Crafting Molds for Casting: A Comprehensive Guide
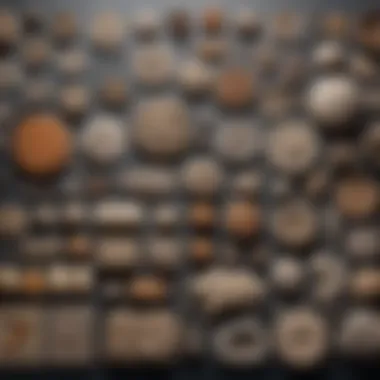
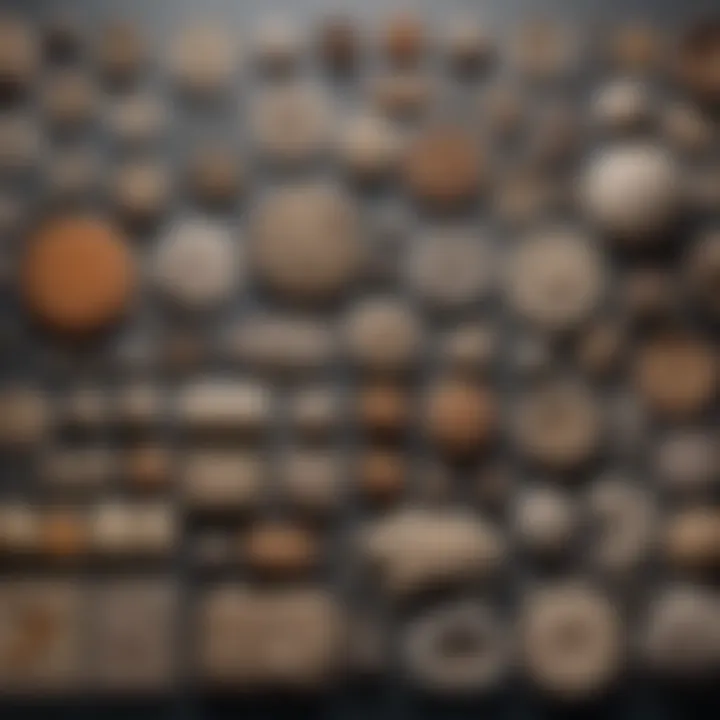
Intro
Creating molds for casting is a precise endeavor that appeals not just to artisans and manufacturers, but to collectors and enthusiasts in geological fields as well. This process holds significance, particularly when it comes to accurately recreating the intricate details of fossils and rocks. A well-crafted mold can capture the essence of a specimen, preserving it for future generations or sharing it with others who share a passion for geological wonders.
Through this guide, we will navigate the complexities of mold-making, considering the unique needs of collectors and those passionate about geology. By dissecting the methods, materials, and best practices used in crafting molds, we aim to empower you with the knowledge required to effectively produce your own molds. Let's dive headfirst into the first essential area of knowledge for a successful mold-making journey.
Rock and Fossil Identification
Before embarking on any mold-making adventure, it’s crucial to recognize what you’re working with. Identifying the types of rocks and fossils is key to ensuring accuracy in replication. In this section, we shall explore how to pinpoint various geological specimens and some tips that can enrich the process.
Types of Rocks and Fossils
Rocks generally fall into three broad categories: igneous, metamorphic, and sedimentary. Each category offers unique characteristics worth noting:
- Igneous Rocks: These form from cooled magma or lava. Common examples include granite and basalt.
- Metamorphic Rocks: Formed under heat and pressure, these include schist and marble that show distinctive layering.
- Sedimentary Rocks: Created from the accumulation of sediments, these often contain fossils and include limestone and sandstone.
Fossils, on the other hand, often capture the remnants of living organisms and can generally be seen in sedimentary rocks. They can be as small as tiny shells or as expansive as dinosaur bones.
Characteristics to Look For
When identifying rocks or fossils, consider the following features:
- Color: The hue can hint at mineral composition.
- Texture: Whether smooth or rough can indicate its formation process.
- Pattern: Look for layering or unique designs, as these may suggest fossilization.
Tools for Identification
Equipping yourself with the right tools can make identification easier:
- Hand Lens or Magnifier: Useful for examining fine details.
- Geological Hammer: This helps to chip away layers and reveal hidden specimens.
- Field Guide: A concise geological guide can assist in recognizing various forms.
"When you know what to look for, the world becomes a treasure trove of geological discovery."
Collecting Tips and Techniques
Having identified your specimens, the next step is knowing how to collect them properly. This ensures that you preserve these geological wonders while minimizing damage.
Best Practices for Collecting
When collecting, it’s paramount to respect the environment:
- Avoid Over-Collecting: Take only what you need to maintain ecological balance.
- Leave No Trace: Ensure your collecting site remains as undisturbed as possible.
Locating Prime Collecting Sites
Research is your best friend when it comes to finding fruitful collecting grounds. Areas known for unique geological formations are excellent starting points. Look for regions where recent geological activity could expose new specimens, such as:
- Riverbanks: Erosion often reveals new finds.
- Construction Sites: These can occasionally expose layers of rock that have not been seen for years.
How to Safely Extract Specimens
Using appropriate techniques is crucial in preserving both the specimen and the nearby environment. Here are a few techniques:
- Digging: Use shovels very carefully to avoid unnecessary breakage.
