Mastering the Art of Silver Crafting with Ring Molds: A Detailed Guide
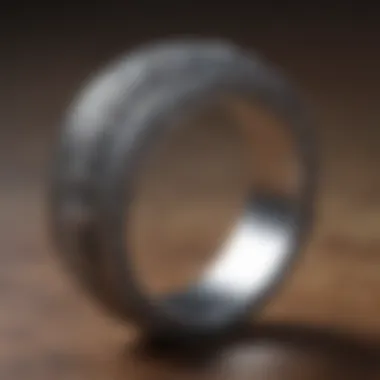
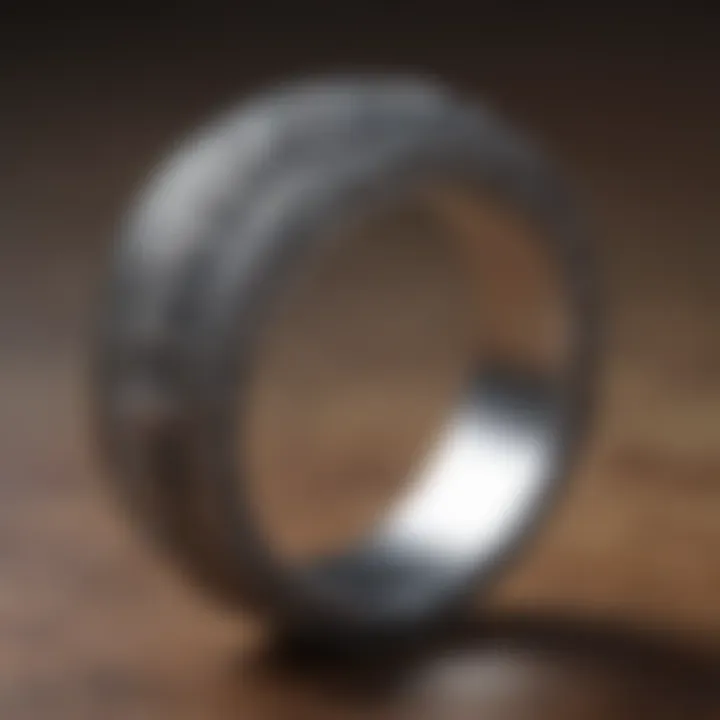
Rock and Fossil Identification
When it comes to silver crafting using ring molds, identifying the right type of metal and its characteristics is crucial for successful casting. Silver ores possess unique properties that require a keen eye and skilled craftsmanship to work with effectively. Understanding the various types of silver alloys and their distinct characteristics is essential for artisans aiming to create intricate jewelry pieces. Utilizing specialized tools like magnifiers, calipers, and metal tests can aid in accurate identification, ensuring a smooth casting process.
Techniques for Crafting with Ring Molds
Crafting silver jewelry with ring molds involves a meticulous process that combines creativity and precision. Artisans must pay attention to every detail, from selecting the appropriate ring size to preparing the mold for casting. In the initial stages, the silver is melted at specific temperatures to achieve the desired consistency for pouring. Once the molten metal is ready, it is carefully poured into the ring mold, allowing for intricate patterns and designs to take shape. After cooling and solidifying, the jewelry piece is carefully extracted from the mold, revealing a unique and beautifully crafted silver creation.
Creative Processes in Silver Casting
The art of silver casting using ring molds offers endless possibilities for creative expression. Artists can experiment with different mold designs, textures, and finishes to craft one-of-a-kind jewelry pieces. From contemporary minimalist styles to ornate vintage-inspired creations, the creative process in silver casting allows for artistic freedom and innovation. By integrating various techniques such as sand casting, vacuum casting, or centrifugal casting, artisans can achieve diverse aesthetics and textures in their silver jewelry designs.
Preserving Silver Jewelry Masterpieces
Once a silver jewelry piece is crafted using ring molds, proper preservation techniques are essential to maintain its beauty and luster over time. Implementing effective storage methods, such as using anti-tarnish strips or storing pieces in air-tight containers, helps prevent oxidation and discoloration. Additionally, regular cleaning and polishing of silver jewelry pieces can prolong their lifespan and keep them looking vibrant and appealing. Creative display ideas, such as using velvet-lined cases or transparent display boxes, enhance the visual presentation of silver jewelry masterpieces, showcasing their uniqueness and craftsmanship.
