Mastering Jewelry Making with a Dremel Tool: Techniques & Tips
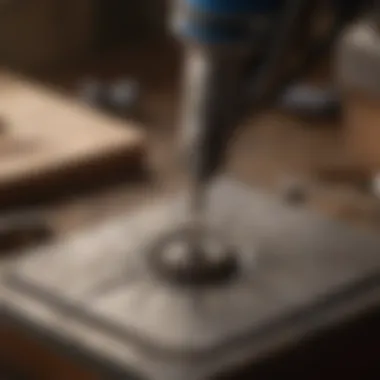
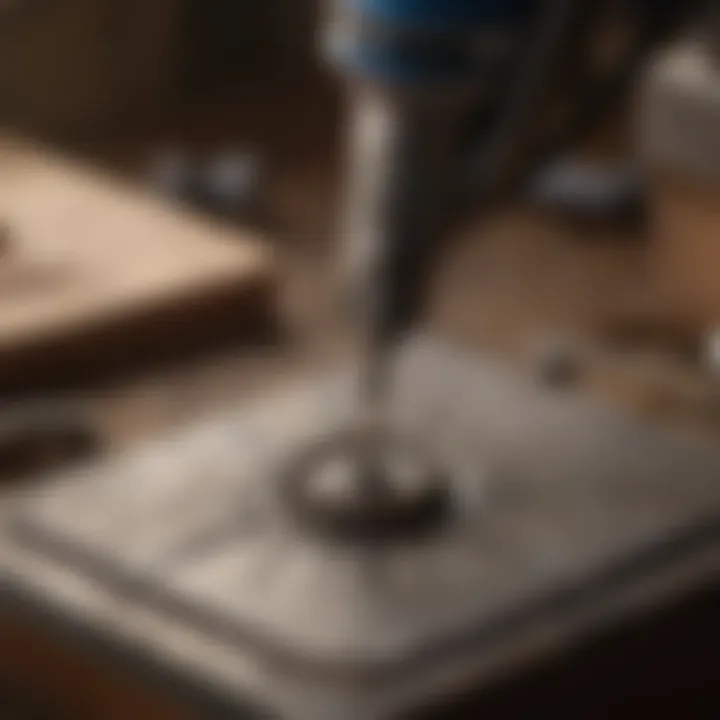
Intro
Jewelry making is a timeless craft that blends artistry and technology, offering a unique opportunity to create personal adornments. Among the many tools employed in this trade, the Dremel tool stands out as a versatile instrument for both novices and professionals. Utilizing this device can significantly enhance the quality and precision of your jewelry designs. With an array of attachments and a compact design, a Dremel tool is particularly well-suited for tasks like engraving, shaping, and polishing materials used in creating one-of-a-kind pieces of jewelry.
In this article, we will explore how to integrate Dremel tools into your jewelry-making processes. We will highlight essential techniques, introduce safety measures, and guide you through the selection of materials and accessories tailored to elevate your crafting experience. By understanding the intersection of craftsmanship and modern tools, this guide aims to empower you in your jewelry-making endeavors.
Key Points
- Introduction to Dremel tools
- Techniques for optimal usage
- Safety tips while working with the tool
- Detailed material selection recommendations
- Specific Dremel accessories beneficial for jewelry making
As we embark on this exploration, you will gain insight into effective practices and strategies for using Dremel tools, enhancing your skills and creativity. Prepare to delve into a realm where precision meets artistry, ultimately transforming your approach to jewelry design.
Foreword to Jewelry Making
Jewelry making is a delicate art that fuses creativity with technical skill. It enables individuals to express themselves, featuring unique designs that might feel personal or culturally significant. This section highlights where the art began and the tools that are integral to the craft.
Historical Context of Jewelry Making
Human beings have worn jewelry since ancient times. Archaeological finds link the craft to civilizations like the Egyptians and Mesopotamians, where jewelry served as both adornment and a status symbol. Various materials, such as gold, silver, and precious stones, were used to signify social hierarchies and cultural beliefs. Alongside tangible beauty, jewelry held symbolic meaning, often associated with protection, wealth, and spirituality.
As innovation progressed, different techniques emerged, reflecting societal changes. The use of the Dremel tool points towards the modernization of jewelry making, allowing for precision cutting, shaping, and engraving. The evolution of tools has transformed an age-old art form into a more accessible practice for enthusiasts today.
