Mastering the Art of Sand Casting Mold Creation: A Comprehensive Guide
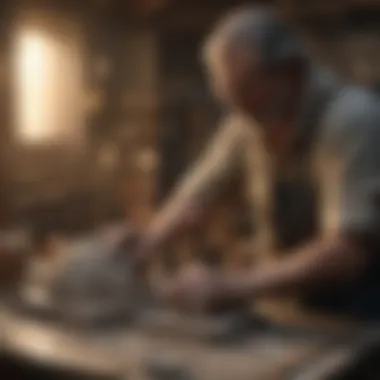
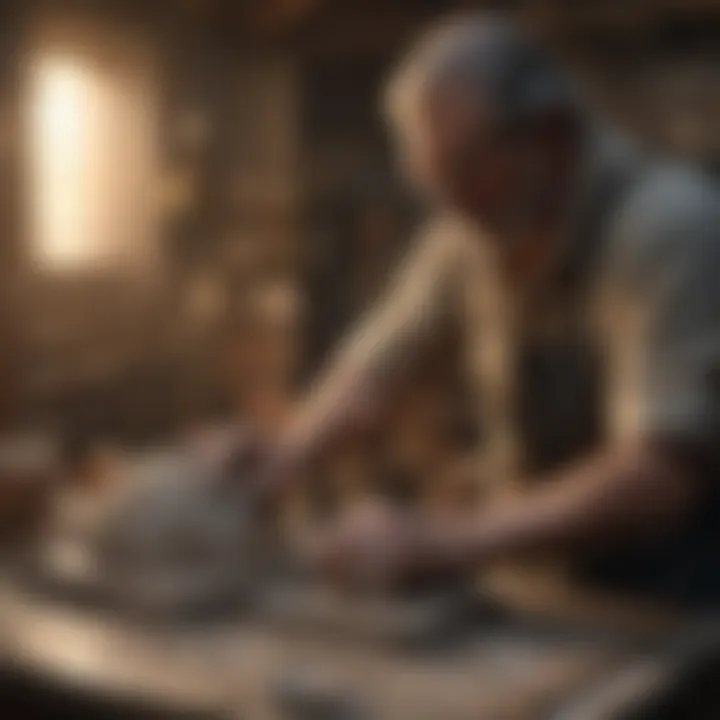
Rockabb and Fossil Identadicduon
Shaking hands with the world of sand casting molds, let us dig into the bedrock of knowledge surrounding rock identification and fossil exploration. Categorized into various types, rocks and fossils offer a glimpse into the Earth's history. Specific characteristics, often subtle and intriguing, can aid in distinguishing one specimen from another. Utilizing specialized tools can magnify the process and unearth hidden details that might elude the untrained eye. Enthusiasts are urged to delve further, as each discovery promises to narrate a unique tale of the Earth's evolution. noDBeping deeer into the arcana of sand casting molds, identifying rocks and fossils requires a discerning eye for detail. The quest involves unraveling the diverse types that constitute the Earth's crust - from sedimentary layers with their time-worn elegance to the fiery metamorphic rocks forged under immense pressure and heat. Fossils, frozen in time, whisper stories of ancient life forms and ecosystems long past. Their identification demands a keen understanding of geology and paleontology, as well as a touch of intuition to discern the fine nuances that differentiate one specimen from another. MissttypeEmbracing the tools of the trade is essential when embarking on a journey to identify rocks and fossils. Magnifying lenticulars can reveal intricate textures and mineral compositions hidden to the naked eye. Chisels and hammers come to play in the careful extraction of specimens without compromising their integrity. Brushes delicately whisk away soil and debris, unveiling the true beauty that lies beneath. The synergy between enthusiast and tool is crucial in unlocking the mysteries concealed within each rock and fossil, making every discovery a momentous occasion.
