Jewelry Saws: Essential Tools and Techniques Explained
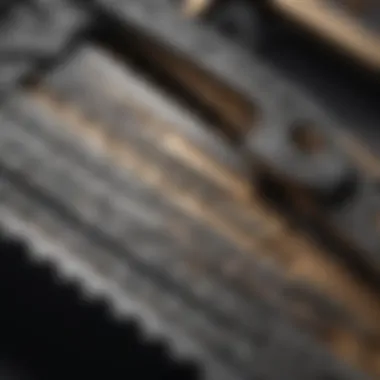
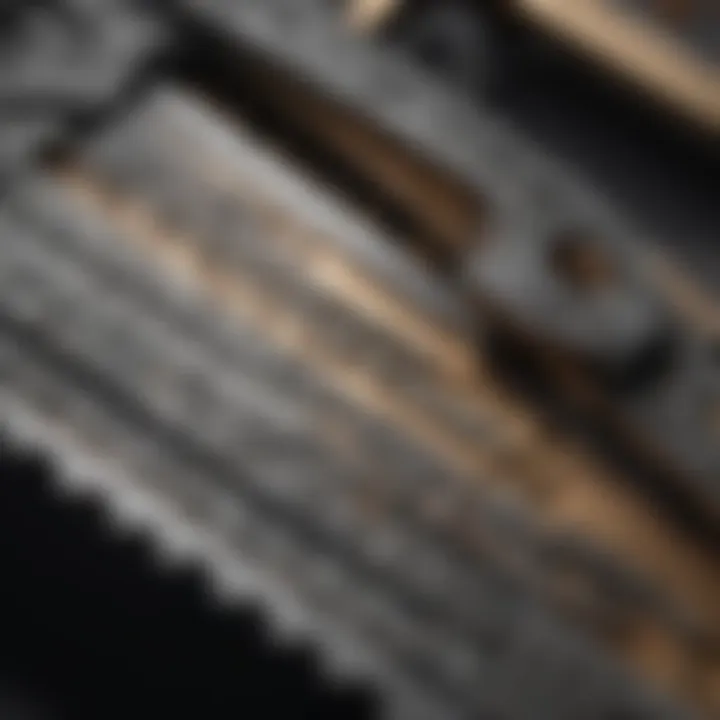
Intro
Jewelry making is a craft that demands precision and skill, particularly when it comes to intricate designs that often require the use of specialized tools. Among these, jewelry saws stand out as essential instruments for artists and collectors alike. Understanding these tools can elevate the artistry and functionality in creating pieces that are not only aesthetically pleasing but also structurally sound. Whether you're just starting out in jewelry making or you're a seasoned expert, a solid grasp of jewelry saws, including their types, applications, and maintenance, is vital for achieving your creative goals.
In this guide, we will cover a variety of topics related to jewelry saws. We'll explore the different types of saws available on the market, the techniques employed in using them effectively, and practical maintenance tips to ensure your tools remain in top condition. Alongside this, we will also discuss safety measures that should be taken while using these saws, allowing you to focus on your craftsmanship without unnecessary distraction.
As we navigate through this comprehensive resource, you'll unwind the significance of jewelry saws in the larger picture of jewelry making. Not only will this guide help enhance your technical proficiency, but it also aims to deepen your appreciation for the intricate craftsmanship that goes into every piece of jewelry. Let's get started.
Understanding Jewelry Saws
Jewelry saws serve as the backbone of skilled craftsmanship in jewelry making. For artisans looking to create, modify, or repair intricate designs, understanding the nuances of these tools is paramount. Knowing how to properly wield a saw can elevate one's skill level, allowing for precision that hand-cutting simply cannot match. This section highlights key elements to consider when diving into the world of jewelry saws, benefits they provide, and their overall relevance in the jewelry-making process.
Definition and Purpose
A jewelry saw is a specialized cutting tool designed for shaping and detailing metals and other materials used in jewelry creation. Its purpose goes beyond mere cutting; it enables artisans to create of delicate curves or intricate patterns with an accuracy that is hard to achieve with other tools. In essence, jewelry saws facilitate the transformation of raw materials into exquisite pieces of art.
Different Types of Jewelry Saws
Understanding the different types of jewelry saws can greatly influence the outcome of projects. Each type has unique characteristics tailored to specific cutting tasks. Knowing these can help artisans choose the right one for their specific needs.
Frame Saws
A frame saw is characterized by its rigid frame that holds the blade taut. This design provides stability, making it easier to execute both straight and intricate cuts. It’s particularly beneficial for larger pieces or materials where precision is crucial. Many jewelers prefer frame saws because they provide better control and allow for a variety of blades to be used, depending on the job at hand.
Frame saws may not be portable; they are often fixed to a bench. The advantage of this design allows for a robust cutting experience. However, this can be a disadvantage if one needs to work in diverse settings or locations.
Precision Saws
Precision saws offer unparalleled detail due to their finer blades and narrower frames. These saws are ideal for delicate work where even a slight deviation can spoil the end product. Artisans often turn to precision saws for tasks involving intricate designs, tight corners, and thin materials, making them a popular choice for professional jewelers.