Importance of Tools in Jewelry Making
Proper tools in jewelry making can make a significant difference in the outcome of a piece. While many artisans crafted with basic implements in the past, it is critical to understand the value of specialized equipment today. High-quality tools, such as the Dremel, provide advanced capabilities compared to rudimentary ones.
The intricate nature of jewelry design often requires executing detailed work. Dremels serve multiple functions, from cutting metal to engraving textures into surfaces. Investing in good tools ensures that artists can express their visions more effectively.
It is equally vital to know the various tools required for specific tasks such as:
- Cutting and shaping materials
- Preparing surfaces for finishing
- Creating detailed designs with precision
In summary, effective tool mastery substantially enhances one’s capability in jewelry making. Those who take their craft seriously should devote equal attention to their toolkit as they do to personal creativity.
Overview of the Dremel Tool
The Dremel tool has become an essential implement for jewelry makers, offering unparalleled versatility and precision. Understanding the key features and various types of Dremel tools helps in making informed choices. This is vital for anyone interested in enhancing their skills or beginning their journey in jewelry creation with a Dremel.
Features of a Dremel Tool
Dremel tools come equipped with a range of features that make them ideal for jewelry making. Notably, their variable speed settings allow for customization during different processes. This means you can adjust the speed depending on the material you are working on, ensuring you achieve optimal results.
Moreover, the ergonomic design promotes comfort during extended use, reducing strain. Additionally, the compact size enhances portability. Users can easily maneuver the tool, even in tight spaces, which is often crucial in jewelry crafting. The variety of attachments available expands the tool's functionality. These can include cutting, grinding, sanding, and engraving bits, offering the capability to perform multiple tasks with one instrument.
Another standout feature is the ease of swapping out attachments. Most attachments can be changed quickly with minimal tools, allowing for greater efficiency in workflow. Dremel tools also feature versatile collets that possess the ability to grip various shank sizes, accommodating a broad spectrum of accessories. This diversity in features greatly enhances the Dremel's usability for intricate applications in jewelry making.
Types of Dremel Tools Available
When considering the types of Dremel tools, one encounters a few popular models suited for jewelry crafting.
- Dremel 3000: This model is appreciated for its simplicity. It features a powerful motor and comes with numerous attachments, making it perfect for beginners.
- Dremel 4000: This model offers more power and versatility. Along with additional attachments, it provides increased speed, which can enhance performance on various materials like wood, metal, and plastics.
- Dremel Lite: This lightweight version is ideal for delicate work. It is easily operated and is promoted for its ease of handling in intricate designs.
- Dremel Ultra-Saw: This variant provides a unique cutting solution, especially for larger materials or thicker pieces that require strong cutting capabilities.
In essence, selecting the appropriate Dremel tool hinges on specific crafting needs. Evaluating both the features and types available will directly enhance the quality of work produced, marking a significant upgrading phase in the jewelry making journey.
Using Dremel for Jewelry Making
Using a Dremel tool for jewelry making greatly expands the possibilities in design and execution. It offers high versatility and precision for intricate work. Many jewelers, hobbyists, and artists have found that it enables them to execute cuts, finishes, and engraverings with much greater ease compared to traditional means.
The Dremel tool allows for a rapid shifting of functionalities, which is essential considering that jewelry often requires detailed and careful attention to various elements. The applications of a Dremel include intricate engravings, diverse cutting techniques, smoothing surfaces, and building complex textures. Understanding how a Dremel fits into this process can improve craftsmanship significantly.
Moreover, there are practical benefits associated with the Dremel, which promotes efficiency. Tasks that once took much longer and required several tools can now be managed with one reliable device. Nonetheless, proficiency with the Dremel is built through practice. Knowing about specific techniques and having the right accessories can truly enhance the experience.
A Dremel should not just be seen as a tool, but also as a catalyst for creativity in the jewelry-making world.
Understanding one’s tool and how to adapt it to individual projects is key in improving your overall craftsmanship and results.
Cutting Techniques
Cutting is one of the primary capabilities where the Dremel tool excels. Precise cutting is crucial, especially when dealing with delicate materials. There are various types of cutting attachments available. Each has its purpose.
