Exploring Rock Lapidary Equipment for Enthusiasts
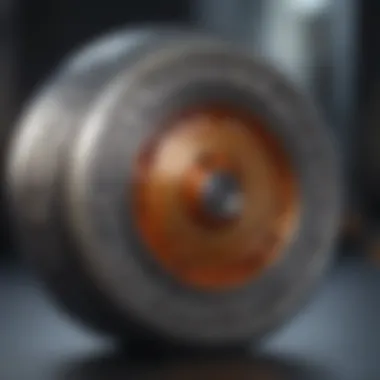
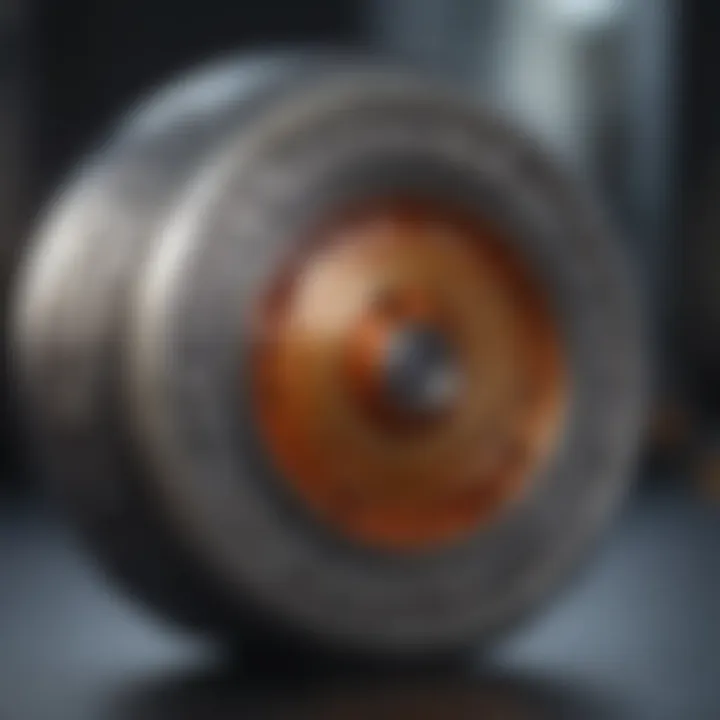
Intro
In the realm of rock collecting, having the right lapidary equipment makes all the difference. Whether you're just getting your feet wet in the hobby or you're a seasoned pro, understanding these tools shears back the mystery that often enshrouds the art of gem cutting and stone polishing. From precision saws to polishing pads, this guide will peel back the layers, diving into the nuances of lapidary work.
By the end, you’ll not only know the essential tools but also understand how to maintain them properly and select which ones will best suit your needs. Safety measures, cost considerations, best practices, and an array of techniques will round out our discussion, ultimately paving the way for you to elevate your craftsmanship to new heights. Let’s kick off our exploration by delving into the world of rock and fossil identification.
Rock and Fossil Identification
Identifying rocks and fossils is a cornerstone of lapidary work. Understanding their characteristics not only helps you during the collection process but also guides your choices when it comes to specialized lapidary tools.
Types of Rocks and Fossils
The world of geology is vast, and rocks can be broadly categorized into three main types:
- Igneous Rocks - Formed from cooled magma or lava. Examples include granite and basalt.
- Sedimentary Rocks - Created from particles or organic material that compact over time, such as sandstone or limestone.
- Metamorphic Rocks - Rocks that have transformed under pressure and heat. Marble and schist fall into this category.
Fossils, on the other hand, provide glimpses into Earth's history, showing what life was like millennia ago. Common fossil types include:
- Trace Fossils - Evidence of activity, like footprints.
- Body Fossils - Actual remains, such as bones or shells.
Characteristics to Look For
When sifting through your finds, pay attention to:
- Color and Texture - These can vary greatly within the same type of rock, giving clues about the environment where they formed.
- Hardness - A simple scratch test can help you understand a rock's durability, guiding you on how to cut or polish it.
- Layering - Visible layers in sedimentary rocks can help identify their origin and age.
Tools for Identification
Having the right tools makes identification much easier:
- Hand Lens - A magnifier that reveals details invisible to the naked eye.
- Rock Hammer - For breaking rocks and revealing their inner beauty.
- Field Guide - A reliable book or digital resource that provides info on various rocks and fossils.
"Knowing your materials gives you a leg up in crafting something extraordinary."
Collecting Tips and Techniques
Armed with knowledge about rock and fossil identification, it's time to talk about collecting techniques. It's not just about finding; it's about finding wisely.
Best Practices for Collecting
A few tips can make your collecting expeditions more fruitful:
- Always carry a sturdy backpack. It keeps your tools and finds safe.
