Unveiling a Spectrum of Mold-Making Materials for Artifacts Collection Enthusiasts
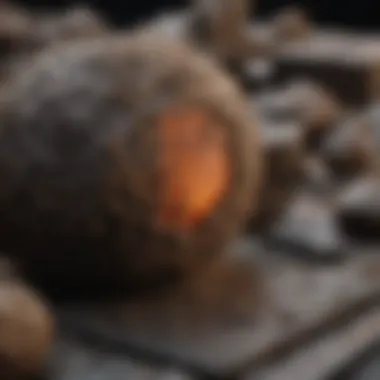

When delving into the realm of artifact collection, one critical aspect to consider is the selection of suitable mold-making materials. From versatile silicone to precise alginate, the options available for molding unique pieces are vast and diverse. This comprehensive guide is tailored to provide valuable insights for collectors aiming to preserve and replicate precious artifacts.
Rock and Fossil Identification
In the context of artifact collection, understanding the materials that constitute rocks and fossils is essential. The identification process involves discerning the various types of rocks and fossils, analyzing their distinct characteristics, and utilizing specialized tools for accurate identification.
Collecting Tips and Techniques
For collectors looking to enhance their artifact collection experience, adopting best practices for collecting is crucial. This section explores how to identify prime collecting sites, extract specimens safely, and offers insights on techniques to optimize the collecting process.
Preservation and Display
To safeguard the integrity of collected artifacts, employing effective preservation techniques is paramount. Discover proper storage methods that ensure the longevity of rocks and fossils, along with creative ideas for displaying these prized possessions in captivating ways.
Geological Insights
Exploring the geological aspects of rocks and fossils enhances the appreciation of these natural wonders. Gain insights into geological formations and processes, uncover the historical significance of various specimens, and delve into notable discoveries that have contributed to the field of geology.
Introduction
In the realm of artifact collection, understanding the significance of mold-making materials is paramount. This article delves deep into the diverse options available for creating molds, catering to the needs of collectors wishing to preserve and replicate valuable pieces. By exploring materials like silicone, alginate, plaster, and latex, enthusiasts can enhance their collection practices and ensure the longevity of their artifacts.
Understanding the Importance of Molds in Artifact Collection
Preservation of Irreplaceable Artifacts
Preserving irreplaceable artifacts is a crucial aspect of the artifact collection process. Mold-making plays a pivotal role in safeguarding the integrity and essence of these valuable pieces. By using molds, collectors can create detailed replicas that not only conserve the original artifact but also allow for further study and analysis without risking damage to the genuine item. The method ensures that the historical significance of artifacts is retained for generations to come, making it a popular choice among collectors seeking to protect their treasures.
Replication for Educational Purposes
Replication for educational purposes serves as another vital function of mold-making in artifact collection. By replicating artifacts through molds, researchers, students, and enthusiasts can study and learn from these historical objects without handling the originals. This educational tool enhances the understanding of various cultures, societies, and historical periods through hands-on engagement with replicated artifacts. The accessibility provided by mold-making for educational replication is a significant advantage, offering a safe and practical approach to learning about our past.