- Chiseling: A good technique for fossils embedded in rock without compromising their structure.
Preservation and Display
Once specimens are collected, preserving them is vital to maintain their integrity and beauty for future enjoyment. Good practices can lead to a lasting collection.
Techniques for Preserving Rocks and Fossils
Preservation methods may vary based on the type of specimen:
- Drying: Ensures moisture does not lead to decay.
- Chemical Treatments: Some fossils may need specific preservatives to enhance durability.
Proper Storage Methods
Safe storage solutions will help keep your collection in prime condition. Consider:
- Acid-Free Boxes: Protect against deterioration due to chemicals in regular materials.
- Temperature and Humidity Control: Maintain stable climate conditions to prevent damage.
Creative Display Ideas
Displaying your collection not only showcases your passion, but can also educate others. Innovative display techniques include:
- Shadow Boxes: An aesthetic way to arrange specimens with background details.
- Glass Cases: Provide protection while letting the beauty shine through.
Geological Insights
Understanding geological processes helps you appreciate your collection on a deeper level. Knowledge enriches the collecting experience.
Geological Formations and Processes
Knowing how certain geological formations occurred enhances understanding of your finds:
- Plate Tectonics: This process shapes Earth’s surface leading to unique rock formations.
- Erosion and Weathering: These forces create fascinating fossils and rock examples.
Historical Significance of Rocks and Fossils
Each specimen carries a story. Fossils, in particular, provide a window into ancient ecosystems. Notable discoveries continuously reshape our understanding of Earth’s history.
Notable Discoveries in the Field
Remaining updated on the latest discoveries keeps your knowledge fresh. Research famous finds; for instance, the discovery of Archaeopteryx, which bridges reptiles and birds, exemplifies how fossil finds can answer profound questions.
This guide serves not merely as a manual but as a gateway to the intricate world of mold-making and geological collecting. Dive deeper and explore every facet, ensuring your journey is as enriching as the specimens you conserve.
Understanding Molds and Casting
Molds play a crucial role in the casting process, especially for those interested in preserving geological specimens. The very essence of a good mold can be likened to the foundation of a sturdy house; without it, the final work lacks integrity and precision. For collectors who want to showcase their finds, the creation of molds is not just an art—it’s a science. Understanding the nuances involved in mold-making can vastly improve the quality of the castings produced, leading to more detailed representations of rocks and fossils.
When it comes to geological collecting, molds ensure that every minute detail of a specimen is captured. Whether one is aiming for a simple plaster cast or a more intricate resin mold, each type has its own merits and applications. Moreover, one must consider factors such as durability, flexibility, and ease of use while choosing the right mold materials. The implications of these choices can significantly affect the end result, determining not just aesthetics but also how the cast performs in various conditions.
In summary, comprehending the principles of molds and casting is foundational for anyone engaged in geological collecting. This knowledge equips collectors with the tools to create authentic representations of their finds, thus enhancing their appreciation and understanding of the natural world.
Defining Molds in Casting
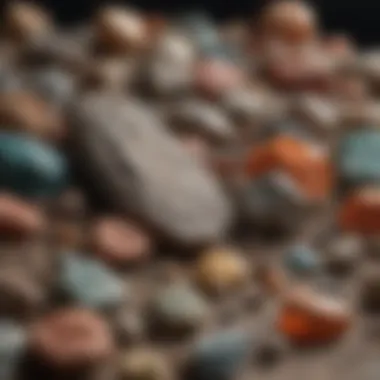
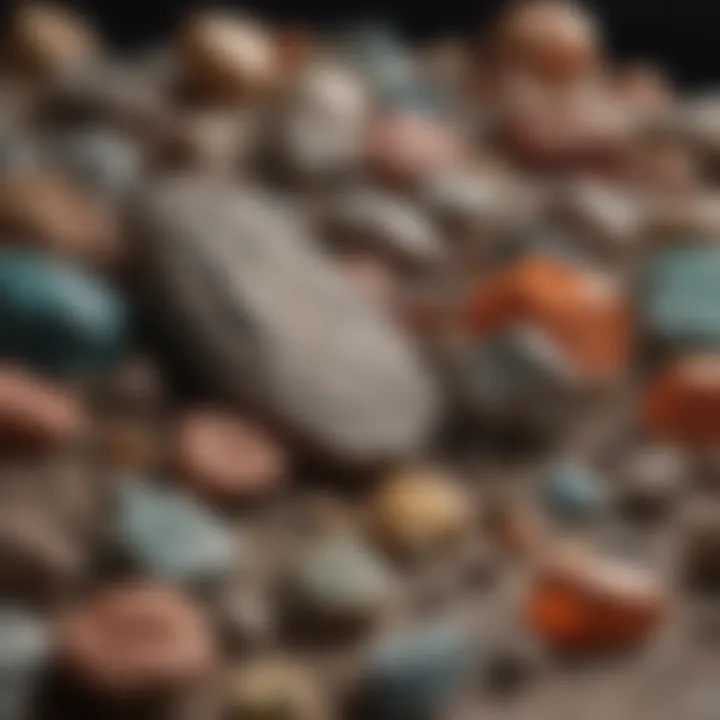
Molds in casting serve as the negative imprint from which replicas are produced. They are often created from the original specimen, capturing every ridge, groove, and irregularity down to the finest detail. Think of a mold as a well-worn glove. Just like the glove conforms perfectly to your hand, a mold takes the shape of the original item, allowing for an accurate reproduction.
