Exploring the Revolutionary Rock Cutting Machine: A Comprehensive Guide
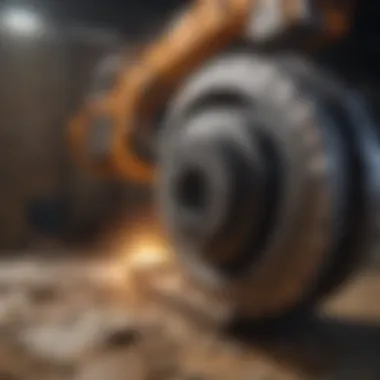
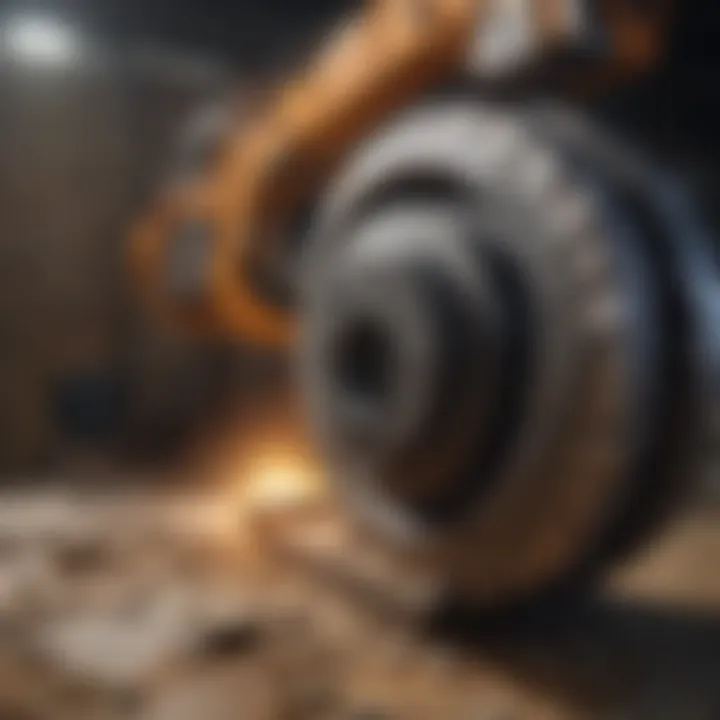
Rock and Fossil Identification
Understanding rocks and fossils is essential for any enthusiast in the field of geology. Rocks come in various types, including sedimentary, igneous, and metamorphic, each with distinct characteristics that indicate their formation process and composition. Fossils, on the other hand, are remnants of ancient life preserved in rocks over millions of years. When identifying rocks, collectors must examine factors such as color, texture, mineral composition, and any visible patterns or structures. Tools like magnifying glasses, hardness picks, and streak plates aid in this process, allowing for a more accurate identification of specimens.
Collecting Tips and Techniques
Successful rock and fossil collecting requires a combination of knowledge, patience, and practical skills. Enthusiasts should research prime collecting sites based on the types of rocks or fossils they wish to find, as different regions may yield varying specimens. When on-site, it is essential to practice ethical collecting by following regulations and respecting the environment. Safely extracting specimens involves using appropriate tools, such as chisels, rock hammers, and brushes, to avoid damaging the samples and surrounding area. Additionally, keeping detailed records of where and when each specimen was found enhances their scientific value and historical significance.
Preservation and Display
Preserving rocks and fossils ensures their longevity and protects them from degradation over time. Techniques like cleaning with gentle brushes, consolidating fragile specimens with adhesives, and storing in acid-free containers aid in preservation efforts. Proper storage methods involve keeping specimens away from sunlight, moisture, and fluctuating temperatures to prevent deterioration. When displaying collected rocks and fossils, collectors can showcase them in custom-made cabinets, shadow boxes, or museum-style mounts to highlight their beauty and uniqueness. Creative display ideas, such as thematic arrangements based on geological eras or color schemes, add aesthetic appeal to collections.
Geological Insights
Delving into the geological aspects of rocks and fossils provides a deeper understanding of Earth's history and evolution. By studying geological formations and processes, enthusiasts can unravel the environmental conditions that shaped landscapes and preserved ancient life. Rocks and fossils hold historical significance, offering clues to past ecosystems and evolutionary patterns. Notable discoveries in the field have contributed to scientific knowledge, revealing new species, extinct organisms, and geological events that have shaped the planet's geological record.
