Unveiling the In-Depth Lowes Sandblaster: A Comprehensive Exploration
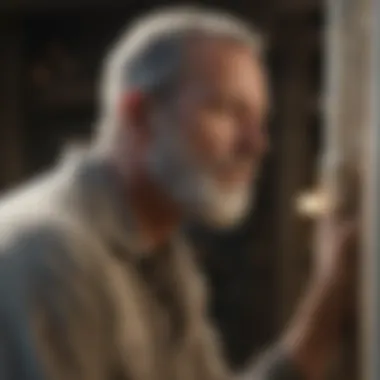
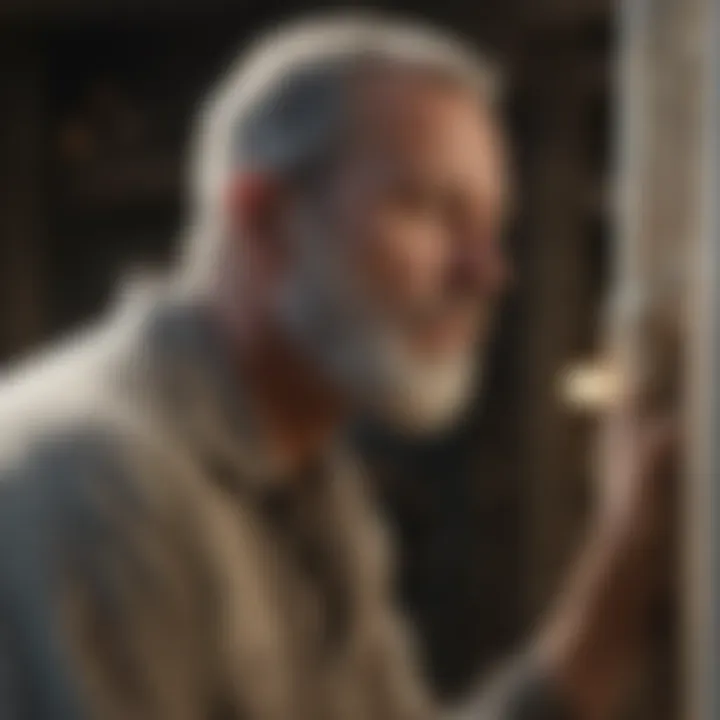
Rock and Fossil Identification
When diving into the world of sandblasting with the Lowes sandblaster, understanding the types of rocks and fossils you may encounter is crucial. From sedimentary to igneous rocks, each possesses unique characteristics. Sedimentary rocks like sandstone often have visible layers or grains, while volcanic igneous rocks such as basalt can be identified by their fine-grained texture. Fossils, remnants of ancient life forms preserved in rock, can vary from imprints to petrified remains. Differentiating between these types is essential for effective sandblasting.
To enhance your sandblasting experience with the Lowes sandblaster, recognizing the key characteristics of rocks and fossils is paramount. Rocks may exhibit hardness, color, and grain size, aiding in their identification. Furthermore, fossils can display specific shapes, patterns, and textures. Considering these attributes will not only facilitate efficient sandblasting but also contribute to a deeper appreciation of geological history.
Utilizing the right tools for rock and fossil identification is imperative when working with the Lowes sandblaster. Tools such as magnifying glasses, hardness picks, and scales allow for detailed examination of specimen features. Moreover, specialized kits containing geological hammers, chisels, and brushes enable precise extraction and handling. Incorporating these tools into your sandblasting equipment ensures accurate identification and meticulous preservation of rocks and fossils.
Introduction to Sandblasting
Sandblasting is a crucial process in various industries, essential for tasks like cleaning, surface preparation, and restoration. In this article, we will delve into the fundamental concepts and techniques of sandblasting, focusing specifically on how the Lowes sandblaster revolutionizes this practice. By understanding the basics of sandblasting, enthusiasts and professionals can maximize the efficiency and effectiveness of their projects. From selecting the right abrasive to mastering the sandblasting equipment, a solid foundation in sandblasting techniques sets the stage for successful applications.
Understanding Sandblasting Techniques
Pressure Blasting
Pressure blasting is a key technique in sandblasting that involves propelling abrasive materials at high pressure onto a surface to achieve various outcomes. The use of compressed air or water pressure accelerates the abrasive particles, resulting in efficient paint removal, surface texturing, and rust or coatings elimination. The precision and power offered by pressure blasting make it a popular choice for tasks requiring intense cleaning or detailed work. However, its high pressure necessitates careful handling to prevent surface damage and ensure safety.