Various types of molds exist, and they can be classified based on the materials used and the casting methods they support. Common examples include:
- Rigid molds: Typically made from materials such as plaster or metal, ideal for instances where durability is a must.
- Flexible molds: Often constructed from silicone rubber or latex, these are perfect for intricate designs as they easily release the finished cast without damaging details.
These molds can be single-use or reusable, with choices largely dependent on the complexity of the object and the desired level of detail.
Applications in Geological Collecting
The applications of molds in geological collecting are as diverse as the specimens themselves. For rock and fossil collectors, accurately reproducing specimens can be invaluable for various reasons:
- Preservation: Molds allow collectors to preserve rare or fragile specimens without risking damage through handling.
- Education: Reproductions can be used for teaching purposes, illustrating geology concepts without exposing the original specimen to wear and tear.
- Display: Beautiful, accurate casts can enhance display cases, allowing collectors to show off their finds in a way that minimizes risk but maximizes visibility.
- Customization: With molds, collectors can create tailored displays or artworks that represent personal interpretations of geological formations.
For instance, when a collector stumbles upon a striking fossil or mineral, having the ability to craft a mold means they can replicate that piece and share it with others, be it through exhibitions or online communities. In essence, the practice of mold-making becomes a bridge connecting personal passion with broader educational or aesthetic opportunities.
"Creating a mold isn't just a process; it's a journey of appreciation for the hidden beauty within nature's artifacts."
Engaging in this craft opens doors to a world of exploration and expression that goes beyond mere collection, ultimately fostering a deeper connection with the geological wonders around us.
Materials for Mold Making
When it comes to mold making, the right materials can make all the difference. This step is vital because it sets the foundation for the quality and durability of the castings you'll create later. By selecting appropriate mold-making materials, you'll ensure that your molds not only capture fine details but also stand the test of time and repeated use. With a variety of options available, each with its own characteristics and advantages, understanding these materials is crucial for achieving your desired results.
Types of Materials
Silicone Rubber
Silicone rubber stands out as a top pick for many when crafting molds. Its flexible nature allows molds to be liberated easily from the cast object. One of the key characteristics of silicone rubber is its resistance to heat and chemicals, making it suitable for a range of projects. Its unique feature is the ability to capture intricate details of an original object, which is particularly useful for geological specimens where fine textures matter.
However, silicone rubber can come at a steeper price compared to other materials. Budget-conscious enthusiasts might find that this is a significant consideration. Still, for those serious about durability and quality, the benefits outweigh the costs, allowing for a superior balance between detail retention and durability.
Latex Rubber
Latex rubber is another popular choice for crafting molds. Known for its elastic properties, it can stretch easily, making demolding a breeze. This characteristic can greatly reduce the chances of damaging delicate cast objects. Many hobbyists appreciate latex for being more budget-friendly.
However, one notable downside is its limited lifespan; over time, latex can lose its elasticity, particularly if it’s exposed to sunlight or heat too often. So, while it’s an affordable option, collectors should consider how frequently they plan to use their molds before resorting to latex.
Plaster
Plaster is often used in molds due to its accessibility and ease of use. It dries quickly and provides a solid structure, making it relatively straightforward for beginners. A key characteristic of plaster is its ability to take a variety of forms, adapting to different shapes and requiring little setup.
The downside of plaster, however, lies in its fragility once set. Heavy or intricate objects might crack or damage plaster molds, limiting their application in certain areas. This makes plaster a more suitable option for one-time castings or specific projects where durability isn't paramount.
Resin
Resin has carved out its niche in the mold-making landscape due to its versatility and strength. It comes in various types, including epoxy and polyurethane, each offering different features. One significant advantage of resin is its remarkable strength and durability, making it a great option for casting objects that will be frequently handled or displayed.
On the flip side, the complexity of working with resin—particularly its mixing ratios and curing times—can be daunting for beginners. Additionally, the cost of high-quality resin can add up quickly. If attention to detail and a deep understanding of the material aren’t parts of your toolkit yet, resin may require a learning curve.
Tools and Equipment
Mold Frames
Mold frames play a crucial role in the mold-making process. They provide important support, keeping the mold in its intended shape while materials cure. A key characteristic of mold frames is their ability to withstand the pressure of poured materials without deforming. Many makers discover that having a sturdy frame becomes essential to ensuring mold integrity throughout multiple uses.
While they can be found in a variety of materials, the most popular ones tend to be plastic or metal. The downside? Depending on the complexity of a mold, finding the right fit for your frame can sometimes be a bit of a hassle.
Mixing Tools
Having the right mixing tools can greatly influence your success in mold making. A sturdy container and a reliable stirring tool are essential for combining mold materials evenly. One key characteristic of mixing tools is that they come in various shapes and sizes, which can help creators tailor their mixing process to the amount and type of material being used.
However, attention must be paid to cleanliness; leftover residue in your mixing container can compromise future batches. So, it’s best to keep a dedicated set of tools just for mold making to avoid unexpected contaminants.