The downside is that they can be less versatile than frame saws because of their design limitations; the blades break easier and require frequent replacement. Thus, keeping a good stock of blades is essential while working with precision saws.
Portable Saws
Mobile and efficient, portable saws suit those who value flexibility in their workspace. The ability to easily move from one work site to another or to work on the go is one of the biggest advantages of these saws.
Portable saws, while not as robust as their frame counterparts, offer convenience for simple cuts or on-site repairs. They are particularly helpful for hobbyists or less technical projects, causing less fatigue than heavier saws. Still, they may not cater to when precision and detail is the key focus.
"Choosing the right saw can make or break your project; understanding the differences is key to mastering jewelry making."
As you explore further into this guide, keep in mind the unique contributions each type of jewelry saw brings to your craft. Whether you prioritize portability, precision, or the stability of a frame saw, understanding what makes each tool unique is crucial to elevating your skills in jewelry-making.
Components of Jewelry Saws
Understanding the components of jewelry saws is crucial for anyone serious about their craft. These components determine how effective and precise the cutting process is, influencing not only the quality of the finished piece but also the efficiency with which an artisan can work. Without delving into the nuances of frames, blades, and handles, one would miss a significant part of mastering jewelry sawing.
Frames
The frame of a jewelry saw is often regarded as its backbone. This structure supports the blade and offers stability during use. Typically made from materials such as steel or aluminum alloy, frames are designed to provide enough tension to keep the blade taut.
A well-constructed frame allows for better control and precision, reducing the likelihood of blade breakage. Moreover, some frames come with a quick-release feature that enables swift blade changes, an essential aspect for jewelers who work with various materials and cut styles. They often have ergonomic designs to ensure a comfortable grip, which is vital for long hours of work.
Blades
Blades play a pivotal role in the cutting process. Without the right blade, even the best frame won’t yield effective results. The two critical aspects to consider when examining blades are the material and teeth configuration.
Material
The material of the blade is an important factor to consider because it directly affects durability and performance. Common materials include high-carbon steel, which is known for its strength and resilience. When it comes to materials, high-carbon steel is a favored choice thanks to its excellent wear resistance and sharpness retention. These blades can slice through a variety of materials, from soft metals like copper to harder ones like silver and gold.
However, these blades can also be prone to breakage under excessive stress and may need regular replacement depending on usage.
Teeth Configuration
Next, we look at the teeth configuration, which can dramatically influence cutting precision and the type of cut achieved. The spacing and shape of the teeth determine how smooth or rough the cut will be. For example, blades with more teeth per inch (TPI) are ideal for intricate or delicate work, as they create finer cuts. Conversely, blades with fewer TPI work well for faster cuts in thicker materials.
So, whether you're carving out detailed designs or cutting larger pieces, choosing the right teeth configuration is essential to achieving the desired results in your jewelry-making endeavors.
Handles
Handles serve as the connection between the artisan and the tool. Comfort in gripping is paramount since a good handle can reduce fatigue during long projects.
Most handles are ergonomically designed and may be made from materials like plastic or cushioned rubber, providing a balance between grip and comfort. Adjustable handles are also beneficial, allowing users to alter the distance between the blade and the grip based on their cutting style.
In summary, selecting the right components of jewelry saws is not just about choosing the most popular options; it's about finding the perfect balance that suits individual needs and projects. From frames that ensure stability to blades that suit different materials, every element plays a vital role in the overall performance of the saw.
"In the world of craftsmanship, the right tools make all the difference."
To conclude this section, understanding the components of jewelry saws lays the foundation for successful projects. Not only does it enhance your precision and creativity, but it also promotes a deeper appreciation for the craft.

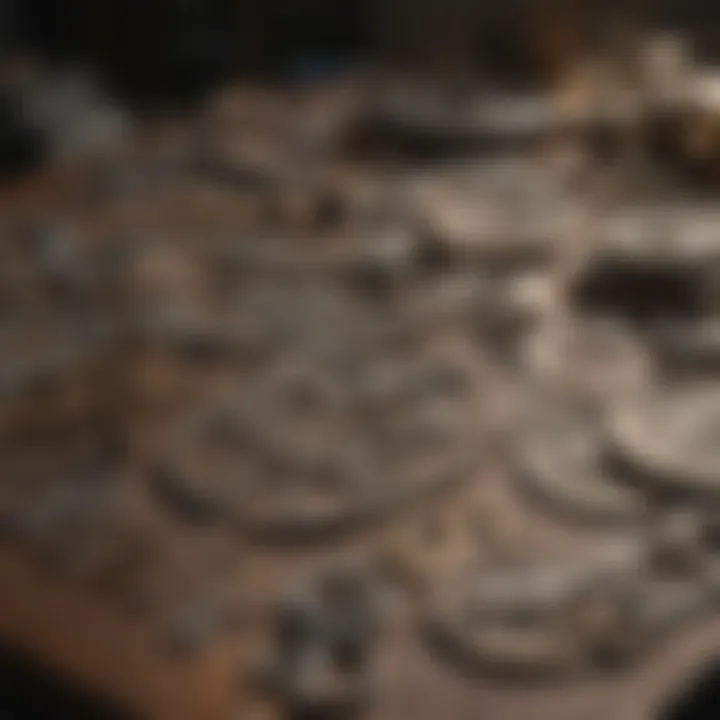
Choosing the Right Jewelry Saw
Choosing the right jewelry saw holds significant importance for anyone delving into the world of jewelry making or repair. This decision impacts everything from the quality of the final piece to the ease of the crafting process. The selection often boils down to specific elements such as material type, thickness of the material being cut, and the level of precision desired. Each of these factors gives insight into how a jeweler can tailor their tool selection. A well-chosen saw not only enhances efficiency but also can ultimately affect the craftsmanship's outcome. In this section, we will dive into what one needs to consider when selecting a jewelry saw and how to make a choice that aligns best with one's particular project needs.
