal casting, with aluminum, bronze, iron, and steel alloys standing out as popular choices for their diverse properties and applications. Each metal type brings unique characteristics to the casting process, influencing factors such as durability, thermal conductivity, and corrosion resistance. This section explores the distinct advantages and disadvantages of utilizing aluminum, bronze, iron, and steel alloys in metal casting projects. Highlighting the versatility of these metals in creating intricate designs and functional components, it underscores the importance of selecting the right material to achieve desired outcomes.
Essential Tools and Equipment
Metal casting is a precise craft that requires a range of essential tools and equipment to ensure successful outcomes. In this section, we will delve into the significance of having the right tools at your disposal, focusing on specific elements that play a crucial role in the metal casting process.
As aspiring metal casters, understanding the importance of essential tools and equipment is fundamental to master the art of metal casting effectively. Each tool serves a unique purpose in the overall casting process, contributing to the quality and accuracy of the final products. From preparing the molds to melting and pouring metals, having the appropriate tools can streamline the entire casting operation and elevate the results to new levels of craftsmanship.
Crucial Tools for Metal Casting
Crucibles, Ladles, Molds, and Fluxes
Crucibles, ladles, molds, and fluxes stand as the cornerstone tools in the realm of metal casting, each offering distinctive features that are indispensable for successful casting outcomes. Crucibles, essential for melting metals, come in various materials such as graphite and clay, with each material offering unique benefits in terms of durability and heat resistance. Ladles play a crucial role in transferring molten metal from the crucible to the mold, ensuring precise pouring and minimal wastage. Molds, on the other hand, are central to shaping the final castings, determining the design and intricacy of the end product. Fluxes, though less commonly discussed, are vital for removing impurities from the molten metal, enhancing the overall quality of the castings.
The key characteristic of these tools lies in their specialized functions that complement each other throughout the casting process, ensuring a seamless transition from raw materials to finished products. The versatility and adaptability of crucibles, ladles, molds, and fluxes make them a popular choice among metal casters, enabling precise control over the casting environment and ensuring consistent results.
Moreover, the unique feature of these tools lies in their ability to withstand extreme temperatures and harsh casting conditions, showcasing their resilience and reliability in demanding metal casting operations. While these tools offer numerous advantages in terms of efficiency and precision, users must also be aware of their limitations, such as the need for proper maintenance and handling to prolong their lifespan and ensure optimal performance.
Step-by-Step Guide to Metal Casting
In a detailed exploration of metal casting, the Step-by-Step Guide section serves as a pivotal component within this comprehensive article. This segment aims to enlighten beginners on the intricacies involved in the metal casting process, guiding them through each essential step methodically and logically. By breaking down the casting procedure into manageable stages, novices can grasp the complexities of metal casting and develop a solid foundation to build upon in their crafting journey. Understanding the nuances of each stage outlined in the Step-by-Step Guide is crucial for enthusiasts looking to delve into this traditional yet artful technique. ### aring the Workspace #### Se Up Foundry Equipment Safely Foundry equipment setup plays a critical role in ensuring a safe and efficient metal casting operation. By meticulously arranging and calibrating the furnaces, crucibles, and other vital tools, casters can prevent accidents and optimize the casting process. The key characteristic of setting up foundry equipment safely lies in meticulous attention to detail and adherence to established safety protocols. This approach is a popular choice for this article as it underscores the