Unveiling the Intricacies of Jewellery Casting Moulds: A Masterclass in Artistry
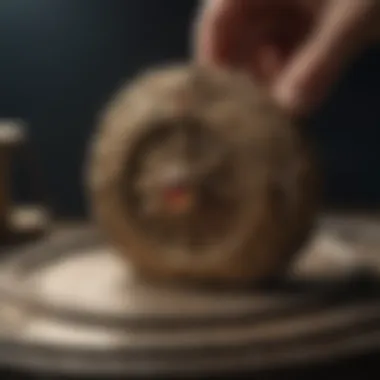
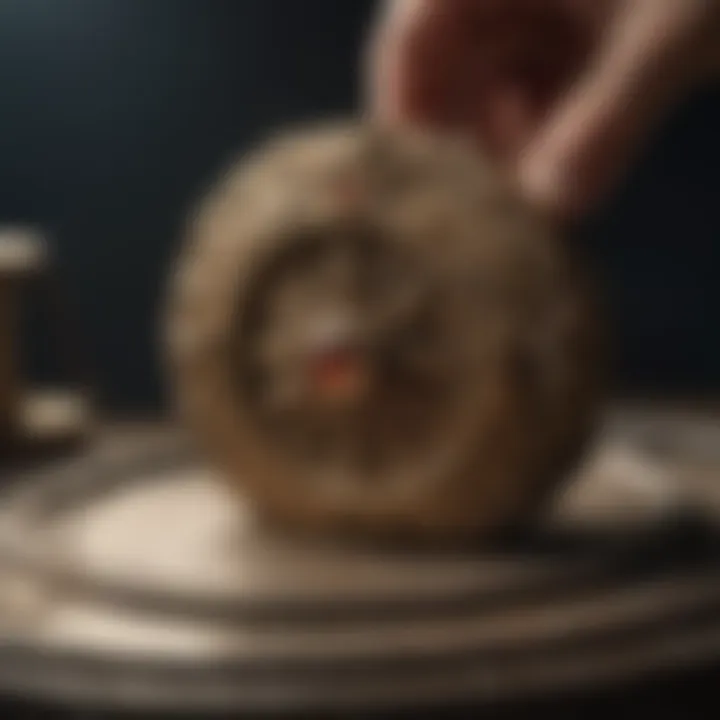
Rock and Fossil Identification
In the realm of jewellery casting moulds, understanding the types of materials used is crucial. Just as a rock or fossil possesses unique characteristics, jewellery casting moulds come in various forms, each with specific attributes. From rubber moulds for intricate details to silicone moulds for simplicity, the choice of material significantly impacts the outcome of the jewellery piece. Identifying the suitable mould type for a particular design is akin to recognizing the distinguishing features of a rare mineral specimen.
Moreover, paying attention to the details is essential in both fields. Just as collectors carefully examine rocks and fossils for specific markings or structures, jewellery makers scrutinize their moulds for imperfections that could affect the final product. Utilizing specialized tools such as mould release sprays and carving instruments, craftsmen ensure that their moulds are pristine, much like how a meticulous rock collector handles fragile fossils with precision.
Best practices for collecting
When it comes to jewellery casting moulds, the gathering of materials and tools follows a protocol similar to that of rock and fossil collection. Adopting best practices in mould selection and maintenance is imperative for achieving optimal results. Just as a rock collector seeks out prime sites for specimen discovery, jewellery makers hunt for premium mould suppliers known for quality and reliability.
Additionally, just as safely extracting specimens from the earth is crucial in rock and fossil collection, handling and storing moulds correctly is vital in jewellery making. Proper extraction techniques ensure that the integrity of the specimen is maintained, much like proper storage methods protect the integrity of the mould and ultimately the jewellery piece it shapes.
Techniques for preserving rocks and fossils
While preservation techniques differ between rocks and fossils versus jewellery casting moulds, the underlying principle remains the same: ensure longevity and protect intrinsic value. For rocks and fossils, preservation involves shielding specimens from environmental factors that could degrade them. Jewelry casting mould preservation typically involves regular cleaning and proper storage to prevent deformation or deterioration.
In considering creative display ideas for rocks and fossils, one must showcase these natural wonders in a visually appealing and educational manner, highlighting their geological significance. Similarly, jewellery makers may explore innovative ways to exhibit their moulds, perhaps showcasing the intricate details of the mould alongside the final jewellery piece, providing insights into the meticulous craftsmanship behind the creation.