Basic Concepts of Mold Making
Types of Molds: Open vs. Closed
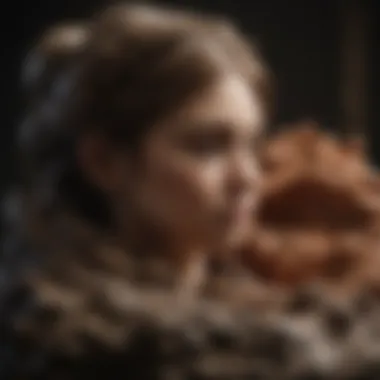
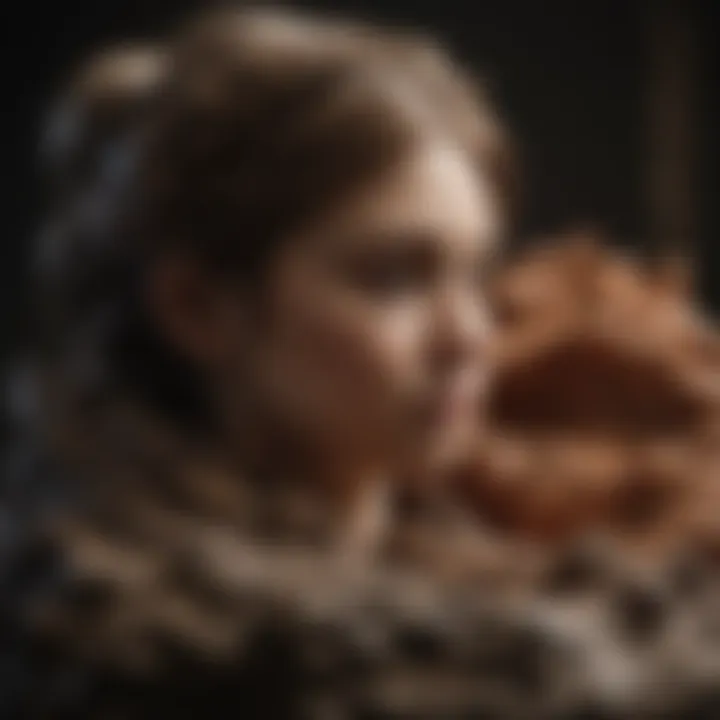
The choice between open and closed molds is a fundamental decision in the mold-making process. Open molds allow for easier removal of the artifact but may result in a less detailed cast. On the other hand, closed molds provide higher detail replication but can be challenging to demold certain shapes. The selection between these types depends on the complexity of the artifact and the desired level of detail in the final mold. Understanding the pros and cons of open and closed molds is essential for collectors aiming to create accurate reproductions of their artifacts.
Mold-Making Process Overview
The mold-making process involves several critical steps, including preparing the artifact and work area, applying the mold material, allowing it to cure, and eventually demolding the finished mold. Each stage requires precision and attention to detail to ensure an accurate replica of the original artifact. By following a systematic approach to mold-making, collectors can achieve consistent results and produce molds that capture the intricate features of their artifacts effectively. The process overview provides a roadmap for collectors, guiding them through the necessary procedures to create high-quality molds for their collections.
Silicone Molds
Silicone molds play a crucial role in the realm of mold-making for artifact collection. Their significance lies in the unparalleled advantages they bring to the table, offering collectors a versatile and reliable option for creating detailed replicas of valuable artifacts. Silicone molds stand out for their flexibility, durability, and ease of use, making them a preferred choice for artisans and collectors alike.
Advantages of Silicone for Mold Making
Flexibility and Durability
Flexibility and durability are two pivotal characteristics that set silicone molds apart in the mold-making process. The flexibility of silicone allows for easy removal of the mold from intricate artifact surfaces, ensuring that even the most delicate details are captured accurately. Moreover, the durable nature of silicone ensures that the molds can be used repeatedly without compromising on quality, making them a cost-effective and efficient choice for artifact replication.
High Level of Detail Replication
Silicone molds excel in replicating high levels of detail with precision and accuracy. This ability to capture intricate details makes silicone an ideal choice for molding artifacts with complex shapes or designs. The flexibility of silicone enables it to reproduce even the smallest features of the original artifact, ensuring that the replica closely mimics the original piece in every aspect.
Ease of Use and Reusability
One of the standout advantages of silicone molds is their ease of use and reusability. The straightforward mixing and pouring process, coupled with the flexibility of silicone, make it user-friendly for both experienced artisans and beginners. Additionally, silicone molds can be reused numerous times without experiencing degradation in quality, providing a sustainable and practical solution for artifact collectors.
Steps for Creating Silicone Molds
Preparation of Artifact and Work Area
Before embarking on the silicone molding process, proper preparation of the artifact and work area is essential. Cleaning the artifact to remove any dirt or debris ensures a smooth mold-making process. Additionally, setting up a clean and organized work area minimizes the risk of contamination and ensures a successful molding outcome.
Application and Curing Process
The application and curing process of silicone molds involves carefully pouring the silicone mixture over the prepared artifact. The mixture is then left to cure according to the manufacturer's instructions, typically forming a flexible and detailed mold. Once cured, the mold can be carefully removed to reveal a precise replica of the original artifact, ready for casting or preservation.
