Essential Lapidary Tools: Saws and Polishers Explained
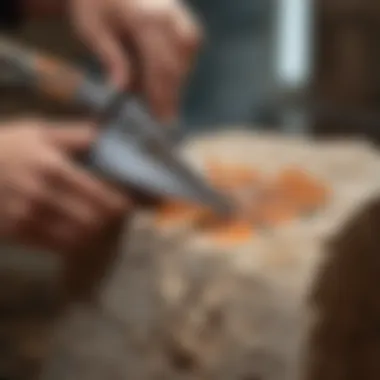
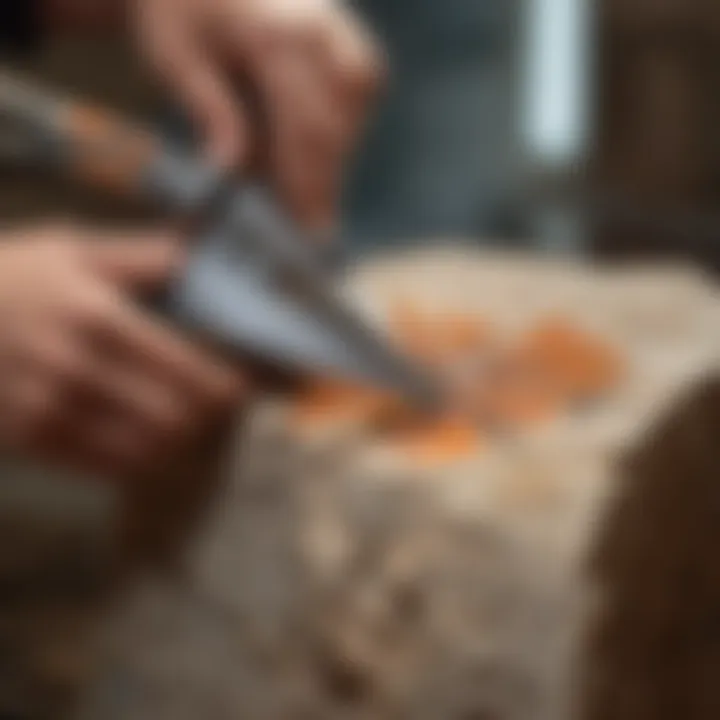
Intro
In the fascinating realm of lapidary arts, the choice of tools can often be the difference between a gem simply being a chunk of rock and it becoming a polished masterpiece. This article primarily zeroes in on two indispensable tools that every lapidary aficionado should have in their toolkit: the saw and the polisher. While these tools may seem straightforward at first glance, a deeper dive reveals an intricate landscape of types, functionalities, and tips that elevate their importance. Whether you're a novice stepping into the enchanting world of lapidary work or a seasoned pro honing your craft, understanding these tools is paramount.
Rock and Fossil Identification
Identifying the right rocks and fossils is one of the initial steps any aspiring lapidary artist or fossil collector must master. This process not only helps in selecting materials worth working with but also sparks the joy of discovery.
Types of Rocks and Fossils
There are three main types of rocks: igneous, sedimentary, and metamorphic. Each type has unique characteristics and formations.
- Igneous Rocks: Formed from cooled magma or lava, examples include granite and basalt.
- Sedimentary Rocks: Comprised of particles, plants, and animals. Think limestone and sandstone.
- Metamorphic Rocks: These began as either igneous or sedimentary but transformed under extreme heat and pressure. Examples include marble and schist.
When it comes to fossils, they fall largely into two categories: body fossils and trace fossils. Body fossils are the remains of the organism, such as bones or shells, while trace fossils, like footprints or burrows, inform us about the behaviors of ancient life.
Characteristics to Look For
When identifying a specimen, it's crucial to observe several key characteristics.
- Color and Luster: These can hint at the mineral composition.
- Texture and Grain: Some rocks have rough surfaces while others are smooth.
- Fossilization Process: In fossils, consider preservation quality and any unique markings that might point to its age and origin.
Tools for Identification
To accurately identify rocks and fossils, several handy tools can come in play:
- Hand Lens: Enhances your ability to see details, proving invaluable for examining mineral structures.
- Field Guide: A printed guide or app that provides information on local geology and fossil species.