Geological Insights
Introduction to Jewellery Casting Moulds
In this article, we embark on a detailed exploration of the intricate world of jewellery casting moulds. Understanding the nuances of jewellery casting moulds is paramount for anyone involved in the field of jewellery making. These moulds play a pivotal role in bringing to life the exquisite and intricate designs that adorn individuals worldwide. By delving into the types of moulds utilized and the casting techniques employed, readers will gain a profound insight into this fundamental aspect of jewellery production.
Understanding the Role of Moulds in Jewellery Casting
Types of Mould Materials
When it comes to jewellery casting, the choice of mould material is of utmost importance. Various materials, such as silicone, rubber, and metal, each offer distinct characteristics that influence the final outcome of the jewellery piece. Silicone, for instance, is favored for its flexibility and ease of use, making it ideal for intricate designs. Rubber moulds provide durability and can withstand high temperatures, crucial for casting certain metals like gold. In contrast, metal moulds are known for their longevity and ability to replicate fine details accurately. Understanding the properties of different mould materials is essential for selecting the most suitable option based on the design requirements and casting technique.
Importance of Mould Design
The design of a mould significantly impacts the quality and intricacy of the final jewellery piece. A well-crafted mould design ensures that every detail of the original pattern is faithfully reproduced during the casting process. Factors such as venting, gating, and cooling channels are carefully incorporated into the mould design to optimize metal flow and reduce defects. The precision and intricacy of the mould design directly contribute to the overall casting efficiency and the final aesthetic appeal of the jewellery piece. Meticulous attention to mould design not only enhances the casting process but also plays a crucial role in achieving consistent quality across multiple castings.
Evolution of Jewellery Casting Techniques
Historical Overview
The evolution of jewellery casting techniques traces back centuries, with civilizations around the world developing unique methods to create intricate adornments. From the ancient lost-wax casting technique practiced by the Egyptians to the sophisticated gravity casting methods of the Renaissance era, each period contributed to the rich tapestry of jewellery casting history. Studying the historical overview of jewellery casting not only provides insight into the origins of the craft but also highlights the ingenuity and creativity of our predecessors in manipulating metal to shape exquisite ornaments.
Modern Innovations

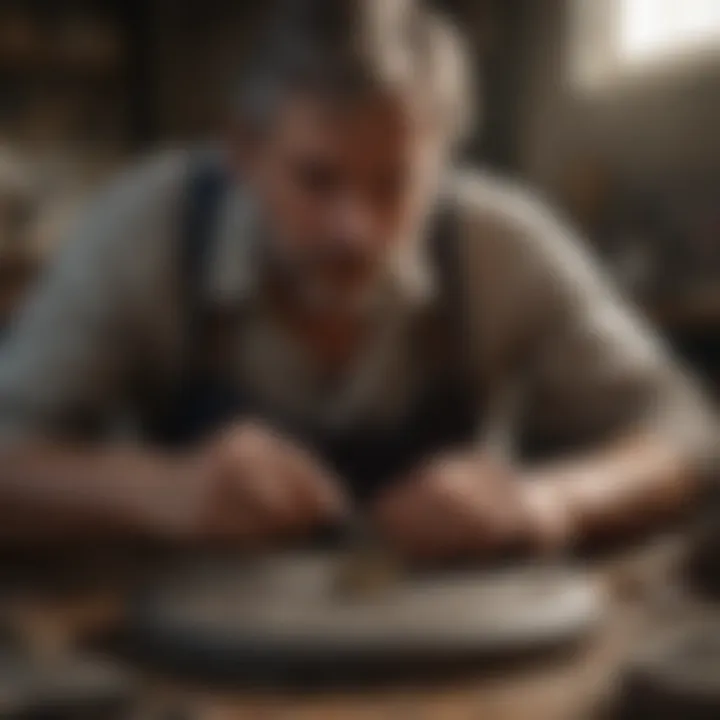
In the contemporary landscape of jewellery casting, technological advancements have revolutionized the way intricate jewellery pieces are produced. Techniques such as CAD (Computer-Aided Design) and 3D printing have streamlined the design process, enabling unparalleled precision and customization. Innovations in casting equipment, such as induction melting furnaces and vacuum chambers, have enhanced casting efficiency and quality control. The integration of modern innovations not only expedites the production process but also opens up a realm of possibilities for creating avant-garde jewellery designs that push the boundaries of traditional craftsmanship.