Criteria for Selection
Material Type
When considering material type, it’s pivotal to understand that different materials have unique properties and lend themselves to various types of jewelry work. For example, steel is most commonly utilized due to its strength and durability. It cuts through metals easily and wears less quickly than others. Yet, something like brass may also be favorable for those working with softer materials, as it can provide a smoother cut with less resistance. Choosing the right material type not only determines what you can cut effectively but also influences how the saw will behave during use, affecting the overall working experience. A steel blade's robustness can be advantageous, although it may require more skill to handle effectively compared to a softer blade.
Thickness of Material
Material thickness is equally crucial when selecting a saw. A thicker material requires a saw that can withstand more force without bending or breaking. Conversely, if working with thin materials, one may benefit from a saw that allows for more delicate cuts without risking damage. For instance, if you’re crafting intricate designs in a thin sheet of silver, a finer blade makes all the difference in achieving those beautiful details, whereas a robust blade might just shred the material. The choice of thickness affects not only the tool but the technique used—a vital consideration for any artisan.
Desired Precision
Desired precision is where artistry meets functionality. Depending upon the complexity of the design, the level of precision required can vary significantly. For intricate designs, a saw with a fine-toothed, narrower blade offers more control and helps to navigate curves and small details without compromising on the aesthetic. On the other hand, for larger, more robust cuts, a larger tooth blade might be advisable as it allows for quicker work without sacrificing the overall integrity of the cut. Achieving the right precision is what can elevate a piece from ordinary to extraordinary; it’s a key characteristic to keep in mind when on the hunt for your ideal saw.
Brand Recommendations
Top Brands
In the realm of jewelry saws, certain brands have carved out a reputation for their quality and reliability. For instance, choosing from reputable brands like Wolf or Diafold can greatly enhance your work experience. These brands are known for their solid construction and variety of options, allowing jewelers to make selections tailored to their needs. While some may be drawn to newer brands promising cutting-edge designs, sticking with renowned manufacturers often translates to longevity and dependable performance. Well-established brands represent a trust factor that blends tradition with contemporary innovation, a significant benefit when investing in tools.
Quality Considerations
Quality considerations often boil down to the craftsmanship of the saw itself. The material used in the frame, the blade's sharpness, and how smoothly it operates all come into play. A jewelry saw with a sturdy frame that doesn’t wobble during cutting will allow for smoother operations, minimizing user fatigue and enhancing precision. Profiling blades may also range dramatically in terms of quality. A well-crafted blade that holds its edge will outperform a cheaply made one, which may require frequent replacements. Assessing quality is not just about performance; it’s about understanding the sacrifice of time and resources that might go into working with less reliable tools.
Investing in a quality saw may feel like an expense at first, but it often pays off in the quality of the work produced and the overall experience you have while making jewelry.
Selecting the right jewelry saw is not merely a matter of preference. It embodies a deep understanding of materials and techniques, ensuring that each cut reflects the skill and artistry of the maker.
Techniques for Using Jewelry Saws
Understanding the nuances of using jewelry saws is fundamental for both hobbyists and professional jewelers. Effective techniques not only enhance the quality of work but also ensure safety and efficiency during the cutting process. This section will guide you through the essential techniques needed to maximize the capabilities of your jewelry saw, ensuring you achieve the best possible results in your creations.
Setting Up the Saw
Before you dive into the actual cutting, setting up the saw properly is critical. A well-aligned saw allows for smoother cuts and decreases the likelihood of blade breakage. To set up your jewelry saw:
- Attach the blade securely: Ensure the blade is tightly fastened within the frame. If it’s loose, it may wobble during operation, causing uneven cuts or snapping.
- Check the tension: The blade should be taut but not overly tight. Too much tension can lead to breakage, while too little can cause inaccurate cutting and splintering.
- Position the workbench: Your work surface should be at a comfortable height. You shouldn't have to hunch over, as this can lead to fatigue and poor cutting technique.
Cutting Techniques
When you’re ready to cut, it’s important to know how to navigate different types of cuts based on the design you’re working on. Here we’ll break down three main cutting techniques that any jeweler should master.
Straight Cuts
Straight cuts are the bread and butter of jewelry making. They allow for clean and precise lines, which are essential in many designs. The main characteristic of straight cuts is their simplicity; they are straightforward, requiring less skill than more advanced techniques.