Measuring Instruments
When crafting molds, accuracy is of utmost importance, which makes measuring instruments indispensable. Utilizing precise measuring tools ensures that the proportions of materials mixed are correct, enhancing the overall quality of the mold. A key characteristic is their ability to measure in both metric and standard units, catering to different preferences.
It's worth noting that some users might overlook measuring instruments for the sake of speed, but poor measurements can lead to disastrous results. A tip for novices: invest in some quality measuring tools to streamline your process and achieve consistent outcomes.
Release Agents
To prevent casting materials from bonding to molds, using release agents is vital. They create a barrier between the mold surfaces and the material being cast. The key characteristic of effective release agents is their ability to be applied thinly and evenly, ensuring that they don’t interfere with the surface finish of the final product.
One downside to consider is that some release agents can leave behind residues that might affect the appearance of the casting. It’s advisable to test them on small samples before full application, ensuring compatibility with your chosen materials.
Planning Your Mold
Planning your mold is the cornerstone of creating a successful cast. Having a clear strategy not only speeds up the process but also enhances the final outcome, allowing you to showcase your findings in the best possible light. By making decisions ahead of time, you ensure that the mold fits your objectives, whether it’s for collecting or educational purposes.
Choosing What to Cast
The first step in planning your mold involves deciding on the specimen you want to replicate. This decision might be influenced by several factors like the rarity of the rock or fossil, its size, or even its uniqueness in terms of formation. Some collectors may lean towards casting more delicate forms, while others might focus on specimens with intricate details, such as crystals or fossils embedded within sedimentary rock.
Start by assessing your collection. Perhaps you stumbled upon a striking ammonite or a vibrant piece of geode; these could be great candidates. Think about the story each piece tells, and this can guide your choosing process. Moreover, consider the size and complexity of the object—some items may require more careful handling than others.
Gather information about how certain materials interact with different specimens. For instance, silicone rubber is often ideal for capturing fine details without damaging the original piece.
Designing the Mold Layout
Once you've pinpointed what you want to cast, the next logical step is sketching out the mold layout. This phase is crucial as it determines how the final piece will come together. A well-thought-out design helps in minimizing errors during the casting process and maximizing the quality of the end product.
When designing the mold, consider these key elements:
- Simplicity vs Complexity: A simple object may only require a two-part mold, while a more complex specimen might need a multi-part mold to allow for proper detail capture.
- Accessibility: Ensure that the design permits easy access for pouring the casting material and removing the original specimen later. Think about how you can set it up to avoid air bubbles or misalignments.
- Alignment Keys: Adding features called 'keys' can assist in aligning the two mold halves correctly, reducing the chances of imperfections in your casting.
Tip: Sketch your design on paper before proceeding, as it lets you visualize what the final product will look like, enabling you to make adjustments if needed.
"An ounce of prevention is worth a pound of cure." Not planning properly can lead to costly mistakes, so take your time here.
Balancing the aesthetics and functionality will greatly enhance your casting experience. The time spent in this planning phase pays off once you see the quality of your cast product, looking just like the original with all its nuances beautifully captured.
Creating the Mold
Creating the mold is one of the most crucial steps in the entire casting process. It is the stage that ensures the shape and details of the item being duplicated are preserved accurately. Laying a solid foundation here dictates how successful the final product will be—think of it as setting the stage for a performance. Without a well-made mold, the casting can end up looking like a haphazard attempt rather than the exquisite piece it should be. Considerations during this phase include the choice of materials, intricacies in designing the mold layout, and meticulous attention to detail in preparing the object. Each of these factors contributes significantly to achieving a flawless result.
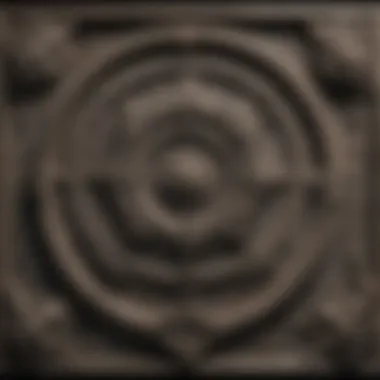
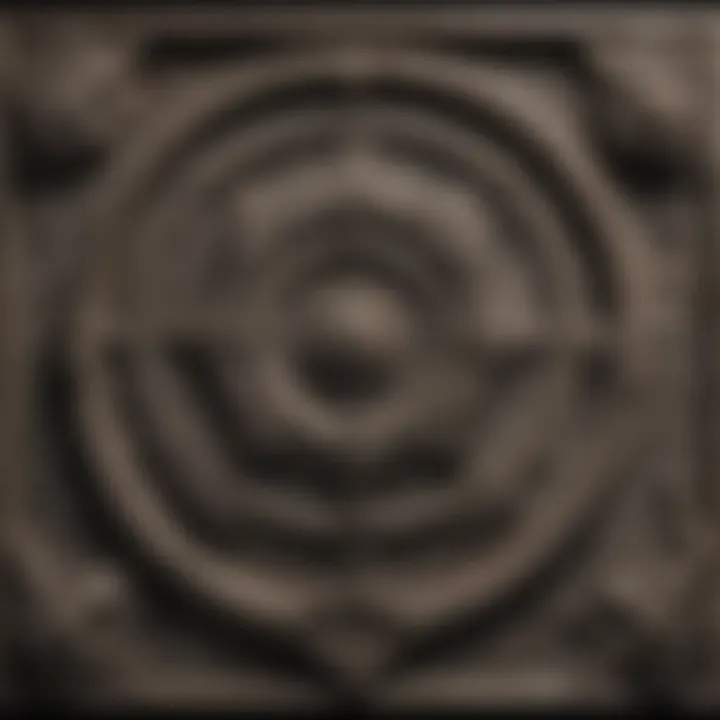
Preparing the Object
A clean, well-prepared object is paramount. This phase lays the groundwork needed for ensuring that the final casting is nothing short of perfect. Two primary tasks need to be completed during preparation: cleaning the object itself and applying a release agent to facilitate removal from the mold.