Introduction
The world of innovative rock cutting machines stands at the forefront of technological advancements in the field of geology and exploration. In this comprehensive guide, we delve deep into the intricacies of rock cutting machines, shedding light on their significance, functionalities, and profound impact on various industries. From enhancing operational efficiency to enabling precise rock extraction, these machines play a pivotal role in modern-day geological endeavors. By unraveling the evolution and application of cutting-edge technologies, readers will gain a comprehensive understanding of how these machines have revolutionized the way we interact with rocks and minerals.
Overview of Rock Cutting Machine
Definition and Purpose
The definition and purpose of rock cutting machines constitute the cornerstone of their utility in various industries. These machines are specifically designed to slice through tough rock formations with precision and efficiency, facilitating diverse operations ranging from mining to excavation. The key characteristic of these machines lies in their ability to leverage advanced cutting tools such as diamond blades and carbide inserts, ensuring swift and accurate rock fragmentation. Despite their complexity, these machines offer a seamless solution for industries requiring precise rock processing, making them a popular choice in this domain. Their unique feature of delivering tailored cutting solutions contributes significantly to the operational success of geological projects, albeit with challenges such as high maintenance costs and operational complexities.
Evolution of Cutting Technologies
The evolution of cutting technologies marks a transformative journey from rudimentary manual techniques to sophisticated mechanical devices. Early rock cutting methods relied on manual labor and basic tools to extract rocks, highlighting the endurance and skill required in the process. Subsequent advancements introduced mechanized cutting machines that revolutionized the mining industry by enhancing productivity and precision. These machines not only streamlined excavation processes but also boosted efficiency, giving rise to a new era of rock cutting technology. Despite their advantages in expediting operations, mechanized cutting machines posed challenges in terms of maintenance and initial investment. However, their pivotal role in shaping modern industrial practices solidifies their position as an essential asset in the realm of rock cutting technology.
Technological Evolution
In the realm of rock cutting machines, the concept of technological evolution stands as a cornerstone, shaping the course of advancements and innovations within the industry. As technology progresses, the methods and tools used for cutting rocks have undergone significant transformations, leading to increased efficiency, precision, and safety in rock-related operations. Understanding the historical context and evolution of these technologies provides invaluable insights into the current state of rock cutting machines and their future trajectory.
The topic of technological evolution in this article delves into the evolutionary journey of rock cutting methods, from manual techniques to sophisticated mechanized systems. By exploring this progression, readers will grasp the fundamental shifts that have occurred over time, driving the industry towards greater productivity and effectiveness. Moreover, highlighting the benefits and considerations of technological evolution offers a comprehensive overview of the challenges and opportunities associated with embracing new cutting technologies.

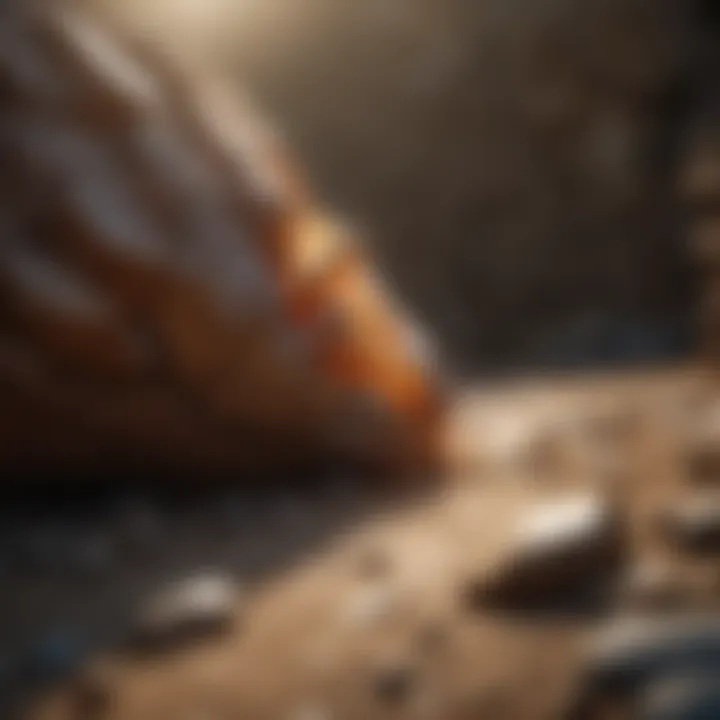
Early Rock Cutting Methods
Manual Techniques
Manual techniques have played a pivotal role in the history of rock cutting, serving as the foundation upon which modern cutting methods have been developed. The manual approach involves labor-intensive processes where operators use handheld tools to carve and shape rocks. Despite its conventional nature, manual techniques remain relevant in certain contexts due to their precision and adaptability to intricate cutting tasks.