Alginate Molds
Unique Properties of Alginate for Mold Making
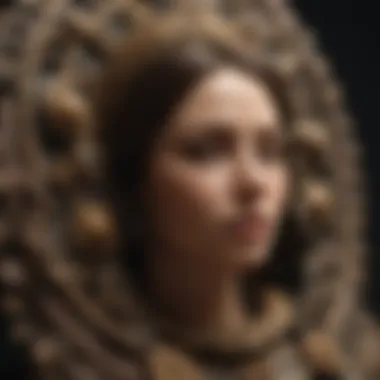
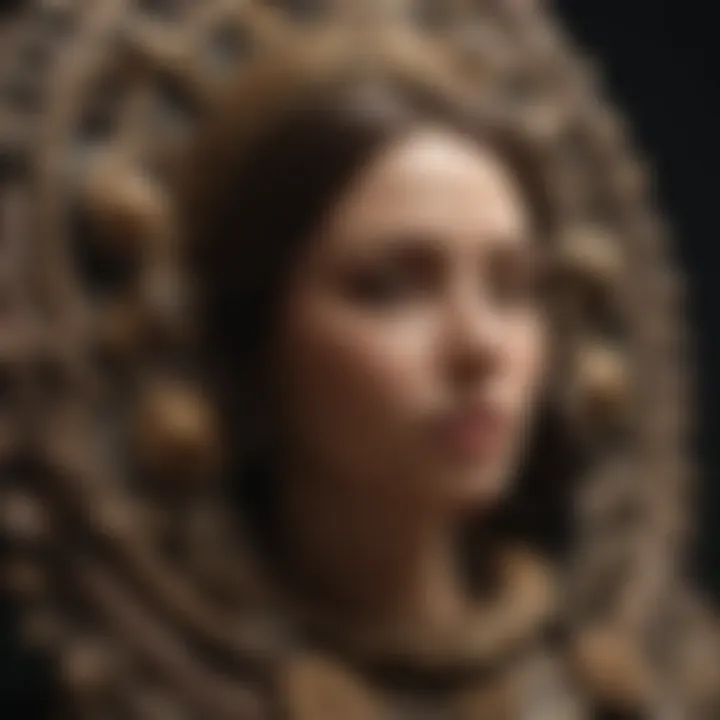
Ideal for Quick Impressions: Alginate molds excel in capturing fine details swiftly, making them ideal for capturing intricate textures and contours with remarkable accuracy. This characteristic of Alginate molds contributes significantly to the efficiency of creating impressions for preservation or replication purposes. The quick-setting nature of Alginate ensures that even delicate artifacts can be replicated without the risk of damage, making it a popular choice among collectors seeking high-detail molds.
Safe for Sensitive Artifacts: The inherent gentle nature of Alginate makes it a suitable option for molding sensitive or fragile artifacts. Its non-invasive and non-reactive composition ensures that even the most delicate items can be safely replicated without causing harm. This feature is crucial in artifact preservation, where maintaining the integrity of the original piece is of utmost priority.
Limited Reusability: While Alginate molds excel in detail replication and artifact preservation, their reusability is limited compared to other materials. The nature of Alginate lends itself to single or limited-use applications, making it important for collectors to plan their molding process efficiently. While the initial mold is highly detailed and accurate, multiple uses may result in loss of fidelity over time. Collectors must consider this limitation when opting for Alginate molds in their artifact replication endeavors.
Process of Making Alginate Molds
Mixing and Setting Time: The process of creating Alginate molds involves carefully mixing the Alginate powder with water to achieve the desired consistency. The quick-setting nature of Alginate requires collectors to work swiftly to create an impression before it solidifies. The mixing and setting time of Alginate molds is a critical aspect that impacts the quality and detail of the final mold, necessitating precision and quick execution.
De-Molding and Finalizing: Once the Alginate mold has set and captured the artifact's details, the de-molding process is initiated by gently removing the Alginate to reveal the replica. The finalizing stage involves inspecting the mold for any imperfections or air bubbles that may have formed during the setting process. Attention to detail during de-molding and finalizing ensures that the replicated artifact retains the original's features accurately, ready for casting or display.
Plaster Molds
In the context of mold-making materials for artifact collection, Plaster Molds play a crucial role due to their unique attributes and benefits. Plaster is favored for its versatility in capturing intricate details and its ability to preserve the original artifact's form accurately. Unlike other mold-making materials, plaster offers a balance between strength and ease of use, making it a popular choice among collectors and artisans.