This technique is a popular choice due to its accuracy, particularly when working with metals or other hard materials. Straight cuts can be tricky, though; if you don't maintain a steady hand, the blade can easily veer off course. The unique feature of straight cuts lies in their potential for speed and efficiency. They are time-saving when you have to make several identical pieces.
Curved Cuts
Curved cuts open up a different realm of possibilities in jewelry design. These techniques allow for flowing designs and intricate shapes. The key characteristic here is flexibility; using the right blade helps you navigate around corners without compromising the integrity of the material.
Curved cuts are beneficial when working with softer metals or materials that don’t splinter easily. They foster creativity, allowing jewelers to bring more artistic elements into their work. However, they demand more practice. The unique aspect of curved cuts is the level of skill they require. If the cuts aren't executed carefully, you may end up with jagged edges that necessitate additional finishing work.
Intricate Designs
Creating intricate designs is where the artistry of jewelry making truly shines. This technique often combines both straight and curved cuts, resulting in detailed patterns or complex shapes. Intricate designs require a steady hand and a good understanding of the material you are working with.
One of the benefits of mastering intricate cuts is the uniqueness it brings to your pieces. Consumers today are drawn to one-of-a-kind items, and intricate designs help fulfill that need for uniqueness. However, these cuts can be quite time-consuming and may result in more waste material if not planned out properly. A key feature to keep in mind when working on intricate designs is the technical skill involved, as mistakes can often result in irreparable damage to the workpiece.
Finishing Cuts
Finishing cuts require a blend of precision and attention to detail, often emphasizing clean lines and polished surfaces. After the main cuts are made, finishing cuts enhance the overall look of a piece, ensuring the boundaries are smooth and professional. This final step in the cutting process can be the difference between a rough-looking piece and a polished jewel that radiates craftsmanship.
Effective finishing cuts often involve using finer blades and may require additional tools like files or sanding sheets. The key here is patience; rushing through finishing cuts can lead to mistakes. Overall, mastering all these techniques can elevate your work in the jewelry realm, giving each piece a touch of professionalism and artistry.
Safety Precautions
When working with jewelry saws, adhering to safety precautions is not just recommended; it’s essential. Jewelers need to manage delicate materials precisely, but these tools can also pose a variety of hazards. Ignoring safety can lead to accidents that affect not only the craftsmanship but also the artisan's well-being. By emphasizing proper safety measures, artisans can enhance their workflow while minimizing the risk of injury. Effective safety practices can yield numerous benefits, such as increased focus, reduced anxiety, and a more enjoyable crafting experience.
Personal Protective Equipment
When it comes to the realm of jewelry making, personal protective equipment (PPE) is your first line of defense. Each piece of equipment serves a particular role, creating a shield around you as you delve deep into your craft. Here’s a closer look at some key components:
- Safety Glasses: Protect your eyes from tiny particles that can fly off during cutting. It’s astonishing how small bits of metal or stone can catch you off guard.
- Dust Masks: Sawing creates dust that can irritate your throat and lungs. A good mask will help avoid respiratory issues so that you can continue enjoying your craft for years to come.
- Gloves: While handling materials and equipment, wearing gloves can provide grip and prevent cuts or scrapes. However, be careful not to use loose-fitting gloves, as they can get caught in the machinery.
- Ear Protection: If you work with machinery that creates noise, such as power saws, having ear plugs or noise-canceling headphones is advisable to protect your hearing.
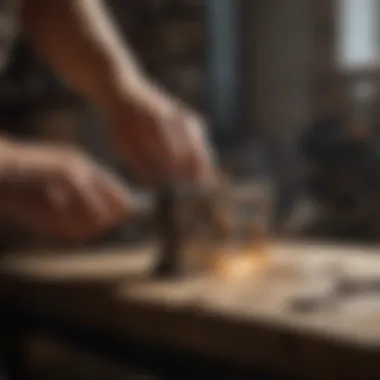
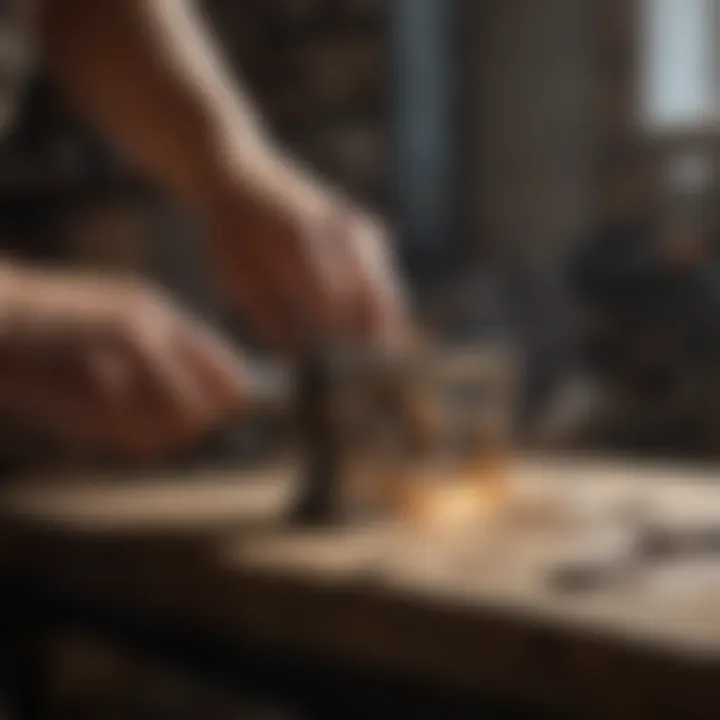
Investing in quality PPE is a small price to pay compared to the potential cost of an injury.