Collecting Tips and Techniques
Transitioning from identification to collection, enthusiasts are beckoned to explore the best practices in harvesting rocks and fossils from their natural habitats. Prime collecting sites, shrouded in geological wonder, await the discerning eye. Locating these gems requires a blend of knowledge and intuition, often leading collectors on thrilling adventures through rugged terrains and ancient landscapes. Safety reigns supreme, guiding each extraction process to ensure the well-being of both collector and specimen. Trekking deeper into the realm of collection, attaining rocks and fossils entails finesse and respect for their origins. Best practices emphasize minimal intrusion into delicate ecosystems, advocating for sustainable methods that leave minimal impact. Extracting specimens demands precision and care, lest the treasures crumble under reckless handling. Each collected piece carries within it a narrative of the Earth's history, awaiting liberation from its rocky embrace to tell its story to the world.
Preservation Chrisplaysyn and Deal-stat
Crossing the bridge between collection and preservation, enthusiasts are faced with the challenge of safeguarding their precious acquisitions for posterity. Techniques vary, from meticulous cleaning to strategic storage solutions that prevent deterioration and ensure longevity. Preserving rocks and fossils demands a delicate touch and thorough knowledge of the materials at hand. Creative displays offer a glimpse into the aesthetic appreciation of these geological wonders, turning collections into miniature museums that narrate tales of eras long forgotten. Navigating the labyrinth of conservation, preserving rocks and fossils demands a fusion of art and science. Implementing appropriate storage methods safeguards specimens from environmental harm, ensuring they retain their pristine condition for generations to come. Creative displays breathe life into collections, transforming them into visual narratives that inspire awe and curiosity. Each exhibit tells a unique story of the Earth's past, inviting viewers to embark on a journey through geological time and unravel the mysteries held within each fragment.
Geological Insights
Delving into the depths of geological insights, enthusiasts uncover the intricate formations and processes that have shaped our planet over millennia. Geological formations, etched by the hands of time, bear witness to ancient upheavals and transformations that have sculpted the landscapes we see today. The historical significance of rocks and fossils transcends mere aesthetics, offering a portal into bygone eras and the diverse life forms that once roamed the Earth. Notable discoveries in the field continue to fuel scientific inquiry, unveiling new chapters in Earth's tumultuous history. Embarking on a voyage of discovery, geological insights unveil the secrets of the Earth's past etched intricately in rocks and fossils. Exploring the historical significance of geological formations illuminates the interconnectedness of natural processes and the evolution of life on Earth. Notable discoveries stand as milestones in scientific progress, shedding light on enigmatic puzzles and expanding our understanding of the world around us. Each revelation serves as a testament to the enduring allure of rocks and fossils, beckoning enthusiasts to delve deeper into the annals of Earth's history.
Introduction
Crafting a Sand Casting Mold is a meticulous process that requires attention to detail and expertise. This guide aims to delve deep into the intricate art of creating sand casting molds, providing enthusiasts and experts with a comprehensive understanding of the craft. By discussing the essential elements, considerations, and benefits of sand casting mold creation, this article serves as a valuable resource for individuals looking to enhance their expertise in this field.
Understanding Sand Casting
Sand casting is a versatile technique widely used in various industries for its unique properties and benefits. Let's explore the definition and concept of sand casting, shedding light on why it remains a preferred choice for many craftsmen.
Definition and Concept
The definition and concept of sand casting revolve around the process of creating intricate molds using sand as the primary material. This cost-effective method enables craftsmen to replicate detailed designs with ease, making it a popular choice for producing complex metal parts. The unique characteristic of sand casting lies in its ability to accommodate a wide range of shapes and sizes, providing versatility to manufacturers and artisans. While it offers flexibility and cost-efficiency, challenges such as pattern wear and sand inclusion should be carefully managed to ensure optimal results.
Applications in Various Industries
Sand casting finds extensive applications across diverse industries, including automotive, aerospace, and art. Its versatility allows for the production of various components such as engine blocks, sculptures, and industrial machinery parts. The key characteristic of sand casting lies in its ability to cater to both small-scale art projects and large-scale industrial production. Despite its advantages in versatility and cost-effectiveness, sand casting may pose challenges in achieving intricate details for highly precise components.