Suction Blasting
Suction blasting differs from pressure blasting by using suction to propel abrasives onto a surface instead of relying solely on high pressure. This method is versatile, offering increased control and precision, making it ideal for intricate jobs with different surface profiles. Suction blasting provides excellent visibility during operation, enhancing accuracy and reducing material wastage. While it may not offer the same power as pressure blasting, its controlled application makes it a favored option for projects requiring finesse and attention to detail.
Wet Blasting
Wet blasting introduces the element of water into the abrasive stream, resulting in a gentler and more precise cleaning action. By combining water with abrasives, wet blasting minimizes dust emissions, ensuring a healthier work environment. The dampened abrasive also reduces the risk of substrate damage while providing effective surface cleaning, particularly for delicate materials or intricate surfaces. The controlled nature of wet blasting makes it a suitable choice for projects where precision and material preservation are paramount.
Applications of Sandblasting
Surface Preparation
Surface preparation involves the initial step of cleaning and abrading a surface before painting, coating, or bonding. It is a critical process to ensure adhesion and longevity of the finishing material. By removing contaminants, rust, old coatings, or irregularities, surface preparation creates a clean, rough surface for optimal material adhesion. The Lowes sandblaster offers specific features that enhance the precision and effectiveness of surface preparation, making it a valuable tool for various projects.
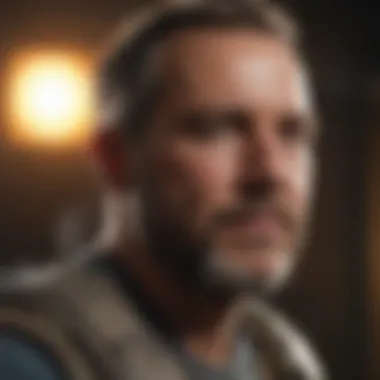
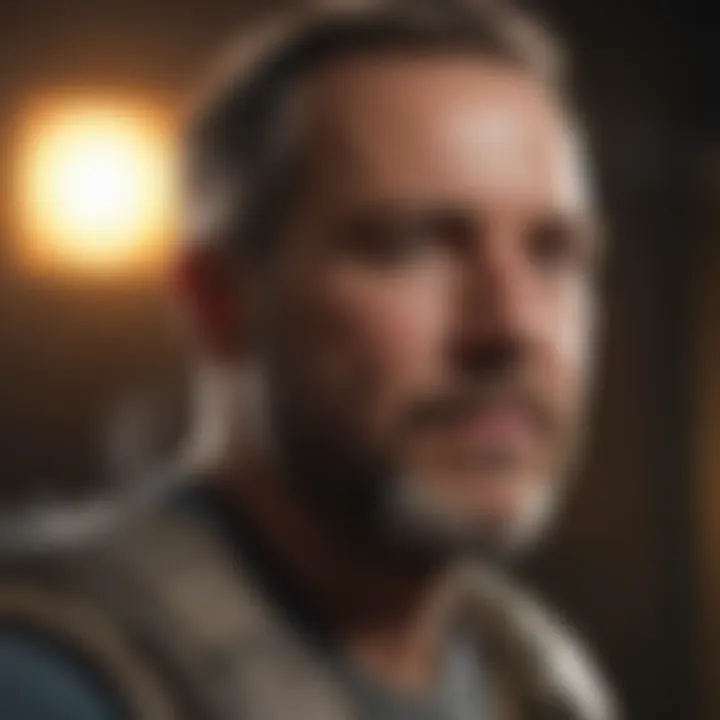
Rust Removal
Rust removal is a common application of sandblasting, aimed at eliminating corrosion from metal surfaces. By using abrasive materials propelled at high velocity, rust particles are dislodged, revealing a clean metal surface ready for further treatment. The Lowes sandblaster's ability to tackle rust efficiently and effectively makes it a reliable choice for restoration projects and maintenance tasks. Its versatility in rust removal applications ensures professional results with minimal effort.
Paint Stripping
Paint stripping involves removing old paint layers from surfaces to prepare them for refinishing or repainting. Sandblasting is a preferred method for paint removal due to its speed and effectiveness in stripping multiple layers of paint in a single application. The Lowes sandblaster's nozzle types, pressure settings, and tank capacity play a vital role in enhancing paint stripping efficiency and ensuring uniform coverage. With the right settings and techniques, the Lowes sandblaster simplifies the paint stripping process, saving time and effort for users.