Safe Operating Practices
Beyond the equipment, implementing safe operating practices should be a top priority. Utilizing the jewelry saw effectively means ensuring that safety is woven into the very fabric of your workflow. Here are some recommended practices:
- Inspect Your Equipment: Before beginning any project, make it a habit to check your jewelry saw for damage. A cracked blade can lead to unexpected breaks. Look for any signs of wear and replace them as needed.
- Maintain a Clean Workspace: A cluttered work area can contribute to accidental slips and falls or misplaced tools. Keep your materials organized and clear away any debris caused during the cutting process. This promotes focus and reduces distraction.
- Work at Eye Level: Position your work so that you can keep both eyes on the blade and material. It prevents straining your neck and offers better control, ultimately resulting in more precise cuts.
- Use the Correct Technique: When cutting, ensure you let the saw do the work. Pushing too hard can lead to miscuts or damage to the blade, and maintaining a steady hand promotes greater accuracy.
Always prioritize safety to ensure a smooth experience when working with jewelry saws. The more careful you are, the more enjoyable your craft will be.
Maintaining Your Jewelry Saw
Keeping your jewelry saw in top-notch condition is essential for achieving precise cuts and maintaining your workflow. Whether you're an experienced artisan or just starting out, understanding how to maintain your tools can save you time and frustration in the long run. Not only does proper maintenance extend the lifespan of your saw, but it also enhances the quality of your work. Here, we delve into two key aspects: cleaning and lubrication, as well as blade replacement.
Cleaning and Lubrication
Cleaning your jewelry saw is not just about aesthetics; it's about functionality. Over time, debris, metal shavings, and dust can accumulate on the frame and blades, which could hinder cutting performance. A well-maintained saw operates smoothly and produces cleaner cuts.
- Regular Cleaning: After each use, take a moment to wipe down the saw with a soft cloth to remove any residue.
- Deep Clean: Periodically, feel free to use a brush with soft bristles to get into those nooks and crannies. Pay special attention to the areas around the blade holders, where grime often builds up.
- Lubrication: Applying a light machine oil to the moving parts of your saw can help to ensure it operates silently and smoothly. Just a few drops is usually enough—too much oil can attract dust.
- Avoid Harsh Chemicals: Stick with mild soap and water for cleaning; abrasive materials can scratch or damage delicate components.
"A clean saw performs better, allowing for smoother, more refined cuts. Taking a few minutes to maintain your tool can change your crafting experience entirely."
Blade Replacement
Changing your saw blades might seem intimidating, yet it's one of the most straightforward maintenance tasks you can perform. It’s crucial to ensure your blades are always sharp and suitable for the material you are working with. A dull blade not only hampers your cutting precision but also increases the risk of breakage.
- Signs of Wear: You’ll know it’s time to replace the blade when you notice increased effort in cutting or an uneven finish on the edges of your material.
- Removal Process: To replace a blade, start by loosening the frame’s blade tension. This can typically be done by adjusting a screw or knob on the frame. Once loose, simply slide the old blade out.
- Installation of New Blade: Position the new blade in the frame, ensuring that it’s aligned correctly. Tighten the tension back to a secure fit—too tight and you risk damaging the blade; too loose and it won’t cut effectively.
- Final Checks: Always double-check the alignment and tension of a newly installed blade before using it. A well-fitted blade can mean the difference between a joy and a headache in your work.
In summary, maintaining your jewelry saw is a critical factor in ensuring longevity and performance. A little effort in cleaning and timely blade replacement can not only improve the quality of your creations but also enhance your overall crafting experience.
Applications of Jewelry Saws
Jewelry saws are crucial tools that find their place in various areas of jewelry making and repair. These saws are not just for cutting; they open up avenues for creativity and precision in every piece crafted. Understanding their applications is vital, whether you're a novice or a seasoned jeweler. Below, we dive into how jewelry saws are employed in different contexts, each emphasizing the importance and benefits of mastering this tool.
In Jewelry Making
In the realm of jewelry making, the jewelry saw emerges as an indispensable ally. It facilitates the creation of intricate designs, allowing artisans to bring complex visualizations to life. A skilled jeweler can achieve both delicate patterns and robust shapes, which is essential in producing fine jewelry pieces. This technique enables not only cutting but also shaping, reducing waste material.
Key elements related to jewelry making using saws include:
- Versatility: Jewelers can switch between different blade types for various materials – whether it’s soft gold or hard platinum.
- Detailing: Sawing allows for exquisite detail, especially when working on filigree designs or engraving patterns.
- Customization: With the ability to cut and shape, jewelers can customize pieces according to client specifications.