- Rock Hammer: Handy for breaking apart specimens, but it's critically important to use it responsibly.
Collecting Tips and Techniques
Gathering rocks and fossils can be as thrilling as it is challenging. Proper techniques can ensure not only personal safety but also the preservation of your finds, allowing them to shine in your collection.
Best Practices for Collecting
- Research First: Know your local laws for collecting; certain areas may be off-limits for various reasons.
- Stay Respectful of Nature: Collect responsibly and sustainably.
- Don’t Overcollect: Leave some specimens behind for future collectors to enjoy.
Locating Prime Collecting Sites
Some spots become legendary among collectors due to their bounty. Look for:
- Riverbeds and Streams: Water movement can often reveal hidden treasures.
- Cliffs and Outcrops: These natural formations can expose layers of geological history.
- Nearby Mines: Often, they allow novice collectors to learn amidst expert excavations.
How to Safely Extract Specimens
- Use Proper Gear: Sturdy boots, gloves, and goggles can prevent injuries.
- Gentle Techniques: Avoid using excessive force that might damage both the surrounding environment and the specimen itself.
Preservation and Display
Once you've collected your specimens, taking the right steps for preservation and display is essential. Proper care will ensure that your treasures withstand the test of time.
Techniques for Preserving Rocks and Fossils
For rocks, using a mild soap and water solution can help in cleaning without damaging their surface. Fossils, on the other hand, may require specialized methods depending on their composition.
- Conservation Sealants: Applying a sealant can protect delicate fossils from humidity and dust.
- Controlled Environments: Store your collection in a consistent environment away from sunlight that can fade colors.
Proper Storage Methods
Choose storage that fits your collection’s needs:
- Acid-Free Boxes: Ideal for long-term storage of delicate specimens.
- Display Cabinets: Consider showcasing your finds, allowing them to be admired while keeping them safe.
Creative Display Ideas
Think outside traditional methods; consider:
- Shadow Boxes: Adding a unique flair to your display with different backgrounds.
- Digital Screens: Presenting a rotating display of your collection can be quite modern.
Epilogue
In the pursuit of lapidary art, the marriage of tools—like saws and polishers—with skills—like rock and fossil identification—poised to create breathtaking pieces. Remember, as with any craft, patience and practice will lead to mastery. Not merely a hobby, this is a journey into the heart of Earth’s history.
Preamble to Lapidary Arts
Lapidary arts hold a cherished position in the world of craftsmanship, transforming raw stones into exquisite pieces of art. This discipline not only emphasizes the aesthetic appeal of stones but also delves deep into their geological significance. Understanding lapidary arts sets the stage for both new and seasoned enthusiasts as it lays the foundational knowledge necessary for effectively utilizing tools such as saws and polishers.
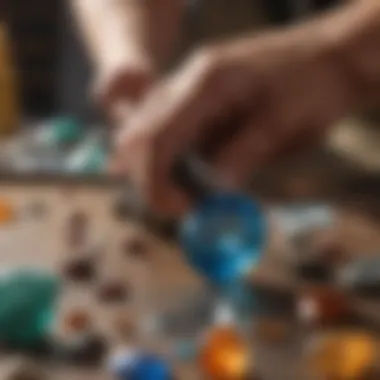
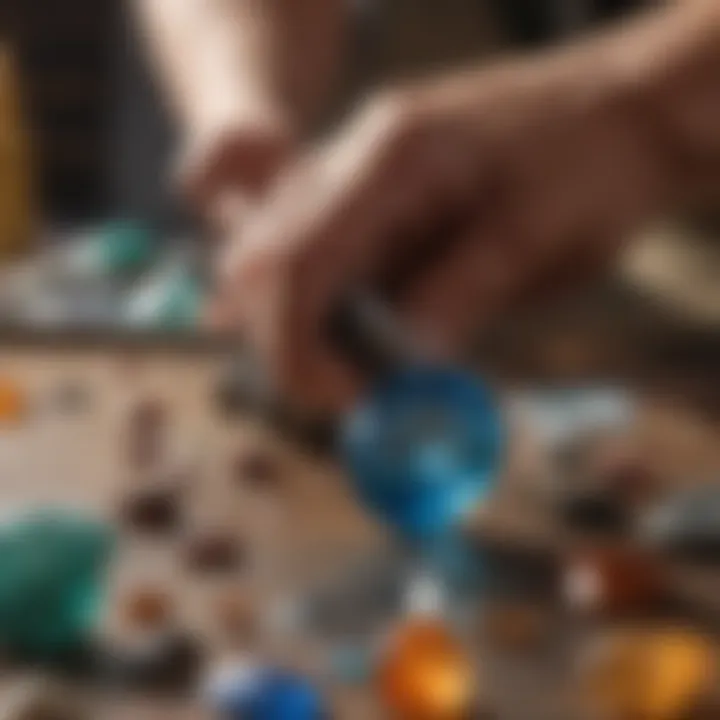
With every cut and polish, lapidary work reveals the hidden beauty within rough geology. Enthusiasts engage in this age-old craft for various reasons. Some are driven by the joy of creation, while others are motivated by the desire to work with nature’s artistic palette. The knowledge of lapidary arts also serves practical purposes – helping collectors to preserve and showcase their finds in a manner that highlights their natural beauty.