Introduction to Lowes Sandblaster
In the realm of sandblasting equipment, the Lowes sandblaster holds particular significance due to its superior features and functionality. As a pivotal part of this comprehensive guide, the Introduction to Lowes Sandblaster section aims to shed light on the essential aspects that make this equipment a standout choice for both professionals and hobbyists. By delving into the specifics of the Lowes brand, readers will gain a deep understanding of the technology behind this sandblaster and the advantages it offers in various applications.
Features of Lowes Sandblaster
Tank Capacity
The tank capacity of the Lowes Sandblaster plays a crucial role in its performance and efficiency. With a generous tank size, users can minimize downtime for refills and maximize productivity during sandblasting projects. The ample capacity allows for extended use without frequent interruptions, making it a preferred choice for those requiring continuous operation. Additionally, the tank design ensures easy refilling and maintenance, enhancing user experience and workflow.
Nozzle Types
When it comes to nozzle types, the Lowes Sandblaster offers a range of options to suit different applications and materials. Whether precision blasting or broad coverage is needed, the nozzle types provided cater to diverse user requirements. Each type is carefully crafted to deliver optimal sandblasting results, ensuring consistent performance and desired outcomes with every use. The versatility in choosing various nozzle types adds a layer of customization and precision to the sandblasting process.
Pressure Settings
The pressure settings of the Lowes Sandblaster are finely tuned to provide the ideal balance of power and control. Users can adjust the pressure settings according to the specific project requirements, allowing for flexibility and precision in sandblasting applications. Whether gentle paint removal or tough surface preparation is needed, the adjustable pressure settings enable users to achieve desired results with ease. This feature enhances the overall user experience and ensures efficient sandblasting operations.
Benefits of Choosing Lowes Sandblaster
Durability
One of the standout benefits of the Lowes Sandblaster is its exceptional durability. Constructed with high-quality materials and robust components, this equipment is built to withstand the rigors of sandblasting projects, ensuring long-term performance and reliability. The durable design minimizes maintenance needs and enhances the longevity of the sandblaster, making it a cost-effective investment for users seeking a reliable and sturdy tool.
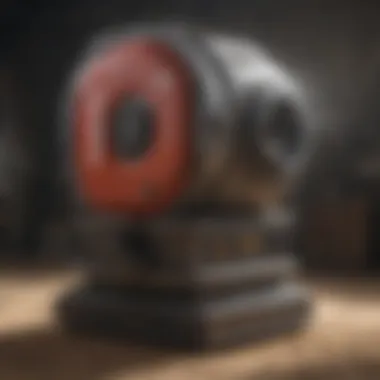
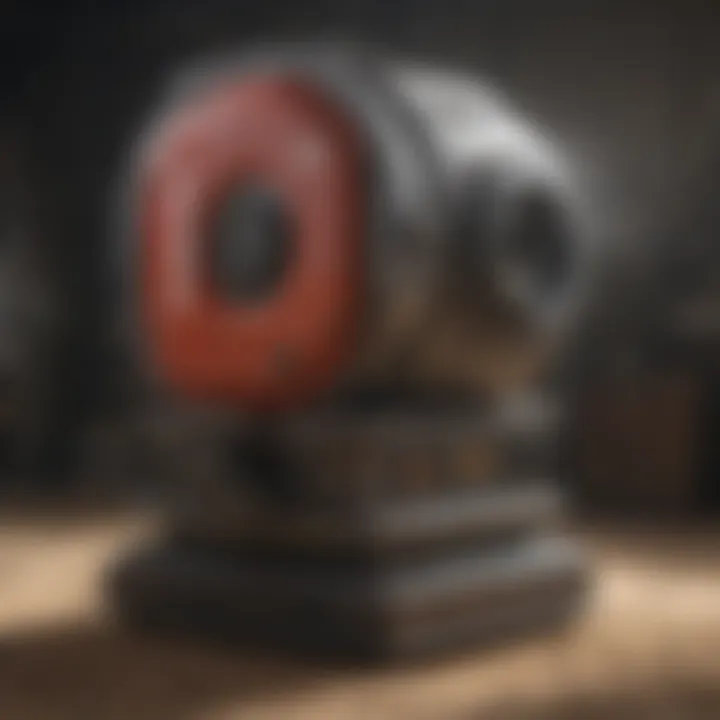
Efficiency
Efficiency is a key attribute of the Lowes Sandblaster, allowing users to accomplish sandblasting tasks with optimal speed and effectiveness. The efficient design of the equipment streamlines the blasting process, reducing wasted time and effort while maximizing productivity. Whether tackling large-scale projects or intricate detailing work, the efficiency of the Lowes Sandblaster facilitates smooth and precise sandblasting operations, leading to quality results in less time.