Introduction to Silver Crafting with Ring Molds
Crafting exquisite silver jewelry requires a mastery of techniques and tools, with ring molds playing a pivotal role in the process. In this article, we delve deep into the world of utilizing ring molds for silver crafting, exploring the intricate steps involved in creating unique designs. By understanding the importance of ring molds in silver casting, artisans can elevate their craft and produce stunning pieces that reflect precision and creativity.
Understanding the Role of Ring Molds in Silver Crafting
Overview of Ring Molds
Ring molds serve as the foundation for creating intricate silver jewelry pieces. Their seamless design allows for precise shaping of molten silver, enabling artisans to bring their designs to life with impeccable detail. The key characteristic of ring molds lies in their ability to provide a structured framework for casting, ensuring that the final piece maintains its intended shape and form. This feature is especially beneficial for artisans looking to craft complex and symmetrical jewelry designs, as ring molds offer stability and consistency throughout the casting process.
Significance in Silver Jewelry Making
The significance of ring molds in silver jewelry making cannot be overstated. They provide artists with a versatile tool that allows for creativity and experimentation in design. The unique feature of ring molds lies in their ability to create intricate textures and patterns in silver jewelry, adding depth and dimension to the finished piece. While the advantages of using ring molds are clear in terms of design possibilities, it's essential to consider their limitations, such as restrictions on size and complexity of designs.
Brief History of Ring Mold Usage in Silver Crafting
Ancient Techniques
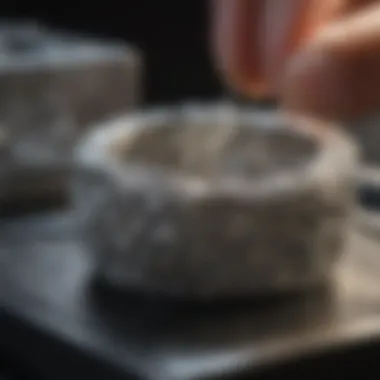
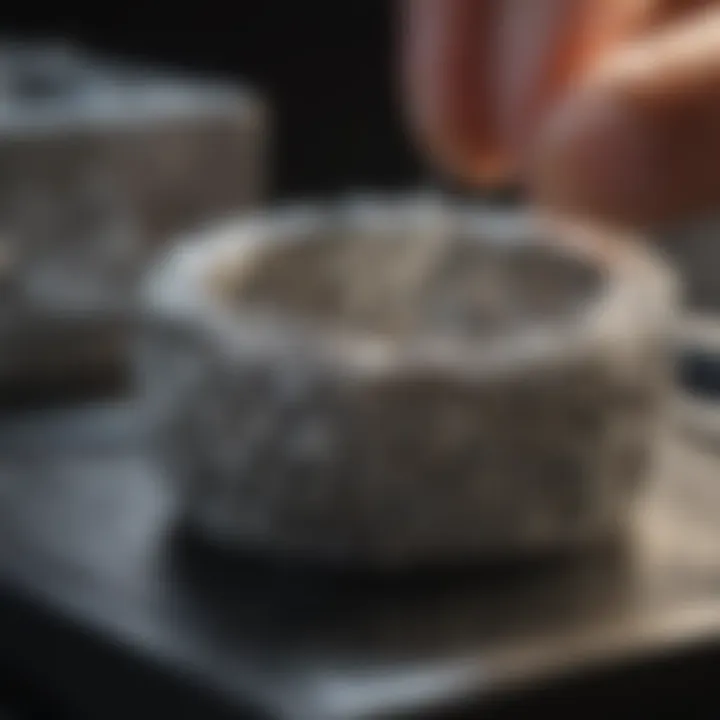
The use of ring molds in silver crafting dates back to ancient civilizations, where artisans employed rudimentary techniques to shape molten metal into jewelry pieces. Ancient techniques of using ring molds involved basic tools and molds made from materials like clay or stone. Despite their simplicity, these early methods laid the foundation for modern jewelry design, showcasing the ingenuity and craftsmanship of ancient artisans.