Specialists argue that engaging with lapidary arts is not merely a hobby; it's a connection to the earth’s history and the stories that each stone can tell. Each gemstone or rock specimen has its own unique tale formed over millennia. By exploring these arts, we cultivate an appreciation for the environment, geology, and our role as curators of natural beauty.
"Every gem you discover is like holding a piece of history—there’s a narrative in every swirl and the sparkle of the stone."
The journey into lapidary tools, particularly the saws and polishers, reflects the importance of technique alongside creativity. Learning to handle these instruments not only learns practical skills but fosters a deeper connection to the materials being worked with. Thus, our exploration of lapidary tools is not just technical; it’s profoundly powered by an appreciation of the age-old capabilities of humankind to shape and give new lives to the stones we cherish.
Through this article, we will uncover how these tools function, their various types, and the critical role they play in the artistic transformation of stones into polished gems, ensuring that every facet is appreciated from its origins to its best sheen.
Understanding Lapidary Saws
Lapidary saws hold a central role in the lapidary arts. Without these tools, the cutting and shaping of stones would be a frustrating endeavor at best. By understanding lapidary saws, one can enhance their craftsmanship while working with gemstones. These saws not only bring a greater precision to stonework but also provide a deeper appreciation of the materials at hand.
In this section, we will break down the different types of saws available, explore how they function mechanically, and discuss important factors to consider when selecting the right saw for your gemstone projects.
Types of Lapidary Saws
Trim Saws
Trim saws are among the most commonly used lapidary saws, primarily designed for small, precise cuts. Their hallmark is a smaller blade that enables the user to trim or shape stones without wasting material. The trim saw typically features a narrow blade, allowing for tight cuts around intricate details.
These saws shine when it comes to preparing rough stones into manageable pieces, ensuring that every slice counts. A key attraction of trim saws is their ease of use. They are particularly popular among hobbyists as their lightweight design and simple mechanisms reduce the learning curve.
However, their small blade can limit their versatility, as they may not be suited for larger stones or extensive shaping. It's essential to balance their benefits against the potential restrictions when considering a trim saw for your lapidary work.
Slab Saws
Slab saws are a step up when larger, thicker stones need cutting. These saws are built for heavy-duty work, capable of slicing through substantial slabs with greater efficiency. The key feature of slab saws is their larger blade, which allows for wider cuts and deeper passes.
These saws are instrumental for those who aim to create larger pieces or for those engaged in volume work, where cutting multiple slabs is necessary. Thanks to their robust construction, slab saws can handle tougher stones, making them a valuable addition in any lapidary workshop.
However, due to their size and power requirements, they might not be the best fit for beginners, but for experienced lapidaries, they provide the capability to tackle more ambitious projects.
Cabbing Saws
Cabbing saws are specialized to produce cabochons, which are stones shaped and polished into a dome-like form. With a focus on creating smooth, rounded edges, cabbing saws often utilize a wider, softer blade designed for the gentler touch needed for cabochon work.
The unique aspect of cabbing saws lies in their ability to be tweaked for precision, allowing users to create intricate designs while working with softer materials. They are particularly beneficial for those focused on cabbing niche stones, as they help to shape stones with a finesse that brings out their inherent beauty.
However, these saws may not handle larger or harder stones as effectively, which poses a challenge for those looking to expand their repertoire.