Utilizing Plaster for Molding Techniques
Suitability for Casting
When discussing the suitability of Plaster for Casting, it becomes apparent that its smooth consistency and setting properties make it ideal for capturing even the most delicate features of an artifact. The key characteristic of Plaster in casting is its ability to create precise replicas with minimal distortion, ensuring an accurate representation of the original piece. This feature is highly beneficial for artifact collection as it allows for the faithful replication of intricate designs and textures. The unique advantage of Plaster in casting lies in its ability to produce high-quality molds that accurately reflect the fine details of the artifacts being preserved, making it a popular choice in this article.
Strength and Detail Preservation
The aspect of Strength and Detail Preservation in Plaster molds is essential for maintaining the integrity of the mold over time. Plaster molds are known for their durability and long-lasting properties, ensuring that the replicated artifacts retain their shape and structure effectively. The key characteristic of Plaster in preserving details lies in its ability to capture intricate patterns and textures without compromising on strength. This ensures that the molds created using plaster maintain the finest nuances of the original artifacts, showcasing a high level of accuracy and authenticity. While the strength of plaster is advantageous in preserving intricate details, its drawback may lie in the handling required due to its solid and sometimes fragile nature, posing challenges during the demolding process.
Creating Plaster Molds
Preparation and Pouring
The process of Preparation and Pouring in creating plaster molds involves meticulous attention to detail to ensure the best results. One key characteristic of this phase is the precise preparation of the mold-making area and the artifact to be molded. Proper surface treatment and alignment are crucial to avoid any imperfections or air bubbles that may affect the mold's quality. The advantage of this meticulous preparation is that it lays the foundation for a flawless mold that accurately captures all the features of the original artifact. However, one must be mindful of the timing and consistency of the plaster mixture to achieve optimal results, as any deviations can impact the final mold's quality.
Demolding and Finishing
Demolding and Finishing are critical steps in the plaster molding process that require delicacy and finesse. Key characteristics of these phases include the careful removal of the plaster mold from the artifact and the subsequent detailing or cleaning to enhance the mold's final appearance. The advantage of proper demolding and finishing techniques is the ability to preserve the mold's integrity and ensure that all details are accurately represented. However, it is essential to handle the demolding process with care to prevent any damage to the fragile plaster mold. Patience and precision are key during the finishing stage to address any imperfections and enhance the mold's overall quality, ensuring a refined and polished final product that faithfully replicates the original artifact.
Latex Molds

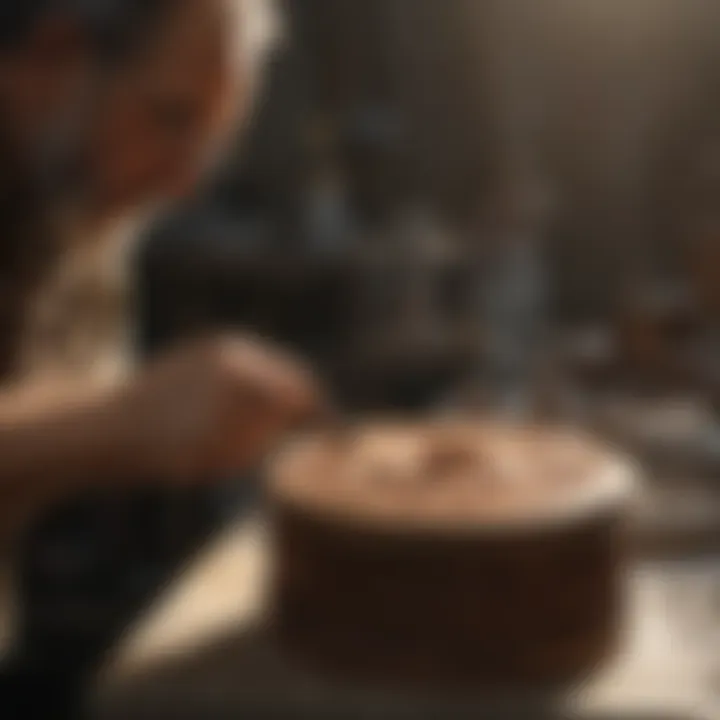
Latex molds play a crucial role in the realm of artifact collection, offering a distinct set of benefits and considerations that set them apart from other mold-making materials. The use of latex in mold making provides collectors with unparalleled versatility, reusability, and longevity, making it a top choice for those seeking detailed and durable artifact replication.