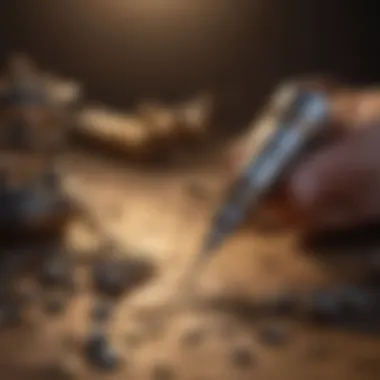
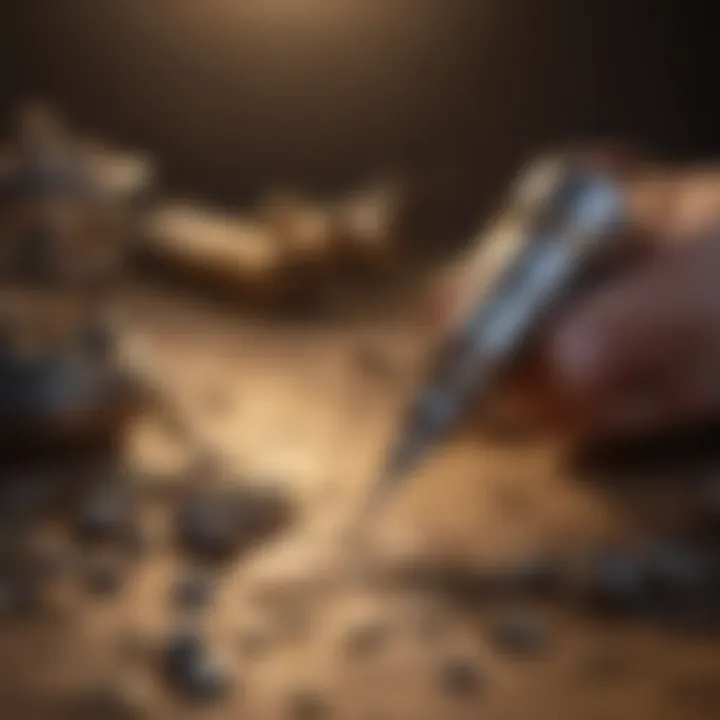
Assessing the specific material you work with is important. The thickness, hardness, and texture of the material will influence the choice of the cutting accessory.
Some tips on cutting include:
- Select the right cutting disc: For metal, a reinforced cutting wheel is recommended. For softer materials, various types of rotary bits will suffice.
- Maintain a steady hand: A smooth and controlled hand will reduce the likelihood of mistakes.
- Plan the cuts: Mark areas to be cut beforehand using a safety pencil. This facilitates accuracy.
Engagement with the Dremel in cutting operations not only smoothens profits on time but also reduces wastage of materials.
Sanding and Finishing
After cutting, the surface of the jewelry piece may require more detail. Sanding and finishing are integral processes to achieve a polished look. Dremel tools shine here as well. Various attachments like sanding drums and flap wheels should be utilized.
In sanding, you want to refine the surface. Begin with courser sandpaper to shape the piece, then follow with finer grades. The caliber of the sanding drum applied is key. This helps to avoid scratches and includes polishing the surface tone.
You may follow these pointers when sanding:
- Work gently: Excessive pressure can damage the material.
- Rotate the workpiece: Constantly alter angles to get a uniform finish.
- Clean frequently: Remove debris often to avoid pawning the work surface.
Finishing should embrace the final touch. Consider using polishing bits for a shiny surface. The right compounds make a difference for the final look.
Engraving Designs
Engraving designs add a layer of unique character to any piece of jewelry. Dremel tools easily modify surfaces to create personalized designs. Many find that engraving can serve both functional purposes—like texture—and aesthetic appeal.
When engraving, start by choosing an appropriate engraving bit. Various shapes exist: from tapered needs to specialty carvings. Many designs can be created by simply moving the Dremel over your sketch.
Practical steps include:
- Initialize with manual outlines: Pre-inscribe lines with a marker or etch them lightly.
- Select moderate speed: Often, slower speeds allow more control and accuracy in engraving.
- Focus on technique: Engage in different angles and strokes to create diverse effects.
Using the Dremel for engraving undoubtedly permits depth and intricacy in your jewelry making endeavors.
Essential Accessories for Dremel in Jewelry Work
Accessorizing your Dremel tool with the right components is critical in jewelry making. Accessories enhance the tool's versatility and performance, allowing for various techniques to be applied smoothly. In this section, we will detail three essential accessories that every jeweler should consider to optimize their Dremel tool experience.