Mechanics of Lapidary Saws
Understanding the mechanics of lapidary saws enhances the efficacy of these tools.
Blade Composition
The blade composition of a saw can make or break its performance. Many lapidary saws utilize diamond blades due to their extreme hardness, which ensures clean, precise cuts. The advantage of diamond blades is their ability to stay sharper for longer compared to traditional steel blades.
However, such blades can come at a premium price, and thus, users must consider the investment against the expected output. Alternatively, abrasive blades, often made from silicon carbide or aluminum oxide, are cost-effective but may not deliver the same longevity or precision.
Understanding these materials and their applications is key for maximizing the performance of lapidary saws.
Motor Specifications
The motor specifications of a saw determine its cutting power and speed. A higher wattage generally means more power, capable of sustaining performance during tough cuts. Most lapidary saws vary between 0.5 HP and 1.5 HP. The choice of motor can significantly affect cutting time, especially when dealing with larger stones.
Moreover, variable speed controls become a critical feature for those attempting precision cuts or dealing with fragile materials. Users should take care to match the motor specifications with their intended cutting tasks to optimize results.
Choosing the Right Saw
When it comes to choosing the right lapidary saw, several factors must be weighed.
Factors to Consider
Several considerations play into the decision-making process. For example, assess the types of stones you'll typically be cutting and the complexity of the shapes you aim to achieve. Each saw type serves a specific purpose, and accordingly, choosing a trim saw, slab saw, or cabbing saw depends on your unique projects.
Additionally, space and power availability come into play—large slab saws require significant workspace and often specialized power sources. Balancing your space with the right machinery can prevent future headaches.
Common Mistakes
A major pitfall when choosing a lapidary saw is underestimating blade longevity and quality. Many novices opt for cheaper blades, only to find themselves replacing them sooner than anticipated. Additionally, not considering the scale of projects can lead to ill-fitting tools that hinder progress.
Understanding the need for long-term investment in quality equipment is crucial for avoiding frustration and wasted resources.
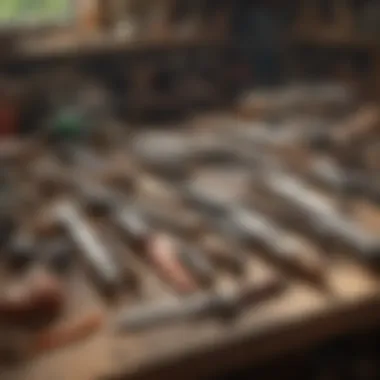
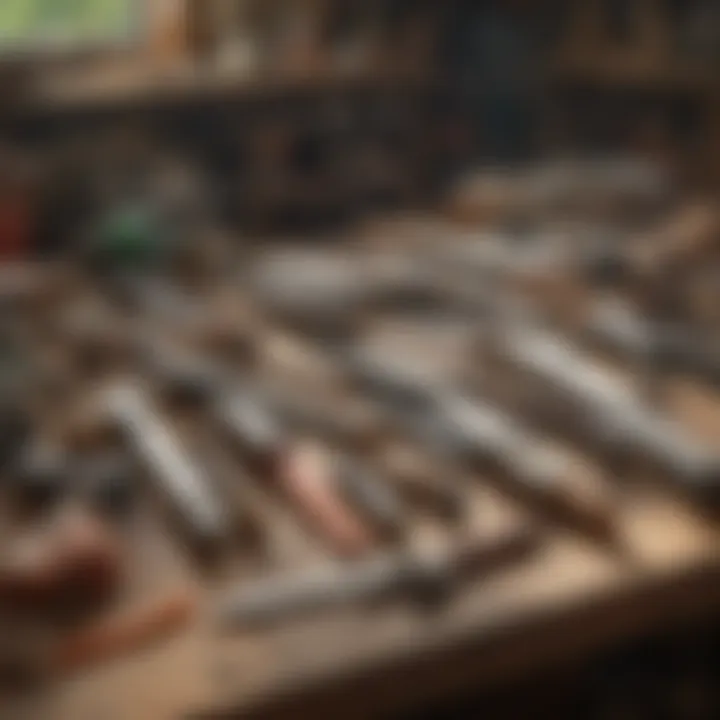
In summary, lapidary saws are not just tools; they are gateways to the art you wish to create. Picking the right saw for your needs sets the foundation for your crafting journey.