- Respect nature. Stick to established trails to minimize your impact.
- Seek permission when collecting on private land.
Locating Prime Collecting Sites
Not all places are ripe for collecting. Research local geological maps, join rock hounding forums on platforms like Reddit and ask seasoned collectors for their insights.
- Quarries - Often rich with diverse specimens.
- Riverbeds - Erosion exposes ancient treasures.
- Roadcuts - The ground's been disturbed, opening a view into layers.
How to Safely Extract Specimens
When digging into the earth for your next prize, safety should always come first. Use protective gear like gloves and goggles, and take care to avoid loose rocks that can fall.
Preservation and Display
After collecting, preserving and displaying your rocks and fossils properly can enhance their value and longevity.
Techniques for Preserving Rocks and Fossils
To ensure your finds last a lifetime, consider:
- Wax Coating - A thin layer of wax can seal moisture and give a shine.
- Resin Applications - Use epoxy or resin for fragile specimens to prevent breakage.
Proper Storage Methods
- Dry and Cool Environment - Store in a place free from humidity to prevent deteriorations.
- Protective Cases - Utilize boxes or cases to guard against dust and accidental damage.
Creative Display Ideas
- Arrange them in shadow boxes, showcasing your collection like a museum exhibit.
- Use stands to elevate samples on a shelf or table, allowing light to bring out their colors.
Geological Insights
The study of rocks goes beyond just aesthetics. Geological insights inform not just the history of the Earth but also the makeup of materials we work with.
Geological Formations and Processes
Understanding how different rocks are formed provides insight into their potential uses in lapidary work.
- Igneous Processes - Formations from the Earth's mantle can yield stunning gems.
- Metamorphic Changes - Reveal strength, making some stones ideal for intricate carvings.
Historical Significance of Rocks and Fossils
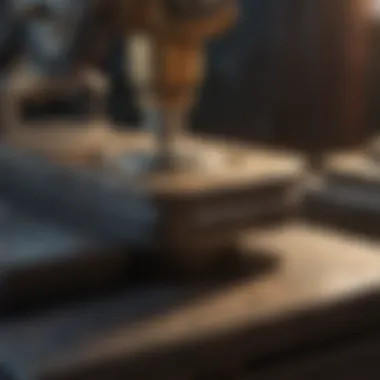
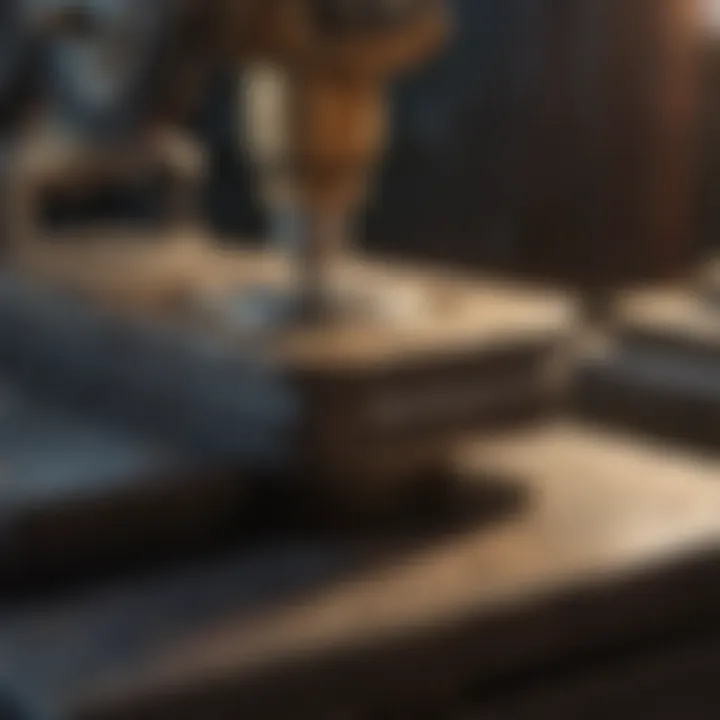
Each type of rock or fossil tells a story from Earth’s past. This can connect collectors to the geological history of their local areas.
Notable Discoveries in the Field
Stay updated on findings through scientific journals or community discussions. Sites like Britannica often have articles on recent discoveries that can enrich your knowledge and inform your own collecting practices.
Preamble to Lapidary Equipment
In the world of gem cutting and stone polishing, the significance of lapidary equipment cannot be overstated. This toolkit is the lifeblood of lapidary art, empowering both novices and seasoned collectors to transform rough stones into stunning gems. Understanding this equipment is crucial—not just for practical purposes but also for enhancing one’s creative expression when working with rocks.