One key characteristic of manual techniques is the tactile feedback and direct control they provide to operators, allowing for nuanced adjustments and fine detailing during cutting processes. This hands-on approach fosters a sense of craftsmanship and expertise that is often valued in artisanal rock cutting projects. However, the main disadvantage of manual techniques lies in their slower pace and limited capacity when dealing with large-scale rock cutting operations, making them less efficient for industrial purposes.
Mechanical Devices
In contrast to manual techniques, mechanical devices represent a leap forward in the evolution of rock cutting methods, introducing motorized tools and equipment to enhance cutting capabilities. These devices leverage mechanical power to achieve faster cutting speeds and higher levels of consistency compared to manual methods. The integration of mechanical devices has revolutionized the efficiency and precision of rock cutting processes, paving the way for increased productivity and reduced manual labor.
The key characteristic of mechanical devices lies in their ability to automate repetitive tasks and handle heavy workloads with minimal human intervention. This feature makes them ideal for industrial applications where speed and accuracy are paramount. However, one potential disadvantage of mechanical devices is the reliance on power sources, which can limit their portability and accessibility in remote or off-grid locations.
Introduction of Mechanized Cutting Machines
Impact on Mining Industry
The introduction of mechanized cutting machines has had a profound impact on the mining industry, redefining the standards of efficiency and safety in rock excavation processes. These machines offer unparalleled cutting power and precision, enabling mining operations to extract ores and minerals with greater speed and resource utilization. The adoption of mechanized cutting machines has not only streamlined mining operations but also elevated safety standards by reducing manual labor and exposure to hazardous environments.
The key characteristic of mechanized cutting machines lies in their ability to operate in challenging mining environments with minimal human supervision, enhancing overall productivity and operational efficiency. This attribute makes them a popular choice for mining companies looking to optimize their extraction processes and maximize resource recovery. Despite their advantages, mechanized cutting machines may face limitations in terms of initial investment costs and maintenance requirements, which could pose challenges for smaller mining operations.
Enhanced Efficiency
Enhanced efficiency stands as a defining feature of mechanized cutting machines, offering unprecedented levels of productivity and precision in rock cutting operations. By integrating advanced technologies and automation systems, these machines can achieve consistent cutting performance across varying rock types and conditions. The enhanced efficiency brought about by mechanized cutting machines not only accelerates rock extraction processes but also reduces operational costs and environmental impact.
The key characteristic of enhanced efficiency in mechanized cutting machines is their ability to optimize cutting parameters and adapt to changing geological conditions in real time. This dynamic adaptability allows operators to achieve higher yields and better quality outputs while minimizing waste and rework. However, challenges related to system complexity and operator training may arise when implementing these advanced machines, requiring careful planning and investment in skill development.
Key Components and Mechanisms
Rock cutting machines are intricate systems comprising various vital parts that work together seamlessly to achieve efficient rock processing and extraction. Among these components, blades and cutting tools play a pivotal role in the overall functionality and performance of the machine. These components are crucial for ensuring precision, speed, and effectiveness in cutting through different types of rocks and materials. Understanding the significance of blades and cutting tools is essential for anyone involved in the operation or maintenance of rock cutting equipment. It is essential to consider factors such as material composition, blade sharpness, and durability when selecting the appropriate tools for specific cutting tasks.
Blades and Cutting Tools
Diamond Blades
Diamond blades are renowned for their exceptional hardness and durability, making them a popular choice for rock cutting applications. The key characteristic of diamond blades lies in their ability to maintain sharpness over an extended period, resulting in precise and efficient cutting. Their unique feature stems from the embedded diamond particles on the cutting edge, ensuring enhanced cutting performance and longevity. While diamond blades offer unparalleled cutting precision and longevity, they can be relatively expensive compared to other blade materials. However, the superior cutting quality and reduced maintenance costs associated with diamond blades make them a valuable investment for rock cutting machines.