Significance of Molding in Sand Casting
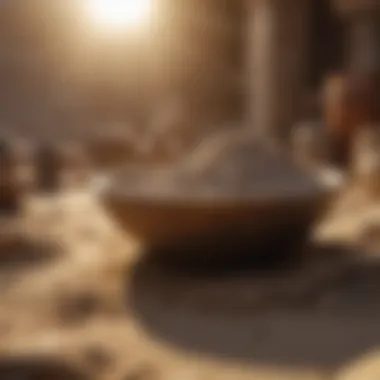
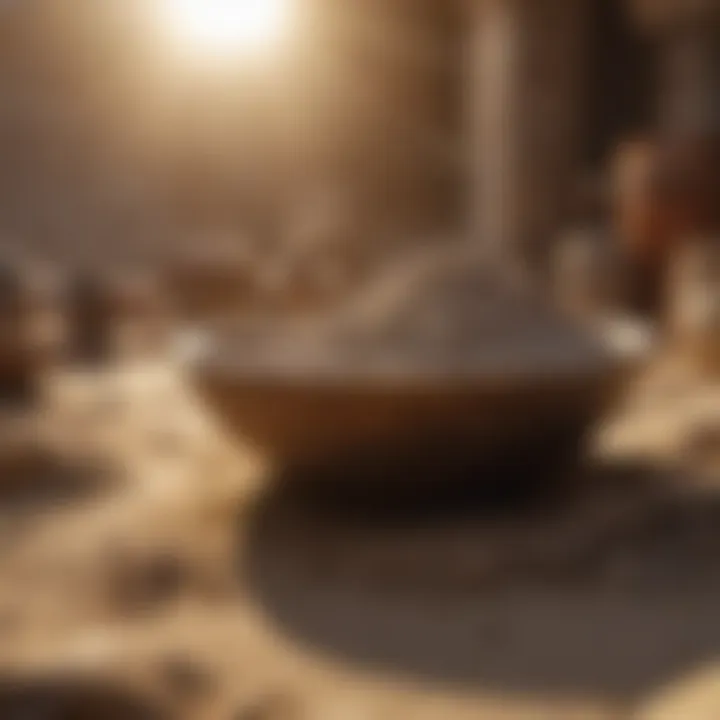
Molding plays a crucial role in ensuring the quality and precision of sand casting products. Let's explore two vital aspects - Ensuring Precision and Detail and Achieving Quality Finished Products.
Ensuring Precision and Detail
The precision and detail in sand casting molds are paramount to achieving accurate final products. Molding ensures that intricate designs and complex geometries are reproduced with fidelity, allowing craftsmen to maintain consistent quality standards. The unique feature of precision molding lies in its ability to capture fine details and subtle contours effectively, enhancing the overall aesthetics and functionality of the casted parts. Despite its advantages in replicating complex forms, precision molding may require meticulous attention to tooling and material selection to mitigate potential defects.
Achieving Quality Finished Products
The quality of finished products in sand casting relies heavily on the molding process. By adhering to rigorous molding standards, craftsmen can enhance product quality, durability, and performance. Achieving quality finished products involves meticulous sand preparation, proper compaction techniques, and strategic gating and riser design. The unique feature of quality molding is its emphasis on defect prevention and material integrity, ensuring that each casted part meets the desired specifications reliably. However, challenges such as porosity and surface defects may arise, necessitating comprehensive quality assurance measures throughout the molding stages.
Materials and Tools Required
Sand casting molds necessitate an array of materials and tools to execute the intricate process successfully. The selection of these components is paramount to the quality and precision of the final product. The choice of sand plays a crucial role in forming the mold, determining its strength and detail reproduction. Furthermore, the tools used in the molding process, such as the pattern for mold design and the rammer and strike-off bar, are indispensable for shaping the sand and ensuring the mold's integrity. Each material and tool serves a specific purpose, contributing to the overall success of the sand casting process.