Lapidary Saw Operation Techniques
When it comes to working with lapidary tools like saws, understanding the operation techniques is a cornerstone for achieving high-quality results. Proper techniques not only ensure the precision of your cuts but also significantly enhance your safety and efficiency. In the lapidary art, the ability to manipulate the tools effectively can turn rough stones into sparkling gems, giving you satisfaction and boosting your artistic flair.
Setting Up the Workspace
Right off the bat, a well-organized workspace is the first step toward success in lapidary work. Begin by selecting a sturdy, stable table with enough space to accommodate your saw and workspace items. Ensure that your tools are within arm's reach to minimize unnecessary movement. Lighting is another crucial factor; a bright work area reduces eye strain and improves accuracy when cutting.
Keep in mind that a clean environment minimizes hazards. Dust and debris can become flying projectiles during cutting, so using a vacuum or designated collection system is ideal. Having a clear layout and a clutter-free area also helps focus your mind on the task at hand, allowing for a more zen-like approach.
Cutting Techniques
Cutting techniques can vary widely depending on the kind of stone and the saw you are using. However, there are a few universal approaches that can be applied. For instance, a gentle, deliberate pace tends to yield better results. Rushing through a cut or applying excessive pressure can lead to uneven lines, or worse, damage to both the stone and the saw blade.
- Start with Sensitivity: It’s wise to begin cutting with light pressure. Allow the saw blade to do most of the work. This alleviates unnecessary stress on the blade, which is key in prolonging its lifespan.
- Follow the Grain: Pay attention to the natural lines and patterns on the stone. Align your cuts accordingly—this technique often showcases the stone's natural beauty and helps prevent chips.
- Angle Matters: Maintain a consistent angle while cutting to avoid jagged edges. For instance, if you’re slab sawing, a slight tilt might help in achieving a smoother surface finish.
Safety Measures
Safety is paramount in lapidary work. Mismanagement or oversight can lead to unfortunate accidents, so adhering to safety measures is non-negotiable.
Protective Gear
Wearing protective gear is akin to donning armor. Safety goggles are essential. Not only do they shield against debris, but they also protect against splashes from unexpected reactions during cuts. Gloves are highly beneficial as well; they give you a better grip and keep your hands safe from sharp edges.
One characteristic of good protective gear is durability. Equipment that endures wear and tear ensures reliable protection, making it a popular choice among lapidary enthusiasts. On the flip side, uncomfortable gear can be a nuisance, possibly leading to careless errors during operation. Thus, finding the right balance of comfort and protection is essential.
Handling Precautions
Handling precautions revolve around the appropriate behavior while operating lapidary tools. They play a significant role in ensuring not just your safety but the integrity of the stones you work on. Be cautious while adjusting settings or replacing blades; ensure the tool is switched off. In addition,
- Stay Focused: Always keep your focus on the task to avoid unintended distractions. It sounds simple, but a moment's lapse can have severe consequences.
- Use Proper Tools for Adjustments: Avoid using makeshift tools or hands to stabilize materials while cutting. Instead, use clamps or vises that are specifically designed for securing stones.
To synthesize the aforementioned points, mastering the art of lapidary saw operation techniques is not merely a mechanical skill; it's about blending technique, safety, and an appreciation for the material you work with. Cutting stones is not just work; it's a journey, and each stage from setup to cutting and safety enhances your effectiveness.
Lapidary Polishers: An Overview
Lapidary polishers play a crucial role in the transformation of rough stones into polished gemstones. They offer not only aesthetics but also provide a level of refinement that can enhance the natural beauty of various materials. Understanding the different types of polishers, their functionalities, and the techniques involved in their use is essential for anyone engaged in lapidary work. Whether you are a hobbyist or a professional collector, knowledge of polishers and their operations can significantly elevate your craft.
Types of Polishers
Rotary Polishers
Rotary polishers are a common choice among lapidary enthusiasts due to their ability to produce a high-gloss finish on stones. One of the main things that set rotary polishers apart is their motorized spinning motion, which applies polishing compounds uniformly across the stone's surface. This characteristic makes them not only efficient but also reliable for achieving consistent results.