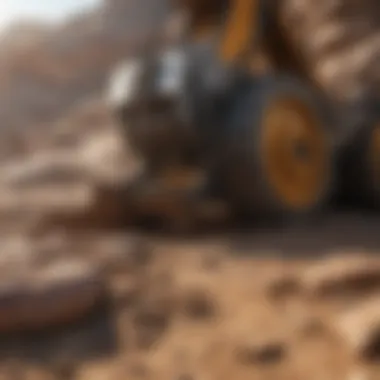
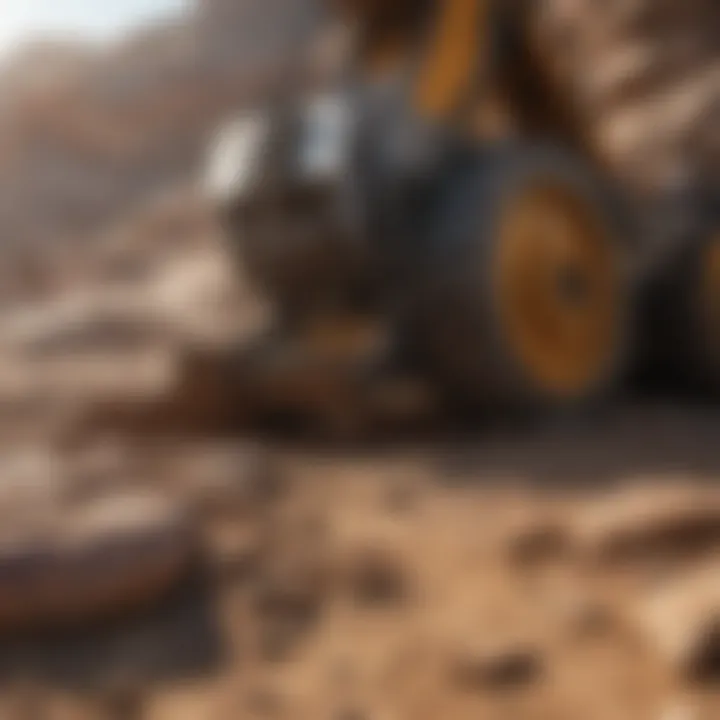
Carbide Inserts
Carbide inserts are another crucial component in rock cutting machines, prized for their hardness and wear resistance. The key characteristic of carbide inserts is their ability to withstand high temperatures and maintain sharp cutting edges even under challenging conditions. This makes them a popular choice for cutting through tough rocks and abrasive materials efficiently. The unique feature of carbide inserts lies in their versatility and longevity, providing reliable cutting performance across various rock types and environments. While carbide inserts offer exceptional durability and cutting efficiency, they may require periodic replacement due to wear over time. Despite this, their overall cost-effectiveness and high performance make them indispensable components in rock cutting machinery.
Applications in Geology
In the realm of geology, the applications of rock cutting machines are crucial for various operations related to mining and excavation. These innovative machines play a fundamental role in the extraction and processing of rocks, offering efficiency and precision in diverse geological tasks. From uncovering valuable ores to facilitating quarrying operations, rock cutting machines have become indispensable tools in the field of geology.
Mining and Excavation
Extraction of Ores
The extraction of ores is a critical aspect of mining operations, and rock cutting machines revolutionize this process by enhancing speed and accuracy. These machines utilize advanced cutting technologies to extract ores with precision, minimizing waste and maximizing output. The key characteristic of ore extraction with rock cutting machines is the ability to dissect mineral-rich rocks efficiently, leading to increased productivity in mining activities. This method is a popular choice for its ability to extract ores from challenging geological formations effectively. One unique feature of utilizing rock cutting machines for ore extraction is the reduced environmental impact compared to traditional mining methods. While the advantages of ore extraction through rock cutting machines include higher productivity and resource optimization, a potential disadvantage lies in the initial investment required for acquiring and maintaining these sophisticated machines.
Quarrying Operations
Quarrying operations involve the extraction of natural stone resources for construction and ornamentation purposes, where rock cutting machines significantly streamline the quarrying process. These machines are instrumental in cutting through dense rock formations to obtain desired stone blocks or materials. The key characteristic of utilizing rock cutting machines in quarrying is their ability to ensure precise cuts, resulting in high-quality stone products. This choice is beneficial for quarrying operations due to the efficiency and precision these machines offer, leading to increased productivity and reduced labor intensity. One unique feature of employing rock cutting machines in quarrying is the minimization of material waste during the extraction process. While the advantages of using rock cutting machines for quarrying operations include improved efficiency and product quality, a potential disadvantage is the need for skilled operators to operate and maintain these complex machines effectively.