Selection of Suitable Sand
Types of Sand for Molding
When delving into the realm of sand casting, understanding the various types of sand available for molding is essential. Different sands possess distinct characteristics that impact the mold's properties. For instance, silica sand is a prevalent choice due to its heat resistance and stability during the casting process. Its fine granules allow for intricate detail capture in the mold, ensuring the fidelity of the final product. Conversely, chromite sand offers superior thermal performance, ideal for high-temperature applications, making it a preferred option for certain molding requirements.
Characteristics of Ideal Molding Sand
The characteristics of an ideal molding sand are pivotal in achieving optimal casting results. A suitable molding sand should exhibit high refractoriness, enabling it to withstand the intense heat of molten metal without deforming. Additionally, excellent collapsibility is crucial for easy removal of the pattern after molding. Other essential traits include good permeability to facilitate gas escape during casting and proper bonding capabilities to maintain the mold's shape. By selecting a molding sand that meets these criteria, the casting process can proceed smoothly, resulting in high-quality finished products.
Essential Tools for the Process
Pattern for Mold Design
The pattern used for mold design serves as a blueprint for shaping the sand into the desired form. It guides the placement and compaction of the sand, ensuring the accurate reproduction of the intended product. A well-designed pattern facilitates the creation of intricate molds with precise details, crucial for achieving the desired finished product quality.
Rammer and Strike-Off Bar
In the molding process, the rammer and strike-off bar are indispensable tools for compacting the sand and leveling it to create a smooth surface. The rammer aids in densely packing the sand around the pattern, reducing the likelihood of voids or imperfections in the mold. On the other hand, the strike-off bar provides a flat, even surface by removing excess sand, enhancing the mold's consistency and finish. These tools work cohesively to ensure uniform compaction and structural integrity throughout the molding process, contributing to the overall quality of the final casting.
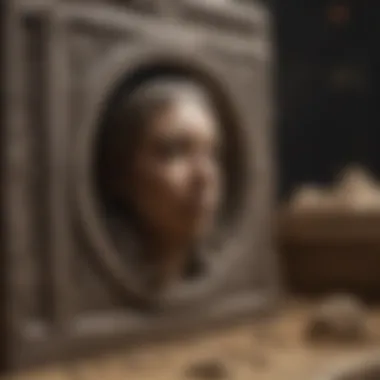
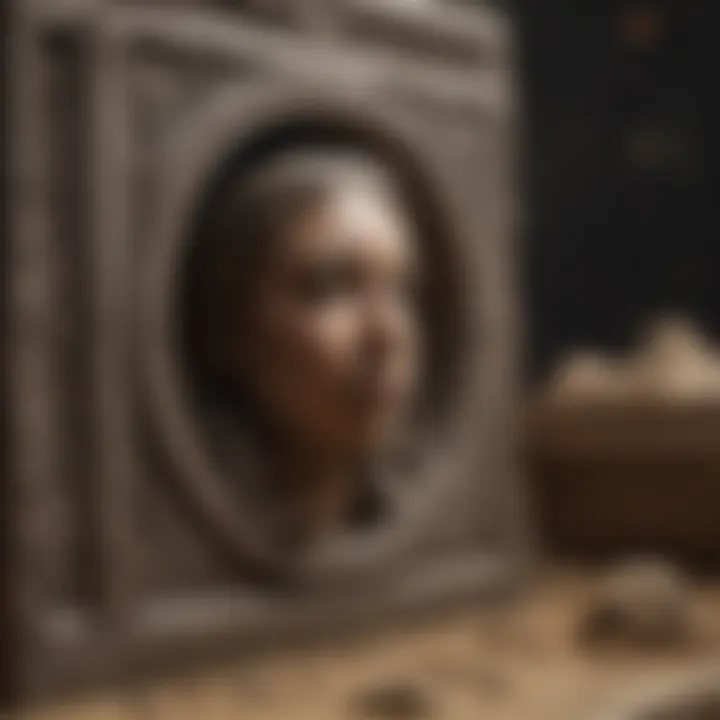
Preparing for Molding
In the intricate process of crafting a sand casting mold, the preparation phase holds paramount significance. Before delving into the molding itself, meticulous attention to detail in preparing for molding ensures the success of the overall sand casting process. It involves a careful consideration of factors that directly influence the quality and integrity of the final casting. Understanding the importance of this preparatory phase allows craftsmen to streamline their efforts towards achieving precision and excellence in the mold formation.