Cutting Discs
Cutting discs are perhaps one of the most fundamental accessories for jewelry work. They are used primarily for cutting various materials, such as metal, plastic, and glass. Their precision can make the difference between clean lines or rough edges that require more work later. Many users prefer thin discs for more intricate cuts, which reduces the material loss and ensures sharper edges.
- Benefits:
- Efficiency: Thin and flexible, enabling intricate cuts.
- Versatility: Suitable for different materials.
- Ease of Use: Applicable in both beginner and advanced projects.
It is advised to confirm the compatibility of the disc with the specific model of your Dremel tool. Whether you choose the Dremel EZ345 or Dremel 420, ensure you have the necessary size for your projects. A lot of practical knowledge can stem from the right choice in discs, impacting not only outcomes but overall satisfaction with your crafted pieces.
Drilling Bits
Drilling bits stand out as another vital accessory for jewelers. They are specifically designed for creating holes in various materials, from soft resin to tougher metals. With various sizes available, selecting the right thickness depends on the design and intended use of the piece.
- Considerations:
- Size Range: Drill bits typically range from 1/64 to 1/8 inch in diameter.
- Material: High-speed steel bits are best for metal, while carbide bits work great with harder stones.
Proper usage of drilling bits can lessen the risk of burs and ensure a clean hole. Additionally, innovative accessories like Dremel’s drill bit sets can provide readiness to tackle various tasks, allowing modular responsibility in crafting.
Polishing Wheels
Polishing wheels are key to achieving a professional finish on your jewelry. These rich-textured wheels buff surfaces smoothly, adding shine and reducing scratches left after cutting or engraving processes. They can be used on a range of materials, including metals and plastics, making them incredibly versatile as well.
- Types to Consider:
- Felt Wheels: Soft and ideal for intricate polish without any scratch risk.
- Cotton Wheels: Great for larger, flatter surfaces.
The choice of polishing wheels directly affects the final appearance of your pieces. Inadequate polishing shortchanges the talent behind your designs. Hence, selection plays a significant role in presenting work that is appealing and refined.
“Accessories are not just additional tools; they are the right tools for the job, resulting in true works of art.”
As this section shows, utilizing the proper accessories can significantly enhance your experience and the quality of your jewelry-making projects. Taking some time to understand these components can lead a long way toward crafting masterpieces that resonate with artistry and precision.
Material Selection in Jewelry Making
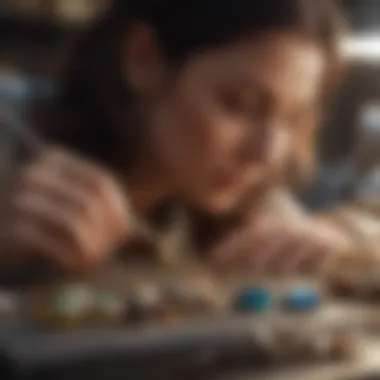
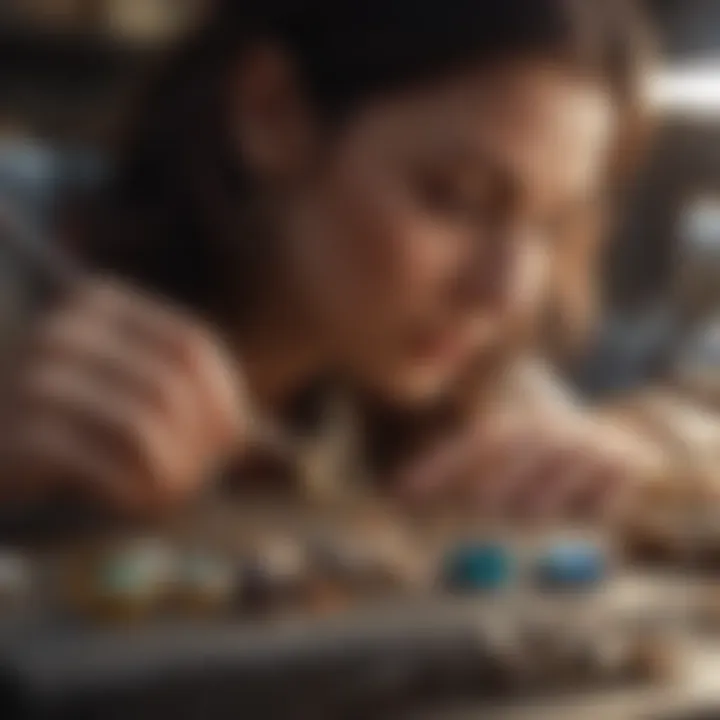
Choosing the right materials in jewelry making is crucial. It impacts both the functional aspects and the aesthetic value of the final pieces. Not only does this selection determine durability and overall design integrity, but it also plays a role in the wearer's experience. A well-considered choice enhances the wearability and appeal of jewelry, catering to National everyday needs and personal style preferences.