Types of Jewellery Casting Moulds
Jewellery casting moulds play a pivotal role in the creation of exquisite pieces, each type offering unique benefits and considerations. Understanding the variations in jewellery casting moulds is essential for achieving desired results and enhancing the production process.
Investment Moulds
Investment moulds are a cornerstone in jewellery casting, known for their intricate techniques that result in precise and detailed designs. The two primary techniques within this category are the Wax Mold Technique and Ceramic Shell Technique.
Wax Mold Technique
The Wax Mold Technique involves creating a wax model of the desired jewellery piece, which is then encased in a ceramic mold. This method allows for intricate details to be captured, making it a popular choice for complex designs. The key characteristic of this technique is its ability to replicate fine details with high accuracy, ensuring the final product retains the intricacies of the original wax model. However, a drawback of this method is the susceptibility of the wax to warping or breaking during the casting process, requiring careful handling.
Ceramic Shell Technique
The Ceramic Shell Technique utilizes a ceramic slurry to build up layers around a wax model, creating a heat-resistant mold. This technique is favored for its ability to withstand high temperatures during the casting process, ensuring the molten metal fills the mold accurately. The unique feature of this technique lies in its capacity to produce intricate designs that require high levels of detail. Despite its advantages in creating complex pieces, this method can be time-consuming due to the multiple layers required in building the ceramic shell.
Sand Casting Moulds
Sand casting moulds offer a more cost-effective approach to jewellery production, with variations such as Greensand Moulds and No-bake Moulds.
Greensand Moulds
Greensand Moulds utilize a mixture of sand, clay, and water to create molds that are relatively easy to work with. The key characteristic of Greensand Moulds is their flexibility, allowing for quick modifications to the mold as needed. This makes them a suitable choice for rapid prototyping or short production runs. However, one drawback is the tendency for greensand molds to degrade quickly, requiring constant monitoring and replacement.
No-bake Moulds
No-bake Moulds, also known as air-set or dry sand molds, offer a faster production turnaround compared to traditional greensand molds. The unique feature of these molds is their self-curing capability, eliminating the need for baking or hardening processes. This efficiency makes them an attractive choice for small to medium-scale jewellery production. However, the surface finish of castings from no-bake molds may exhibit rough textures, requiring post-processing to achieve desired aesthetics.
Centrifugal Casting Moulds
Centrifugal casting molds utilize centrifugal force to distribute molten metal into the mold cavity, with techniques such as Spin Casting and Vacuum Casting.
Spin Casting
Spin Casting involves placing the mold in a spinning chamber while pouring the molten metal, allowing centrifugal force to evenly distribute the metal. This method is popular for its efficiency in producing duplicate pieces with consistent quality. The key characteristic of Spin Casting is its ability to create homogeneous castings with minimal porosity, making it ideal for mass production. However, a limitation of this technique is the potential for air entrapment in the mold, which can result in defects in the final casting.
Vacuum Casting
Vacuum Casting leverages vacuum pressure to draw the molten metal into the mold, ensuring a precise and bubble-free fill. The key characteristic of this technique is its ability to eliminate voids and porosity in the castings, resulting in high-quality finishes. Vacuum Casting is a preferred choice for creating intricate and delicate designs that require flawless detailing. However, the setup and maintenance of vacuum equipment can add complexity and cost to the casting process.