Innovations and Advancements
In the realm of rock cutting machines, the segment of Innovations and Advancements plays a pivotal role in reshaping the landscape of rock extraction and processing. This section delves into the cutting-edge advancements that are driving the industry forward, enhancing efficiency, precision, and safety measures. By exploring the latest innovations, readers will gain a profound insight into how technology is revolutionizing the traditional methods of rock cutting. The focus here is on highlighting the key technological breakthroughs and their implications for the geology and exploration domains.
Automation and Robotics
Integration of AI
The Integration of Artificial Intelligence (AI) stands at the forefront of advancements in rock cutting machines. Through the incorporation of AI algorithms and machine learning capabilities, these machines can autonomously analyze data, optimize cutting processes, and adapt to varying geological conditions in real-time. This integration not only streamlines operations but also augments productivity and precision in rock cutting processes. The predictive analytics enabled by AI offer a proactive approach to maintenance, ensuring minimal downtime and efficient resource utilization. The ability of AI to learn from patterns and continuously improve the cutting performance sets a new standard for operational excellence in the field of rock cutting.
Remote Operation
Remote Operation represents a paradigm shift in the way rock cutting machines are controlled and monitored. By enabling operators to oversee and manage these machines from a remote location, it enhances safety measures by reducing direct human interaction in hazardous environments. The key characteristic of Remote Operation lies in its capacity to enhance operational flexibility and accessibility, particularly in challenging terrains or underground mining settings. The real-time monitoring and control features empower operators with a comprehensive view of the cutting process, allowing for immediate adjustments and optimizations as needed. While the advantages of Remote Operation include increased safety and operational efficiency, challenges such as connectivity issues and latency issues may arise, necessitating robust solutions for seamless remote operations in this context.
Environmental Impact
Rock cutting machines play a vital role not only in the efficiency of mining operations but also in their environmental impact. Understanding the significance of environmental considerations in this article is crucial for gaining insights into how modern industrial processes can strive towards sustainability. By delving into the environmental impact of rock cutting machines, we can highlight key elements that drive this sector's evolution towards more eco-friendly practices.
Efficiency and Sustainability
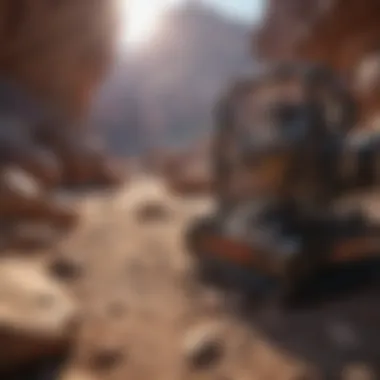
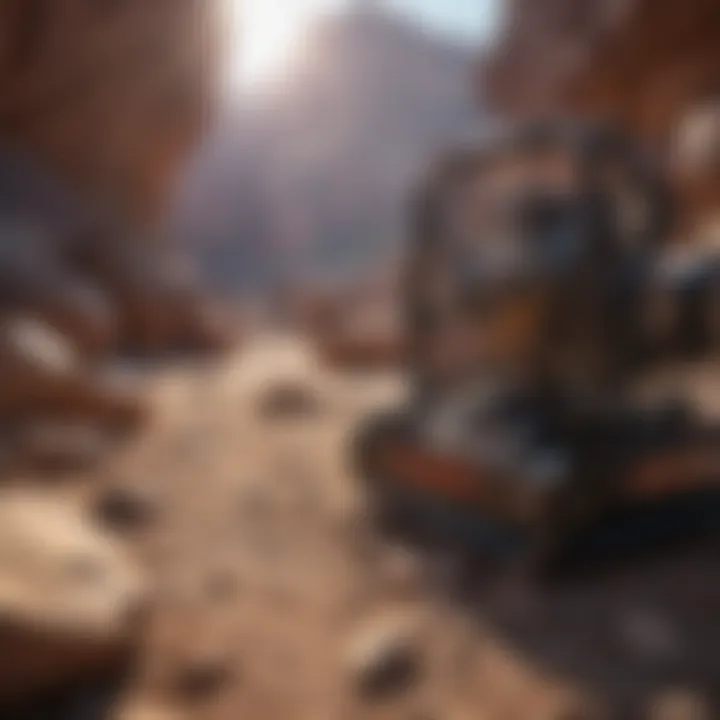
Reduced Waste Generation
Reduced waste generation stands out as a pivotal aspect of environmental conservation in rock cutting processes. This practice involves optimizing operations to minimize leftover materials and enhance resource efficiency. The key characteristic of reduced waste generation lies in its ability to streamline production processes while minimizing environmental footprint. Its advantage in this context lies in efficiently utilizing raw materials and reducing unnecessary waste, contributing to overall sustainability objectives.