Cleaning
Cleaning may sound trivial, but it is anything but. This step involves removing dirt, dust, and any residues which could interfere with mold integrity. If the object is dirty, it may leave behind unwanted blemishes in the casted piece, ruining the overall effect. A well-cleaned object is like a blank canvas, ready for capturing every detail and nuance.
The key characteristic of cleaning is its thoroughness. Using a toothbrush or soft cloth soaked in soapy water, and maybe even a fine brush to get into nooks and crannies, showcases this. Popular choices in this article revolve around using warm, soapy water, as it effectively dissolves grime without damaging the object. However, an area of caution is using abrasive materials, which can scratch the surface.
Advantages of cleaning include:
- Improved accuracy in capturing details.
- Elimination of surface imperfections.
Disadvantages can be:
- Time-consuming, especially for irregularly shaped objects.
- Potential risk of damage if done hastily.
Applying Release Agent
Once the object is clean, applying a release agent comes next. This substance forms a barrier between the mold and the object, allowing the mold to be removed easily without damaging either part. It’s pivotal in ensuring that the details of the object remain intact once the mold is created.
The key characteristic of using a release agent is its effectiveness. There are various types available, such as silicone spray or petroleum jelly. Silicone spray is particularly popular as it provides a smooth surface for easy removal after casting, which is a major advantage in molding processes. It’s simple to apply—just a light mist over the object suffices, resulting in an easier demolding process.
However, it’s worth mentioning some unique features: different materials may require different types of release agents, so choosing the right one is critical. Consider this: if using an oily substance with a porous mold, it could absorb onto the mold and mess with the form, causing casting flaws.
Advantages of applying a release agent include:
- Smooth detachment of mold from object.
- Reduced risk of damaging the original object.
Disadvantages can be:
- Incorrect application could lead to mold getting stuck.
- Additional step that may take more time.
Mixing the Mold Material
Mixing the mold material is a delicate art that requires precision and attention to ratios. Selecting the right combination based on the materials chosen ensures the durability and final quality of the mold itself. The ideal material will depend on factors like the detail of the original object and the intended purpose of the mold.
Common choices, such as silicone or latex, require careful measuring and stirring for even consistency. Many mold makers find success by mixing according to the product’s specifications, ensuring that the resultant mix hardens just right to capture intricate details.
Pouring and Setting the Mold
Mastering the pouring technique can make a tremendous difference in the outcome of your casting. This involves pouring the mixed mold material over the prepared object, ensuring that all details are adequately covered. The pouring needs to be controlled and intentional to prevent bubbles or uneven surfaces, which can ruin the final mold.
Pouring Technique
Pouring technique can't be overstated. It is about the finesse with which the material is added. A gentle pour often allows the material to flow smoothly, accommodating minute details without trapping air bubbles. The trick is to pour from the edge of the mold, letting the material seep around rather than pouring directly onto the object. This not only reduces the chance of bubbles forming but helps maintain the original shape better.
The core advantage here is that applying pressure from the edges allows the mold material to surround the object evenly, capturing its shape accurately. Conversely, pouring too quickly might be the downfall, as that could lead to unwanted imperfections.
Setting Time and Conditions
After the mold has been poured, setting time needs careful consideration. This is the period in which the material transitions from liquid to solid. Depending on the type of material used, this time can vary significantly. A common guideline is to give it at least 24 hours, but always check the manufacturer's specifications for insights.
Setting conditions also matter. Temperature and humidity can influence the curing process. A damp environment, for instance, could extend drying time, so it is wise to ensure the mold is set in a controlled atmosphere.
Understanding these nuances will allow collectors and enthusiasts to elevate their casting processes, capturing specimens with unmatched fidelity.
Demolding Process
The demolding process is a pivotal stage in the mold-making journey, serving as the bridge between creation and completion. Here, you see the mold transform from a raw vessel to a tangible product ready for inspection, showing the care taken in the previous steps. The technique employed during this stage can significantly affect the final output, influencing everything from the detail of the cast to its structural integrity. A well-executed demolding process ensures that the cast emerges intact, showcasing the meticulous workmanship that went into crafting the mold.
Careful Removal Techniques
Removing the cast from the mold requires a blend of patience and finesse. Rushing this step can lead to irreparable damage to both the mold and the cast itself. When it comes to precision, some techniques stand out:
- Flexible Molds: For materials like silicone rubber, flexibility enables easier release. Gently bending the mold can help dislodge the cast without much effort.
- Levering Techniques: Using tools such as a small flat screwdriver can effectively create leverage without causing harm. Just ensure not to dig in too deeply.