Evolution in Modern Jewelry Design
In the evolution of modern jewelry design, ring molds have undergone significant advancements to meet the demands of contemporary artisans. Today, jewelers have access to sophisticated tools and materials that allow for more intricate and intricate designs. The key characteristic of this evolution lies in the precision and innovation applied to mold-making techniques, resulting in customizable molds that cater to diverse design preferences. While modern advancements have expanded design possibilities, they also come with considerations such as cost and production time.
Benefits of Using Ring Molds in Silver Casting
Precision in Molded Designs
The precision offered by ring molds in silver casting is unmatched, allowing artisans to create detailed and intricate designs with accuracy. The key characteristic of precision in molded designs lies in the ability to capture even the smallest details of a design, ensuring a flawless end result. This feature is particularly beneficial for artisans who specialize in intricate and delicate jewelry pieces, as ring molds offer the control and precision required for intricate craftsmanship.
Repeatability in Production
One of the significant advantages of using ring molds in silver casting is the repeatability they offer in production. By using consistent molds for multiple pieces, artisans can recreate designs with precision and accuracy, maintaining uniformity across their collection. The unique feature of repeatability in production streamlines the manufacturing process, reducing inconsistencies and ensuring a cohesive presentation of jewelry pieces. However, it's essential to note that over-reliance on mold-based production may limit creative freedom and diversity in design.
Techniques for Silver Casting with Ring Molds
In the realm of silver crafting with ring molds, the techniques employed hold paramount importance in ensuring the precision and quality of the final jewelry piece. One cannot understate the significance of mastering the art of silver casting using ring molds, as it dictates the intricacy and perfection of the designs created. By delving into the specific elements of techniques for silver casting, artisans can harness the full potential of ring molds to bring their creative visions to life.
Preparing the Silver Alloy for Casting
Selection of High-Quality Silver
When embarking on the journey of crafting silver jewelry, the selection of high-quality silver is a critical step that sets the foundation for exquisite creations. The purity of the silver alloy chosen plays a pivotal role in the final outcome, ensuring durability, shine, and authenticity in the jewelry piece. Opting for premium-grade silver guarantees a superior finish and longevity to the jewelry, elevating its overall quality and aesthetic appeal.
Melting and Alloy Mixing
Once the high-quality silver is selected, the process of melting and alloy mixing comes into play, determining the physical properties and workability of the material. This crucial step involves carefully blending the silver with other metals to achieve the desired alloy composition. Proper melting techniques and precise alloy mixing are essential to ensure a homogeneous mixture that can be molded seamlessly using ring molds. By mastering the art of melting and alloy mixing, artisans can control the characteristics of the silver alloy, facilitating intricate designs and flawless casting results.
Creating the Mold Structure
Types of Ring Molds
The choice of ring molds in silver crafting encompasses a variety of shapes, sizes, and materials, each offering unique benefits and design possibilities. From simple band molds to intricate geometric shapes, the diversity in mold types allows artisans to experiment with different styles and finishes in their creations. Selecting the appropriate ring mold type depends on the design requirements and desired outcome, with each mold offering specific advantages in terms of ease of use, detailing capabilities, and versatility in creating diverse jewelry pieces.