Lapidary equipment serves a specific purpose: to facilitate the processes involved in shaping and refining stone materials. Each piece of equipment, from saws to polishers, plays a role in this intricate art form, enabling artisans to achieve precision and creativity in their work.
One of the critical aspects of engaging in lapidary work is the choice of tools. Each type of equipment is designed with particular functions in mind, influencing both technique and results. A keen understanding of these tools can lead to better quality finishes and more efficient workflows, ultimately elevating the finished product.
Moreover, the evolution of lapidary equipment reflects advancements in technology and techniques. As new tools emerge, they offer greater efficiency and versatility, which can enrich the artistic process. This evolution enables artisans to explore more complex designs and achieve finer details, pushing the boundaries of what's possible in lapidary art.
Thus, becoming familiar with this equipment provides not just practical benefits, but also fosters a deeper connection to the art form itself.
Definition and Purpose of Lapidary Equipment
At its core, lapidary equipment encompasses a diverse range of tools and machinery utilized for the processing of stones and gems. The primary purpose here is straightforward: to cut, grind, and polish raw minerals into pieces suitable for jewelry, art, or collection. The breadth of lapidary equipment is vast, with each tool tailored to different stages of stone processing.
For instance, saws are essential for cutting large rock specimens into smaller, manageable pieces. Grinding machines follow, offering refinement by shaping edges and removing any rough surfaces. Finally, polishing tools are the pièce de résistance, responsible for giving stones their radiant and lustrous finish. Each piece of equipment is a cog in the machine that drives the lapidary process; understanding its specific function is vital to mastering craft.
Moreover, using the right lapidary equipment can significantly affect the outcome. Achieving a high-quality finish often relies on using tools that are not just appropriate, but also well-maintained. Therefore, an understanding of both the purpose of each tool and how to use them properly is essential for anyone looking to succeed in this field.
Historical Context and Evolution
The history of lapidary equipment is as ancient as the craft itself. From the prehistoric times when stones were simply chipped and shaped with rudimentary tools, to today’s sophisticated machinery, the evolution of lapidary tools reflects the growth of technology and artistic expression.
Historically, lapidaries utilized basic tools made from stone, bone, or wood. It was through painstaking labor and sheer ingenuity that early artisans managed to create stunning works from materials that many might pass by as mere rocks. Over time, as metallurgy advanced, tools began to incorporate metal blades and wheels, greatly enhancing their efficiency and effectiveness.
The 19th century ushered in a significant transformation with the introduction of powered equipment, allowing for higher production rates and more intricate designs. Today, we see a blend of traditional techniques and modern technology. This evolution not only showcases the artisan’s skills but also embodies the continuously developing nature of craftsmanship in lapidary work.
"Fans of lapidary art will recognize that while techniques and tools have changed, the passion for transforming rough stones into breathtaking works of art remains timeless."
Types of Lapidary Equipment
Understanding the different types of lapidary equipment is crucial for anyone interested in the art of stone cutting and polishing. Selecting the right tools can make a world of difference in both the quality of the work and the ease of the process. Each piece of equipment serves a unique purpose and holds various advantages that can enhance the experience of both novices and seasoned rock enthusiasts.
Sawing Tools
Types of Saws
When it comes to cutting stones, saws are foundational tools in a lapidary's arsenal. The most common types include diamond saws and wire saws. Diamond saws are favored for their efficiency in slicing through hard materials, such as agate or jade. Their key characteristic is their ability to cut with precision, which reduces the chances of chipping the stone. This makes diamond saws a popular choice among lapidaries who prioritize clean lines in their cuts.
On the other hand, wire saws offer flexibility that diamond saws can't match. They can navigate tighter curves, making them ideal for artists looking to create intricate shapes from their specimens. However, they may not provide the same level of power when dealing with tougher materials, leading some users to perceive them as less effective for larger stones. Ultimately, both types of saws have their place in a well-equipped lapidary workshop.
Choosing the Appropriate Saw
Selecting the proper saw is more than just a matter of preference; it involves understanding the specific needs of your project. Think about what type of stone you'll be working with. If you're focused on tougher varieties, a diamond saw will serve you best. Its durability allows for extended use, meaning you won't be frequently shopping for replacements.
However, for artists who enjoy various designs, a wire saw’s adaptability can be a real game changer. It's essential to note that while wire saws promote creativity, they require a more delicate hand and understanding of technique, as they can easily bend or break under improper use.
Grinding Machines
Belt Grinders
Belt grinders are a staple for smoothing and shaping stones after they've been cut. Their design typically features a continuous loop of abrasive material driven by a motor. One of the main draws of belt grinders is their versatility; they can handle a variety of materials, including softer stones like quartz and harder varieties like granite.