- Twisting the Mold: For harder materials, a slight twist can free the cast. This method particularly shines with resin or plaster casts.
Always handle with care. The aim here is not just to extract the cast; it’s to do so in a manner that preserves the fine details captured within the mold. Especially for geological specimens where every crevice matters, precision speaks volumes.
Post-Demolding Inspection
Once the casting is free, the next logical step is the post-demolding inspection. This process often feels like a final exam before rolling out a product. Taking the time here not only helps in assessing the quality of the cast but also aids in refining future mold-making endeavors. During this phase, collectors should look for:
- Surface Imperfections: Check for air bubbles, bumps, or other anomalies that may have crept in during the casting stage.
- Detail Fidelity: Evaluate if the cast captures all the nuances of the original object. This is crucial for geological specimens, as minute details can often tell a larger story.
- Structural Integrity: Assess whether the cast feels sturdy, especially for pieces that are meant to be showcased or further processed.
"A clean cast is a happy cast. Small inspections can save big headaches down the road."
By carefully documenting any flaws or aspects needing improvement, one can make educated adjustments next time around.
In summary, the demolding process is a critical intersection of technique and analysis, combining practical skills with a discerning eye for detail. This stage allows for the extraction of not just a cast, but an expression of the craft, making it vital for collectors looking to elevate their geological assortments.
Casting Methods
When it comes to crafting molds for casting, understanding the various casting methods is fundamental. Different casting techniques cater to different materials and desired outcomes, so selecting the right one can make all the difference in the final product. Each method carries its own characteristics, benefits, and special considerations that every collector should keep in mind when aiming to preserve geological specimens effectively.
Choosing a Casting Material
Plaster Casting
Plaster casting has been around for a long time, and it's popular for good reasons. One of the main appeals of plaster is its ease of use. It’s readily available, works well for capturing fine details, and sets relatively quickly. In geological contexts, it is particularly useful for making replica specimens, as it can easily replicate the textures and features of original stones or fossils.
Key characteristic: Plaster has a low-cost advantage, making it accessible for enthusiasts not wanting to break the bank. However, it's worth noting that plaster is also brittle, which might limit its usability for items that may be subjected to stress.
A unique feature of plaster casting is how easily it accepts dyes—allowing for more realistic colors when working on casts that need to look authentic. But it’s important to handle plaster casts with care; they can chip easily.
Resin Casting
Resin casting is another method that offers unique benefits for those in the geological collecting community. This material is known for its versatility and durability, making it suitable for a wide array of applications. It’s particularly beneficial when creating pieces that you want to maintain over time without degrading.
Key characteristic: Resins can be transparent, which allows for encapsulating fossils or other objects while showcasing them beautifully. This feature is a game-changer for display purposes.
However, mixing the resin correctly requires precision, as errors can lead to weak spots in the final piece. Plus, certain resins can emit strong fumes, which necessitate good ventilation during the casting process.
Metal Casting
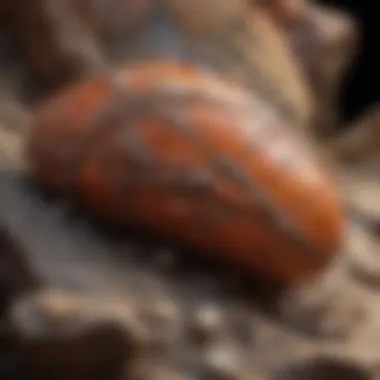
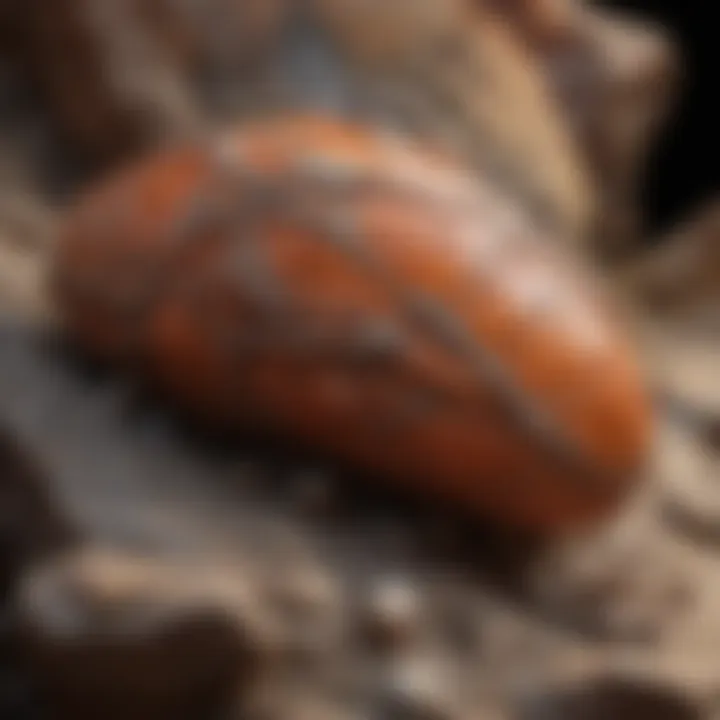
Metal casting is a heavyweight player when it comes to durability and aesthetic appeal. Used often in more advanced applications, metal casting allows for creating intricate designs that simply can’t be achieved with softer materials. It’s great for those serious about displaying their pieces—just think about those shiny metal replicas of geological wonders.