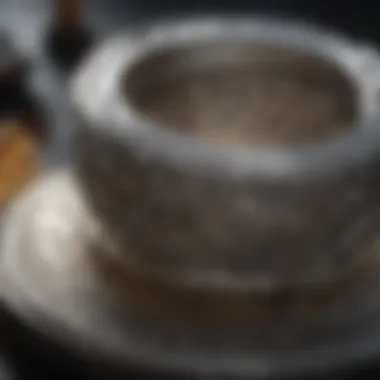
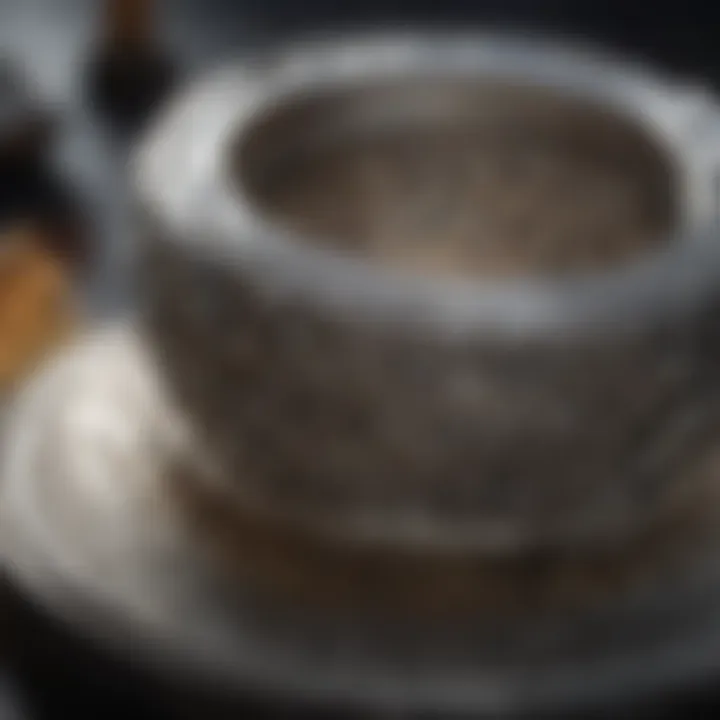
Mold Preparation Techniques
Before casting the silver alloy into the mold, meticulous preparation techniques are employed to ensure the successful replication of the desired design. Proper mold preparation involves cleaning, conditioning, and aligning the mold components for optimal casting results. Fine-tuning the mold surface texture and structure enhances the detailing and definition of the final jewelry piece, showcasing the artisan's attention to detail and precision in craftsmanship.
Casting Process with Ring Molds
Pouring the Molten Silver
The art of pouring the molten silver into the ring mold demands finesse and control to achieve flawless casting outcomes. This stage requires precise handling of the molten silver, ensuring it flows smoothly and uniformly into every crevice of the mold. The pouring technique directly impacts the final shape, texture, and integrity of the jewelry piece, defining its overall appearance and quality. By mastering the art of pouring, artisans can create intricate designs with sharp detailing and clean lines, showcasing their expertise in silver casting.
Cooling and Removing the Jewelry Piece
Once the molten silver is poured and solidified within the ring mold, the cooling and jewelry removal process is initiated to unveil the final masterpiece. Proper cooling ensures that the silver solidifies evenly and retains its intended shape and texture. Careful jewelry piece removal from the mold is vital to prevent any distortions or damage to the delicate design. By following meticulous cooling and removal procedures, artisans can unveil flawlessly crafted silver jewelry pieces, ready for further finishing touches and embellishments.
Design Creativity in Silver Jewelry Making
In the realm of silver jewelry making, design creativity is the cornerstone that elevates a piece from mere adornment to a work of art. This section delves into the importance of fostering innovative design concepts when utilizing ring molds for crafting. By pushing the boundaries of traditional silversmithing, artisans can showcase their unique artistic vision and create signature pieces that resonate with customers on a deeper level.
Design creativity in silver jewelry making not only sets a jeweler apart from their competitors but also allows them to express their individual style and craftsmanship. By embracing innovative design possibilities with ring molds, artisans can experiment with shapes, textures, and materials to forge pieces that stand out in a saturated market.
When discussing design creativity in silver jewelry making, considerations such as functionality, wearability, and aesthetic appeal must be taken into account. Balancing these elements while incorporating personal flair can result in jewelry pieces that are both visually striking and commercially successful. Through this exploration, designers can discover new techniques, push their artistic boundaries, and create collections that resonate with a discerning audience.
Innovative Design Possibilities with Ring Molds
Customized Ring Designs
Customized ring designs offer a bespoke touch to silver jewelry, allowing customers to express their unique personalities through one-of-a-kind pieces. This section delves into the intricate process of crafting personalized rings using ring molds, highlighting the attention to detail and craftsmanship required for each custom creation.