A notable advantage of rotary polishers is their versatility. They can accommodate various polishing wheels and pads, allowing for adjustments according to the type of stone being polished. However, they require a steady hand and proper technique. Improper use can lead to uneven finishes or even damage to the stones, which is a clear disadvantage for beginners.
Vibratory Polishers
On the other hand, vibratory polishers function differently, relying on a vibrating mechanism to move stones against polishing media. This method can be particularly effective for small or intricately shaped pieces where uniform contact is essential. The unique feature of vibratory polishers lies in their gentle action, which tends to minimize the risk of over-polishing or chipping.
Vibratory polishers are favorable for those who prefer a less hands-on approach. They can be left to work while the user attends to other tasks. However, they may not produce the same level of shine as rotary polishers, particularly on harder stones. Careful consideration should be given when choosing which polisher to employ based on the desired outcome and the characteristics of the stone.
Functionality of Polishers
Polishing Compounds
Polishing compounds are essential for achieving that coveted luster on a gemstone. These abrasives come in various forms, including powders and pastes, enabling lapidary artists to select the appropriate compound for their specific needs. The characteristic of these compounds varies widely, with coarser types being suitable for initial grinding and finer selections reserved for final polishing stages.
Understanding the right compound to use not only aids in getting a better finish but also extends the life of both the stone and the polisher. Applying the incorrect compound can lead to unsatisfactory results or even damage the workpiece. Thus, it's critical to match the polishing compound to the type of stone being processed.
Surface Finishing
Surface finishing is, perhaps, one of the final stages in the lapidary process, playing an important role in how the stone is perceived. This procedure determines how reflective and smooth the surface will appear, and thus can greatly impact the overall value of the gemstone. The distinguishing feature of an effective surface finishing process is that it can reveal or obscure flaws, enhancing the piece's natural beauty.
A diligent approach towards surface finishing not only ensures a polished look but can also increase durability. While some techniques may be labor-intensive, others can be more efficient. The choice should depend on the complexity of the stone's shape and the level of detail desired. In this regard, achieving a high-quality surface finish is not merely an aesthetic choice; it is an investment in the integrity of the gem.
Polishing Techniques and Best Practices
Polishing stones is a crucial element in the lapidary arts, elevating the aesthetic and tactile qualities of gemstones. This process not only enhances the visual appeal but also allows the craftsman to showcase the underlying beauty of each stone. Without proper polishing techniques, a well-cut stone may not reach its full potential. Understanding these methods can make all the difference.
Preparing Stones for Polishing
Before diving into the polishing phase, preparing the stones is half the battle won. This step involves ensuring that the stones have been adequately cut and shaped. Any rough edges or inconsistencies can prevent a smooth finish.
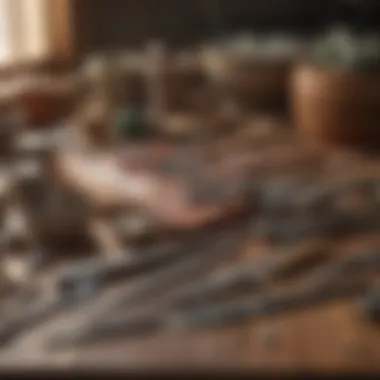
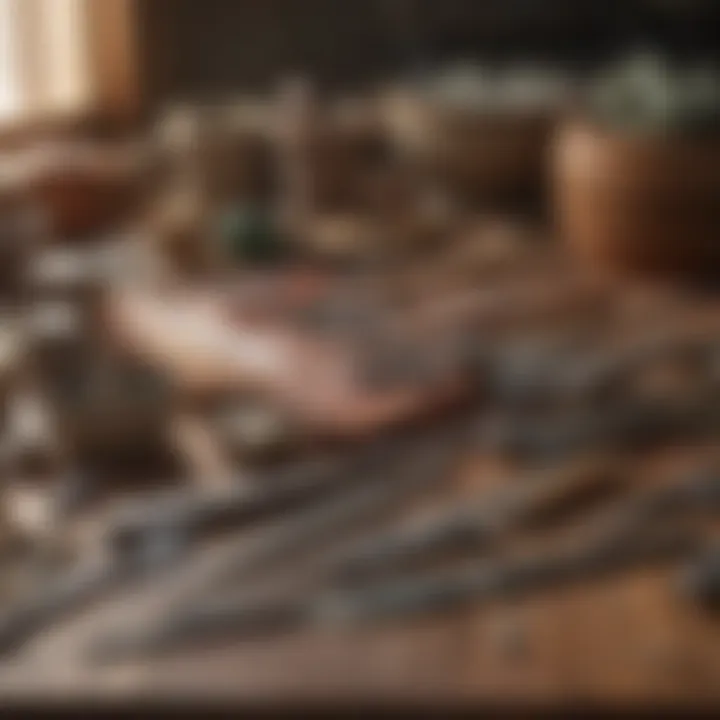
Proper cleaning is essential; stones should be free of dust, dirt, and oils. A simple rinse under warm water usually suffices. If you want an extra edge, some lapidarians use a mild soap solution. Pay attention to details here—getting the stones ready can save hours of polishing later on.