Understanding Different Materials
When it comes to crafting jewelry, a variety of materials come into play. Broadly, these materials can be categorized into metals and non-metal options. Each material presents its own set of qualitites and challenges, demanding careful contemplation.
- Metals: These include gold, silver, copper, and brass. Their malleability and durability make them favorable for many designs. Each metal carries different tarnishing and welding properties. Conducting impact tests or chemical tests can help to ascertain quality and durability.
- Non-metals: Materials like beads, gemstones, glass, and ceramic can offer interesting textures, colors, and dimensions. Non-metals often encourage more creative expression with unique patterns and contrasts.
It's important to experiment with various types to locate the personal fit. Building a selection of materials can foster greater versatility in future projects.
Metal vs.
Non-metal Materials
Choosing between metals and non-metals can define the characteristics of the jewelry being created:
- Metals generally ensure durability and longevity. They can be molded with tools like the Dremel for precise configurations.
- Non-metals often reflect personal tastes and trends, providing possibilities that many metals cannot match in terms of design intricacies.
Before committing to material, it's wise to consider the end use of jewelry, personal preferences, and maintenance requirements.
Key Considerations:
- Cost: Metals are often more costly than non-metal materials.
- Weight: Depending on the application's need, lighter materials can be preferable.
- Care: Each material demands specific handling and cleaning techniques.
In essence, understanding materials redefines artistry and craftsmanship in jewelry making with a Dremel. Making informed decisions leads to improved satisfaction with each piece created.
Safety Measures When Using a Dremel
Safety measures are crucial when using a Dremel tool, especially in the context of jewelry making. Engaging in any crafting process entails a certain level of risk, and Dremel tools are powerful devices designed to cut, sand, and engrave materials at high speeds. Without proper safety precautions, one might face accidents that can result in serious injuries or long-term damage. Effective measures ensure smooth, enjoyable crafting sessions and protect against both minor and significant hazards.
Protective Gear Recommendations
While the Dremel is an extremely versatile tool, taking care of yourself while using it is just as important. Here are some recommendations for protective gear:
- Safety Goggles: Always wear safety goggles to protect your eyes from dust and debris that the Dremel can produce. These items are simple to use and can save your vision.
- Dust Masks: Airborne particles from materials mean that dust masks are necessary. They protect your lungs from harmful inhalation while sanding or cutting.
- Ear Protection: The noise from the Dremel can become quite loud, particularly during extensive use. Earplugs or ear muffs can safeguard your hearing in the long run.
- Gloves: Wearing gloves can protect your hands from sharp edges and hot materials. However, be cautious, as gloves can sometimes get caught in the tool.
- Aprons: Aprons protect your clothing and skin from finished products and abrasive material particles. They are particularly useful in keeping your working area clean.
Proper implementation of protective gear creates a sustainable workspace that allows for extended periods of creativity without the distraction of physical discomfort or injury.
Work Environment Best Practices
Having a safe work environment is just as essential as protective gear. The following practices can help reduce risks when using the Dremel:
- Well-Ventilated Area: Ensure your workspace is well-ventilated to avoid respiratory issues caused by dust exposure. Open windows or use a fan to allow for airflow.
- Clean Workspace: Keeping the area organized helps prevent accidents. Clear away unnecessary tools and debris. A clutter-free space is easier to navigate.
- Stable Surface: Utilize a sturdy table or workbench to handle heavy operations. This stability reduces the likelihood of accidental slips and ensures safe usage.
- Lighting: Proper illumination is a must for accurate work. Poor lighting can lead to mistakes and mishaps, specifically when handling sharp and rotational objects.