The speed at which you can grind is also crucial—faster speeds mean quicker results, but it's less forgiving if you apply too much pressure. This can lead to unwanted scratches, which necessitate a gentler touch. Additionally, there's an array of belts available with varying grades of grit, affording users precise control over the smoothness of the finish.
Wheel Grinders
Wheel grinders, meanwhile, consist of rigid disks or wheels coated with abrasive materials. They excel in achieving sharp edges and fine shapes on stones, making them invaluable for detailed lapidary work. One key characteristic of wheel grinders is their ability to maintain a consistent grinding surface, which can be a huge advantage when precision is paramount.
However, the downside is that they can produce more heat, which might contribute to thermal shock in some stones. This makes it critical to monitor the grinding process closely to ensure the stone can handle the applied pressure and speed. In short, while wheel grinders might offer an edge in terms of precision, they require careful handling to avoid damaging your pieces.
Polishing Tools
Polishing Pads
After grinding, the polishing stage comes next. Polishing pads are typically used in conjunction with polishing compounds to achieve a high gloss finish. They can be made from different materials, including felt and foam, each lending its own unique properties to the polishing process.
A key benefit to polishing pads is that they're quite versatile; you can easily switch out compounds to suit varying materials, allowing for a range of finishes from matte to glossy. However, it’s worth noting that the wrong pad can cause scratches or not polish effectively, so careful selection matters.
Rotary Polishers
Rotary polishers, on the flip side, are electrical tools that provide more power and efficiency. They can cover larger areas more quickly than pads alone, edging them closer to professional results in a shorter amount of time. Rotary polishers are especially beneficial for larger stones or slabs, where hand-polishing would be tedious and time-consuming.
That said, they require a steady hand and careful technique. Improper usage can lead to uneven surfaces or even potential damage to the stone. Thus, while rotary polishers can expedite the process, they come with their own set of risks that demand respect and caution.
Cabochon Making Equipment
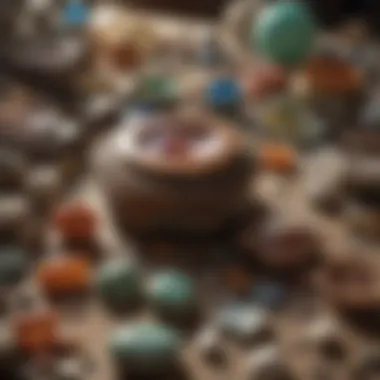
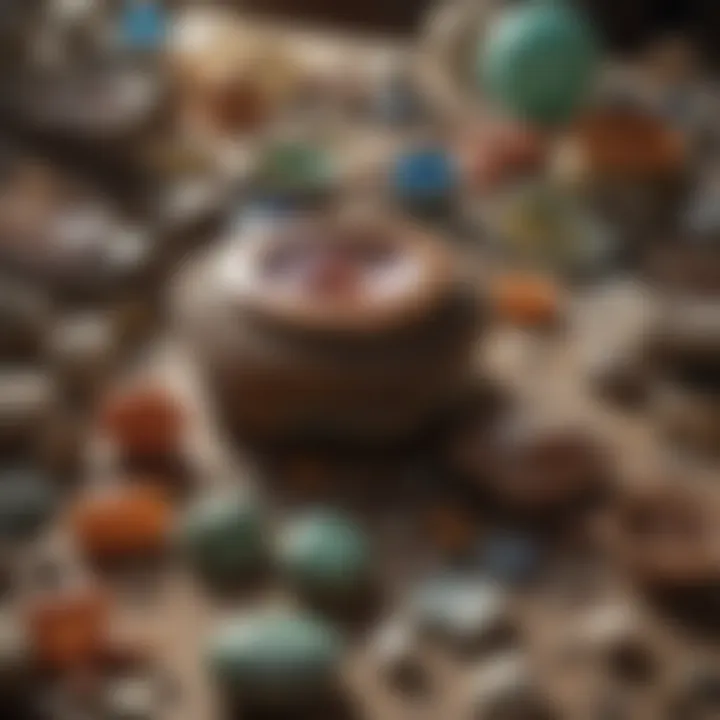
Specimens Suitable for Cabochons
When it comes to creating cabochons—polished, non-faceted gemstones—the choice of stone is critical. Some materials, like opal and lapis lazuli, are particularly well-suited due to their unique color patterns and hardness, which lend themselves to cabochon cutting. Specimens suitable for cabochons display both aesthetic beauty and the physical durability needed for shaping and polishing.
Choosing the right specimen not only impacts the final appearance but also the technical challenges you may face when shaping the stone. Softer materials may be easier to work with but could lose their integrity if not handled properly.