Energy-Efficient Models
The adoption of energy-efficient models in rock cutting machines is a game-changer in improving sustainability within the industry. These models prioritize energy conservation through advanced technologies and design elements. The key characteristic of energy-efficient models is their ability to lower energy consumption without compromising operational effectiveness. Choosing energy-efficient models for rock cutting applications proves beneficial by reducing carbon emissions and operational costs. While these models offer significant advantages in lowering environmental impact, it is essential to consider potential trade-offs in terms of upfront costs and performance optimization.
Challenges and Mitigation
Noise and Vibration
Mitigating noise and vibration levels is essential to ensure the well-being of workers and surrounding communities in rock cutting operations. The key characteristic of addressing noise and vibration issues lies in adopting noise reduction technologies and vibration damping mechanisms to minimize disturbances. While these practices are crucial for creating a healthier work environment and reducing community impact, they may pose challenges in terms of operational costs and equipment modifications.
Erosion Control
Erosion control techniques play a vital role in preserving land integrity during mining and excavation activities. The key characteristic of erosion control measures is their ability to prevent soil loss and maintain landscape stability. Implementing erosion control strategies is a popular choice in rock cutting applications due to their contribution to environmental conservation and sustainable land use. However, challenges may arise concerning the implementation of erosion control measures, such as the need for ongoing monitoring and maintenance requirements.
Future Prospects
In a constantly evolving industry like rock cutting machines, exploring future prospects is crucial. This section delves into the potential advancements that could shape the future landscape of rock cutting technology. By analyzing upcoming trends and innovations, this article sheds light on the transformative changes that could enhance efficiency and sustainability in rock cutting processes.
Integration of Cutting-edge Technologies
Nanotechnology Applications
Nanotechnology applications hold immense promise for the future of rock cutting machines. Their ability to manipulate materials at the nanoscale level enables precise cutting and increased durability of tools. Nanotechnology applications play a pivotal role in enhancing the performance and longevity of cutting blades, contributing to reduced maintenance costs and enhanced cutting efficiency. Despite their small size, nanomaterials exhibit exceptional strength and hardness, making them a popular choice for improving the wear resistance of cutting tools in the rock cutting industry.
Predictive Maintenance Systems
Predictive maintenance systems offer a proactive approach to equipment maintenance, predicting potential failures before they occur. By leveraging data analytics and machine learning algorithms, these systems can forecast maintenance needs based on equipment usage and performance metrics. This predictive capability minimizes downtime, improves operational efficiency, and reduces overall maintenance costs. The unique feature of predictive maintenance systems lies in their ability to optimize maintenance schedules, ensuring that maintenance activities are carried out precisely when needed, preventing unexpected breakdowns and prolonging the lifespan of cutting machines.
Global Industry Trends
The global industry trends surrounding rock cutting machines provide valuable insights into the future trajectory of the industry. By examining market growth forecasts and innovative research initiatives, this section showcases the potential opportunities and challenges that lie ahead.
Market Growth Forecast
Market growth forecasts play a pivotal role in guiding strategic decisions within the rock cutting industry. They offer projections on market demand, emerging technologies, and competitive landscapes, allowing industry players to adapt and innovate effectively. The unique feature of market growth forecasts is their predictive nature, providing stakeholders with foresight into potential market developments and opportunities for growth. By leveraging market growth forecasts, companies can align their business strategies to capitalize on emerging trends and stay ahead of the competition.
Innovative Research Initiatives
Innovative research initiatives drive the exploration of cutting-edge technologies and methodologies in rock cutting machines. These initiatives focus on pushing the boundaries of current capabilities, fostering creativity and innovation within the industry. The key characteristic of innovative research initiatives is their ability to inspire new approaches to rock cutting challenges, leading to breakthrough solutions and improved operational outcomes. By promoting collaboration and knowledge exchange, innovative research initiatives pave the way for enhanced efficiency, sustainability, and performance in rock cutting technologies.