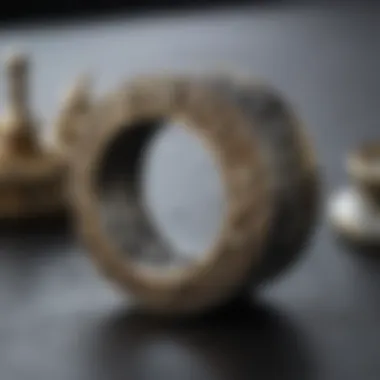
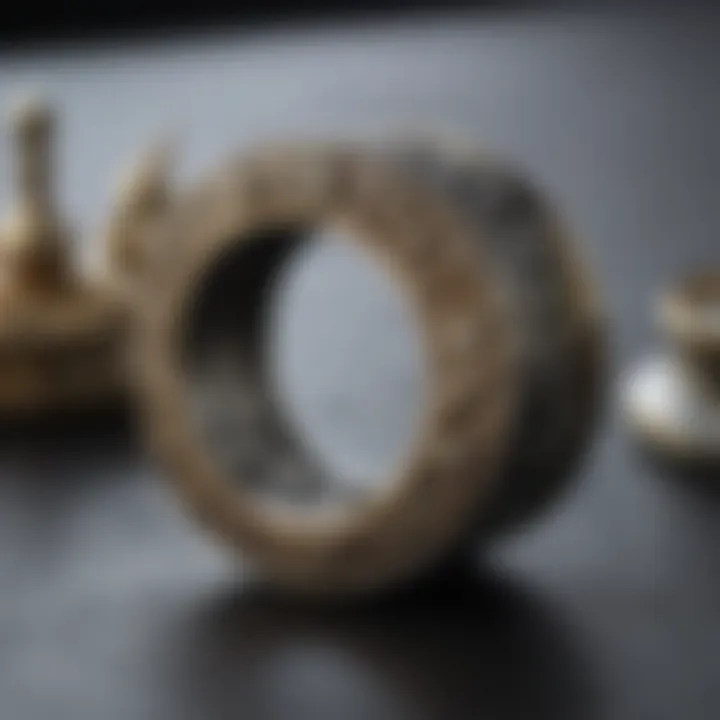
Factors Affecting Mould Selection
When delving into the intricate realm of jewellery casting moulds, one must understand the critical role that factors affecting mould selection play in the crafting process. The choice of mould for jewellery casting is a decision that impacts the final outcome, quality, and efficiency of the production. Factors such as material compatibility, complexity of design, and production volume are paramount in determining the most suitable mould for a specific jewellery piece. By carefully considering these factors, jewellers can ensure a seamless and successful casting process.
Material Compatibility
Metal Alloys
Metal alloys are a fundamental aspect of mould selection in jewellery casting. Their unique blend of properties, including durability, malleability, and heat resistance, make them a popular choice for creating high-quality jewellery pieces. The key characteristic of metal alloys lies in their ability to withstand the extreme temperatures involved in the casting process, ensuring that the mould maintains its shape and integrity throughout. While metal alloys offer numerous advantages such as excellent detail reproduction and smooth finishes, they come with the disadvantage of higher costs compared to other mould materials.
Temperature Sensitivity
Temperature sensitivity is another crucial aspect to consider when selecting mould materials for jewellery casting. The ability of a mould material to withstand and conduct heat efficiently directly impacts the casting process's success. Materials with high temperature sensitivity can produce intricate designs and textures on jewellery pieces. The key characteristic of temperature sensitivity lies in its influence on the mould's flexibility and ease of use during the casting process. While materials with high temperature sensitivity offer advantages such as precise detailing and minimal shrinkage, they may pose challenges in handling and maintenance.
Complexity of Design
Intricate Patterns
Intricate patterns play a significant role in mould selection, especially for jewellery pieces that require detailed and elaborate designs. The key characteristic of intricate patterns lies in their ability to add depth and visual interest to the final jewellery piece. When choosing a mould for intricate patterns, jewellers prioritize precision and accuracy to ensure that the design is faithfully reproduced during the casting process. While intricate patterns offer the advantage of creating unique and eye-catching jewellery pieces, they may present challenges in terms of mould release and assembly.
Textural Details
Textural details contribute to the aesthetics and tactile appeal of jewellery pieces, making them a vital consideration in mould selection. The key characteristic of textural details lies in their ability to enhance the overall look and feel of the jewellery piece. Materials that can capture and retain textural details effectively are preferred for creating visually stunning pieces. While textural details offer the advantage of adding a distinct touch to jewellery designs, they may require meticulous handling and finishing techniques to preserve the desired textures.
Production Volume
Mass Production
Mass production holds significance in mould selection for jewellers specializing in bulk manufacturing of jewellery pieces. The key characteristic of mass production lies in its ability to optimize the production process, reducing turnaround times and costs per unit. When choosing moulds for mass production, jewellers focus on efficiency and consistency to meet high demand without compromising quality. While mass production offers advantages such as economies of scale and streamlined workflows, it may pose challenges in terms of customization and design flexibility.