Key characteristic: The resilience of metal allows for functional uses, not just decorative. For collectors looking to produce tools or replicas that will withstand time and handling, metal is often the preferred choice.
This method requires specialized tools and techniques, making it less accessible for casual DIYers. It’s time-consuming and may require skills in metallurgy or casting that many may not possess immediately.
Pouring the Casting Material
Once the appropriate material has been chosen, pouring it into the mold is the next step. This is a crucial stage where precision can make or break the whole project. Factors like temperature, viscosity, and the environment all play key roles in ensuring that the material fills the mold properly and forms the intended shape without any air pockets. Proper pouring technique and patience is essential for a successful cast.
Finishing Touches
Finishing touches in mold crafting are more than just aesthetic; they are crucial for ensuring the final casting is both functional and visually pleasing. This stage addresses the practicality of inspecting and refining your mold and the final product, emphasizing that attention to detail can significantly impact the display and usability of your geological specimens.
Trimming and Cleaning the Mold
Trimming and cleaning the mold is an essential step in the molding process. After the demolding process, it’s common for edges to be rough or uneven. This can happen due to minor imperfections in the pouring or setting process.
- Why trim? The primary goal is to ensure that your mold produces casts that are free from blemishes and defects. Trimming involves removing excess material, such as flash, which is the extra resin or rubber that can form along the seams.
- Method: Use a sharp utility knife or scalpel for this task. It’s wise to go slow and steady, as too much pressure can compromise the integrity of the mold itself.Here’s a simple procedure to follow:
- Inspect the edges of your mold for uneven areas.
- Carefully cut away any excess material.
- Smooth the edges using sandpaper.
- Finally, clean the mold with a soft cloth to remove dust or debris.
Cleaning the mold is equally crucial. Any dust particles left can become part of the casting and affect the finish of your specimen. So, give it a rinse under warm water followed by a gentle wipe-down. If the mold material allows it, a little soap can be used, too, but always do a patch test to avoid damaging your mold's surface.
Quality Check of the Final Product
Conducting a quality check on the final product ensures that all the labor invested in the molding and casting pays off. Each cast should be examined under specific criteria to guarantee that it meets the necessary standards for a geological collection.
- Appearance: Look for any surface blemishes, inconsistencies, or unexpected texture changes. The cast should mirror the original object accurately.
- Dimensions: Use a caliper or ruler to ensure your cast has maintained the desired proportions. Sometimes materials can shrink or warp; catching these issues early is vital.
- Functionality: If the cast is to serve a specific function, like fitting into a display, ensure it meets all functional requirements. Test it against its intended use to confirm compatibility.
"A careful inspection saves time and resources, ultimately enhancing your collection's quality."
In summary, finishing touches are not just the cherries on top; they are critical to the overall success of your mold-making project. By investing the time to trim, clean, and perform quality checks, you’ll ensure that your geological casts are not only beautiful but also serve their intended purpose effectively. This diligence reflects the dedication of any serious collector, and enhances the value of the collection as a whole.
Common Issues and Troubleshooting
Understanding the ins and outs of common problems in mold-making is crucial for any collector or enthusiast looking to craft their own molds. Problems in molding can lead to significant failures and wasted time or materials, so recognizing these issues and knowing how to remedy them can make a world of difference in achieving successful casts. This section discusses identifying two of the most common issues—air bubbles and misalignments—along with their impact on the overall process of mold-making. It will also explore remedies for casting failures, offering a comprehensive guide to overcoming these challenges.
Identifying Problems in Molding
As any seasoned collector knows, not every casting goes according to plan. Being able to recognize the root causes of mold failures can save you both hassle and heartache. Below, we categorize some of the specific problems:
Air Bubbles
Air bubbles are pesky little nuisances in the world of mold-making. They form when air is trapped in the casting material and can create voids in the final product. Understanding their nature is key.
The key characteristic of air bubbles is their unpredictability. They tend to catch you off guard if you’re not paying close attention. When casting with materials like resin or plaster, bubbles often appear when pouring; they can compromise the surface integrity of the final product and alter its appearance.
Air bubbles are a problematic aspect of the casting process. While bubbles themselves might not seem like a major concern, they can weaken the durability of the mold, impacting its effectiveness in capturing fine details. To mitigate this, many mold-makers incorporate techniques like pouring from a height to minimize turbulence, or using a vacuum chamber to degas the material prior to use—both proven methods to reduce bubble formation.
Misalignments
Misalignments occur when the mold halves do not line up perfectly during the casting process. This might happen due to error in the initial design or errors during the demolding phase. Their impact can be significant, as misalignments can lead to distorted figures and poor-quality casts.
A key characteristic of misalignments is their ability to ruin the aesthetic aspect of the finished piece, making it less appealing, especially for collectors focused on detail. In this context, misalignments can be viewed as a decisive factor between a mere replica and a well-crafted piece art.
One unique feature of misalignments is they can often be fixed with adjustment during the setup phase. Using clamps or aligning guides can ensure the mold remains balanced and correctly oriented. Additionally, being meticulous during the molding process—including how the initial layers are poured—can help prevent misalignments from occurring in the first place.