Good work habits and attention to the space world around you assist greatly during projects. Remember that taking the time to prepare your workspace and adopting safety measures builds a strong foundation for a successful jewelry-making experience with a Dremel.
Taking these safety measures can not only protect you but also enhance your craft by allowing you to focus.
Tips for Beginners in Jewelry Making
Starting in jewelry making can feel daunting yet also rewarding. Understanding fundamental aspects allows newcomers to cultivate their creative expression and skills. With a Dremel tool, this transition can be smmoth, promoting experimentation.
Project Ideas for New Crafters
As beginners, knowing what projects to undertake is crucial. Simple designs help build confidence while refining techniques. Here are some approachable ideas to initiate your crafting journey:
- Wire Wrapped Rings: An easy starter project that focuses on shaping wire. You can combine different colors or materials to personalize it.
- Leather Pendant Necklaces: Cutting shapes from sapi leather is possible with a Dremel tool. It's a straightforward approach, emphasizing the style's versatility.
- Beaded Bracelets: Combine various beads and clasps for a custom piece. This project emphasizes balancing creativity with dexterity.
Choosing the right project is vital for maintaining interest. Successful completion leads to encouragement for further experimentation.
Common Mistakes to Avoid
Mistakes prepare every crafter for growth. Learning from them ensures smoother experiences in future projects. Here are some common pitfalls to be mindful of:
- Rushing the Process: Patience always proves valuable in jewelry making. Dremel tools can make tasks quick, but haste may result in imprecision.
- Neglecting Safety: Minus proper gear, working with tools can be risky. Always wear safety goggles and masks to protect against dust and fragments.
- Using Incorrect Accessories: Different tasks require specific attachments. Using wrong discs or bits might lead to errors in your work or can damage the materials.
Remember that jewelry making evolves with experience. Avoiding these mistakes contributes to personal accountability in the learning process. Each step you take enhances your understanding of both craftsmanship and creativity while utilizing a Dremel tool.
Advanced Techniques in Jewelry Making with Dremel
Advanced techniques in jewelry making using a Dremel tool can open up numerous creative pathways for artisans. When jewelers opt for a Dremel, they harness enhanced precision and flexibility. This reinforces both the craftsmanship and artistic expression found in each piece. Advanced techniques not only elevate the final design but also allow makers to experiment and innovate.
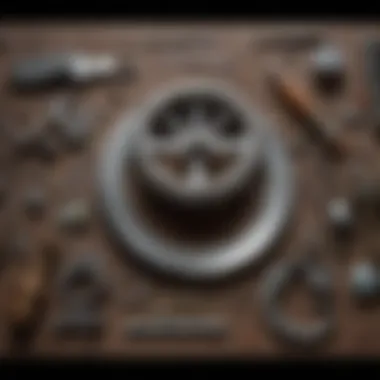
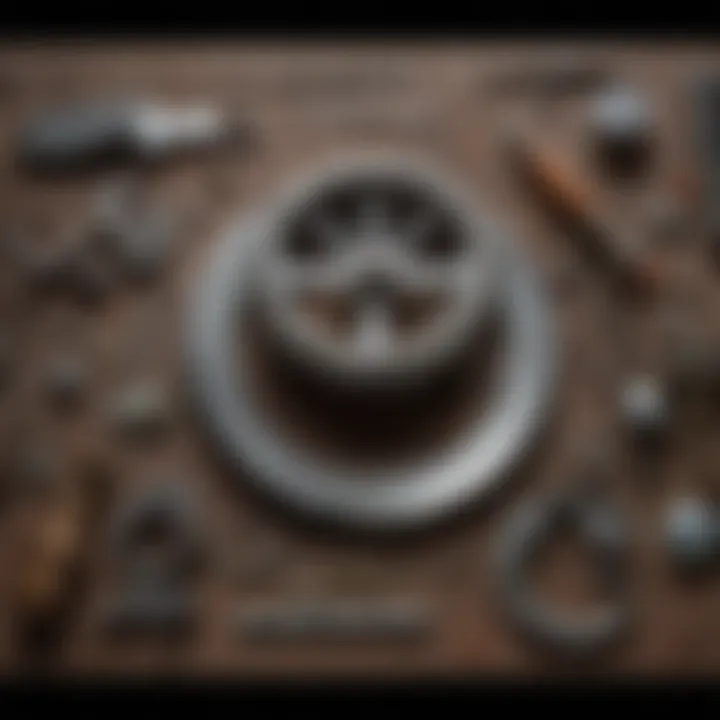
The enhancement of design possibilities can lead to unique jewelry creations that truly reflect individual style. Using Dremel tools means jewelers must consider the various applications that arise from molding, combining, and manipulating materials. This section will delve into these concepts in more depth, examining why mastering advanced techniques can significantly influence the quality and originality of jewelry.