Customized Pieces
Creating customized jewellery pieces requires careful consideration of mould selection to ensure that each piece reflects the client's unique preferences. The key characteristic of customized pieces lies in their personalized nature, catering to individual tastes and styles. Jewellers crafting customized pieces prioritize flexibility and adaptability in mould design to accommodate varying design requirements. While customized pieces offer the advantage of exclusivity and personalization, they may involve higher production costs and longer lead times.
Techniques for Creating Jewellery Moulds
In the realm of jewellery crafting, mastering the art of creating moulds is crucial for producing intricate and flawless pieces. Techniques for creating jewellery moulds encompass a set of skills and processes that are integral to the overall jewellery casting process. Understanding these techniques is fundamental to ensuring the success and quality of the final product. Delving into the nuances of these techniques will provide invaluable insights into the craftsmanship behind each jewellery piece.
Lost-Wax Casting Process
Wax Pattern Creation
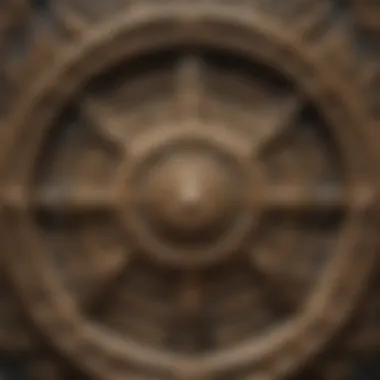
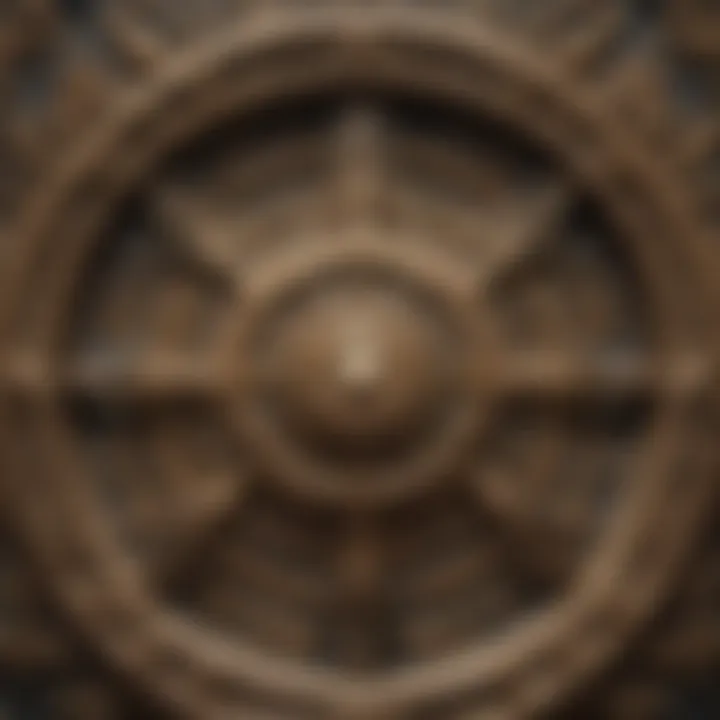
Wax pattern creation is a pivotal stage in the lost-wax casting process. This intricate process involves sculpting the desired design into a wax model, which will serve as the blueprint for the final jewellery piece. The key characteristic of wax pattern creation lies in its ability to capture intricate details with precision, allowing for complex designs to be faithfully reproduced. This method is popular in jewellery making due to its versatility in creating elaborate patterns and textures. However, a disadvantage of wax pattern creation is its susceptibility to deformities during handling, requiring meticulous attention to detail to prevent flaws in the cast piece.
Investment Casting
Investment casting plays a crucial role in transforming wax patterns into metal jewellery. This process involves encasing the wax patterns in a ceramic shell, which is then heated to remove the wax, leaving behind a hollow mold for casting. The main advantage of investment casting is its ability to create near-perfect replicas of the wax patterns, resulting in finely detailed finished products. This technique is favored for its precision and fine finishing, making it an ideal choice for intricate jewellery designs. However, investment casting can be time-consuming and labor-intensive, adding to the production timeline and costs in certain scenarios.
Silicone Mould Making
Mold Preparation
Mold preparation is a critical step in silicone mould making, determining the success of capturing the design details accurately. The key characteristic of mold preparation lies in creating a flawless mold that can withstand the casting process without deformities. This method is popular for its flexibility and durability, allowing for easy demolding and extended reuse. However, one disadvantage of mold preparation is the potential for air bubbles to trap within the mold, leading to imperfections in the final pieces. Careful attention to detail during mold preparation is essential to ensure the quality of the resulting jewellery.