importance of workplace safety in metal casting practices. The unique feature of setting up foundry equipment safely is its ability to create a secure work environment that minimizes risks and enhances overall efficiency when executing casting tasks. ### Creating Designing Molds #### Patterns, C and Mold Making Techniques Exploring the realm of mold design is paramount in metal casting, with patterns, cores, and specific mold making techniques playing significant roles in shaping the final casting products. Understanding the intricacies of pattern creation, core placement, and mold construction is essential for achieving precise and high-quality castings. The key characteristic of patterns, cores, and mold making techniques is their role in determining the final shape and structure of the cast metal product, influencing its finish and overall quality. This aspect is a beneficial choice for this article as it highlights the craftsmanship and attention to detail required in mold design processes. The unique feature of patterns, cores, and mold making techniques lies in their versatility, allowing casters to experiment with various designs and functionalities to customize their castings according to specific requirements. ### Melting and Pouri tal #### Proper Techniques fo ing Metal Alloys Mastering the art of melting metal alloys is a fundamental aspect of metal casting that requires precision and skill. Proper techniques for melting metal alloys involve understanding the melting points of different metals, maintaining optimal temperatures, and ensuring a homogeneous molten metal composition for casting. The key characteristic of proper melting techniques is their ability to transform solid metal into a molten state suitable for molding, ensuring consistency and quality in the casting process. This practice is a popular choice for this article as it underscores the significance of controlled melting processes in achieving successful castings. The unique feature of proper techniques for melting metal alloys is their capacity to enhance casting efficiency and product quality, enabling casters to create durable and well-formed metal castings. ### Casting and Finishing #### ving Castings, Cleaning, lishing The final stage of casting involves the meticulous process of removing the castings from molds, cleaning any excess material, and polishing the finished products to achieve a refined and aesthetically pleasing appearance. Proper removal, cleaning, and polishing techniques are crucial in ensuring the integrity and visual appeal of the cast metal items. The key characteristic of removing castings, cleaning, and polishing is their role in enhancing the final product's presentation and durability, resulting in professional-looking metalwork. This process is a beneficial choice for this article as it emphasizes the importance of post-casting procedures in achieving flawless and market-ready metal castings. The unique feature of removing castings, cleaning, and polishing lies in the craftsmanship and attention to detail required to transform rough castings into polished artifacts, showcasing the caster's skill and dedication to quality craftsmanship.
Advanced Techniques and Tips
In the realm of metal casting, 'Advanced Techniques and Tips' play a pivotal role in pushing the boundaries of what can be achieved. As beginners progress in their metal casting journey, mastering these advanced techniques becomes paramount for honing their craft. These techniques not only allow for the creation of more intricate and complex metal castings but also enable casters to experiment with different methods and materials. Embracing advanced techniques opens up a world of possibilities, fostering creativity and innovation in metal casting.
Exploring Different Casting Methods
Sand Casting
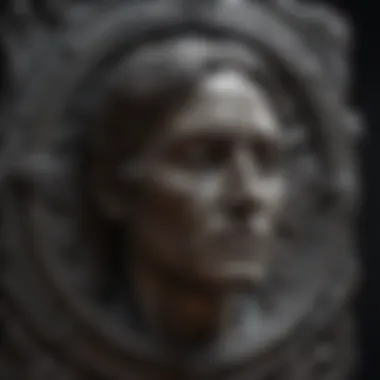
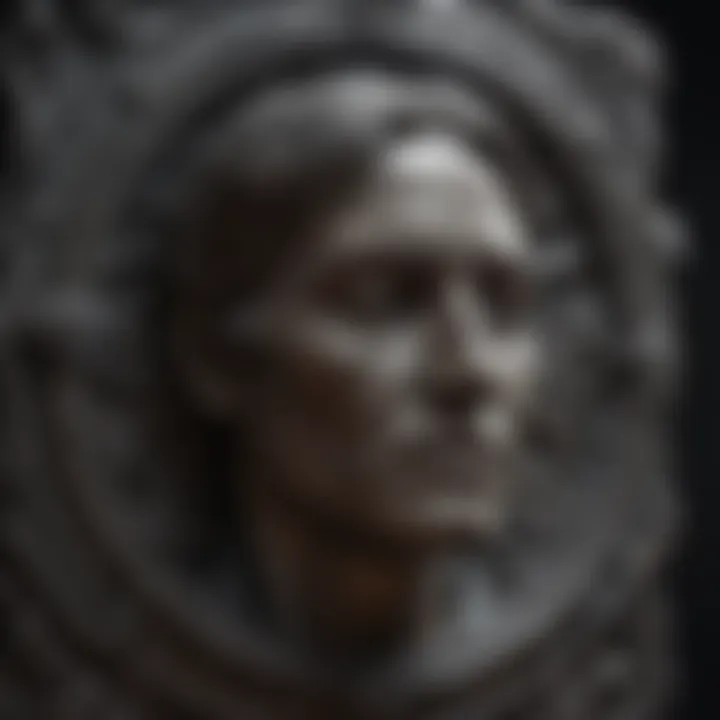
Sand casting stands as one of the oldest and most versatile casting methods available, offering a cost-effective and straightforward approach to metal casting. It involves creating a mold using compacted sand around a pattern, which is then removed to leave a cavity for pouring molten metal. Sand casting is known for its flexibility in accommodating various shapes and sizes, making it a preferred choice for many beginners due to its accessibility and adaptability.