Technique Overview
A clear overview of the cabochon making technique is vital for anyone looking to delve into this delicate process. To begin, it often involves several steps—sawing, shaping, grinding, and finally polishing. Each step has its own nuances that must be navigated carefully to ensure a smooth finish.
Key characteristics of this technique include using progressive grits in your grinding process and ensuring consistency in your polishing strokes. It’s a labor of love that requires patience but can yield some breathtaking results. The sheer joy of transforming a rough stone into a glossy cabochon makes all the effort worthwhile, solidifying the importance of mastering the craft.
“Investing in the right equipment is like having a good map—a tool that guides your journey in the lapidary world.”
In summary, understanding the types of lapidary equipment not only enhances your ability to work skillfully with stones but also lets you appreciate the finer aspects of this serene craft. Each tool, whether it be a saw, grinder, or polisher, holds the potential to elevate your craftsmanship to new heights.
Essential Safety Equipment
When it comes to lapidary work, safety shouldn't be tossed to the wind. A mishap here can result not only in seriously damaging one’s prized possessions but also in personal injury. It’s essential to recognize that the equipment we use, while crucial for achieving stunning results in stone cutting and polishing, can come with inherent risks. Therefore, investing in the right safety gear becomes paramount.
Personal Protective Gear
Gloves
Gloves can be a lapidary artist's best friend. They serve as a buffer between your skin and the sharp edges or rough surfaces of the stones being worked on. A key characteristic of high-quality gloves is their cut resistance, which minimizes the risk of laceration from jagged stone pieces. It's a beneficial choice particularly when performing tasks like sawing or grinding. The best gloves usually feature a snug fit, allowing for dexterity while still providing that critical layer of protection.
A unique aspect of using gloves is the material used. Many opt for leather or synthetic fibers that still allow breathability. This is important because a sweaty hand can easily drop a slippery stone and lead to accidents.
However, there can be disadvantages as well. Sometimes, gloves can limit tactile feedback, making it harder to feel what you’re working on. But the risk of injury far outweighs the minor inconvenience of losing some sensitivity. Overall, gloves are a fundamental component of any lapidary toolkit, safeguarding hands while working on delicate projects.
Safety Glasses
Safety glasses are non-negotiable in the realm of lapidary work. The nature of cutting, grinding, and polishing stones creates debris that can fly at alarming speeds. This is where safety glasses come in, functioning as a shield against flying fragments that might injure your eyes. A key characteristic of quality safety glasses is their impact-resistant lenses.
One notable benefit of safety glasses is their versatility; many models offer anti-fog features and UV protection, making them suitable for extended wear. It's crucial for those engaged in intensive lapidary tasks to be able to see clearly and without obstructions. The unique feature of wraparound design further enhances protection by preventing particles from entering from the sides.
On the downside, some glasses can be uncomfortable for prolonged use, especially if they don't sit right. To combat this, it's advisable to try a few pairs to find one that fits well. Overall, investing in quality safety glasses is essential for preserving one of your most valuable assets—your vision.
Workspace Safety Guidelines
Setting up a proper workspace is a linchpin in ensuring safety while performing lapidary tasks. It’s not just about personal gear; the environment plays a significant role in minimizing risk.
Ventilation Considerations
Proper ventilation is crucial when working with lapidary equipment. Many processes, such as polishing or cutting, can generate dust or fumes that are harmful if inhaled over time. A key characteristic of good ventilation is the ability to circulate air efficiently. This becomes especially beneficial when using machinery that generates heat or dust.
An efficient setup might involve windows, fans, or even an exhaust system that pulls dust away from your work area. While setting up ventilation could require an upfront investment, the long-term health benefits undeniably outweigh the costs. Furthermore, comfortable air quality allows for longer working hours without undue fatigue.
However, there's always the caveat that poor installation of ventilation can lead to blowback situations where harmful particles may become more concentrated in certain areas, thus creating a new risk. It's vital to have a clear plan for ensuring optimal airflow.
Fire Safety
Just as important as any personal protective gear, fire safety must not be overlooked. With machines generating heat and numerous materials involved, the risk of fire can creep up unexpectedly. A key characteristic of effective fire safety is prep—having fire extinguishers handy and knowing their location is indispensable.
Fire extinguishers specifically meant for chemical fires can be invaluable if any volatile materials accidentally ignite. Regular checks on equipment and the elimination of any combustibles around your workspace enhance safety significantly. It’s a good idea to have your fire safety procedures outlined and reviewed regularly.
On the downside, many fail to consider electrical safety, which also plays a critical role. Using faulty wiring or equipment can lead to sparks or shorts that might cause fires. Thus, vigilance is necessary, both in terms of equipment maintenance and workspace safety protocols. Overall, a well-prepared workspace can drastically improve safety during lapidary work, allowing artists to focus on their craft without unnecessary worry.