Effective Polishing Methods
Different methods suit various types of stones and desired finishes. It's crucial to choose the right approach to achieve that coveted gleam.
Process of Polishing
The process of polishing generally begins with coarse grits and progresses to finer ones. Starting with a coarse grit allows you to remove any stubborn scratches, gradually moving up to finer grades to buff the surface to a shine. The key characteristic here is gradual progression. Going too quickly can result in uneven surfaces and scratches.
Why is this method so celebrated among lapidary enthusiasts? Firstly, it provides consistent results that genuinely elevate the stone’s character. The slow and steady method tends to yield the best outcomes—it's almost like watching the stone evolve as you work it. However, one downside might be the time commitment; it can feel tedious for those looking to churn out polished stones in bulk, but patience is truly a virtue in this craft.
Achieving Desired Finish
Achieving the desired finish is what every lapidary aims for. It is about fine-tuning the surface to meet excellence or the specific requirements of commissions. The most notable characteristic in this pursuit is that it often demands significant attention to detail. You might start with polishing powders or compounds like cerium oxide, depending on the stone type.
This step can be gratifying, transforming a dull stone into a lustrous gem; it's where the magic happens. A distinctive feature about this stage is the variety of finishes one can accomplish—from a high gloss to a soft sheen. There's room for creativity and personal touch. Some might prefer to celebrate the raw beauty of a stone while others chase the glimmering perfection. Realizing the right balance between technique and individuality is what makes this stage both exciting and challenging.
In summary, mastering polishing techniques requires a blend of preparation, process, and adjusting to finish requirements. It's a notoriously detail-oriented craft, and those who invest the effort often reap the most astonishing results. Remember, every stone has its own story waiting to be revealed, and with the right methods, you’ll be the one to share it.
Maintenance of Lapidary Tools
Maintaining lapidary tools like saws and polishers is essential for achieving consistent quality in gemstone cutting and polishing. Proper upkeep doesn't just extend the lifespan of these machines but also ensures each stone is cut and polished to perfection. For rock and fossil collectors, understanding how these tools function and how to care for them can elevate their craft significantly.
Regular maintenance helps in preserving the efficiency and effectiveness of your lapidary equipment. It allows you to manage issues before they escalate into serious problems, which can be costly and time-consuming. The benefits of routine maintenance and care are countless, including ensuring safety during operation and achieving the best possible finishes on your stones.
Routine Maintenance for Saws and Polishers
Setting a schedule for routine maintenance is like turning over a new leaf in your lapidary journey. It becomes a habit, a part of your crafting process. Regularly checking the blades for nicks or wear, cleaning dust and debris from the machines, and lubricating moving parts are vital tasks. Here are some pointers for maintaining your saws and polishers:
- Inspect blades regularly: Blades should be checked for wear and tear or any chips that can affect cutting quality.
- Clean the machine often: A clean workspace will ensure smooth operation. Dust and residues can impede performance and affect results.
- Lubricate moving parts: Proper lubrication helps in reducing friction, extending the tool's life.
Each of these steps contributes to a seamless experience. And, believe it or not, it can even make your work feel more enjoyable!
Troubleshooting Common Issues
Issues are part and parcel of using equipment; learning to troubleshoot is key. Let's look into common problems that might arise:
Blade Wear
Blade wear is one of the critical concerns when it comes to lapidary saws. Over time, blades can become dull, affecting their cutting efficiency. This wear and tear contribute to the precision of your cuts and directly impact the quality of the finished stone. A key characteristic of blade wear is the gradual increase in friction during cuts, leading to uneven or rough edges. Knowing when to replace or sharpen blades is crucial, and it's a popular topic among lapidary enthusiasts.