Investment Casting
Investment casting, also known as lost-wax casting, is a precise method that yields high accuracy and intricate detailing in metal castings. This process involves creating a wax pattern that is coated in ceramic slurry, burned out to leave a mold cavity, and then filled with molten metal. Investment casting is renowned for its ability to produce complex shapes with fine details, making it ideal for crafting jewelry, artistic pieces, and aerospace components.
Die Casting
Die casting is a robust and efficient casting method that utilizes a metal die to produce uniform and high-quality metal parts. This process involves injecting molten metal into a steel die under high pressure, allowing for the quick production of parts with tight tolerances. Die casting is commonly used in manufacturing industries for mass production of components in automotive, electronics, and appliances due to its repeatability and high productivity.
Troubleshooting Common Issues
Porosity, Shrinkage, and Metal Inclusions
Porosity, shrinkage, and metal inclusions are common defects that can arise during the metal casting process. Porosity refers to voids or gas pockets within the casting, shrinkage results in dimensional inaccuracies or cracks, and metal inclusions are foreign particles embedded in the metal. By understanding and addressing these issues, casters can improve the quality of their castings and ensure that each piece meets the required standards. Proper workpiece design, melting practices, and mold preparation are crucial in minimizing these common defects and achieving high-quality castings.
Conclusion and Further Resources
In the journey through the intricate world of metal casting, the conclusion and further resources section plays a pivotal role in consolidating the knowledge and offering avenues for continuous learning and skill enhancement. This final segment serves as a compass, guiding beginners towards honing their craft and exploring new horizons within the realm of metal casting. It encapsulates the essence of the guide by emphasizing the importance of practice, patience, and a thirst for continuous learning.
By highlighting key takeaways for beginner casters, this section empowers enthusiasts to embrace the challenges and rewards associated with mastering metal casting. It underlines the significance of perseverance and dedication in cultivating expertise in this intricate art form. Moreover, it encourages beginners to seek further resources to expand their knowledge base and practical skills in metal casting.
Key Takeaways for Beginner Casters
Practice, Patience, and Continuous Learning
In the realm of metal casting, the trio of practice, patience, and continuous learning emerges as the cornerstone of success for aspiring casters. Practice entails dedicating time and effort to honing one's skills, experimenting with different techniques, and refining casting methods through hands-on experience. Patience plays a crucial role in mastering this craft, as success in metal casting often requires meticulous attention to detail and perseverance through setbacks. Continuous learning, on the other hand, involves consistently seeking new knowledge, staying updated on industry trends, and engaging in skill development opportunities.
The integration of practice, patience, and continuous learning fosters a growth mindset among beginner casters, encouraging them to embrace challenges and persist in their quest for mastery. These elements not only enhance technical proficiency but also instill a sense of resilience and adaptability crucial for navigating the multifaceted world of metal casting. By prioritizing these aspects, novice casters can unlock their creative potential, refine their craftsmanship, and lay a strong foundation for future endeavors in the field.
Exploring Advanced Courses and Workshops
Opportunities for skill enhancement through advanced courses and workshops offer a transformative pathway for beginner casters eager to elevate their craft. These immersive learning experiences provide a platform for enthusiasts to delve deeper into specialized aspects of metal casting, engage with industry professionals, and broaden their horizons within the field. By delving into advanced courses and workshops, novice casters can gain insights into innovative techniques, advanced materials, and cutting-edge technologies shaping the future of metal casting.
The key characteristic of advanced courses and workshops lies in their ability to bridge the gap between theoretical knowledge and practical application, offering hands-on training and mentorship from seasoned experts. This experiential learning environment not only enhances technical skills but also fosters a collaborative community of passionate individuals dedicated to pushing the boundaries of metal casting. While advanced courses provide a structured curriculum for skill development, workshops offer a creative space for experimentation and discovery, encouraging participants to explore unconventional approaches and push the limits of their creativity.
Embracing opportunities for skill enhancement through advanced courses and workshops equips beginner casters with the tools, techniques, and inspiration needed to excel in the dynamic world of metal casting. By seizing these opportunities, enthusiasts can fast-track their learning journey, expand their network, and embark on a fulfilling career path driven by innovation and artistic expression.