Utilizing a jewelry saw can mean the difference between a standard piece and a standout design. The precision cuts create flat surfaces that fit seamlessly when soldered, ensuring structurally sound jewelry that lasts.
In Repair Work
In the world of jewelry repairs, a jewelry saw becomes an essential tool for restoring or reworking existing items. When it comes to repair work, the need for precision cannot be overstated. Here, the saw serves several functions:
- Removing damaged sections: When a piece is broken, the jewelry saw allows for carefully cutting out damaged parts without compromising the integrity of the overall design.
- Resizing: Jewelers can effectively resize rings or chains by sawing through links or bands safely and accurately.
- Reworking designs: Often, older pieces need an update or redesign after years of wear. A jeweler can skillfully use a saw to cut and adjust, breathing new life into cherished items.
A jewelry saw isn’t just a tool; it’s a pathway to combining history with present trends in repair work.
The ability to effectively utilize a jewelry saw for repairs highlights its role in maintaining the legacy of jewelry pieces. Repair work retains the sentimental value attached to jewelry, making expertise in this area crucial for jewelers.
Comparing Jewelry Saws with Other Cutting Tools
When discussing jewelry making, the tools involved play a crucial role in precision and craftsmanship. This section dives into the comparison between jewelry saws and other cutting tools, enhancing the understanding of their unique characteristics, advantages, and limitations. Understanding these differences can help jewelers make informed choices tailored to their specific needs around design and technique.
Versus Coping Saws
Coping saws and jewelry saws are often seen as cousins in the world of cutting tools, but the devil's in the details.
- Purpose: The coping saw is designed primarily for larger cuts and is great for thicker materials. If you’re working with wood or thicker sheets of metal, a coping saw might just feel like the right fit, but jewelry saws excel when it comes to intricate cuts. Those who want to work on smaller designs would benefit more from the precision of jewelry saws.
- Blade Type: Coping saws use a more robust blade compared to jewelry saws. Their blades are thicker and less nuanced, which might help in quick cuts but won't provide the delicate intricacy of jewelry saw blades. When it comes to fine detail — think of cutting tiny gemstones or creating delicate patterns on thin metals, jewelry saws take the prize.
- Versatility: While coping saws can handle a variety of materials, jewelry saws cater exclusively to the needs of fine jewelry making. Artists focusing on detailed work like filigree should grab a jewelry saw as soon as they can. If the goal is intricate craftsmanship, jewelry saws should be your go-to tools.
"Choosing the right saw is as crucial as the design itself — every cut tells a story."
Versus Band Saws
Band saws are a different beast altogether. With their larger sizes and capabilities, they shine in certain contexts but might not suit every jeweler’s needs.
- Cutting Volume: Band saws are typically used for larger cuts and can handle thicker stock efficiently. However, for detailed work, they might not offer the finesse required for jewelry making. If you need to prepare material quickly and on a larger scale, a band saw could be handy, but it won't replace the precision found in jewelry saws.
- Blade Size: The blades on band saws are much wider and meant for speed over precision. Jewelry saws, on the other hand, come with fine, thin blades designed for intricate detailing, allowing artists to maneuver with grace through their materials. This subtlety isn’t something a band saw can promise.
- Space and Setup: Band saws usually require more workspace and installation, which can make them less practical for small studios that focus on intricate designs. Jewelry saws, in contrast, are portable and easy to set up, often only requiring a stable work surface.
Common Issues and Troubleshooting
Understanding common problems that arise while using jewelry saws is an indispensable aspect of mastering this craft. Whether you are a seasoned jeweler or a budding artist, being able to identify and fix these issues can save valuable time and resources. From blade breakage to the frustration of uneven cuts, navigating these hurdles is crucial for achieving precise results and maintaining the integrity of your work.
Blade Breakage
Blade breakage is a common plight for jewelry makers, and it can happen surprisingly often, even to the most diligent artisans. The root causes can range from improper blade tension to the choice of an inadequate blade for the material being cut.