The key characteristic of customized ring designs lies in their ability to tell a story. Whether commemorating a special occasion or symbolizing a meaningful bond, personalized rings hold sentimental value that goes beyond their aesthetic appeal. By offering customizations such as engravings, birthstone settings, or intricate patterns, jewelers can forge connections with their clients and create heirloom pieces that transcend trends.
Incorporating gemstones into customized ring designs adds a touch of luxury and elegance, enhancing the visual impact of the piece. From vibrant colored gemstones to classic diamonds, the choice of gemstone can convey a specific message or accentuate the design elements of the ring. While custom gemstone settings can elevate the overall look of a ring, designers must carefully consider factors such as durability, color harmony, and gemstone authenticity to ensure a cohesive and stunning final product.
Incorporating Gemstones
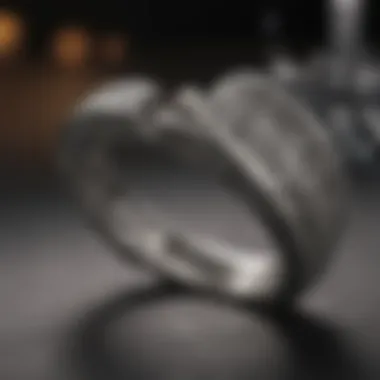
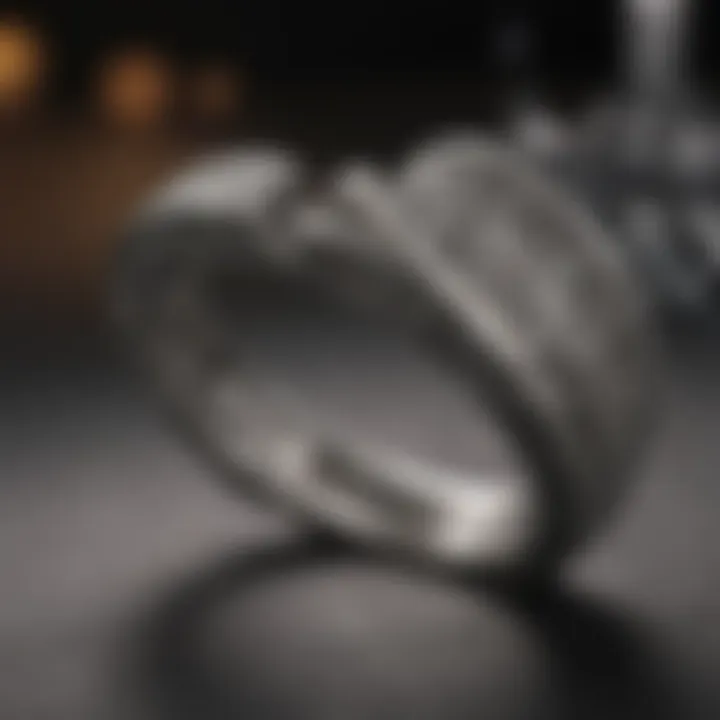
The incorporation of gemstones into silver jewelry opens up a world of creative possibilities, adding depth, color, and symbolism to each piece. By carefully selecting and setting gemstones within ring molds, artisans can elevate their designs and create captivating jewelry that captivates the eye.
The key characteristic of incorporating gemstones lies in the ability to add a pop of color or a touch of sparkle to a silver piece, enhancing its allure and desirability. Whether using traditional precious stones like sapphires and emeralds or opting for unique and rare gems, the choice of gemstone can significantly impact the overall aesthetic and perceived value of the jewelry.
Incorporating gemstones also allows designers to infuse meaning and symbolism into their creations. From birthstone rings that celebrate personal milestones to talismanic gems that offer protection and luck, each gemstone carries its own significance and can resonate deeply with the wearer. By understanding the lore and properties of gemstones, artisans can craft pieces that not only appeal visually but also hold sentimental value for the wearer.