Remedies for Casting Failures
Remedies for casting failures touch on proactive measures as well as reactive solutions to address issues once they arise. Here are some tips to guide you through:
- For Air Bubbles:
- For Misalignments:
- Vibration Techniques: Gently vibrating the mold can help bubbles rise to the surface.
- Slow Pouring: Reduce the height from which you pour the material. Smaller pours can cause fewer bubbles.
- Heat Treatment: In some cases, warming the casting material slightly can make it less viscous, allowing bubbles to escape more easily.
- Double-Check Measurements: Before you start pouring, ensure your mold's dimensions are accurate.
- Secure Your Mold: Use clamps or external supports to keep the mold from shifting after pouring.
- Trial Runs: It’s worth doing a quick test run to identify potential misalignment issues before proceeding with your final cast.
In summary, tackling common issues like air bubbles and misalignments is vital for achieving quality in mold-making. By staying ahead of these challenges and implementing effective remedies, you ensure that your casting efforts yield successful and satisfactory results.
Best Practices in Mold-Making
When diving into the world of mold-making, adhering to best practices is not just a recommendation—it's essential. This section emphasizes the significance of sound techniques and careful methodologies to ensure that each mold you create yields high-quality castings. Proper practices enhance durability, improve accuracy, and maximize the longevity of both molds and the castings derived from them. Familiarity with these practices will positively impact your end results, providing you with reliable molds for your geological collection.
Safety Precautions
Before getting hands-on with mold-making, understanding safety precautions is a must. This isn’t merely about avoiding mishaps but ensuring a smooth, efficient process. Here are some key safety measures:
- Wear Protective Gear: This includes gloves, goggles, and masks. The materials used, especially resins and silicones, can emit fumes or may irritate the skin.
- Ventilate Your Workspace: Good airflow minimizes inhalation of any hazardous materials. Working in a garage with open windows can be ideal.
- Avoid Skin Contact: Molds and casting materials can cause irritation. Always handle them with care and keep your workspace free from spills.
- Read Material Safety Data Sheets (MSDS): Understanding the properties and hazards associated with your materials is crucial. These sheets guide you on proper handling and emergency measures.
In the world of craftsmanship, being cautious is half the battle. Investing time to prepare properly can save trouble down the line.
Storage of Molds and Castings
Proper storage of your molds and castings ensures that they remain in pristine condition for future use. Neglect in this area might lead to damage or deterioration over time. Consider the following points for effective storage:
- Temperature Control: Store molds in a cool, dry place. Excessive heat or humidity can warp molds, especially those made from flexible materials like silicone.
- Use Protective Cases: For castings, consider using padded boxes or containers that prevent scratching and breakage. Keeping them in a secure location can also prevent unforeseen accidents.
- Organization: Clearly label and organize your molds and castings. When embarking on future projects, knowing exactly what you have can save time and effort.
- Routine Inspections: Periodically check the condition of your molds and castings. Look for signs of wear, cracks, or degradation. Catching these early can allow for repairs or replacements before they become unusable.
"The investments made in proper safety and storage practices are foundational to the longevity and success of mold-making endeavors."
By integrating these best practices into your mold-making routine, you not only safeguard yourself and your creations but also advance the quality and reliability of your contributions to your geological collection.
Ending
The conclusion wraps up the intricate journey through mold-making and casting, underscoring its importance not just for functionality, but also for the aesthetic and informational value it brings to geological collections. Understanding how to craft effective molds opens the door to capturing the delicate details of specimens that tell the story of our planet's history. When done right, these molds offer a means to preserve and share pieces of the Earth's artistic and scientific wonders with a wider audience.
Recap of Key Techniques
Reflecting back on the journey, several techniques stand out as pivotal in the mold-making process:
- Material Selection: The choice between silicone rubber, latex, plaster, or resin can significantly impact the final product. Each material has its specific attributes; silicone is flexible, while plaster provides rigidity.
- Preparation: Thorough cleaning of objects prior to molding ensures that the captured details are accurate and minimizes defects. Additionally, the application of release agents cannot be overlooked, as it prevents sticks that compromise the mold integrity.
- Pouring Methods: The technique used to pour the mold material can influence the presence of air bubbles and the overall quality of the cast. A slow, steady pour often yields better results than a rushed one.
- Post-Demolding Care: Inspecting the mold immediately after removal allows for quick identification of any defects. This is a critical step that can save time and materials in future casts.
It’s through these techniques that collectors not only create beautiful replicas but also contribute to the understanding of geological specimens.
Encouragement for Experimentation
In the world of mold-making, there are no hard and fast rules. This aspect can be quite liberating for enthusiasts and collectors alike. Experimentation not only fosters creativity but can also lead to unexpected successes. For instance, mixing different materials or altering the mold design can yield fascinating textures and structures.
- Try new combinations: By integrating various casting materials, unique properties and visual appeals may emerge that standard methods do not provide.
- Customize Mold Shapes: Consider designing molds that emphasize the natural contours of the specimen. Custom shapes can showcase your collection in a whole new light, attracting the eyes of fellow collectors and viewers.
- Iterate on Failures: Do not shy away from mistakes. Every failed attempt demonstrates valuable lessons about what works and what doesn't, refining your technique over time.
This dynamic approach not only enhances skills but can also enrich the joy found in the collecting experience. As you delve deeper into this art form, remember that the path of experimentation is where true innovation lies, often leading to delightful surprises.