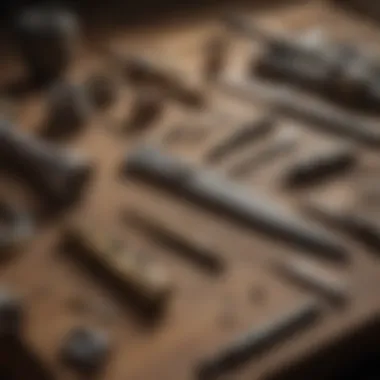
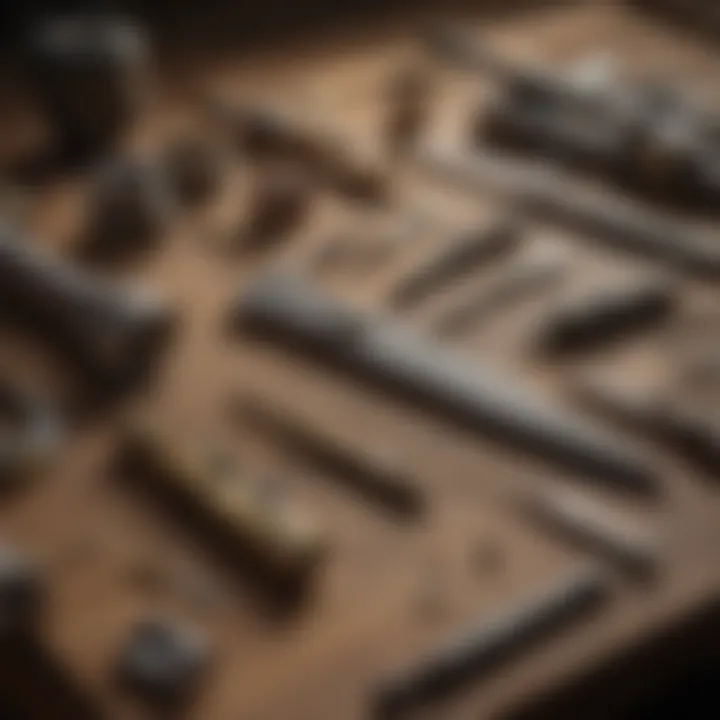
- Tension Matters: The tension on a blade must be just right; too tight and it’s more likely to snap, too loose and it can wander off-course. A good rule of thumb is to find the sweet spot by ensuring you can press the blade without excessive bending but not so much that it feels like a guitar string ready to snap.
- Material Choice: Using the right blade for the specific material is significant. For instance, if you’re working with hard metals, ensure that you opt for a blade designed to handle those. Using a delicate saw on a tough material is a sure recipe for breakage.
- Angle of Attack: Another often-overlooked factor is how you approach the cut. If you're pushing too hard or at an awkward angle, the stress on the blade increases, leading to an unfortunate snap. Always maintain a consistent and smooth cutting motion, allowing the saw to do the work.
"Recognizing the nuances of blade behavior is essential in extending its life and improving the overall cutting experience."
Uneven Cuts
Uneven cuts can be the bane of any jeweler's existence. Such discrepancies not only compromise the aesthetic quality of your work but can also affect the structural integrity of the piece. Here are some potential causes and solutions:
- Guide Your Cuts: When cutting, guiding the saw along a marked line is crucial. If the saw wanders or isn’t kept in line with the edge, you can end up with wavy or jagged edges. Marking your lines with a fine pencil or a scribe can create a helpful guide.
- Technique Check: The way you hold your saw can make a world of difference. If your hands are not steady or if you’re applying uneven pressure, the resulting cut will reflect this lack of control. Practice holding your hands firm, with a comfortable grip, and focus on maintaining a gentle rhythm.
- Blade Condition: The condition of your blade plays a massive role. Dull blades not only cause more friction, leading to uneven cuts but can also worsen the risk of breaking. Regularly monitoring and replacing your blades can significantly improve the quality of your cuts.
Innovations in Jewelry Saws
The jewelry industry is constantly evolving, pushing artisans towards innovation. This section hones in on recent advancements in jewelry saws, highlighting their importance not just in terms of efficiency but also precision and creativity. In a world where every detail matters, staying ahead of the curve with the tools used can transform the entire crafting process.
Technological Advances
In recent years, technology has seeped into every nook and cranny of the jewelry-making industry. New machinery and tech advancements have revolutionized the way jewelers approach sawing tasks.
One of the most notable advancements is the introduction of digital saws that utilize computer-aided design (CAD) software. These saws can read complex designs and adjust their cutting paths accordingly, resulting in far more accurate cuts than manual techniques can achieve. More than just a gimmick, these machines save valuable time and minimize the trial-and-error phase, allowing for precision that can be measured and replicated.
Another exciting development is the improvement in blade technology. These blades now have advanced coatings that prevent wear and tear, leading to longer-lasting tools. Jewelers no longer need to frequently swap out blades mid-project, which enhances workflow.
Let's take a look at some specific benefits of these technological advances:
- Higher Accuracy: The precision offered by digital adjustments reduces human error.
- Time Efficiency: Less time spent on adjustments translates to quicker project turnarounds.
- Enhanced Durability: Modern blades require less frequent replacements, cutting material costs.
"Innovation in tools directly correlates with an artisan's ability to push the boundaries of design. Without these tools, creativity often has unspoken limitations."
New Materials and Blades
The evolution of materials used in jewelry saw blades has been significant. Previously, saw blades were primarily made of steel, but innovations have introduced composite materials and specialty coatings that enhance performance.
One such advancement is the introduction of diamond-tipped blades, which offer not only exceptional cutting abilities but also greater longevity. These blades can slice through harder materials that standard steel blades struggle with, such as ceramic and certain gemstones. For jewelers who often work with varied materials, this variety of options allows for more versatility in designs.
Additionally, there’s been a shift towards using flexible materials in the construction of blades. This flexibility permits the saw to navigate curves and intricate patterns with ease, allowing artisans to maintain control and produce clean cuts even in the most complex designs. Some blades also feature innovative teeth configurations adapted to specific cutting tasks, further enhancing functionality.
The new materials and blade offerings also positively impact sustainability. Many of these innovations focus on reducing waste, whether through longer blade life or creating recyclable components, aligning modern jewelry crafting with eco-friendly practices that many consumers now demand.