Pattern Alignment and Setup
Ensuring Correct Positioning
The aspect of ensuring correct positioning within the pattern alignment and setup stage is crucial for several reasons. This specific step determines the exact placement of the pattern within the mold, directly impacting the final outcome of the casting. By meticulously aligning and positioning the pattern, craftsmen can eliminate potential errors or inconsistencies in the mold formation process. This careful consideration significantly enhances the chances of producing high-quality castings with intricate details and precise dimensions.
Securing the Pattern in Place
Securing the pattern in place is a fundamental aspect of the molding process as it ensures stability during the subsequent steps. By firmly securing the pattern within the mold, craftsmen minimize the risk of displacement or shifting that could result in defects in the final casting. This reliable fixation guarantees that the mold retains its intended shape and structure throughout the pouring and solidification stages. While this step may seem mundane, its role in maintaining the integrity of the mold cannot be understated.
Establishing Gating and Riser Design
In sand casting, gating and riser design play a crucial role in optimizing the overall metal flow and preventing defects in the casting. Efforts to design efficient gating systems enable smooth metal flow during the casting process, ensuring uniform filling of the mold cavity. This optimization reduces the likelihood of defects such as incomplete castings or shrinkage cavities, improving the overall quality of the final product.
Optimizing Metal Flow
Optimizing metal flow through strategic gating design is essential for achieving consistent and defect-free castings. By controlling the flow of molten metal into the mold cavity, craftsmen can prevent issues such as turbulence or improper filling that may lead to defects. This meticulous consideration of metal flow optimization enhances the casting process's efficiency and results in high-precision components with minimal surface imperfections.
Preventing Defects in Casting
One of the primary objectives of establishing an effective gating and riser design is to prevent defects in the casting. By strategically placing gates and risers, craftsmen can eliminate common casting defects such as porosity, shrinkage, or misruns. This preventive measure ensures that the final castings meet industry standards for quality and integrity, reducing the need for rework or refinishing. The meticulous attention to gating and riser design demonstrates a commitment to excellence in sand casting, enhancing the overall success of the molding process.
Creating the Mold
In the intricate process of sand casting, creating the mold stands as a pivotal stage, delineating the form and structure of the final casted product with utmost precision and accuracy. The significance of this phase lies in its ability to encapsulate the design intricacies envisioned by the craftsmen, bringing to life the desired shape and dimensions flawlessly. Attention to detail is paramount during mold creation, as any deviations or inconsistencies can result in defects or imperfections in the final casting. By focusing on key elements such as mold geometry, sand compaction, and gating design, artisans can lay the foundation for a successful casting process, ensuring that each piece meets the highest quality standards.