Techniques in Lapidary Work
In the world of lapidary, the technique is king. Understanding the various methods for handling stone is critical for not only creating beautiful pieces but also for ensuring that the process is safe and efficient. In this section, we will delve into the essential techniques of cutting, grinding, and polishing stones, exploring how each contributes to the overall craftsmanship in lapidary work.
Cutting Techniques
Basic Cuts
The cornerstone of any lapidary operation is the Basic Cuts. These cuts serve a fundamental purpose: they allow lapidaries to shape their stones into manageable pieces. The precision in these cuts is essential, as they dictate the foundation of all subsequent processes. A key characteristic of Basic Cuts is their simplicity; they are straightforward enough for beginners yet critical for advanced techniques.
A unique feature of Basic Cuts is their versatility. Whether you're slicing through a raw piece of agate or shaping a soft piece of soapstone, these initial cuts can adapt to different materials. However, they come with both advantages and disadvantages. On the plus side, they require minimal equipment and can be executed with basic tools. On the flip side, a machine mishap at this stage can lead to unrepairable damage to the piece.
Advanced Techniques
Once a lapidary has mastered the basics, they often move onto Advanced Techniques. These encompass more complex cuts that require a deeper understanding of the material properties and precision craftsmanship. A notable characteristic of Advanced Techniques is the level of control required; these techniques can significantly enhance the aesthetics of the stone, allowing for intricate designs that captivate the eye.
The unique feature of these techniques lies in their potential for customization. Advanced cuts allow lapidaries to express creativity, transforming ordinary stones into works of art. Nonetheless, the learning curve can be steep. Missteps in this arena may lead to wastage of both time and material. Thus, a solid foundation in basic techniques is crucial to navigate this stage effectively.
Grinding Techniques
Understanding Grit Grades
Grind techniques are pivotal in lapidary work because they shape the surface of the stone before polishing. Understanding Grit Grades helps in choosing the right abrasives for specific projects—it's not just a matter of picking any old wheel.
What sets grit grades apart is the degree of coarseness, marked by numbers. Lower numbers signify coarser grits, while higher ones mean finer grits. This system allows lapidaries to achieve the precise finish they desire. An advantage of understanding grit grades is that it enhances efficiency; using the right grit can save time and effort in polishing. However, misjudging the size can lead to oversmoothing a desired texture or leaving too much roughness, which could require repeated grinding.
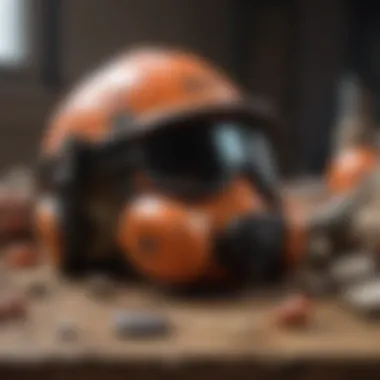
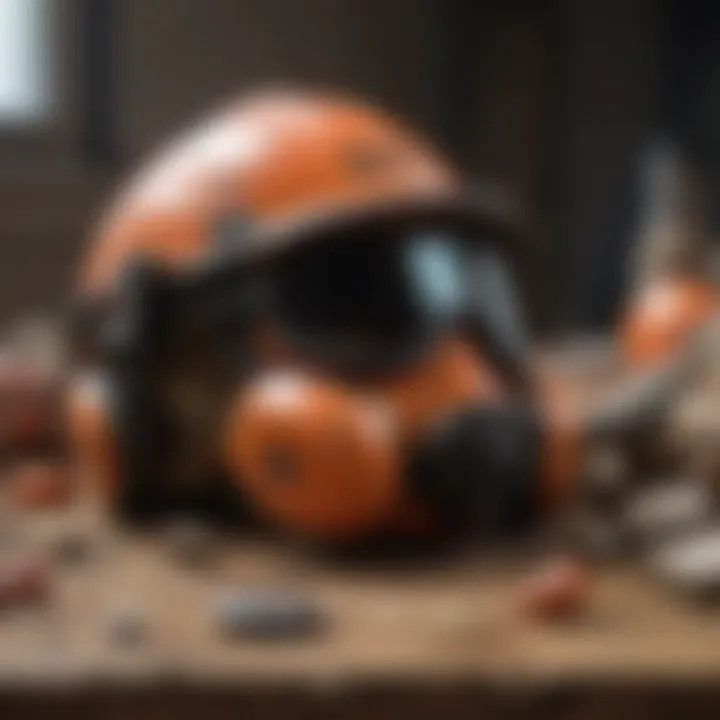
Effective Grinding Patterns
Moving beyond grit, the discussion on Effective Grinding Patterns is vital. Patterns dictate how the grinder interacts with the stone surface, which can heavily affect the end result. A characteristic feature of these patterns is that they help in achieving uniformity across the surface of the stone.