In summary, innovations in jewelry saws open doors for jewelers and artisans, making the crafting experience richer and more diverse. With the combination of advanced technology and new materials, jewelry makers are now empowered to expand their creative horizons and tackle challenges that once seemed insurmountable.
Cultural Significance of Jewelry Saws
The role of jewelry saws extends beyond mere functionality; they are entwined with cultural stories and historical contexts that enrich the practice of jewelry making. They aren't just tools; these saws echo craftsmanship, artistry, and the human alliance with materials, tracing a pathway from ancient traditions to modern practices. Investing time to understand their cultural significance can deepen one's appreciation of not just the saws themselves, but the jewelry that emerges from their use.
Historical Context
Jewelry making is an ancient craft, reaching back to various civilizations where artisans showcased skills passed down through generations. Historically, tools like the jewelry saw enabled jewelers to shape and cut materials with precision, becoming fundamental in many cultures worldwide.
For instance, during the time of Ancient Egypt, gold and silver were not just valuables; they symbolized status and power. Jewelers employed rudimentary saws made from stone and metal to carve intricate designs, which often held spiritual significance within their society. This connection between tool and ritual underscores the importance of jewelry saws—it wasn't only about extracting beauty but also about imbuing pieces with meaning.
Fast forward to the Renaissance, where advancements in craftsmanship and artistry flourished. Saws became vital in creating detailed metalwork favored by nobility. The meticulous saw work seen in pieces from this era, particularly in silver and gold jewelry, showcases how essential these tools were in pushing forward creative boundaries.
As we look more closely at cultural narratives, artifacts found in archaeological sites worldwide reveal how jewelry saws have evolved. Their versatility is not just a testament to technological advancement but also a reflection of cultural shifts, adapting to changing artistic expressions over the years.
Impact on Jewelry Design
The innovation and versatility of jewelry saws shape how artists conceive jewelry pieces today. These tools are not simply for cutting material; they open doors to intricate designs and detailed craftsmanship, allowing jewelers to explore creativity without limits.
The following points highlight how jewelry saws impact design:
- Precision Cutting: Jewelry saws can create precise lines and curves in various materials, enabling artisans to execute elaborate designs with minimal effort. The delicate nature of these cuts allows for unique features that capture a viewer’s eye.
- Adaptation of Styles: Different cultures have adopted different techniques and styles over centuries. Jewelry saws facilitate this exchange, allowing for a blend of methods from various regions. A modern designer might use a saw to incorporate elements from African beadwork fused with contemporary Western design.
- Innovation in Materials: The advancement of materials used alongside saws influences design trends. For example, the introduction of synthetic materials and alternative metals requires jeweler's saws that can handle different hardness levels, pushing the envelope for new jewelry aesthetics.
As the world leans further into individual expression and personalization, the jewelry saw stands at the frontline. This means the cultural significance of these tools will continue to evolve, reflecting the changing ideals of beauty, craftsmanship, and identity.
Jewelry saws are more than tools; they are bridges connecting ancient traditions with contemporary artistry, allowing creators to convey narratives through intricate designs, bearing testimony to human creativity and cultural heritage.
Epilogue
In wrapping up our thorough examination of jewelry saws, it’s crucial to recognize their role beyond mere cutting tools. This article has peeled back the layers to reveal essential elements in the use, maintenance, and evolution of jewelry saws, which are indispensable for any jewelry artisan or enthusiast.
Recap of Key Points
Throughout the discussion, several pivotal points have emerged:
- Understanding Types of Jewelry Saws: From frame saws designed for sturdy cutting to precision saws meant for detailed work, different types cater to varied needs.
- Importance of Proper Maintenance: Regular cleaning and timely blade replacement ensure optimal performance, minimizing the frequency of unexpected challenges during projects.
- Safety First: Wearing appropriate personal protective equipment and adopting safe operating practices are non-negotiable to prevent accidents.
- Cultural and Historical Relevance: Jewelry saws have a rich history that intertwines with the artistry of jewelry making, impacting designs throughout the ages.
These points underscore the broader significance of expertly wielding a jewelry saw, not merely in technical terms, but also as part of a narrative that celebrates craftsmanship.
Future Trends in Jewelry Saw Usage
Looking ahead, several trends may influence how jewelry saws are utilized in the coming years:
- Integration of Advanced Technologies: With rapid technological advancements, tools might evolve to include digital features, making precise cutting easier for both novices and professionals.
- Sustainable Materials: There's growing interest in eco-friendly materials that could shift traditional tool manufacturing towards more sustainable practices.
- Educational Workshops: As the art of jewelry making gains popularity, more hands-on workshops will likely emerge, focusing on imparting skills effectively, especially around saw usage.
- Online Communities: A surge in online platforms (like Reddit) dedicated to jewelry crafting will provide spaces for sharing techniques, troubleshooting problems, and innovating new approaches.
Embracing these trends can significantly enhance the mastery of using jewelry saws, fostering an environment of creativity and technical excellence. As the landscape of jewelry making continues to evolve, staying abreast of these changes is essential for anyone serious about this craft.