Versatility
The versatility of the Lowes Sandblaster sets it apart as a versatile tool for various sandblasting applications. With its adaptability to different materials and surfaces, users have the freedom to explore a wide range of projects with ease. From delicate surface treatments to heavy-duty cleaning tasks, the versatility of the Lowes Sandblaster empowers users to achieve professional-grade results across diverse applications. This flexibility enhances the overall utility and value of the equipment, making it a preferred choice for those seeking versatility in their sandblasting endeavors.
Using the Lowes Sandblaster Effectively
In the realm of sandblasting, employing the Lowes Sandblaster effectively holds paramount importance for achieving optimal results and prolonging equipment lifespan. Understanding the nuances of using this equipment not only enhances productivity but also ensures safety and precision in abrasive blasting tasks. This section will delve into specific elements, benefits, and considerations regarding the effective utilization of the Lowes Sandblaster.
Preparation and Safety Measures
Safety Gear
Safety gear is a critical component in the sandblasting process, safeguarding operators against potential hazards such as abrasive rebound and airborne particles. Proper safety gear, including protective eyewear, gloves, and respiratory masks, plays a pivotal role in minimizing injuries and maintaining operator well-being. The durability and ergonomic design of safety gear make it a popular choice for professionals engaging in sandblasting activities. Additionally, the unique feature of adjustable straps and comfortable padding ensures prolonged wear without compromising protection levels.
Work Area Preparation
Effective work area preparation sets the foundation for a smooth and efficient sandblasting operation. Clearing the workspace of debris, ensuring proper ventilation, and implementing containment measures contribute to a safe and organized environment. By delineating designated blasting zones and utilizing shielding for adjacent surfaces, work area preparation mitigates the risk of collateral damage and optimizes workflow. The versatility and ease of setup associated with work area preparation make it a valuable asset in achieving consistent results while reducing cleanup efforts.
Material Handling
Efficient material handling streamlines the abrasive blasting process, enhancing productivity and minimizing downtime. Proper handling techniques, such as utilizing lift assist devices and organizing abrasive materials, contribute to a seamless operation. The key characteristic of material handling lies in its ability to facilitate quick and precise replenishment of abrasives, ensuring uninterrupted workflow. While manual material handling provides flexibility in smaller-scale projects, automated systems offer increased efficiency and consistency in abrasive distribution.
Techniques for Optimal Results
Distance and Angle
Optimal distance and angle play a pivotal role in controlling the intensity and coverage of abrasive blasting. Maintaining the appropriate distance between the nozzle tip and the work surface ensures uniform material removal without causing surface damage. The key characteristic of optimizing distance and angle lies in striking a balance between aggressiveness and precision, enhancing the efficacy of the sandblasting process. By adjusting the nozzle angle according to the surface curvature and material hardness, operators can achieve desired results with minimal material wastage.
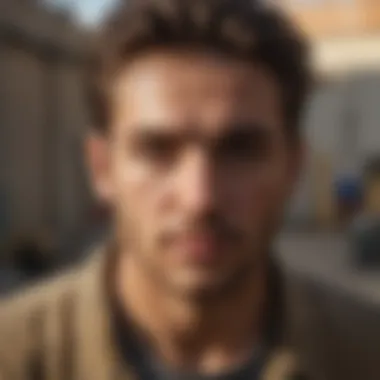
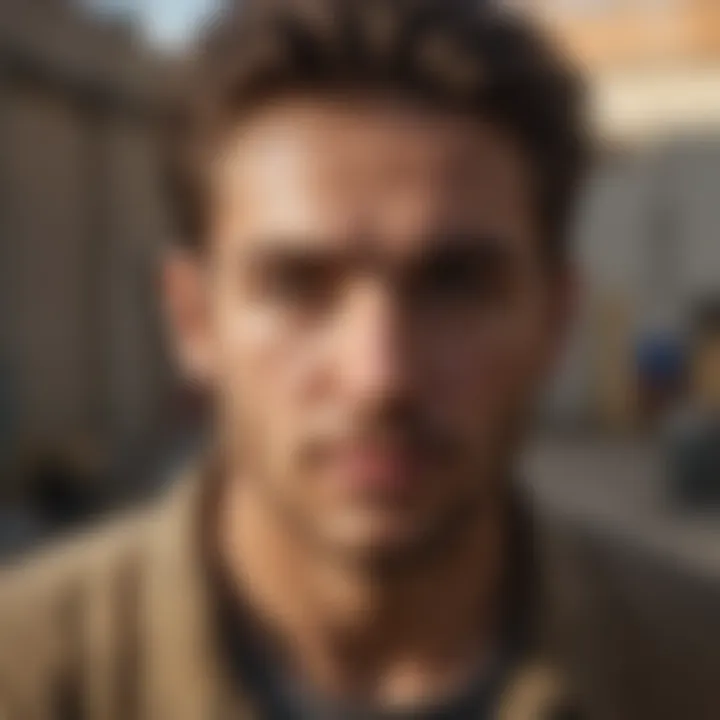
Speed of Movement
The speed of movement dictates the efficiency and quality of abrasive blasting, influencing material removal rates and surface finish. Consistent and controlled movement speed enables uniform coverage and prevents over-blasting or uneven results. The key characteristic of ideal movement speed lies in adapting to the material being processed and adjusting based on desired surface texture. By calibrating movement speed to match abrasive flow rates and nozzle settings, operators can optimize material removal while minimizing operational errors.