This systematic approach provides benefits in both speed and quality. A well-executed pattern reduces the chances of chipping or scratching the stone unnecessarily. However, complexity can be a double-edged sword. Overcomplicating paths without a clear plan may lead to inconsistencies and a subpar finish.
Polishing Techniques
Polishing Compounds
When it comes time to give that final touch, Polishing Compounds play a vital role. These compounds are specifically designed to smooth and shine the surface of stones, embellishing their natural beauty. The key characteristic of these compounds is their composition, often comprising a mix of abrasives that facilitate various polishing effects, depending on the desired outcome.
These compounds offer versatility, suitable for different stones and finishes. However, selecting the wrong type can result in scratches, marring the surface of a beautifully worked stone. Understanding how to match the right polishing compound to your material minimizes this risk, ensuring a high-quality finish.
Achieving Gloss Finish
Lastly, the goal of all polishing efforts is to achieve a Gloss Finish. This aspect is crucial as it reflects the lapidary’s skill and knowledge of the materials used. A gloss finish highlights color and pattern, transforming the stone from a mere object into a work of art.
The unique feature here lies in the technique involved; achieving this high shine involves careful layering of compounds and precise application. This process is beneficial because it enhances the visual appeal of the stone dramatically. However, achieving the perfect gloss can be labor-intensive and time-consuming, requiring patience and attention to detail.
In the world of lapidary, every cut, grind, and polish contributes to the story a stone tells.
Mastering these techniques is not merely about physical manipulation of materials; it’s an art form that reveals the myriad possibilities waiting within each stone.
Maintenance of Lapidary Equipment
Maintaining lapidary equipment is a critical aspect of the craft that often gets overshadowed by the excitement of cutting and polishing stones. A well-maintained tool not only enhances working efficiency but also ensures the safety of the user. Regular maintenance contributes to the longevity of equipment and minimizes the risk of malfunction during crucial operations. Investing time into proper upkeep can save collectors and craftsmen alike from costly repairs or replacements. Moreover, understanding the nuances of maintenance can elevate the quality of the finished piece, resulting in a glossier polish and more precise cuts.
Routine Cleaning Procedures
Cleaning is the cornerstone of maintaining lapidary equipment. Here’s a breakdown of routine cleaning procedures:
- Dust and Debris Removal: After every session, take a moment to wipe down the tools using a soft cloth or brush. Dust and tiny stone particles can accumulate, causing wear over time. This quick fix prevents minor issues from turning into bigger problems down the line.
- Fluid Checks: If your equipment uses any liquids, like coolant or lubricants, keeping them at the appropriate levels is essential. Dirty or low liquid levels may not effectively cool or lubricate tools, causing overheating and reduced efficiency.
- Inspecting Accessories: Take the time to examine any bits or pads used in the machines. Look for signs of wear or damage. It’s often cheaper to replace these components periodically than to deal with the aftermath of a broken tool.
- Regular Deep Cleaning: Every few months, carry out a thorough cleaning. Before diving into the nitty gritty, unplug all machines. Use a cleaning solution suitable for the materials of your equipment. Pay extra attention to nooks and crannies where dust may hide.
Storage Solutions
A well-organized workspace can facilitate efficient lapidary work. Proper storage solutions are just as crucial as cleaning them regularly:
- Dry Environment: Always store your equipment in a dry place to avoid rust or corrosion. A moisture-free toolbox can significantly prolong the life of your tools. Consider using silica gel packs or dehumidifiers if your workspace is prone to humidity.
- Dedicated Storage Areas: Create a separate area for each type of tool. Keep cutting, grinding, and polishing equipment apart to avoid any potential damage. Having a designated spot allows quick access and encourages better organizational habits.
- Protective Covers: Using protective covers can shield tools from dust and accidental damage. If tools need to be packed away, wrapping them in soft cloth or using tool cases will help maintain their condition.
- Inventory Check-Up: At least once a year, take stock of your equipment. Document the condition of each tool, checking for wear and tear. A well-maintained inventory allows collectors to replace items as needed without last-minute hitches during a project.
"Investing time in equipment maintenance is investing in the quality of your craftsmanship."
Ultimately, with the right cleaning procedures and thoughtful storage solutions, lapidary equipment not only works better but can serve its owner for years to come. It’s a small price to pay for the sustained joy of crafting beautiful gems.