Combining Materials
Combining different materials utilizing a Dremel tool opens up exciting options for jewelry makers. Many jewelers create pieces from metals alongside organic materials like wood or stone. With the Dremel's power, one can drill, sand, and polish these diverse materials to create harmonious pieces. The Dremel enables precise actions, which pushes the boundaries of creativity.
When working with mixed media, it is crucial to understand the characteristics of each material. For instance:
- Metal often needs a specific Dremel bit to achieve the desired effect.
- Wood may require a gentler touch to avoid demolishing its grain.
Looking at vital safety considerations, it's also advisable to ensure that incompatible materials are used appropriately to avoid damage or mechanical failures during crafting.
There exist particular tools and bits optimized for challenging combinations, such as diamond-coated bits for hard materials. When these pieces are finished, it can truly create awe-inspiring results. In the realm of combining materials, patience and practice will lead to progressive mastery over time.
Creating Intricate Designs
Creating intricate designs with a Dremel tool turns conventional jewelry making into a platform for breathtaking artistry. Jewelers can utilize various bits and attachments to engrave detailed patterns, replicate nature-inspired shapes, or even craft elaborate artwork on smaller surfaces. Such complexity brings sophistication to every item crafted.
For intricate designs, the following factors should be emphasized:
- Dremel Bits: Selecting the right bit is vital. Fine tips maximize detail.
- Speed Control: Slower speeds may enhance precision during intricate carving.
The results are often nothing short of artistry in its highest form. There’s no question that integrating advanced techniques impacts the final piece significantly. The ability to create lucrative designs establishes a clear distinction between everyday jewelry and extraordinary. Clearly, mastery over Dremel tool capabilities leads to those standout creations which resonate values in design, craftsmanship, and personal touch.
Mastery of advanced Dremel techniques in jewelry making speaks to depth of creativity and brings unique designs to life.
Resources for Continued Learning
Continued learning serves as the cornerstone for any craft, including jewelry making. As technology and techniques evolve, staying up-to-date ensures that enthusiasts can refine their skills and expand their creative capabilities. This section underscores the significance of accessible resources that contribute not only to practical skill development but also to a deeper understanding of the art and science behind jewelry making. Here are essential elements to consider:
- Broaden Skillset: Engaging with various learning platforms introduces new methods and tools that can significantly enhance the creative process.
- Explore the Modern Techniques: Continued education allows jewelers to integrate innovative techniques. Knowledge of advancements can make a difference in design and execution.
- Authentic Feedback: Courses, workshops, and engaging with the community presents opportunities for constructive critique. Peer feedback is invaluable.
These resources cater to all levels of expertise, ensuring that newcomers and seasoned artisans alike find something of value.
Online Courses and Workshops
Online platforms provide a space to learn at your pace. Therefore, enthusiasts can find courses specifically aimed at skills relevant to using the Dremel tool in jewelry making. For example, platforms like Udemy, Craftsy, and Skillshare offer insights from established professionals. These courses cover several key areas, including:
- Live Practice and Demonstration: Participants benefit from real-time projects and live demonstrations, fostering a hands-on understanding of techniques.
- Focus on Specific Tools: Some courses even provide targeted training on using the Dremel, elucidating advanced techniques that heighten proficiency and creativity.
- Community Interaction: Engaging with fellows through forums and discussion boards during the course supports exchange of ideas, tips regarding product usage, and advises on tackling challenges.
Books and Publications on Jewelry Making
Various books and publications are also excellent resources for deepening your knowledge in jewelry making. They often explore topics from fundamental techniques to complex design principles.
- Comprehensive Guides: Many well-regarded texts offer a holistic approach, integrating both theoretical knowledge and practical applications.
- Step-by-Step Tutorials: Publications often break down techniques for Dremel use in accessible sections, making for easy comprehension and application in practice.
- Inspiration and Designs: Books can serve as a valuable source of inspiration, featuring pictures and blueprints that spark creativity love to whosoever delve into them.