Sand Mixture Preparation
Mixing Sand and Additives
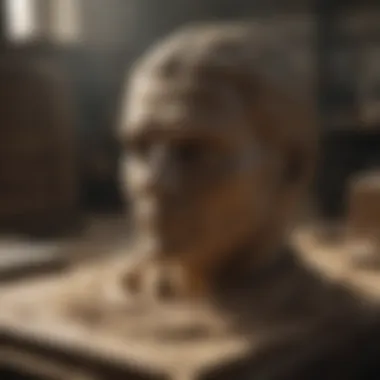
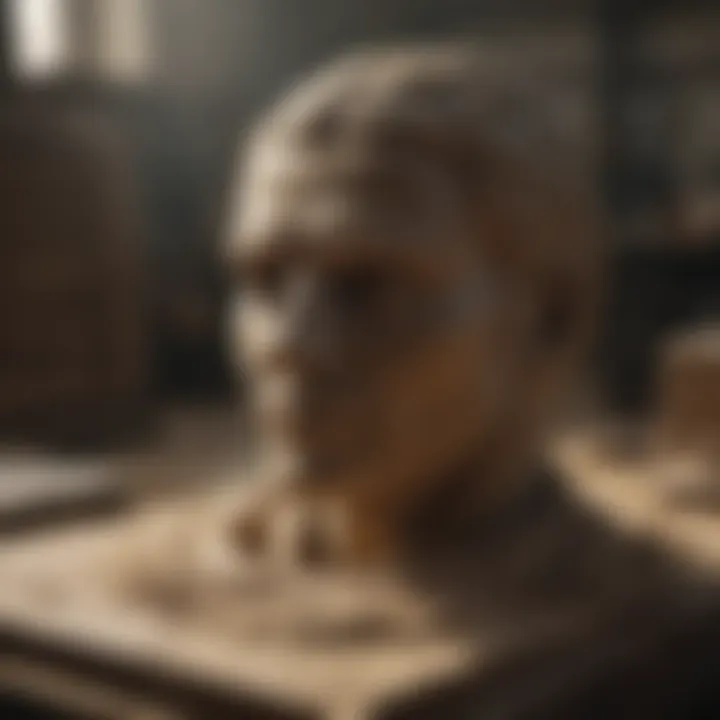
Mixing sand and additives is a critical aspect of sand casting mold creation, as it determines the mold's structural integrity and material properties. The combination of sand with additives such as clay, water, and binders plays a crucial role in enhancing mold strength, permeability, and thermal stability. The key characteristic of this process lies in achieving the optimal sand-to-additive ratio, ensuring that the mixture exhibits the right consistency for molding. By meticulously blending the components, craftsmen can create a homogeneous sand mixture that facilitates effective mold formation, enabling intricate patterns and designs to be accurately replicated.
Achieving the Desired Consistency
Achieving the desired consistency in the sand mixture is essential for ensuring uniform mold compaction and dimensional accuracy during the casting process. The consistency of the sand mixture affects its flowability, cohesion, and adhesion properties, directly impacting the mold's surface finish and detail reproduction. By adjusting the moisture content and additives' proportions, craftsmen can control the mixture's workability and strength, allowing for precise mold filling and compaction. Striking the right balance between moisture content and sand composition is crucial in achieving the desired mold consistency, enabling craftsmen to create molds that meet the specific requirements of each casting project.
Molding Techniques
Hand Packing vs. Machine Molding
The choice between hand packing and machine molding techniques significantly influences the efficiency and precision of the sand casting process. Hand packing offers artisans a hands-on approach to mold creation, allowing for intricate details and customization based on individual craftsmanship. In contrast, machine molding provides consistency and repeatability in mold production, ensuring uniform compaction and dimensional accuracy across multiple molds. The unique feature of hand packing lies in the artisan's ability to finesse intricate patterns and textures manually, while machine molding excels in producing large quantities of molds with consistent quality and efficiency.
Ensuring Uniform Compaction
Ensuring uniform compaction is essential in sand casting mold production to prevent defects such as porosity, shrinkage, and deformation in the final casted products. Uniform compaction guarantees consistent mold density and structural stability, reducing the risk of metal turbulence and non-fill defects during casting. By implementing techniques such as jolting, squeezing, or vibration, craftsmen can achieve uniform compaction throughout the mold, promoting metal flow optimization and minimizing casting flaws. The key aspect of uniform compaction lies in meticulous control of the compaction process, ensuring that each mold section receives equal pressure and support for optimal casting results.