Benefits of Latex in Mold Making
Versatility for Various Shapes:
Latex molds stand out for their exceptional versatility in capturing intricate shapes and textures. This feature enables collectors to replicate a wide range of artifacts with precision and detail, preserving the essence of each piece with accuracy. The ability of latex molds to conform to unique forms and contours makes them a popular choice among artifact enthusiasts looking to recreate even the most complex of items. The flexibility of latex allows for seamless molding of irregular shapes and surfaces, ensuring a high level of fidelity in the reproduction process. This adaptability ensures that collectors can faithfully replicate the essence of each artifact, making latex molds a valuable asset in the preservation and display of historical items.
Reusability and Longevity:
The reusability and longevity of latex molds further solidify their position as a preferred mold-making material. Unlike many other mold-making substances, latex molds can be used multiple times without compromising the quality of the casts. This attribute not only enhances the cost-effectiveness of using latex but also ensures that collectors can reproduce artifacts consistently over time. Additionally, the durability of latex molds ensures that they can withstand the rigors of the casting process, maintaining their integrity through multiple uses. Collectors benefit from the longevity of latex molds, as they offer a reliable and enduring solution for artifact replication that can endure repeated casting without diminishing in quality.
Steps to Craft Latex Molds
Coating and Building Layers:
The process of creating latex molds begins with coating the artifact with layers of liquid latex, building up the mold thickness gradually. This step is crucial in ensuring that the mold captures all the intricate details of the original artifact, preventing any inconsistencies or air bubbles that may affect the casting process. By coating the artifact systematically and allowing each layer to dry before applying the next, collectors can create a robust mold that faithfully replicates every nuance of the original piece.
Curing and De-Molding:
Once the latex layers have been applied and dried, the mold is cured to strengthen its structure and prepare it for casting. Curing typically involves allowing the mold to rest for a specific period, ensuring that it reaches optimal consistency for casting. After the curing process is complete, the mold is carefully demolded to reveal the negative impression of the artifact. This step requires precision and care to avoid damaging the mold and ensures that it remains intact for future use. By following the proper de-molding procedures, collectors can extract the mold successfully, readying it for the casting phase and ensuring that all details are captured accurately.
Conclusion
Choosing the Right Mold-Making Material
Considerations for Artifact Type
When discussing Considerations for Artifact Type, it is essential to analyze the specific nuances and intricacies of each material in relation to the artifacts being molded. Understanding the properties of the artifact, such as its shape, texture, and fragility, is paramount in selecting the appropriate mold-making material. For instance, silicone molds are ideal for capturing intricate details on robust artifacts, while alginate may be favored for its quick impression capabilities on delicate objects. Balancing these considerations ensures that the chosen material aligns perfectly with the requirements of the artifact, ultimately enhancing the molding process.
Balancing Detail Replication and Ease of Use
The careful equilibrium between Detail Replication and Ease of Use is a crucial aspect when deliberating on mold-making materials. Achieving a high level of detail replication while maintaining user-friendliness is a delicate balance that influences the choice of material. Silicone molds excel in intricate detail reproduction, making them suitable for artifacts demanding precision. Conversely, alginate offers ease of use, enabling quick mold creation but with potential limitations on detail preservation. Understanding this balance enables collectors to make informed decisions based on the specific requirements of their artifact projects.
Further Exploration and Experimentation
Continuous Learning in Mold Making
Continuous Learning in Mold Making embodies the essence of growth and improvement within the realm of mold creation. Embracing new techniques, materials, and advancements ensures that collectors enhance their skills and expand their capabilities in artifact replication. This aspect encourages a proactive approach to learning, encouraging experimentation and innovation in mold-making practices to refine the replication process further.
Pushing Boundaries in Artifact Replication
The concept of Pushing Boundaries in Artifact Replication delves into the exploration of unconventional methods and creative approaches to mold creation. By challenging traditional practices and venturing into uncharted territories, collectors can push the limits of artifact replication to achieve unique and novel outcomes. This facet inspires creativity and ingenuity, fostering a dynamic environment where boundaries are constantly expanded and artistic innovation thrives in the realm of artifact collection.
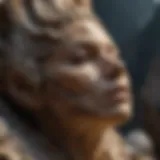