Choosing to engage with these resources demonstrates a commitment to evolving in one’s craft. Investing time into continued learning sets the stage for success in jewelry making. This dedication contributes greatly to potential mastery over tools like the Dremel, ultimately enriching one’s portfolio and artistic voice.
Epilogue
The significance of the conclusion in any article cannot be underestimated. It serves as a capstone, encapsulating the core messages while reflecting on the journey covered throughout the text. In the context of jewelry making using a Dremel tool, the conclusion draws attention to key insights and takeaways that help readers digest the valuable information shared earlier.
As technology continues to evolve, so does the jewelry making craft. Embracing the innovations found in tools like the Dremel allows artisans and hobbyists to expand their creative horizons significantly. The perfect fusion of precision and versatility in this tool not only simplifies various processes but also leads to the possibility of intricate designs that were once time-consuming and challenging.
In reviewing the information presented within this comprehensive guide, it becomes clear that acquiring a Dremel tool can profoundly affect one's crafting capabilities. This versatility, whether it involves cutting, sanding, engraving, or polishing, provides a platform to explore unlimited creative boundaries.
Moreover, adhering to safety measures ensures an enjoyable and harm-free experience, thus promoting engagement rather than frustration. As the concept of crafting evolves through digital resources and community interactions, beginners and veterans alike can harness newfound skills.
The future of jewelry making is closely tied to the adaptation of modern tools, empowering artisans to execute high-quality craftsmanship.
In summary, reflecting on your new skills with Dremel tools will encourage continuous growth as you integrate new techniques and methodologies from the detailed content provided. Thus, one step forward into incorporating contemporary options and views lays down the path to becoming a proficient jeweler.
The Future of Jewelry Making with Technology
The landscape of jewelry making is experiencing a profound transformation with the integration of technology. The adoption of precise tools like the Dremel is now commonplace among silversmiths, beaders, and general crafters. The ability to manipulate materials effectively and accurately is enhanced through technology, bringing uniqueness to an artisan's product.
In practical terms, the consideration of digital crafting will likely enhance the creativity and diversity of jewelry. Using CAD (Computer-Aided Design) software facilitates the designing of custom pieces before physically creating them. This modern method allows crafters to envision their designs precisely, which can lead to better outcomes when finally making pieces with tools like the Dremel.
Social media platforms provide venues to share and develop ideas among artists across the globe. Communities fostered online facilitate discussions that educate users about trends, techniques, and tools tailored to modern interest.
To ensure a competitive edge, particularly among professional jewelers, maintaining liaison activities not only keeps them updated but also improves their adaptability to advancing software and tools.
Final Thoughts on Utilizing Dremel in Jewelry Craft
In summation, the Dremel tool is critical for effective jewelry making. It opens possibilities for efficiency, dimension, and personalization in the creation process, leading to unique pieces that appeal to consumers or collectors alike. Beginners are encouraged to recognize the importance of practice while armed with these tools. Early trials may be challenging, but mastery occurs not without effort.
Beyond mere functionality, the act of using Dremel encourages exploration and oftentimes results in unexpected yet attractive designs that can overpass traditional jewelry making boundaries. Suppose someone's skill might be initially focused on simple earrings or rings. In that case, opportunity presents itself to expand into more complex types as they grow more comfortable using Dremel tools.
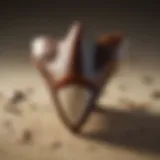
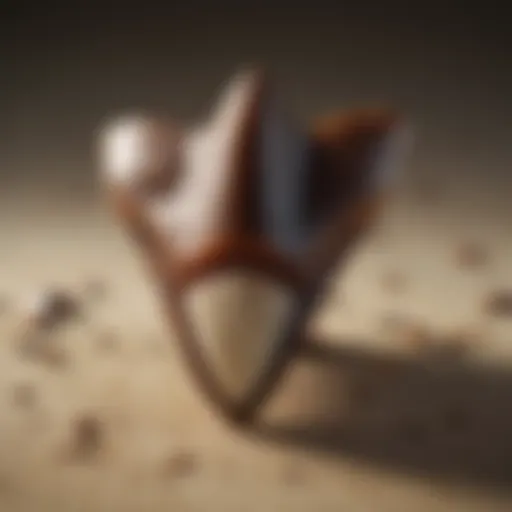