Finishing Touches and Quality Checks
In the intricate art of crafting a sand casting mold, the segment dedicated to finishing touches and quality checks plays a pivotal role in ensuring the integrity and precision of the final product. By delving deep into this topic, enthusiasts and experts alike are equipped with the necessary knowledge to perfect their craftsmanship. Surface Finishing: Given its significance, the process of surface finishing holds paramount importance in the realm of sand casting. Smoothing and Leveling stands out as a crucial step within surface finishing, as it not only enhances the visual appeal of the mold but also contributes to the overall quality of the casting. The meticulous act of smoothing and leveling involves the careful removal of imperfections and irregularities on the mold's surface, ensuring a flawless end result. Craftsmen embrace this practice for its ability to refine the mold's texture and appearance, ultimately elevating the casting's quality. Despite requiring precision and patience, smoothing and leveling remains a favored technique due to its effectiveness in producing top-notch molds. Its unique feature lies in its ability to transform a rough surface into a polished masterpiece, showcasing the artisan's dedication to excellence. Trimming Excess Material: Complementing the process of smoothing and leveling is the essential step of trimming excess material. This phase is crucial in achieving the desired dimensions and contours of the mold. By carefully eliminating surplus material, craftsmen refine the mold's shape and structure, ensuring it aligns with the intended design. Trimming excess material is a preferred choice in this context due to its role in fine-tuning the mold with precision and skill. Its distinctive feature lies in its capability to enhance the mold's intricacies by removing any superfluous elements. The advantages of trimming excess material in this article are apparent, as it enables craftsmen to create molds that meet their exact specifications.
Inspection and Testing
As the sand casting mold nears completion, the stages of inspection and testing come to the forefront, embodying the commitment to quality and excellence in craftsmanship. Ensuring Mold Integrity: The meticulous process of ensuring mold integrity entails thorough assessments to guarantee that the mold retains its structural stability and integrity throughout the casting process. This element is crucial as any flaws or weaknesses in the mold could jeopardize the final product's quality. Craftsmen value this step for its ability to identify and rectify any potential issues that may compromise the mold's performance. The unique feature of ensuring mold integrity lies in its proactive approach to preempting casting defects, thereby upholding a superior standard of quality. Quality Assurance Measures: Alongside ensuring mold integrity, the implementation of quality assurance measures further solidifies the commitment to excellence in sand casting. These measures encompass a range of protocols aimed at verifying the mold's conformity to desired standards. Craftsmen employ quality assurance measures to validate the mold's precision, durability, and compatibility with the casting process. The key advantage of incorporating quality assurance measures into this article lies in its role in affirming the quality and reliability of the final mold. By adhering to stringent quality checks, craftsmen uphold the craft's legacy of precision and meticulousness.
Conclusion
Crafting a sand casting mold is a meticulous process that requires attention to detail and precision. In this comprehensive guide, we have delved into the intricate steps involved in creating a mold that is essential for successful sand casting. Each stage from selecting the materials to the finishing touches plays a crucial role in ensuring the quality and integrity of the final product. By following the guidelines laid out in this article, artisans and professionals can hone their skills and achieve excellence in sand casting.
Achieving Excellence in Sand Casting
Achieving excellence in sand casting is a journey that involves continuous improvement and innovation. The drive to constantly refine techniques and processes is a hallmark of top-tier craftsmanship in this field. Continuous improvement allows craftsmen to iterate on their methods, experiment with new approaches, and ultimately enhance the quality of their castings. This dedication to refinement paves the way for superior results and sets a high standard in the art of sand casting.
Continuous Improvement and Innovation
Continuous improvement and innovation are central to advancing the art of sand casting. By constantly evaluating and adapting techniques, craftsmen can stay ahead of the curve and push the boundaries of what is achievable in molding. The key characteristic of continuous improvement is its iterative nature, where small changes accumulate to bring about significant enhancements in the final product. This approach fosters a culture of learning and growth within the industry, driving sand casting to new heights of excellence.
Honoring the Craftsmanship of Molding
Honoring the craftsmanship of molding is a tribute to the skill, dedication, and artistry that goes into creating a sand casting mold. This aspect underscores the deep-rooted tradition and expertise passed down through generations of mold-makers. The key characteristic of honoring craftsmanship lies in recognizing the intricate workmanship and artful precision required in mold-making. It celebrates the synergy between tradition and innovation, honoring the legacy of master craftsmen while embracing modern advancements in materials and techniques. By paying homage to the legacy of molding, artisans uphold a standard of excellence that resonates with enthusiasts and industry professionals alike.