Benefits of Monitoring Blade Wear:
- Improved consistency in cuts.
- Reduced waste of material, as a sharp blade is more efficient.
However, the downside can be that some collectors might put off blade checks, thinking they won’t notice until it’s too late. This can lead to longer work times and disappointing results.
Motor Problems
Motor problems can derail a lapidary session faster than you can imagine. They can arise from various sources, including overheating, electrical issues, or misalignment. The motor is the powerhouse behind your saw and polisher, making it imperative that it's in optimal condition. Key symptoms include unusual noises or an unexpected drop in power.
Characteristics of Motor Problems:
- They can manifest suddenly, catching many off-guard.
- Addressing these issues early can save time and frustration.
The significant advantage of knowing how to troubleshoot motor problems is that it allows you to swiftly identify the issue, be it a blown fuse or a dislocated belt. However, not addressing signs early can lead to extended downtime, which every lapidary should strive to avoid.
"An ounce of prevention is worth a pound of cure"— This saying rings particularly true for lapidary practitioners. Taking the time to properly maintain and troubleshoot your tools will ultimately enhance your crafting experience.
End
As we reflect on the intricacies of lapidary tools, particularly the saws and polishers, it becomes clear that these instruments are not mere extensions of a crafter’s hands; they are pivotal in transforming raw stones into polished gems. The journey from an unrefined rock to a gleaming jewel is far from simple. It involves a meticulous process that requires skill, knowledge, and the right equipment. By mastering the operation of saws and polishers, lapidary artists can unlock a world of creativity and precision.
The future of lapidary work is as bright as the gems themselves. This craft is evolving thanks to advancements in technology and a growing community of enthusiasts. Artists now have access to state-of-the-art tools that make the cutting and polishing process more efficient and less hazardous. Not only does this enhance the final product, but it also allows for more intricate creations. As we delve into this future, the significance of maintaining and understanding these tools remains critical. Without proper care, even the best tools can falter, leading to unsatisfactory results.
For those venturing into lapidary work, the importance of practical knowledge cannot be overstated. Each facet of this craft, from choosing the right saw to applying effective polishing techniques, plays a role in the overall quality of the work. The more informed and skilled collectors and artists become, the better their creations will reflect the beauty hidden within stones.
Ultimately, lapidary tools like saws and polishers do more than shape gemstones; they shape creativity, inspiration, and skill within a community that continues to share its passion for the art. Just as no two stones are alike, neither are the techniques and results of different lapidaries. Embracing this diversity and committing to lifelong learning will certainly push the boundaries of what is possible in the world of lapidary work.
"The beauty of a gem is not just in its appearance, but in the craftsmanship that reveals it."
In summary, as the lapidary arts evolve, there will always be room for innovation, education, and a deeper understanding of the tools at our disposal. This foundation will encourage the art form not only to survive but to thrive in the years to come.
The Future of Lapidary Work
Looking ahead, it’s evident that the future holds exciting developments in lapidary work. The rise of technologies such as 3D printing and digital design tools is already making waves in the community. Artists can draft and visualize their designs with precision before ever touching a stone. Moreover, innovations like laser cutting are gradually becoming accessible tools for more lapidary artists, offering an alternative that can produce clean lines and intricate patterns that traditional saws might struggle to replicate.
As we step further into this future, collaboration between traditional artisans and tech-savvy creators is likely to yield remarkable results. Imagine a world where vintage craftsmanship meets cutting-edge technology. Enhanced online platforms might foster this exchange, allowing lapidary enthusiasts to share techniques and learn from one another.
This evolution also means that the market for lapidary stones will likely diversify, offering a wider range of gemstones for both collectors and consumers. With growing interest, the demand for unique, high-quality pieces will only increase, pushing artisans to elevate their skills further. A shift in how people perceive gems—viewing them not just as commodities but as art—may also drive new practices and sustainability efforts within the industry.
In short, the future of lapidary work is not just about tools and techniques; it’s about a vibrant community that continues to embrace change and innovation while honoring the art’s deep-rooted traditions.