Artistic Finishing Techniques
Artistic finishing techniques play a crucial role in enhancing the beauty and durability of silver jewelry, elevating them from raw castings to polished masterpieces. This section explores the importance of honing finishing skills when working with ring molds, focusing on techniques that add texture, depth, and character to silver pieces.
Polishing and texture detailing are integral steps in the jewelry-making process, as they refine the surface of the metal and create visual interest. By meticulously polishing silver pieces to a high shine or incorporating textured finishes like matte, hammered, or brushed surfaces, artisans can imbue their creations with a tactile quality that invites touch and admiration.
The key characteristic of polishing and texture detailing lies in their ability to showcase the craftsmanship and attention to detail invested in each piece. Whether aiming for a glossy finish that reflects light with brilliance or opting for a rustic texture that evokes a sense of raw beauty, these finishing techniques add a layer of sophistication and artistry to silver jewelry.
Patination and oxidation effects offer a way to introduce color, depth, and antiquity to silver pieces, creating a weathered or aged appearance that adds character and dimension. By selectively applying patina solutions or allowing silver to naturally oxidize, designers can achieve a range of tones from warm browns to rich blues, giving their jewelry a unique and heirloom-like quality.
The unique feature of patination and oxidation effects lies in their ability to transform a plain silver piece into a work of art with history and personality. By embracing these techniques, artisans can create jewelry that tells a story, evokes emotion, and connects with wearers on a nostalgic level.
Maintenance and Care of Ring Molds
In the realm of silver crafting and jewelry making, the longevity and quality of ring molds play a crucial role in ensuring impeccable final pieces. Proper maintenance and care of ring molds are essential aspects that deserve meticulous attention. By adhering to stringent maintenance practices, artisans can uphold the integrity of their molds, leading to consistent and flawless casting results. This section delves into the intricate details of maintaining and caring for ring molds, shedding light on the intricacies involved in preserving these vital tools.
Cleaning and Storage Tips
Proper Cleaning Methods:
When it comes to preserving the functionality and durability of ring molds, employing proper cleaning methods is paramount. Utilizing specialized cleaning solutions and techniques tailored for the specific material of the molds is a prudent approach. From gentle scrubbing to advanced cleaning processes, every method employed should aim to remove residual metal particles and surface impurities without compromising the integrity of the mold. Proper cleaning not only promotes the longevity of the molds but also enhances the precision of future castings, ensuring each jewelry piece retains its desired form.
Storing to Prevent Damage:
Equally vital is the aspect of storing ring molds to safeguard them against potential damage. Proper storage conditions involve shielding the molds from external factors such as moisture, heat, and corrosive elements. Implementing customized storage solutions, such as individual mold compartments or protective cases, can prevent scratches, warping, or oxidation. By meticulously organizing the storage space and adopting preventive measures, artisans can preserve the pristine condition of their ring molds, prolonging their lifespan and optimizing casting outcomes.
Ensuring Longevity of Ring Molds
Regular Maintenance Practices:
In the journey of silver crafting, the consistent application of regular maintenance practices is imperative for sustaining the performance and structural integrity of ring molds. These practices encompass routine inspections, lubrication of moving parts, and periodic refurbishment to address wear and tear. By integrating maintenance into the crafting workflow, artisans can detect early signs of mold degradation and undertake timely interventions to prevent potential casting flaws. The systematic execution of maintenance rituals fosters a culture of precision and excellence, elevating the overall quality of the crafted jewelry pieces.
Avoiding Common Mistakes:
Another critical facet of ensuring the longevity of ring molds lies in understanding and circumventing common mistakes that may jeopardize their durability. Mishandling, exposure to abrasive substances, or neglecting maintenance schedules are pitfalls that can compromise the efficacy of the molds. By cultivating an awareness of these pitfalls and embracing best practices, artisans can steer clear of inadvertent errors, safeguarding their investment in premium-quality ring molds. Proactive error avoidance strategies contribute to sustained mold performance, enabling artisans to pursue their creative vision with unwavering confidence.
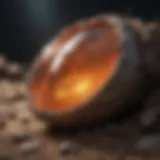