Curing Process
The curing process in silicone mould making involves setting the prepared mold to solidify the silicone material. This crucial stage ensures that the mold attains the desired flexibility and strength for casting operations. The key characteristic of the curing process is its ability to stabilize the mold, allowing for repeated use without compromising on the intricate details of the jewellery piece. Silicone molds are popular for their ease of use and high fidelity in capturing intricate designs. However, a potential disadvantage of the curing process is the longer curing time required, which can impact the overall production schedule in time-sensitive projects.
Vacuum Casting
Pressure Casting
Pressure casting is an essential technique in vacuum casting where molten metal is forced into the mold under pressure to ensure complete filling and reduced porosity. The key characteristic of pressure casting lies in its ability to produce dense and high-quality castings with minimal defects. This method is preferred for its efficiency in capturing the finest details of the mold, making it suitable for intricate jewellery designs. However, a disadvantage of pressure casting is the need for specialized equipment and controlled environments, adding complexity to the casting process.
Finishing Techniques
Finishing techniques in vacuum casting play a vital role in enhancing the aesthetics and quality of the final jewellery pieces. The key characteristic of finishing techniques is their ability to refine the surface texture, remove imperfections, and impart a flawless appearance to the cast pieces. This method is popular for its versatility in achieving different surface finishes, from matte to high gloss, enhancing the overall appeal of the jewellery. However, one potential disadvantage of finishing techniques is the labor-intensive nature of some processes, requiring skilled artisans to execute intricate detailing and polishing for a flawless outcome.
Quality Control in Jewellery Casting
Quality control in jewellery casting is a critical component that ensures the production of flawless and high-quality jewellery pieces. It plays a vital role in maintaining the standards of craftsmanship and meeting customer expectations. By implementing rigorous quality control measures, jewellery manufacturers can identify and rectify any defects or imperfections in the casting process, thereby enhancing the overall value and appeal of the final product.
Surface Finish
Polishing Methods
Polishing methods in jewellery casting are a fundamental aspect that significantly contributes to the final appearance and quality of the piece. The meticulous process of polishing involves the removal of any surface imperfections, creating a smooth and lustrous finish. One key characteristic of polishing methods is their ability to enhance the brilliance and shine of metals, giving the jewellery a luxurious and refined look. This choice of finishing technique is highly favored for its ability to add a professional touch to jewellery pieces, elevating their aesthetic appeal. Despite the time and effort required for thorough polishing, the result is a stunning finish that positively impacts the overall outcome of the jewellery.
Defect Detection
Defect detection is a crucial element in quality control for jewellery casting, as it helps identify any flaws or irregularities in the manufactured pieces. The key characteristic of defect detection lies in its ability to spot even the smallest imperfections that may affect the final quality of the jewellery. By utilizing advanced techniques such as magnification and inspection tools, manufacturers can ensure that every piece meets the highest standards of craftsmanship. While defect detection adds an additional layer of scrutiny to the production process, it ultimately guarantees that only impeccable jewellery pieces reach the hands of customers.
Dimensional Accuracy
Tolerance Evaluation
Tolerance evaluation is essential in maintaining the dimensional accuracy of jewellery pieces during the casting process. This aspect focuses on ensuring that the final product meets the specified dimensions and tolerances set for each design. The key characteristic of tolerance evaluation is its ability to uphold the precise measurements laid out in the initial design, preventing any deviations that may compromise the overall integrity of the jewellery. By meticulously evaluating tolerances at each production stage, manufacturers can uphold consistency and precision in their creations. While adherence to strict tolerances may require meticulous attention to detail, the result is jewellery pieces that align perfectly with the intended design.
Measurements Validation
Measurements validation serves as a method of verifying the accuracy and consistency of the dimensions in jewellery casting. This process involves cross-checking measurements at various stages of production to ensure that each component aligns with the specified dimensions. The key characteristic of measurements validation is its role in confirming the structural integrity and precise sizing of jewellery pieces. By validating measurements throughout the casting process, manufacturers can detect and rectify any discrepancies promptly. While measurements validation may add an additional layer of complexity to production workflows, it is essential for guaranteeing that the final jewellery pieces meet the exact specifications outlined in the design phase.