Overlapping Patterns
Overlapping patterns are essential in ensuring complete surface coverage and preventing missed spots during abrasive blasting. By overlapping each pass slightly, operators guarantee uniformity in material removal and avoid leaving behind residue or inconsistencies. The unique feature of overlapping patterns lies in its ability to create a cohesive finish and maintain surface integrity throughout the sandblasting process. While mastering overlapping techniques may require practice and precision, incorporating this method enhances overall efficiency and results in a professional-grade finish.
Maintenance and Care for Lowes Sandblaster
In this comprehensive guide to Exploring the Lowes Sandblaster, it is crucial to emphasize the significance of proper maintenance and care to ensure the longevity and optimal performance of this essential tool. Maintenance and care for the Lowes Sandblaster not only prolong its lifespan but also guarantee a safe and efficient sandblasting process.
Cleaning and Storage
Flushing the System
Flushing the system of the Lowes Sandblaster is a critical step in its maintenance routine. By flushing the system, any residual abrasives or contaminants are removed, preventing clogs and maintaining the equipment's functionality. This process ensures that the sandblaster operates smoothly during each use, enhancing performance levels and prolonging its lifespan.
Removing Residual Abrasives
The process of removing residual abrasives from the Lowes Sandblaster is essential to prevent abrasive buildup, which can compromise the equipment's efficiency. By thoroughly eliminating any remaining abrasives, users can maintain the sandblaster's integrity and prevent potential blockages or damage. This step contributes significantly to the overall maintenance and care procedures that aid in preserving the sandblaster's quality and performance.
Storage Recommendations
Proper storage of the Lowes Sandblaster is vital to safeguard its components and ensure its readiness for future use. Following appropriate storage recommendations, such as keeping the equipment in a dry and secure location, prevents potential damage from moisture or external elements. Additionally, storing the sandblaster in a designated area away from contaminants or extreme temperatures prolongs its lifespan and maintains its functionality over time. Adhering to recommended storage practices guarantees that the sandblaster remains in optimal condition and ready for efficient operation whenever needed.
Regular Inspections and Troubleshooting
Check for Leakage
Regularly checking for leaks in the Lowes Sandblaster is a fundamental aspect of its maintenance. Detecting and addressing leaks promptly prevents material wastage and ensures the equipment operates at its best. This proactive measure not only sustains the sandblaster's efficiency but also aids in maintaining a safe working environment for the user.
Inspect Nozzle Wear
Inspecting the nozzle wear of the Lowes Sandblaster is essential for identifying potential issues that may impact its performance. By monitoring and evaluating the condition of the nozzle regularly, users can replace worn-out parts promptly, thereby optimizing the sandblaster's efficiency and precision during operation. This meticulous inspection process contributes to the overall maintenance and care routine, enhancing the equipment's longevity and overall functionality.
Common Issues and Solutions
Exploring common issues and their solutions with the Lowes Sandblaster is paramount to troubleshoot any operational challenges effectively. By understanding prevalent issues, such as blockages or pressure inconsistencies, users can implement targeted solutions to resolve these problems efficiently. Identifying and addressing common issues promptly allows for uninterrupted sandblasting sessions and maintains the equipment's reliability and performance.