Cost Considerations in Purchasing Equipment
Purchasing lapidary equipment can feel a bit like navigating a minefield, especially for those just starting out. There’s a plethora of choices available, and each piece of equipment comes with different price tags attached. Understanding the costs associated with lapidary equipment is vital for making informed decisions. This section aims to shed light on budgeting essentials, potential pitfalls, and the relationship between quality and price.
Budgeting for Beginners
As a rookie in the lapidary world, getting a handle on budgeting shouldn’t be overlooked. Successful budgeting means knowing what you can afford without breaking the bank. The excitement of buying new tools can sometimes cloud judgment, leading to splurging on items that might not be necessary right away or may be too advanced for beginner skills.
Here are a few budgeting tips tailored for newcomers:
- Research First: Before diving into purchases, take time to investigate what tools are actually essential. Not every shiny piece of machinery is necessary at the outset.
- Prioritize Your Needs: Focus on foundational equipment first. Starting with cutting tools, such as a diamond saw, then gradually acquiring grinders and polishers may be wise.
- Set a Realistic Budget: Determine how much money you’re willing to spend at the beginning. It’s important to factor in ongoing costs like consumables—grit, polishing pads, etc.
- Look for Starter Kits: Many suppliers offer starter kits, which bundle multiple essential items at a price that is often lower than buying each item individually.
Budgets may require adjustments as skills develop, but laying solid groundwork from the start can prevent financial strain while pursuing this craft.
Evaluating Quality vs. Price
When it comes down to brass tacks, evaluating quality against price is like weighing gold against lead. It can feel tempting to opt for the lowest bidder when equipment shopping. However, skimping on quality might lead to frustrations down the road, such as needing more frequent replacements or, worse, tool failures during critical projects.
Consider the following factors while balancing quality and price:
- Material and Build: Generally, tools forged from high-grade materials tend to last longer and perform better. Investing in a decent saw or grinder can save headaches in the long run.
- Brand Reputation: Some brands have built a solid reputation based on reliability and performance. Research reviews or ask fellow hobbyists on forums like reddit.com for recommendations.
- Warranty and Support: A good warranty can be worth its weight in gold. It provides peace of mind against manufacturing defects.
- Long-Term Investment: Think about the life span and how much you plan to use the equipment. If you're looking at an investment piece, it might be better to spend more now than to face continual repairs or replacements.
"In the lapidary community, as in life, shortcuts often lead to more complex problems later on. Invest wisely."
Navigating the complex landscape of costs in the lapidary field requires patience and a discerning eye. By carefully weighing initial expenses against the quality of tools and equipment, enthusiasts can build a collection that serves them well through their creative journeys.
End
When we wrap our heads around the realm of lapidary equipment, it’s clear that this isn’t just about tools—it's a journey into the art and science of transforming rough stone into polished gems. Understanding the nitty-gritty of this craft offers invaluable insights for both hobbyists and seasoned professionals alike. Embracing the finer details can elevate one's work, resulting in stunning pieces that not only shine bright but also tell a story.
Recap of Key Points
As we look back on what we've covered, several key takeaways emerge:
- Diverse Equipment Types: From saws to polishing tools, each piece of equipment serves a specific function in the honing process.
- Safety First: Ignoring safety equipment is like driving a car without a seatbelt—it's just not smart. Personal protective gear and workspace safety go hand-in-hand to ensure a risk-free environment.
- Techniques Matter: Mastering cutting, grinding, and polishing techniques affects the final product. It’s not just about rolling up your sleeves; it’s about knowing the methods that yield the best results.
- Investment Choices: Cost can be a tipping point for many. Understanding the balance between quality and affordability is crucial when investing in lapidary equipment.
- Maintenance is Key: Keeping tools in tip-top shape ensures longevity and better performance in the long run.
Future Trends in Lapidary Equipment
Looking ahead, the world of lapidary equipment is ripe for innovation. Several trends stand out:
- Eco-friendly Materials: With global awareness about sustainability on the rise, expect more equipment to be made from recyclable materials or designed for less waste.
- Technological Integration: Advanced technologies, such as smart sensors for grinding machines, are likely to become commonplace, allowing for precision cuts and adjustments as needed.
- Custom Capabilities: More manufacturers might offer customizable options that cater to individual preferences and skill levels, making lapidary work more accessible to beginners while still challenging for veterans.
- Community Engagement: Online platforms and social media will continue playing a vital role in connecting enthusiasts, providing forums for sharing experiences, tips, and innovations. Places like and could become treasure troves of shared knowledge for all things lapidary.
This article should serve as a stepping stone to foster a deeper understanding of not only what tools are available but also how their proper use and maintenance can enhance the quality of your work.
Conclusively, embracing the craft of lapidary with informed choices profoundly impacts the art of gemstone creation, where each piece is a reflection of skill, patience, and passion.